Entrevista a Fernando Burguera, responsable del Área de Ingeniería Avanzada de Batz
Batz trabaja de forma directa para prácticamente todos los principales OEM de automoción del mundo en alguna de sus unidades de negocio. Y uno de sus atractivos es su apuesta por la reducción de peso. En esta línea se encuentran soluciones como las pedaleras, fabricadas principalmente en composite. Fernando Burguera, responsable del Área de Ingeniería Avanzada de la compañía, explica a Plásticos Universales en qué consisten y cuáles son los retos a la hora de abordar su diseño.
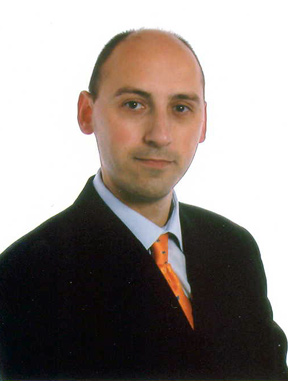
Fernando Burguera, responsable del Área de Ingeniería Avanzada de Batz.
Ustedes han desarrollado una pedalera fabricada en composite, lo que supone una gran evolución…
Así es. Las pedaleras han estado presentes en los vehículos de motor desde su origen, y siempre con una funcionalidad clara y definida. Aunque para ser precisos, esto último no es del todo correcto, puesto que existen determinadas funciones añadidas que se pueden implementar en las pedaleras.
¿Por ejemplo?
Sistemas de seguridad para evitar daños a las extremidades inferiores de los usuarios en caso de colisión, sistemas de pedales ajustables que se desplacen y adapten a la ergonomía del usuario, etc. Por tanto, si la función principal ya está definida y es conocida y común a todos los vehículos, lo que se requiere es una mejora en peso y coste para contribuir a la mejora del vehículo completo.
¿De qué manera?
El acero con el que se hacen tradicionalmente los pedales es fiable y conocido, pero también muy pesado y, según qué procesos tomen parte, caro. El reto del diseño en plástico consiste en conseguir emular las propiedades de rigidez y resistencia de sus homólogos de acero, pero manteniendo una ventaja importante en peso y coste. Hay que tener en cuenta que cuando hablamos de pedaleras hablamos de la pieza más crítica del vehículo, la que nunca querríamos que fallara: el pedal de freno. Las exigencias para él, tanto en rigidez como en resistencia a la rotura, son brutales.
Lógico…
Tradicionalmente las pedaleras se fabrican con piezas de acero o metal estampadas y unidas o soldadas entre sí. Si se sustituyera cada pieza individualmente por otra pieza de plástico, seguiríamos necesitando un proceso de ensamblado y, con toda seguridad, la competitividad se reduciría notablemente. Sin embargo, el diseño de piezas de plástico permite un alto grado de libertad de diseño e integración de piezas en una sola.
¿Realmente aporta las mismas prestaciones que el metal en cuanto a resistencia y seguridad?
Hay un factor importante a recalcar aquí, aunque pueda parecer obvio: el diseño en plástico de piezas críticas mecánicamente nunca puede ser similar al diseño realizado en acero o metal. Las propiedades específicas del mejor de los plásticos están lejos de lo que se puede obtener con acero, sobre todo en rigidez.
¿Entonces?
Hay que plantearse el reto de sustituir globalmente una pedalera basada en acero o metal por una basada en plástico, no la sustitución de cada uno de sus componentes. Por tanto, ¿podemos hacer las mismas piezas actuales de acero en plástico manteniendo las propiedades? No. ¿Podemos, sin embargo, sustituir una pedalera basada en acero por otra basada en plástico manteniendo las propiedades? Sí, con un diseño adecuado.
También hay que puntualizar que no toda la pedalera va a ser de plástico, todavía hay reductos que deben usar metales, debido a sus altos requerimientos específicos o porque la geometría particular de una pedalera determinada no permita el espacio necesario para un diseño en plástico.
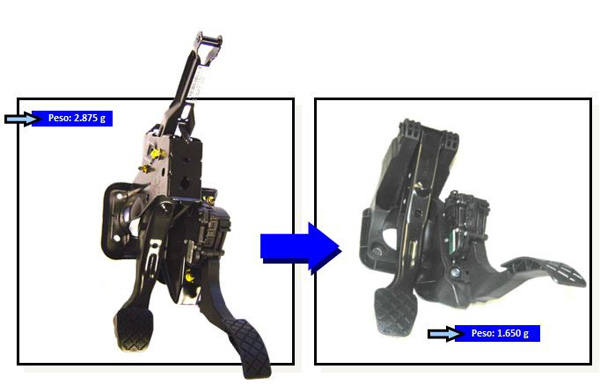
¿Qué tipo de plástico es apropiado para esta aplicación?
Cuando se habla de utilización de plástico en pedaleras hay que tener en cuenta que la función es fundamentalmente estructural, no estética. No estamos tan mediatizados por el aspecto que debe tener la pieza al final, como por el hecho de que tenga un comportamiento mecánico muy alto. Los materiales deben tener cargas de fibra que consigan darle esas propiedades. Habitualmente se usan poliamidas y polipropilenos con porcentajes de fibra de vidrio que oscilan entre el 30% y el 50%. Otras matrices no se utilizan tanto. Las fibras de carbono, vegetales, etc. tampoco tienen una presencia significativa. Sin embargo, la hibridación plástico-metal es una solución que puede resultar altamente competitiva, según en qué casos.
¿En qué medida influye el material en el diseño de una pedalera? ¿Difiere mucho éste según el material empleado?
En Batz intentamos trabajar con materiales base lo más económicos posible para ganar en competitividad. Preferimos usar PP en lugar de PA si conseguimos un diseño que cumpla con los requerimientos, lo cual no es fácil. Estamos en automoción y el OEM nunca regala nada. Un PP cargado con un 30% de fibra de vidrio, por ejemplo, tiene una densidad un 20% menor que su equivalente en PA. Dado que el precio por kilo puede estar en torno al 75% del precio de la PA, nos encontramos que un mismo diseño —y por tanto un mismo volumen— en PP+30GF es hasta un 40% más económico que el mismo diseño en PA+30GF. Claro que las propiedades mecánicas también son inferiores, luego hay que analizar si es factible desarrollar la pieza con este material optimizado.
¿Puede poner un ejemplo?
Sí, un ejemplo de optimización en función del material es el soporte de una pedalera, que puede ser una pieza notablemente masiva, dentro del área en que nos movemos. La función de un soporte es, como su mismo nombre indica, soportar el resto de los componentes, sobre todo los pedales, y las cargas máximas a que están sometidos. El caso más extremo de carga abusiva se produce sobre el freno, para garantizar que nunca va a fallar en uso normal. Luego, la zona de mayores tensiones en el soporte es justamente el alojamiento del pedal del freno. Si las tensiones producidas en el soporte en esa zona son excesivas para un PP con fibra, por ejemplo, una primera solución consistiría en migrar el material del soporte a PA, por ejemplo, pero esto implica cambiar el material no sólo en la zona del pedal de freno, que es la que está más cargada, sino también en todo el resto del soporte, sobredimensionándolo y sobrepreciándolo excesivamente. Aquí es donde hay que buscar soluciones más imaginativas que simplemente esa migración al material superior: buscar diseños, hibridaciones o incluso procesos alternativos para intentar mantener la competitividad sin alterar el material base.
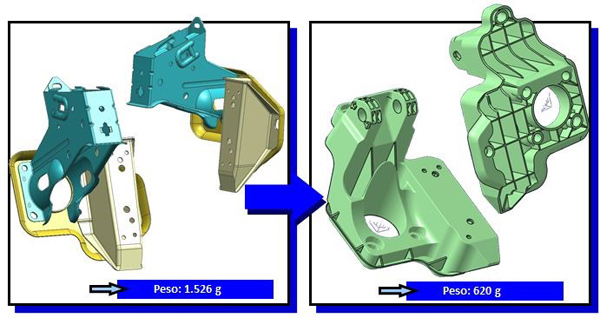
¿Es ése el principal reto al que se han enfrentado a la hora de sustituir el metal por el plástico en las pedaleras?
Probablemente, nuestro principal reto no tiene nada que ver con cuestiones técnicas, sino con aspectos más psicológicos. “Entiendo tus argumentos técnicos, pero ¿tú de qué querrías que fuera el freno de tu coche, de plástico o acero?”. Esta pregunta, que se nos ha planteado en algunos OEM, es quizás lo más complicado de combatir.
Entiendo…
Además, desde épocas inmemoriales, los vehículos llevan pedales de acero y, en general, no dan problemas. Ciertamente, hacer algo más ligero y más económico es interesante, pero puede generar una incertidumbre, una sensación de inseguridad, de salto al vacío que lleve al OEM a plantearse si merece la pena el riesgo. Por otro lado, el usuario último no va a percibir el cambio, no se le va a vender en la publicidad que los pedales son de plástico, porque, de hecho, podría ser hasta contraproducente para la imagen del vehículo.
¿Y en cuanto a retos técnicos?
Para ser sincero, cuando empiezas a trabajar con plásticos para sustituir acero o metal es cuando te das cuenta de lo fácil que resulta diseñar con metales. Diría que el punto principal a tener en cuenta es la gran influencia que tiene el proceso en las características finales de las piezas de plástico. Ciertamente, el acero laminado tampoco es totalmente isotrópico, por ejemplo, pero la diferencia de obviar esa anisotropía no suele ser importante, mientras que en el plástico sometido a tensiones críticas es vital, así como controlar otros aspectos resultantes de la producción, como las líneas de soldadura. Además, factores como el envejecimiento o las relajaciones de tensiones, que en el acero no se contemplan, ganan una importancia capital.
¿Qué aspectos se han de tener en cuenta a la hora de diseñar las pedaleras?
La pedalera está localizada en un sitio de difícil acceso dentro del vehículo, habitualmente entre el firewall, la columna de dirección, el HVAC (sistema de climatización) y demás elementos adyacentes. También influye notablemente la localización de los elementos actuados, como servofreno y cilindro hidráulico del embrague. Muchos de estos elementos tienen que poder recibir mantenimiento, lo que hace que el espacio disponible para la pedalera esté siempre comprometido. Además, las funciones adicionales que cada OEM quiera implementar van a condicionar el diseño, como el sistema de seguridad ante colisiones, las uniones rápidas a servofreno y cilindro de embrague, etc. Con todo ello lo primero que se ha de realizar es apreciar el espacio disponible y la geometría admisible para los pedales.
¿Geometría?
Sí, dicha geometría nos va a dar una estimación de los materiales utilizables. Por ejemplo, los pedales de embrague y acelerador suelen hacerse en PA de forma habitual, pero en algunos casos de formas especialmente estrechas o retorcidas, la única solución es volver al metal. Posteriormente, hay una iteración de diseño-optimización, que en el caso de Batz, se apoya ventajosamente en el uso de herramientas contrastadas de optimización topológica.
¿Con qué objetivo?
Reducir peso y por tanto coste de materia prima, pero es el ingeniero de producto junto con el de procesos el que tiene que estudiar las opciones utilizables en cada caso y guiar las iteraciones de diseño. Hay más detalles que tienen que ver con los parámetros referentes a las sensaciones percibidas por el usuario, sistemas de asistencia, ratios de transmisión, etc., pero esa es otra historia que no tiene tanto que ver con los materiales en general.
El sector presta especial atención a la reducción del peso de los vehículos. ¿Qué otras partes tradicionalmente feudos del metal se podrán sustituir en un futuro por plástico?
Batz ha desarrollado una cultura de aligeramiento concentrada en sus productos actuales. Esta cultura hace que estemos investigando continuamente en materiales alternativos (composites, magnesio, etc.), procesos novedosos (WIT, etc.) y, últimamente, en nuevos productos en los que aplicar todas esas tecnologías desarrolladas. En la unidad de negocio Batz Lightweight Technologies se producen actualmente frontends y deflectores aerodinámicos totalmente de plástico, en otra muestra de pieza tradicionalmente metálica migrada a materiales plásticos. Este mismo movimiento se puede aplicar a otros conjuntos, tanto a niveles de mecanismos como de piezas estructurales, y se aprecia que la irrupción de los vehículos eléctricos con su necesidad de aligeramiento para mejorar la autonomía y para compensar el peso de las baterías está empujando en este sentido. Pero hay que tener en cuenta que para conseguir entrar en una nueva función del vehículo el ahorro de peso y coste es tan sólo uno de los factores a tener en cuenta.
¿En qué proyectos trabaja Batz en la actualidad?
En tecnologías que nos permitan conseguir piezas más económicas aun usando procesos más complicados. Concretamente, estamos investigando piezas plásticas con tecnología WIT (Water Injection Technology) para permitir una distribución del material más resistente y rígida a igualdad de peso, o más ligera a igualdad de resistencia. También se está trabajando en piezas híbridas metal-plástico, con la óptima relación entre ambos materiales para conseguir el ratio perfecto resistencia/rigidez y peso/precio. Otra área de trabajo son materiales alternativos, tanto en cuando a biopolímeros basados en PLA con fibras naturales, como en cuanto a textiles de fibra continua. Asimismo, la expansión de todo este conocimiento generado al resto de los productos actuales de Batz, y a nuevos productos en desarrollo como reposacabezas activos, sistemas de elevación de rueda de repuesto, palancas de cambios, etc.
La apuesta de Batz
Batz, S. Coop. es una cooperativa encuadrada en el Grupo Mondragón, cuyos headquarters se encuentran en Igorre (Bizkaia). La compañía comenzó su andadura hace 50 años produciendo troqueles de estampación. En el año 1982 se creó una nueva unidad de negocio denominada Sistemas de Automoción, dedicada a producir componentes para vehículos, mayoritariamente metálicos debido a su cultura previa. “Es en esta unidad donde se engloba el área de conjuntos de pedales. Una evolución acelerada en los últimos diez años nos ha llevado a globalizar la actividad, hoy en día tenemos un total de 14 plantas productivas alrededor del mundo, e incluso diversificar hacia otros mercados, como Energía, pero también a profundizar en los retos que nos plantea la evolución de nuestros productos tradicionales”, explica Burguera. La empresa trabaja principalmente en automoción, y eso implica forzosamente una investigación permanente hacia la reducción de peso y coste. Y ahí es donde los composites tienen un camino evidente a recorrer. “Nuestra apuesta es firme hasta el punto de que recientemente se ha creado Batz Lightweight Technologies absorbiendo y potenciando otra actividad que fue creada ya en 1992, dedicada a piezas estructurales y aerodinámicas en materiales compuestos. Toda esta diversificación de actividades hace que debamos hablar actualmente del Grupo Batz, en el cual trabajamos actualmente del orden de las 1.500 personas”, apunta.