Una impresora 3D con parámetros industriales
Tradicionalmente englobadas dentro del Rapid Prototiping (RP), las técnicas de ‘additive manufacturing’ (AM) se pueden clasificar en función del estado inicial del material utilizado para la fabricación del prototipo: basados en líquidos, sólidos o polvo. Los sistemas RP cuyo estado inicial del material es el líquido consiguen a través de curing (curado) que el líquido sea convertido a estado sólido, como sucede en los Stereolithographt Apparatus (SLA). Los sistemas RP basados en sólidos engloban todas las técnicas con materiales de partida en forma de hilo, rollo, láminas, polvo, etc. Técnicas como por ejemplo la sinterización selectiva por láser (Selective Laser Sintering o SLS), utilizan un láser para fundir pequeños granos de plástico, cerámica, vidrio, metal y otros materiales en capas de una estructura 3D.
Junto con la evolución de los materiales empleados y la reducción de su coste, el vencimiento de algunas patentes relacionadas con estas tecnologías contribuye a la gran expansión que estas tecnologías están experimentado en la actualidad. De entre ellas, la impresión 3D, directamente relacionada con la tecnología FDM (Fusion Deposition Modeling), se está haciendo tremendamente popular. A ello contribuye el movimiento ‘RepRap’ que, además de mantener un código de control abierto para los controladores, preconiza el principio de ‘self construction’ a través del cual una impresora puede construir piezas constitutivas de una nueva impresora.
Requisitos industriales para una impresora 3D
Una de las limitaciones de la tecnología FDM es que necesita una calibración muy precisa para que el resultado de las piezas sea el deseado. Las soluciones más populares (RepRap) se basan en tecnología de control en bucle abierto, a través del empleo de motores paso a paso, que pueden afectar a la calidad a medida que se produzcan pequeños cambios en la calibración.
Además, dado que estas máquinas construyen piezas a través de la superposición de capas sucesivas, un error en una capa inferior inevitablemente se propagará en las capas siguientes. El resultado de un fallo de calibración característico es la inclinación indeseada de una cara vertical. Este problema acarrea la frecuente necesidad de desechar piezas mal construidas y la recalibración de la máquina a través de la construcción de piezas de prueba. Todo ello supone un gasto de material, energía y tiempo. Además, con áreas de trabajo y velocidades elevadas aumenta la incidencia de la propagación de errores de posicionamiento debidos a defectos de calibración.
Estos eran, es esencia, los requisitos de la impresora 3D diseñada por el profesor y alumno del Master de Mecatrónica de la Universidad de Vigo para participar en el primer concurso MachineStruxure de Schneider Electric. El alcance del proyecto incluye el diseño mecánico, eléctrico y del software para una impresora de piezas de plástico PLA en tres dimensiones. El objetivo es crear una máquina capaz de realizar piezas de gran tamaño sin defectos provocados por la propagación de errores de trayectorias y con un consumo de tiempo lo más ajustado posible a las nuevas dimensiones. Esta máquina ha de solventar la problemática de calibración y des-calibración a través de la utilización de tecnología de posicionamiento en lazo cerrado que se traduce en el empleo de servomotores. El uso de servomotores, además, propicia el posicionamiento rápido, lo que permite reducir tiempos a la hora de fabricar varias piezas en una misma tanda en un uso claramente industrial. De esta manera, se pretende reducir la generación de piezas rechazadas y de piezas fabricadas para asistencia en las fases de recalibración. Todo ello redunda en un ahorro de costes de material y de consumo de energía y tiempo. Además, la impresora 3D está concebida para permitir el cálculo exacto y automático del coste que supone la realización de cada pieza.
Estructura de la máquina
Desde el punto de vista mecánico, la máquina es una configuración de tres ejes cartesianos (Schneider Electric), más un cuarto eje síncrono respecto a la velocidad de avance y que se encarga de la extrusión del hilo de plástico.
La estructura cartesiana realiza movimientos interpolados en los ejes XYZ. Esta estructura se encarga de posicionar y mover el extrusor del material, que consta de un eje y un generador de calor (resistencia) controlado para mantener una temperatura constante (con la finalidad de la fundición del hilo de plástico, 210º para el hilo de PLA). Dicho hilo de plástico está enrollado en una bobina y es desenrollado por la acción de un cuarto motor (Figura 1).
Cada uno de los ejes XYZ son movidos por servomotores (Schneider Electric) que están conectados a los correspondientes ServoDrives. El extrusor utiliza un servomotor tipo ICLA (motor con servo integrado). Todo ello conectado a través de CanMotion y CanOpen a un controlador LMC058 de Schneider Electric. Completan el hardware los dispositivos para el control térmico del extrusor, un medidor de consumo eléctrico conectado a través de Modbus, y una pantalla táctil para el IHM de control de impresión.
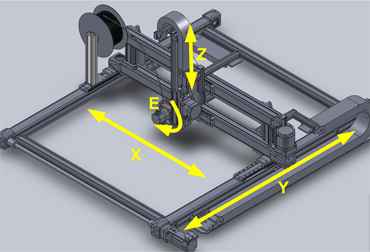
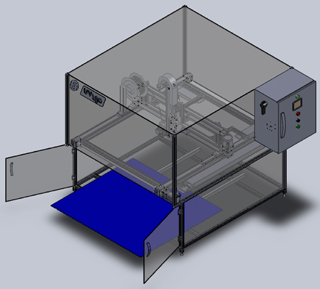
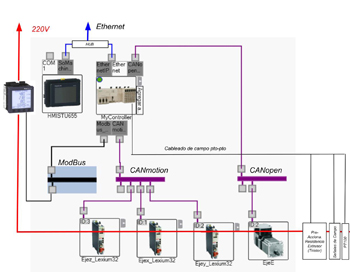
Control de la máquina
Con esta configuración se implementa una fabricación o impresión en capas (layer manufacturing), que consiste en ir depositando el hilo fundido en una serie de capas paralelas. Cada capa se realiza a través de movimientos interpolados 2D (con los ejes X e Y) del extrusor, de tal forma que se realizan trayectorias que delimitan el contorno de esa pieza en esa cota Z y de trayectorias en el interior con una forma y un espaciado que depende de la robustez que se le quiera dar a esa capa. Típicamente, por ejemplo, las primeras capas y últimas tienen una densidad del 100% mientras que el resto se espacian de acuerdo a un parámetro inicial de factor de robustez o densidad deseado, de forma que el interior de la pieza se tiende a estructurar en forma de celdas a fin de ahorrar en material y tiempo de impresión.
La mayoría de las máquinas de RP trabajan con diseños en forma de ficheros STL (Triangulation tessellated). Un modelo STL contiene un conjunto de superficies planas triangulares. La gran mayoría de sistemas CAD 3D comerciales son capaces de convertir modelos de sólidos en este formato. A partir de esta representación, otros algoritmos convierten el diseño en capas (Slice) horizontales paralelas (secciones horizontales), y trayectorias lineales para recorrer la superficie en código G (ISO). Aplicaciones como ‘Cura’ (de acceso libre), permiten realizar este tipo de conversión.
Este fichero de trayectorias en código G es finalmente transferido al controlador. Este controlador será el encargado de ejecutar la interpolación cartesiana en tres ejes XYZ según las trayectorias descritas en el fichero. Además, el controlador sincroniza el movimiento del cuarto eje (eje del extrusor) que se mueve a velocidad constante dependiendo de la trayectoria que se esté ejecutando en cada momento.
Tanto este programa de control como la interfaz IHM se han desarrollado con la plataforma SoMachine de Schneider Electric. El sistema se completa con una aplicación de configuración y gestión para PC, quese conecta vía OPC con el controlador. En este PC está, además, la aplicación de preprocesado para convertir el diseño 3D en un código ISO ejecutable.
Eficiencia Energética
Uno de los requisitos de la máquina es el registro del consumo de tiempo, energía y materia prima que se consumen en la realización de cada pieza con dos objetivos: poder realizar una ‘facturación de la fabricación de pieza’ ajustada a estos parámetros, y poder analizar el resultado que, sobre estos parámetros, tengan las decisiones tomadas en la fase de diseño y preparación, para así poder decidir el diseño de pieza óptimo contando con el criterio de coste de fabricación.
Por lo tanto, además del registro del tiempo empleado y del material consumido, se registrará el consumo energético total a lo largo de la fabricación de una pieza, y para ello se emplean los FB’s de la librería de Eficiencia Energética de Schneider Electric. Los valores acumulados de todos estos parámetros se ponen a disposición del PC de diseño y gestión al final del proceso. Con los recursos de eficiencia energética proporcionados por el entorno de desarrollo, no solamente es posible obtener un valor del consumo total, sino también acceder al consumo individual por eje y por trayectoria. Esta es sin duda la funcionalidad que, desde la perspectiva universitaria, será más interesante ya que será la que se utilice en el marco de la línea de investigación del Departamento de Ingeniería de Sistemas y Automática de la Universidad de Vigo relativa a ‘nuevas estrategias y algoritmos de control para la impresión 3D’.
El concurso
En 2013, Schneider Electric España convocó la 1ª Competición MachineStruxure, destinada a estudiantes y profesores de ingeniería de universidades españolas. Se proponía el diseño de una máquina empleando la nueva herramienta de desarrollo de sistemas de automatización SoMachine de Schneider Electric y, entre otras cosas, se valoraba el empleo de los recursos para eficiencia energética disponibles a través de dicho entorno de desarrollo. Finamente, de entre once propuestas resultó elegido el proyecto ‘Diseño de un impresora 3D con parámetros industriales’, firmado por Julio Garrido Campos y Jaime Prado Cambeiro, profesor y alumno respectivamente del master de mecatrónica impartido en la Escuela de Ingenieros Industriales de Vigo.
El concurso, dotado con un premio de 15.000 euros en equipamiento para la implantación de un aula ‘MachineStruxure’, y 4.000 euros a disposición del equipo ganador para implementar, de acuerdo con Schneider Electric, la solución ganadora. Esto ya se ha traducido en el aula MachineStruxure del Departamento de Ingeniería de Sistemas y Automática de la Universidad de Vigo, que ha sido equipada con ocho puestos formados, respectivamente, por un controlador LMC058 y un HMI (y sus correspondientes licencias SoMachine), además de una configuración cartesiana de ejes Schneider con los correspondientes servomotores y servodirives (tres LXM32). Estos ejes constituyen la planta de prueba para los ocho puestos, pero son también la base sobre la que se construirá la impresora con el resto de la dotación del premio, en lo que ya están trabajando conjuntamente el equipo ganador y Schneder Electric España.
El proyecto ‘RepRap’
El proyecto ‘RepRap’ (de replicating rapid prototyper) propone el desarrollo abierto de impresoras 3D que pueden imprimir la mayoría de sus propios componentes. Todos los diseños y software generados por el proyecto son distribuidos libremente. Su capacidad de autorreplicación está contribuyendo a su popularidad, dado que estas impresoras pueden imprimir elementos mecánicos para generar a su vez nuevas impresoras.
El proyecto nació en 2005 en la Universidad de Bath (Reino Unido) de la mano del profesor Adrian Bowyer. Ese año se puso en marcha el correspondiente blog, y a partir de 2007 empezaron a implementarse las primeras impresoras. Desde entonces éstas no han dejado de crecer y extenderse. La impresora RepRap usa la tecnología FFF (Fuser Filament Fabrication), donde un hilo de plástico (ABS o PLA, por ejemplo) es calentado hasta su punto de fusión en un cabezal o ‘extrusor’, conformando la pieza capa tras capa. Como plataforma de control se emplea el popular Arduino con placas adicionales para controlar los motores paso a paso y el extrusor.
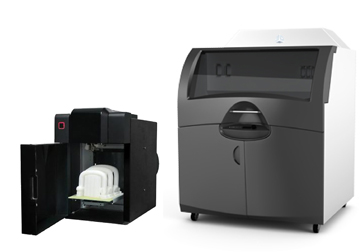
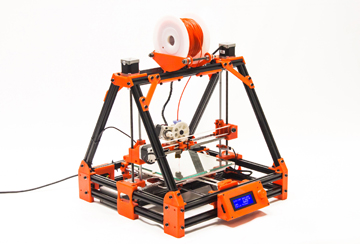
Figura 5: Impresora 3D RepRap.
Referencias:
- Protectia, patentes y marcas. Art. ‘Caduca la patente clave para impresión 3D’. Francesca Nandolini. Marzo 2014
- Machine design. Art. ‘How designer can get the most out of additive manufacturing’. Ziad About, vicepresidente y director general de Quicpart Solutions. Octubre 2013.
- RepRap. Sitio official: http://reprap.org/wiki/RepRap