Unmasking the myths of the successful construction of moulds with resin for Stereolithography
The direct construction of moulds through the Stereolithography is being now a new service, the evidence as a series of new commercial applications. While traditionally the previous resins for SL could not offer the life time for a job, the commercial success of new materials we are ProtoComposites, ProtoTool 20 L and NanoForm, are showing new possibilities in the time and cost savings. Success depends not only on the commercial introduction of these technologically advanced resins, but also the creation of a network of experts experienced in the design and manipulation of composite moulds.
The following information is the first of a series on the "myths of the industry" on the rapid tooling resins for SL to be held in the coming months by DSM Somos and collaborating companies engaged also in the increase of international knowledge at this new stage of product development.
Myth 1: companies focused on the CNC machining in high speed will not choose the incorporation of moulds of SL in their production capacities
While the rapid construction of moulds industry had already reported on some positive findings, Paramount had not experienced first-hand with no material for SL that could respond to the demands of its clients with regard to the qualitythe material and design. However, some of the new information from the industry caught his attention:
- You could save time using hybrid moulds: while the cavity machines, are manufactured inserts through loadable SL manually;
- Savings could also be achieved in time in the construction of the mould insert: a mold of SL can be finished and assembled in the mold in a period between three and five days, depending on the size of the mould;
- SL technologies can produce prototype parts and/or molds on the same platform;
- You can increase the production capacity: through SL many moulds can be made at the same time;
- The reduction of costs and labour is possible: once the 3D information is inserted in the team of SL, the time of the employee can dedicate to other functions
- Cost savings are real: in some dimensions, the cost of the realization of a mold by SL is less than the of the CNC machining, with a cost optimized for molding by injection of small volumes.
The decision to experiment with molds made by SL was taken with some reservations, as well as a great prevention. The incentive after the decision: a new material composed for SL with a performance that go further traditional resins for SL - Somos ProtoTool 20 L. The main parameters of their benefits include: high precision, resistance to abrasion, during the moulding process, temperature HDT that surpass even the thermoplastic many engineering usually molded parts.
In one of the three technical studies that the company contributed later to the EMS (the complete technical data and the results of the study "Injection Molding with Composite Stereolithography Resins" can be obtained on the web site of Society of Manufacturing Engineers at www.sme.rg)We are ProtoTool played a determining role to helping Paramount to solve a problem that would have been weeks of delays in the production of which should be injection moulded parts with an extremely aggressive material: nylon-6 with 33 per cent of glass.
The project included the co-development of an air system of Ingersoll-Rand who was redesigning to incorporate machined metal components injection molded thermoplastics. When the production moulds were about to be completed, was identified as a problem in the geometry of one of the components of the case. The correction of the mould needed between 4 to 5 weeks.
The team identified the internal piece that should be modified to correct the error, but what was learned in theory should be experienced. Test piece with rapid prototyping materials didn't make sense; all tests should be carried out with the real material, because the speed of the engine of the product reach 30,000 rpm and the accelerated speed of the air can create temperatures very compromising to the majority of thermoplastics. At least two pieces molded in the actual material of the final product would be required. If the change of design work, the provider could proceed to adjust the primary mold and Assembly could start 2-3 weeks before.
The customer described the piece as "very functional" and explained that they were being used successfully in a pilot development along with other components molded engineering.
The results of tests conducted by Paramount Industries with ProtoTool showed that there were opportunities to improve the supply of services of the company from an economic point of view, through the incorporation of this technology, while maintaining quality for their customers.
While this first test using composites of SL was useful at Paramount to verify the validity of ProtoTool with thermoplastic aggressive, the decision to integrate the technology into its plant was only decided after verification validity in applications of current major with thermoplastic series of less aggressive nature.
Four additional studies facilitated the decision, with results that generally checked the quality of the molds made from ProtoTool when used materials such as nylon-6 with fiber glass, polypropylene, styrene, ABS and polycarbonate, as well as series of volumes that can be expected (to 1700)(, depending on the material). The analysis of costs and time-saving based on the knowledge of the company showed that there is a valid number of applications in which ProtoTool not only saves time (reductions of time standard of 50 per cent), but which also translates into savings for their clients.
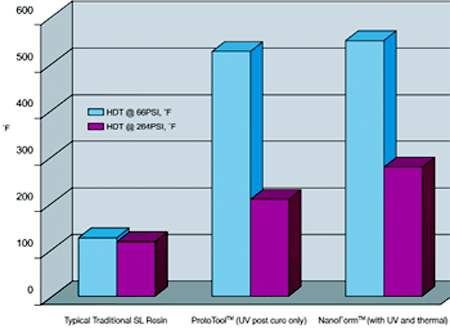
"The probability of life has been historically a fundamental criterion for the construction of injection moulds which, by definition, must be produced numerous pieces." Another value that is used to measure the level of success is the amount or the performance of the mold that you should expect from a fast mold. Paramount goals to apply technologies of SL in the construction of mould inserts give priority to the quality of the piece and specified engineering resin to be used in the moulding. The ability to quickly make pieces by moulding by injection without affecting the design is at the forefront of the priorities, while the useful life of the mold should be secondary. "Our research has shown clearly that quality and quantity are possible using the composite advanced SL we are" concluded Williams.