Procesa hasta 6.000 packs de botellas/h en la planta de Bisleri en Bombay
Ferag instala el transportador deniway a 20 m en una planta embotelladora de agua
Los dos sistemas de transporte de cadena de placas deniway con una longitud de 290 m y 170 m, que Ferag ha instalado en la principal planta embotelladora de agua de Bisleri en India, transportan botellas y packs de la estación de llenado, situada en la planta superior, al área de expedición, ubicada en la planta baja.
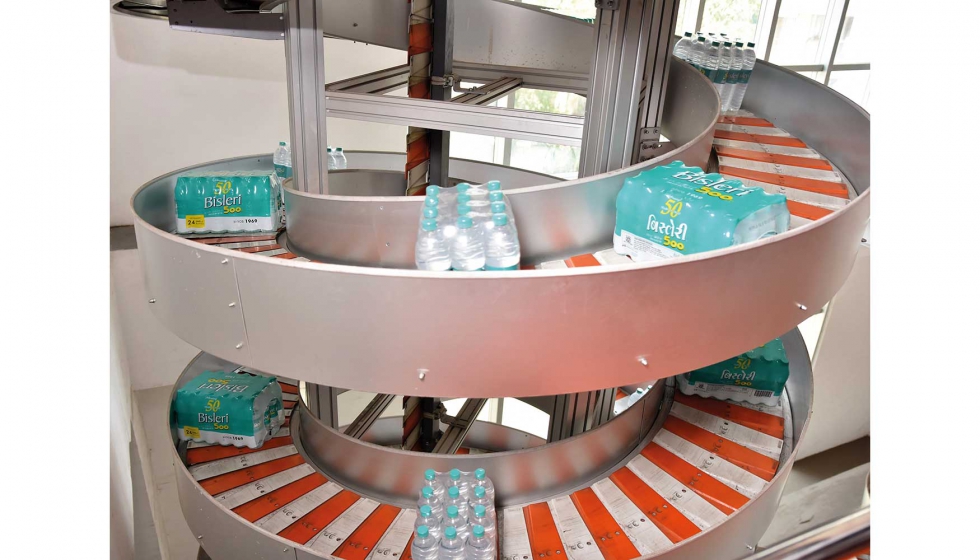
Para optimizar el espacio, Ferag ha diseñado un transporte vertical en espiral que alcanza 20 m, el más alto construido por la empresa suiza hasta la fecha. La capacidad de procesamiento de estos sistemas de transporte de final de línea alcanza hasta 6.000 packs de botellas por hora.
De esta tecnología de transporte, llaman la atención las tres espirales por donde circulan las botellas, y que ocupan un espacio muy reducido. La espiral más larga del sistema sube hasta 20 m para transportar los packs retractilados de botellas fabricadas con PET de distintas capacidades (250 ml/ 24 botellas; 250 ml/48 botellas, 500 ml/24 botellas, 1000 ml/12 botellas, 2000 m/9 botellas) por cinco pisos hasta el segundo nivel inferior de la planta baja, donde se encuentra el área de almacén y expedición.
Las otras dos espirales, de 11 y 6 m de altura respectivamente, forman un par de cintas transportadoras de una segunda línea, destinada exclusivamente al transporte de garrafas de agua de 5 a 20 l. Tras el proceso de llenado, bajan en vertical por la segunda espiral hasta el primer nivel por debajo de la planta baja. En cuanto a la tercera espiral, se ocupa en el transporte de garrafas vacías desde el área de limpieza, en la planta baja, hasta las máquinas de enjuague y llenado, en la primera planta de la instalación.
La tecnología de Ferag admite radios de curvatura muy estrechos, lo que garantiza la enorme flexibilidad del transportador en espiral. Las espirales del sistema deniway tienen un diámetro de tan solo 2.5 m y salvan diferencias de altura muy pronunciadas, al tiempo que requieren poco espacio.

A esto hay que añadir su gran eficiencia energética: cada línea solo necesita un motor, gracias a la tecnología deniway de la empresa suiza, basada en el principio de “rodamiento frente a deslizamiento”. El sistema de accionamiento controlado por carga se ha diseñado de tal forma que cada una de las líneas del transportador puede manejar un peso total de transporte de hasta 1,45 toneladas por minuto, lo que se traduce en 100 packs por minuto, o 6000 por hora.
Tecnología a prueba de climas monzónicos
Si bien la tecnología de transporte de Ferag ha funcionado a la perfección desde el primer momento —al fin y al cabo, deniway es todo un clásico de la empresa suiza—, los ingenieros del proyecto de la planta de Bisleri en Bombay tuvieron que hacer frente a una serie de retos antes de poner en marcha el sistema.
Puede que el mayor de ellos fuera los plazos tan ajustados, que implicaba entregar e instalar los módulos de deniway en medio de la estación de lluvias monzónicas: una condición climática extremadamente adversa para quienes no están acostumbrados a este tipo de clima. “Lo aceptamos con deportividad y calma. Después de todo, eso nos permitiría demostrar al cliente que nuestros sistemas son lo suficientemente potentes para resistir climas calurosos y húmedos y funcionar correctamente bajo esas condiciones”, apunta Kawal Arora, director gerente de WRH Global India, la filial de comercialización de Ferag participante en el proyecto.
La instalación de los componentes del sistema en el almacén de varias alturas tampoco planteó problemas. Desde el principio, Ferag hizo los ajustes necesarios en deniway para facilitar su integración en los sistemas de Bisleri. No hay que olvidar que por la naturaleza sumamente modular de los sistemas de Ferag, las instalaciones también se pueden adaptar y ampliar con facilidad.
Sin rastro de suciedad: deniway es apto para los productos alimenticios
Otro importante factor, sin duda, inclinó la balanza a favor de la tecnología de Ferag: la higiene. Como fabricantes de bebidas, en Bisleri se da una especial importancia no solo a la alta calidad de los productos, sino también a la higiene en la producción. El agua procedente de manantiales o ríos pasa por un proceso de tratamiento con ozono de varias etapas para destruir gérmenes y bacterias, se filtra varias veces y, luego, se eliminan los minerales dañinos por ósmosis inversa. A continuación, se aportan de nuevo los minerales beneficiosos en su justa medida. Cuatro máquinas de alta velocidad embotellan el agua mineral resultante siguiendo rigurosos controles. Por lo demás, los tapones de las botellas y garrafas se desinfectan por ozonización durante el proceso de embotellado.
Ni que decir que el sistema también debe cumplir con esos estrictos requisitos. El transportador lleva las botellas vacías y recién lavadas a las máquinas de llenado por una tercera espiral deniway, que tiene que permanecer en todo momento limpia para esta operación tan delicada. El mismo sistema se aplica a las unidades periféricas de las máquinas de embotellado. Tanto el empujador electromecánico que carga los productos en la sección de la cinta deniway descendente como la línea en sí tienen que ser aptas para el transporte de productos alimenticios envasados.
En resumidas cuentas, Bisleri solo contemplaba la posibilidad de una tecnología de transporte de alta calidad, sin desgaste y cuyos componentes se pudieran limpiar con facilidad. Y había que evitar a toda costa los sistemas que requieren lubricantes. La tecnología deniway cumple con creces todos esos requisitos. De no ser así, otros productores del sector de la alimentación como Nestlé y Mondelez no llevarían tanto tiempo utilizándolo.
Al final de la línea, en las plantas inferiores de almacén y expedición, se hace patente otra ventaja decisiva del sistema. En palabras de Arora, la tecnología de deniway es inigualable por ser “una de las interfaces más eficaces entre las primeras fases de producción y la paletización que se encuentran actualmente en el mercado”.
Video de la instalación: https://www.youtube.com/watch?v=SwLYYVdyyyM&t=
Acerca de Bisleri
La denominación 'Bisleri' viene del emprendedor italiano Felice Bisleri, propietario de la marca de agua mineral Sorgente Angelica en Nocera Umbra (Perugia). En 1965, Bisleri expandió su negocio en la India. Pasados cuatro años, la empresa india de productos alimenticios, Parle Group, se hizo cargo de la empresa. Desde entonces, ha experimentado un crecimiento sin precedentes, siendo, con diferencia, la marca líder en bebidas refrescantes del subcontinente indio. Hace tan solo unos meses, coincidiendo con la celebración de su 50 aniversario, Bisleri abrió una modernísima planta de embotellado en su sede de Bombay. La empresa se siente especialmente orgullosa de ello, pero también de ser “el primer y único productor mundial de agua mineral en línea vertical”.
Acerca de WRH Global Ibérica
WRH Global Ibérica, fundada en 1989, es una de las 20 filiales con la que el Grupo Walter Reist Holding, con sede en Hinwil (Suiza), desarrolla localmente todas sus áreas de negocio para España y Portugal. WRH es líder mundial en la fabricación e integración de sistemas automatizados en la Industria Gráfica, a través de su división FERAG. Desde 2008, la compañía ha iniciado un proceso natural de diversificación de negocio hacia el Sector de la Intralogística, con soluciones de transporte y clasificación altamente innovadoras, flexibles y muy eficientes energéticamente, consolidadas sobre la base tecnológica y experiencia en la Industria Gráfica. La compañía tiene un volumen de facturación de más de 300 millones de francos suizos (273 millones de euros), y emplea a más de 1.000 personas, contando con 2 plantas de fabricación en el país helvético.