Desenmascarando los mitos de la construcción exitosa de moldes con resinas para estereolitografía
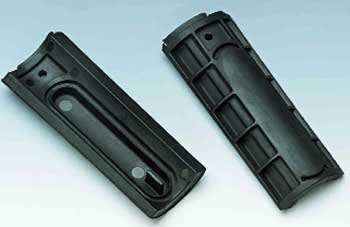
La construcción directa de moldes a través de la estereolitografía está siendo objeto ahora de una nueva atención, como lo evidencias una serie de nuevas aplicaciones comerciales. Mientras que tradicionalmente las resinas para SL anteriores no podían ofrecer el tiempo de vida necesario para un trabajo, los éxitos comerciales de los nuevos materiales Somos ProtoComposites, como ProtoTool 20L y NanoForm, están demostrando nuevas posibilidades en el ahorro de tiempo y costes. El éxito no sólo dependerá de la introducción comercial de estas resinas tecnológicamente avanzadas, sino también de la creación de una red de expertos experimentados en el diseño y manipulación de moldes compuestos.
La siguiente información es la primera de una serie sobre los “mitos de la industria” en torno al rapid tooling con resinas para SL que se realizarán en los próximos meses por DSM Somos y compañías colaboradoras dedicadas también al incremento del conocimiento internacional en este nuevo escenario del desarrollo de producto.
Mito 1: las compañías centradas en el mecanizado CNC a alta velocidad no elegirán la incorporación de moldes de SL en sus capacidades de producción
A pesar de que la industria de la construcción rápida de moldes ya había informado sobre algunos descubrimientos positivos, Paramount no había experimentado de primera mano con ningún material para SL que pudiera responder a la exigencia de sus clientes en lo relativo a la calidad, el material y el diseño. Sin embargo, algunas de las nuevas informaciones de la industria captaron su atención:
- Se podía ahorrar tiempo mediante el uso de moldes híbridos: mientras la cavidad se mecaniza, se pueden fabricar insertos mediante SL cargables manualmente;
- También se podían lograr ahorros en tiempo en la construcción del inserto del molde: un molde de SL puede ser acabado y montado en el molde en un periodo entre tres y cinco días, dependiendo del tamaño del molde;
- Las tecnologías SL pueden producir piezas prototipo y/o moldes en una misma plataforma;
- Se puede aumentar la capacidad de producción: mediante SL se pueden realizar numerosos moldes al mismo tiempo;
- La reducción de costes y de mano de obra es posible: una vez la información 3D está introducida en el equipo de SL, el tiempo del empleado puede dedicarse a otras funciones
- Los ahorros en costes son reales: en algunas dimensiones, el coste de la realización de un molde a través de SL es inferior al del mecanizado CNC, con un coste optimizado para el moldeo por inyección de pequeños volúmenes.
La decisión de experimentar con moldes hechos mediante SL se tomó con ciertas reservas, así como también con una gran prevención. El incentivo tras la decisión: un nuevo material compuesto para SL con unas prestaciones que van más lejos de las resinas para SL tradicionales – Somos ProtoTool 20L. Los principales parámetros de sus prestaciones incluyen: elevada precisión, resistencia a la abrasión, duración durante el proceso de moldeo, temperaturas HDT que sobrepasan incluso a las de muchos termoplásticos de ingeniería habitualmente moldeados.
En uno de los tres estudios técnicos que la compañía aportó posteriormente para la SME (los datos técnicos completos y los resultados del estudio “Injection Molding with Composite Stereolithography Resins” pueden obtenerse en el sitio web de Society of Manufacturing Engineers en www.sme.rg), Somos ProtoTool jugó un papel determinante al ayudar a Paramount a resolver un problema que le hubiera supuesto semanas de retraso en la producción de piezas que debían ser moldeadas por inyección con un material extremadamente agresivo: nylon-6 con un 33 por ciento de vidrio.
El proyecto incluyó el co-desarrollo de un sistema de aire de Ingersoll-Rand que se estaba rediseñando para pasar de incorporar componentes metálicos mecanizados a termoplásticos moldeados por inyección. Cuando los moldes de producción estaban a punto de ser terminados, se identificó un problema en la geometría de uno de los componentes de la carcasa. La corrección del molde necesitaba entre 4 y 5 semanas.
El equipo identificó la pieza interna que debía ser modificada para corregir el error, pero lo que se supo en teoría debía ser experimentado. Probar la pieza con materiales de prototipado rápido no tenía sentido; todas las pruebas debían ser realizadas con el material real, porque las velocidades del motor del producto alcanzan las 30.000 rpm y las velocidades aceleradas del aire pueden crear temperaturas muy comprometedoras para la mayoría de los termoplásticos. Se necesitarían al menos dos piezas moldeadas en el material real del producto final. Si el cambio de diseño funcionaba, el proveedor podría proceder a adaptar el molde primario y el montaje podría comenzar 2 ó 3 semanas antes.
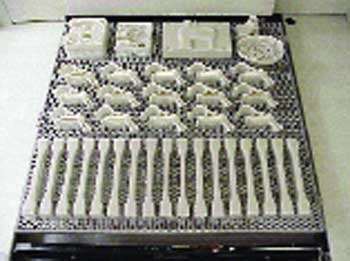
El cliente describió las piezas como “muy funcionales” y explicó que estaban siendo utilizadas con éxito en la ingeniería de un desarrollo piloto junto con otros componentes moldeados.
Los resultados de las pruebas realizadas por Paramount Industries con ProtoTool demostraron que había oportunidades para mejorar la oferta de servicios de la empresa desde un punto de vista económico, mediante la incorporación de esta tecnología, manteniendo la calidad para sus clientes.
Mientras esta primera prueba utilizando materiales compuestos de SL fue útil en Paramount para verificar la validez de ProtoTool con termoplásticos agresivos, la decisión de integrar la tecnología en su planta se decidió sólo tras verificar validez en aplicaciones de series mayores con termoplásticos corrientes de naturaleza menos agresiva.
Cuatro estudios adicionales facilitaron la decisión, con resultados que en general verificaron la calidad de los moldes hechos con ProtoTool cuando se recurre a materiales como nylon-6 con fibra de vidrio, polipropileno, estireno, ABS y policarbonato, así como en series de volúmenes que pueden ser esperados (hasta 1.700, dependiendo del material). El análisis de ahorro de tiempo y costes basado en el conocimiento de la compañía demostró que hay toda una serie válida de aplicaciones en las cuales ProtoTool no sólo permite ahorrar tiempo (reducciones de tiempo habituales del 50 por ciento), sino que también se traduce en ahorros económicos para sus clientes.
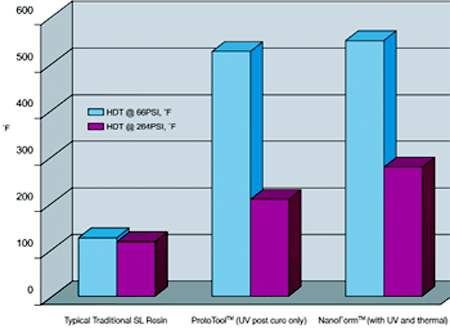
“La probabilidad de vida ha sido históricamente un criterio fundamental para la construcción de moldes de inyección que, por definición, deben producir numerosas piezas. Otro valor que se utiliza para medir el nivel de éxito es la cantidad o el rendimiento del molde que uno debe esperar de un molde rápido. Los objetivos de Paramount al aplicar tecnologías de SL en la construcción de insertos para moldes priorizan la calidad de la pieza y la resina de ingeniería especificada para ser usada en el moldeo. La capacidad para fabricar rápidamente piezas mediante moldeo por inyección sin perjudicar el diseño está a la cabeza de las prioridades, mientras que la vida útil del molde debería ser secundaria. Nuestras investigaciones han mostrado con claridad que calidad y cantidad son posibles utilizando los materiales compuestos avanzados para SL de Somos” concluye Williams.