“Las tecnologías composites pasarán de los vehículos nicho a las series medias y, en un futuro, a la gran serie”
Entrevista a Javier Martínez Cue, director de I+D de FPK Lightweight Technologies
Partner y proveedor de los principales fabricantes de automóviles, FPK Lightweight Technologies es una empresa vasca que sabe muy bien que el futuro del sector pasa por aligerar el peso de los vehículos. Nuevos materiales y productos y avanzados procesos son los tres pilares de esta compañía del Grupo Batz, cuyo director de I+D, Javier Martínez Cue, relata en esta entrevista cómo ha evolucionado la sustitución de piezas de metal por plástico en esta industria, y explica las ventajas medioambientales y económicas que supone aligerar el vehículo.
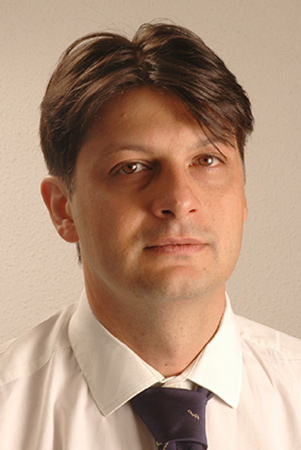
Javier Martínez Cue, director de I+D de FPK Lightweight Technologies.
FPK diseña y suministra componentes estructurales y aerodinámicos en composite o en plástico reforzado…
Sí, queremos ayudar a nuestros clientes a reducir emisiones bien a través del ahorro de peso o bien a través de la mejora aerodinámica. FPK es una línea de negocio del grupo Batz y estamos enmarcados en la corporación Mondragón. Actualmente contamos con 3 ubicaciones, en el País Vasco, en Alemania y en Brasil. La idea es industrializar nuestros productos en nuevas ubicaciones donde la línea de negocio Batz Sistemas cuenta actualmente con plantas de producción.
A grandes rasgos, ¿por qué se persigue conseguir vehículos más ligeros?
Existe una relación directa entre el peso y el consumo de combustible. Se trabajan varias líneas para reducir el consumo de combustible y, por tanto, de emisiones de CO2. Una de ellas es la mejora de la eficiencia de las motorizaciones y la otra es la mejora aerodinámica del producto. Además, una tercera línea sería el aligeramiento de peso, que cada día cobra más importancia.
¿Es el plástico la mejor alternativa?
El composite es una de las alternativas, pero también se trabajan aleaciones ligeras o aluminios, entre otras. Pero, sin duda, el composite o plástico reforzado poco a poco gana terreno y tiene un importancia creciente, al combinar un alto grado de libertad de diseño con la ligereza de los materiales.
¿Qué le queda por conquistar al plástico en el vehículo?
La estructura del coche, aunque ya tenemos ejemplos en el mercado: el modelo i3, un coche eléctrico de BMW que tiene su monocasco autoportante elaborado en carbono, un termoestable reforzado con fibra de carbono. A día de hoy, esos materiales y tecnologías tienen precios muy altos, por lo que están ligados a vehículos nicho, a series cortas, como el i3. Pero a medida que evolucionen las tecnologías composites y, sobre todo, se reduzcan los precios de las materias primas, veremos como van pasando de los vehículos nichos a las series medias y, en un futuro a largo plazo, a la gran serie.
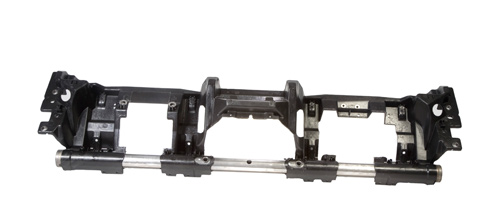
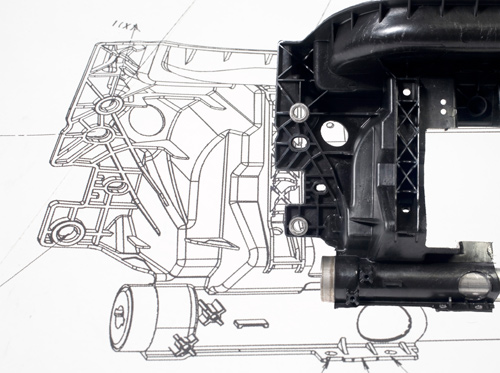
Cockpit carrier.
Hay quien afirma que llegará un momento en que incluso todo el acristalamiento será de policarbonato. ¿Qué opina al respecto?
Pienso que se logrará pero que costará convencer a los fabricantes. Esta es una de las principales dificultades que también encontramos en la parte estructural. Para una pieza estructural clave, un componente de seguridad o muy técnico, el hacer una primera evolución del metal al plástico reforzado, supone un camino de muy largo recorrido porque hay que demostrar muy bien que funciona.
Demuestre usted que funciona. ¿Cómo defendería el plástico frente a otro material resistente?
El plástico cumple los requerimientos y especificaciones ideales para lograr un menor peso. En cuanto a la función mecánica, la ventaja se consigue a través de la libertad de diseño. Aunque las propiedades mecánicas unitarias del plástico sean inferiores al metal, se compensa con una rigidez equivalente, incluso superior, y una buena resistencia, a través de la geometría o el diseño, entre otras propiedades.
¿Ha influido la proliferación del vehículo eléctrico en la búsqueda de nuevas fórmulas que aligeren las piezas?
Sí, en varios aspectos. En primer lugar, se han presentado oportunidades para componentes nuevos relacionados con el almacenamiento de energía, soportes de batería, entre otros, adaptados a la arquitectura del vehículo eléctrico. La segunda cuestión es que el ahorro de peso es aún más importante que en los vehículos de combustión interna porque claramente en éste, el peso va contra las prestaciones. Ahí la receptividad de los fabricantes de coches a introducirse en la búsqueda de materiales con tecnologías ligeras es mayor.
Entiendo…
Por otro lado, vemos que por el momento las oportunidades para el coche eléctrico siguen siendo para volúmenes muy pequeños y que, en algunos casos, lo que se ha hecho es “tunear” la arquitectura de un coche, de una motorización convencional, para introducir el motor eléctrico y el almacenamiento de energía eléctrica. Creo que en el futuro habrá arquitecturas pensadas para series específicas más grandes, por lo que puede que se presenten nuevas oportunidades de materiales compuestos.
Entonces, ¿qué futuro augura para el vehículo eléctrico?
Los especialistas creemos que su implantación va a ser muy lenta. Hablan de porcentajes y volúmenes aún pequeños a partir del año 2020. Será un camino que se dará bastante más despacio de lo que se pronosticó hace diez años.
¿Por la poca autonomía de la batería?
Sí, y también por las infraestructuras, sobre todo el vehículo eléctrico puro, ya que es muy dependiente de los puntos de carga y no es fácil dar con una solución.
También existe una mayor concienciación por el respeto del medioambiente. ¿Ha propiciado el uso de nuevos materiales que permitan ser reciclados?
Existe una relación directa entre el ahorro de combustible y las emisiones de CO2. Hay un mercado también de plásticos reciclados bastante consolidado en Europa para materiales commodities como el polipropileno y la poliamida. Con el uso de materiales reciclados el fabricante de coches puede obtener una reducción de costes interesante y se contribuye a la mejora medioambiental.
Uno de los ejes decisivos de innovación en la industria plástica para aplicaciones automóviles es el desarrollo de materiales. ¿Cuáles son los más empleados y con cuáles trabaja FPK?
A día de hoy, el más empleado es el polipropileno, el commodity más habitual, más barato, más abundante en cualquier mercado y, además, un material muy amigable a la hora de transformarlo. Le sigue la poliamida en nuestro campo de piezas estructurales y funcionales.
Luego entraríamos en los plásticos técnicos, en los cuales hay un potencial de ahorro de peso mucho mayor, aunque su aplicación es sólo viable en aquellas aplicaciones con un mayor requerimiento, debido al precio de la materia prima.
Ustedes ofrecen soluciones de componentes estructurales ligeros para el fronted carrier, cockpit carrier, la cavidad de rueda de repuesto y la caja de batería. ¿Qué propone FPK y qué ventajas se obtienen en cada pieza?
Nosotros ofrecemos soluciones en varias líneas. Estamos trabajando en la búsqueda de materiales de mejores prestaciones mecánicas aplicables a tecnologías actuales ya industrializadas. En base a estas mejoras podemos hacer viables determinados componentes o productos. También trabajamos con termoplásticos técnicos y con fibras de carbono.
¿Y en el campo de la tecnología del plástico?
Por un lado, pretendemos ampliar las tecnologías industrializadas generando nuevas variantes tecnológicas que aporten ventajas en el comportamiento mecánico del producto con la integración, por ejemplo, de refuerzos de fibra continua en el proceso de inyección. Son, en principio, adaptaciones de tecnologías existentes y, por lo tanto, de relativa fácil implementación en la serie.
También desarrollan nuevas tecnologías…
Sí, trabajamos en el desarrollo de tecnología innovadora, con un horizonte a medio plazo, que permita un mayor nivel de integración de funciones de las piezas, una mayor complejidad y también abaratar el producto, pudiendo integrar la fabricación de la materia prima en el proceso y, en definitiva, reducir el coste del producto final.
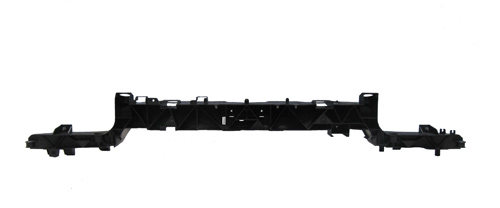
¿Trabajan con bioplásticos?
Los conocemos pero a día de hoy los encontramos muy caros en comparación con los plásticos convencionales. Son bio y no derivados del petróleo, pero todavía está por demostrar si el impacto medioambiental que genera la producción de sus materias primas mejora el de los materiales convencionales. No obstante, el mayor hándicap que encontramos es que de momento son caros en comparación con los plásticos convencionales.
No están en su línea de actuación…
No, sin embargo, si bajo demanda de algún fabricante de vehículos, tenemos que utilizar un polímero de origen bio, las tecnologías están preparadas. Realmente, hay materia prima, sobre todo poliamidas, que se puede transformar por inyección convencional, pero su coste es elevado.
¿Tendría sentido un plástico biodegradable en el automóvil?
Hasta ahora nos han pedido que los componentes no fallen y garantizar la vida de servicio en el vehículo. Parece un contrasentido decir que la pieza se pueda desintegrar. Nosotros creemos más en el reciclado, como manera de minimizar el impacto ambiental, así como en diseñar los componentes para que sean mas fácilmente reciclables.
En algunos casos, la pieza se compone de varios plásticos de diferente tipología. ¿No plantea un problema a la hora de reciclarlo después?
Habitualmente se compone de un único plástico. Hay una minoría de piezas que son bimaterial y tienen elementos metálicos. Éstas se ensamblan y atornillan y, en ocasiones, se sobreinyectan. Reciclar ese tipo de componentes es un reto. Separar la chapa del plástico es viable y no hace falta una tecnología complicada para ello, sin embargo, económicamente no siempre es rentable la separación de materiales en estos productos, por eso en ocasiones este tipo de componentes complejos acaban en el vertedero. La tendencia —no sólo por el ahorro de coste y peso— es intentar desarrollar componentes monomaterial y sin refuerzos metálicos para que se puedan desmontar fácilmente.
¿Puede poner un ejemplo?
Un caso habitual de FPK es el frontal. El soporte de montaje de los faros, radiador, la cerradura, capota, parachoques etc. Se trata de una pieza que durante muchos años ha tenido en Europa un diseño híbrido, de metal y plástico, combinado en un proceso de moldeo por inyección. Estas chapas se pueden separar por prensa o triturando las piezas y separando magnéticamente o por decantación, pero como decía, a la hora de hacer números, no siempre compensa.
¿Cree que la reciclabilidad de los componentes es un aspecto que preocupe al fabricante de vehículos?
Sí, les preocupa. No está en el orden de importancia del peso del componente o del coste pero sí, el reciclado les preocupa. De hecho, hay fabricantes que tienen unas normas específicas a la hora de fabricar las piezas para que luego se puedan desmontar o desensamblar y separar materiales para reciclar.
Además, trabajan en el campo de los componentes aerodinámicos para las cápsulas bajo motor, recubrimientos bajo piso y deflectores y componentes de panelado…
Sí, son componentes en los que, salvo vehículos nicho del tipo 4x4, no ha habido transición del metal al plástico. Son soluciones añadidas para conseguir una mejora aerodinámica del vehículo, una especie de carenado que se monta en los bajos, y tienen una triple función: aerodinámica, protección de los bajos y del motor del vehículo y una función acústica. Si existe un matiz importante en este tipo de piezas es, además de la mejora aerodinámica, lograr ser muy competitivos. Las tecnologías que usamos para fabricar piezas combinan la transformación del plástico con la fabricación de la materia prima.
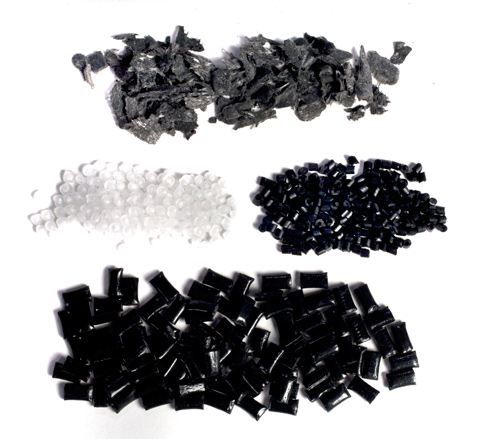
Destaque alguna solución de las que ofrecen, por su relevancia o complejidad…
Si tuviese que destacar dos, por un lado resaltaría un componente consolidado en plástico reforzado en Europa, el frontend. Casi todos los fabricantes europeos de automóviles tienen frontend de plástico o híbridos en sus diferentes modelos. Destacan dos cuestiones: el coste y un ahorro de peso de hasta un 35% frente a la solución metálica. Se consigue un ahorro de coste interesante por la integración de funciones, consiguiendo realizar una pieza con muchas funciones en un solo golpe de prensa de inyección.
¿Y la segunda?
Aunque no es un componente consolidado, destacaría el soporte de panel de instrumentos, una pieza que integra una gran cantidad de funciones y un componente de seguridad muy técnico con requerimientos de crash dinámico. Está ubicada por debajo del tablero de instrumentos, es el conjunto que soporta el tablero de instrumentos y todos los elementos relacionados con el cockpit, la columna de dirección, los airbags de pasajero, la caja de calefacción… Es una aplicación muy interesante en la que hemos trabajado y seguimos trabajando.
¿Qué tecnologías emplea FPK para conseguir componentes de automoción más ligeros?
Actualmente en fabricación contamos con cinco tecnologías: SMC, GMT, LFT, IMC e inyección convencional. Básicamente están clasificadas en tecnologías en moldeo por compresión y en tecnologías en moldeo de inyección. En ambos casos también tenemos tecnologías en las que formamos un semiproducto y lo convertimos en piezas como es el caso de la SMC, GMT o la inyección convencional y otras, donde integramos la fabricación de la materia prima en el propio proceso de moldeo en continuo.
Háblenos de sus proyectos de futuro.
Estamos inmersos en una fase de globalización. Hasta hace cuatro años, FPK era una única planta productiva, pero, tras integrarnos en el grupo Batz, ahora contamos con otros dos centros productivos. Trabajamos para que los productos de peso ligero también se industrialicen en las otras plantas del grupo. Probablemente sea nuestro reto más difícil en estos momentos. Además, pretendemos desarrollar productos innovadores.
¿Qué tipo de productos?
Queremos sustituir el metal por el plástico en piezas de primera evolución que nunca antes se han desarrollado en composite (en serie media o grande). Aquí la clave son los nuevos materiales, materiales optimizados o las variantes de las tecnologías existentes.