Uniones soldadas y uniones adhesivas en materiales compuestos
Desde 1980 hasta la actualidad los materiales compuestos de matriz termoplástica han suscitado un creciente interés en la industria aeronáutica unido al desarrollo de resinas termoplásticas de propiedades mecánicas elevadas, tales como la polieteretercetona (PEEK), el polisulfuro de fenilo (PPS) o la polieterimida (PEI). Este interés responde tanto a su buen comportamiento mecánico-ambiental como a que permiten procesos de fabricación sencillos, extraordinariamente rápidos y fácilmente automatizables.
Las matrices termoplásticas se caracterizan, en contraposición con las termoestables, por una microestructura formada por cadenas poliméricas lineales no entrelazadas. A consecuencia de ello, sus procesos de fabricación no implican reacciones químicas de polimerización o curado, sino sólo transformaciones físicas, básicamente reblandecimiento o fusión durante el calentamiento y solidificación durante el enfriamiento.
Debido a la especial naturaleza de este tipo de resinas, los materiales compuestos basados en ellas plantean la posibilidad de realizar uniones soldadas, que consisten en el reblandecimiento de la matriz en la zona de unión mediante calentamiento local unido a la aplicación de una presión de consolidación que promueve la unión íntima entre los sustratos. Existen distintas posibilidades en cuanto al método de soldadura de materiales compuestos termoplásticos que se clasifican según la forma de calentamiento de la entrecara de unión: placa caliente, vibración, ultrasonidos, inducción, resistencia, etc.
La soldadura por resistencia consiste en el calentamiento del material mediante el paso de corriente eléctrica por un implante conductor (efecto Joule) situado en la entrecara de soldadura y que queda embebido en el material una vez realizado el proceso. Las principales ventajas de este método de soldadura son su simplicidad, rapidez (tiempos de proceso del orden de pocos minutos) y un equipamiento sencillo y poco costoso. El principal inconveniente frente a otras técnicas de soldadura es la permanencia en la zona de unión de un inserto que, en función de su naturaleza, puede llegar a comprometer el comportamiento mecánico-ambiental del material.
Las uniones mediante adhesivos en materiales compuestos de matriz termoplástica plantean una serie de problemas derivados de la inercia química de este tipo de resinas, sobre todo cuando parte de sus cadenas poliméricas presentan una ordenación cristalina (matrices termoplásticas de naturaleza semicristalina como el PEEK y el PPS). A consecuencia de ello, la preparación superficial de las zonas de unión cobra un papel muy relevante en este tipo de procesos, no existiendo consenso en la literatura de referencia acerca del procedimiento más adecuado ni del adhesivo idóneo.
El presente estudio analiza estos dos tipos de uniones en laminados de PPS reforzados con fibras de carbono para unas condiciones de contorno dadas. La calidad de las uniones obtenidas se cuantifica mediante ensayos de cortadura con solape simple.
Procedimiento experimental

Uniones adheridas
Para la realización de este tipo de uniones se emplean dos adhesivos de distinta naturaleza: FM300 y polieterimida (PEI).
El FM300 es un adhesivo termoestable (base epoxi) de elevadas características mecánicas y empleado profusamente en uniones adhesivas de materiales compuestos avanzados de matriz termoestable. Tiene un ciclo de curado a 180°C y 3bar de presión con una duración aproximada de 150 min. Al ser base epoxi, debe conservarse a -18°C hasta su utilización.
En las uniones realizadas en el presente trabajo con FM300 (siempre mediante bolsa de vacío en autoclave) se consideran dos tipos de preparación superficial de los sustratos: abrasión mecánica y preparación mediante lámina de pelado (peel-ply).
En términos generales, la preparación superficial mediante peel-ply es una técnica rápida y sencilla que permite obtener superficies con una rugosidad superficial adecuada. Consiste en incorporar a los sustratos una lámina con una determinada textura previamente a su consolidación. Esta lámina, que se retira en el momento de realizar la unión, debe ser inerte desde el punto de vista químico, fácil de retirar de la superficie sobre la que se aplica y resistente a las temperaturas de fabricación de los sustratos. En este trabajo se emplea una lámina de pelado cuya temperatura de servicio se encuentra, según fabricante, en torno a 260ºC en uso continuo y en torno a 400ºC para uso intermitente.
La abrasión mecánica se realiza mediante chorro de arena, método aplicado con éxito para la realización de uniones adheridas en materiales compuestos de matriz termoestable.
La polieterimida (PEI), segundo material empleado como adhesivo en este trabajo, es una resina termoplástica amorfa de elevadas propiedades mecánicas que, al igual que el PPS, se emplea como matriz en materiales compuestos avanzados de gran interés en la industria aeronáutica. Presenta una temperatura de reblandecimiento en torno a 215°C y, empleada como adhesivo, tiene como ventajas su compatibilidad con el PPS, tiempos de procesado cortos y que, al ser químicamente estable como el resto de las resinas termoplásticas, se conserva a temperatura ambiente.
Las uniones realizadas mediante una película de PEI se llevan a cabo en bolsa de vacío en autoclave a 260°C y 4bar con un ciclo de 90 min de duración. Con el fin de optimizar la compatibilidad entre adhesivo y el material de los sustratos, éstos se modifican previamente a su consolidación mediante la adición de una capa de PEI sobre las superficies de unión.
No se somete a dichas superficies a ninguna preparación superficial previamente a la realización de la unión.
Uniones soldadas
Se sitúa el agente calefactor entre los dos sustratos, limpiados previamente con acetona, aislándolo eléctricamente de los mismos mediante dos capas de preimpregnado de PPS / fibra de vidrio según el esquema mostrado en la figura 2. Se hace pasar corriente eléctrica por la malla metálica hasta alcanzar la temperatura de soldadura (dentro del rango de temperaturas de proceso del PPS) y, tras un tiempo de permanencia a la misma (pocos minutos), se inicia el enfriamiento mediante la retirada de la corriente. Durante todo este proceso se aplica presión en la zona de soldadura mediante bolsa de vacío y sin sobrepresión exterior (es, decir, fuera del autoclave). Se emplea este tipo de configuración debido a que los estudios realizados en el Área de Materiales Compuestos del INTA acerca de soldadura de materiales compuestos termoplásticos se enmarcan en el ámbito de la reparación de daños en estructuras avanzadas.

Ensayos
La calidad de los distintos tipos de uniones realizadas se cuantifica en este estudio mediante ensayos de cortadura con solape simple según la norma ASTM D 1002. Es bien conocido que la desviación de la línea de carga con respecto a la línea de unión que tiene lugar en este ensayo conduce a una combinación entre esfuerzos de cortadura y de pelado en la zona de solape. Este estado de carga es más desfavorable que uno de cortadura puro pero tiene como ventaja un alto grado de similitud con solicitaciones reales.
Todos los ensayos se realizan en condiciones normales, esto es, 23ºC y 30% de humedad relativa. Se ensayan al menos 8 probetas por cada panel que se obtienen mediante corte con discos de diamante.
Resultados y discusión
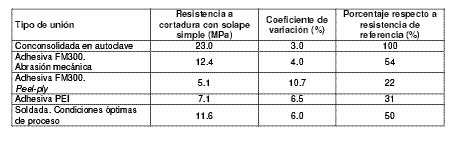
Uniones adhesivas
Las uniones con el mismo adhesivo y preparación superficial mediante peel-ply presentan valores de resistencia muy bajos (22% de la resistencia de referencia) y con un grado de dispersión elevado. Se observa en ellas que el FM300 no se adhiere a la superficie de los sustratos, quedando simplemente compactado entre ambos. Tras un análisis de dichas superficies, se encuentra que el motivo de la falta de adherencia es la presencia de PTFE en las mismas. Esta sustancia antiadherente procede del peel-ply, descompuesto parcialmente durante el ciclo de fabricación de los sustratos. A la vista de estos resultados, se concluye que el peel-ply empleado no es el más conveniente para este tipo de aplicaciones, debiendo quizás recurrir a soluciones basadas en tejidos de fibra de vidrio.
Las uniones con adhesivo termoplástico (PEI) también ofrecen valores bajos de resistencia (31% de la resistencia de referencia). Entre las posibles causas de estos resultados están una hipotética transferencia de agentes desmoldeantes a las superficies de unión durante la fabricación de los sustratos (no retirados mediante ningún tipo de preparación superficial) o la necesidad de un reajuste en los parámetros del ciclo de adhesión.
Uniones soldadas frente a uniones adheridas
Las uniones soldadas, que conducen a un valor medio de resistencia a cortadura con solape simple del 50% del valor de referencia, se realizaron con una presión de consolidación de la soldadura del orden de 0.8bar (bolsa de vacío), que responde a condiciones reales para la reparación de daños en campo. Este valor para la presión de consolidación, parámetro de influencia directa en la calidad de la unión, es un valor relativamente bajo comparado con los empleados en la bibliografía consultada en materiales y procesos similares para la obtención de resistencias superiores al 75% del valor de referencia [SIE02].
El mejor valor de resistencia en uniones adhesivas con FM300 es similar al proporcionado por las uniones soldadas, pero debe tenerse en cuenta que se ha obtenido aplicando el ciclo de curado recomendado por el fabricante del adhesivo. Cabe esperar, por lo tanto, un mejor comportamiento de las uniones soldadas frent
Conclusiones
En este trabajo se han llevado a cabo uniones soldadas por resistencia y uniones adhesivas entre sustratos de PPS reforzado con tejido de fibra de carbono. Para las primeras se han empleado dos tipos de adhesivos, FM300 y PEI, y dos tipos de preparación superficial, peelply y abrasión mecánica. Para las segundas se empleó como agente de calentamiento una malla de acero inoxidable aislada eléctricamente de los sustratos mediante capas de PPS reforzado con tejido de fibra de vidrio.
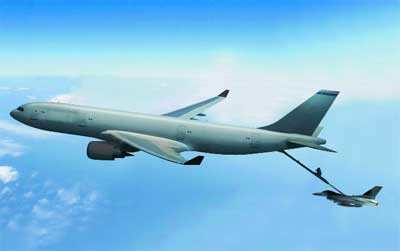
Se han obtenido valores de resistencia a cortadura con solape simple del 54% de la resistencia de referencia en uniones adhesivas con FM300 y abrasión mecánica. El peel-ply empleado para la otra variante de preparación superficial ha resultado no ser inerte químicamente a las temperaturas de fabricación de los sustratos. Asimismo, se considera necesaria una optimización del proceso correspondiente a la unión con PEI.
Se han obtenido valores de resistencia del 50% del valor de referencia para las uniones soldadas, similares a los mejores resultados obtenidos en uniones adhesivas. Se debe tener en cuenta, sin embargo, que mientras que estos últimos corresponden a ciclos óptimos de curado, los primeros corresponden a condiciones de proceso desfavorables que reproducen procesos reales de reparación de daños en estructuras aeronáuticas
Referencias
- [FEN03]
- Fernández I., Blas F., Frövel M., "Autoclave forming of thermoplastic composite parts", Journal of Materials Processing Technology", nº 143-144, pp. 266-269, 2003
- [OFF01]
- Offringa A., Myers D., Buitenhuis A., "Redesigned A340-500/600 fixed wing leading edge (Jnose) in thermoplastics", Proceedings of the 22nd SAMPE Europe Conference, pp. 331 - 343, 2001
- [SIE02]
- Sierksma D., Resistance welding of carbon fibre reinforced thermoplastic composites, Thesis Report, Faculty of Aerospace Engineering, Delft University of Technology, 2002