Gracias a una personalización de la plataforma de gestión 'WeldCloud', realizada en colaboración con Esab
ADR controla de forma remota la calidad en la soldadura de sus ejes
ADR Group es capaz de controlar de forma remota la calidad de ejecución de cada soldadura individual de sus ejes, gracias a una personalización de la plataforma de gestión 'WeldCloud', realizada en colaboración con Esab, una de las multinacionales más importantes que operan en el sector de la soldadura.
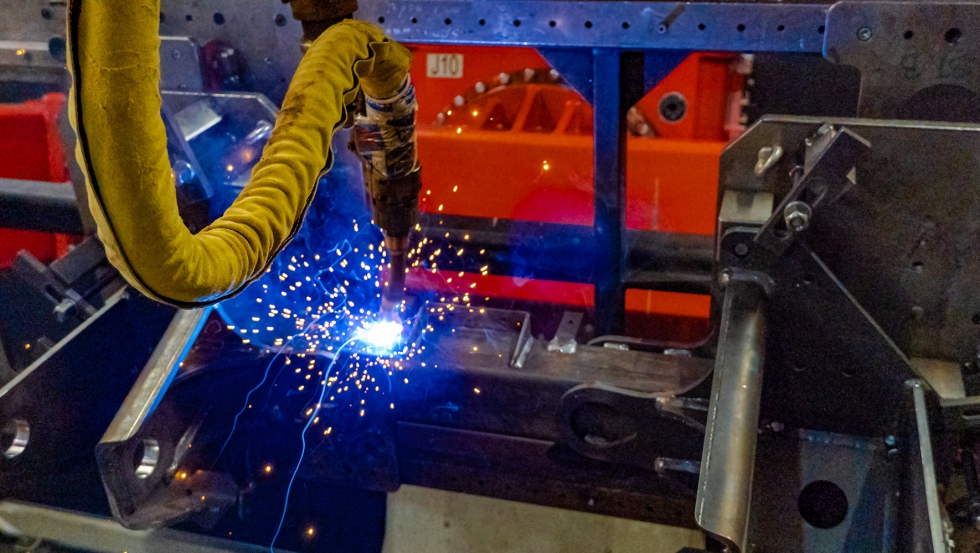
La fiabilidad estructural de un eje está inducida por numerosos factores, el primero de los cuales es inherente a la resistencia de los aceros utilizados para su construcción. Junto a esta necesidad aparece de inmediato la calidad de las soldaduras necesarias para ensamblar las diversas partes del eje. De hecho, de poco sirve tener aceros certificados con prestaciones garantizadas si las soldaduras no están igualmente certificadas y garantizadas, que al unir los componentes del eje dan lugar a su estructura de soporte.
Consciente de esta realidad, ADR Group utiliza desde hace años únicamente materiales certificados para la fabricación de todos sus productos, desde ejes hasta suspensiones y bogies, cuyo procesamiento se realiza con los medios más modernos. Un ejemplo de ello es el sistema de soldadura Esab que opera en la planta de producción de ADR Polska en Zagórz (Polonia).
Dado que Esab es uno de los fabricantes de sistemas de soldadura más importantes del mundo, con más de cien años de experiencia, en este caso concreto ha suministrado a ADR treinta sistemas 'Aristo' basados en el inversor Mig 5000 Iw operativo de forma robótica y automática.
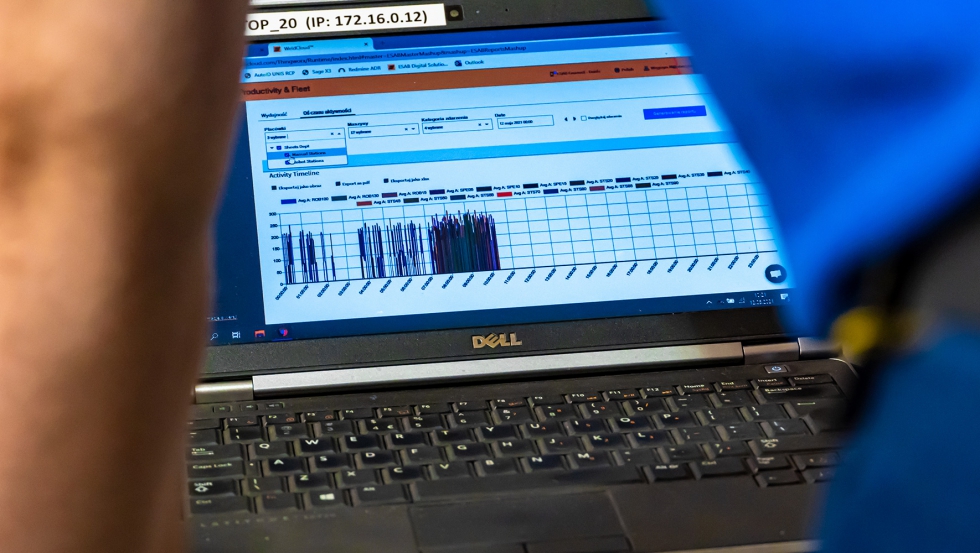
El control remoto del proceso de soldadura asegura la calidad del producto.
En la práctica, la intervención humana se limita a cargar una máscara con las piezas a soldar entre sí, operación que luego se realiza por un robot de forma rápida, segura y garantizada. La calidad final es certificada por la plataforma de gestión de datos 'WeldCould', diseñada por Esab pero personalizado a este caso concreto de acuerdo con las necesidades de ADR para permitir que las oficinas técnicas centrales del Grupo monitoreen el trabajo en su 14 fábricas optimizando sus ejecuciones casi en tiempo real.
Gracias a 'WeldCloud' cada fase de soldadura es monitoreada constantemente, tanto en términos de calidad del producto final como en términos de tiempo, este último factor que juega indirectamente a favor de los clientes de ADR ya que ayuda a contener los costos de producción.
Baste pensar que tras la introducción de la plataforma solo en la planta de Zagórz, los tiempos muertos de procesamiento se han reducido en aproximadamente un 19% y esto solo gracias a la posibilidad de operar en base a datos objetivos que han permitido intervenir positivamente en procesos productivos más pesados. El famoso lema 'Presto e bene' (Pronto y bien) de ADR no es en última instancia un simple eufemismo, sino una realidad concreta.
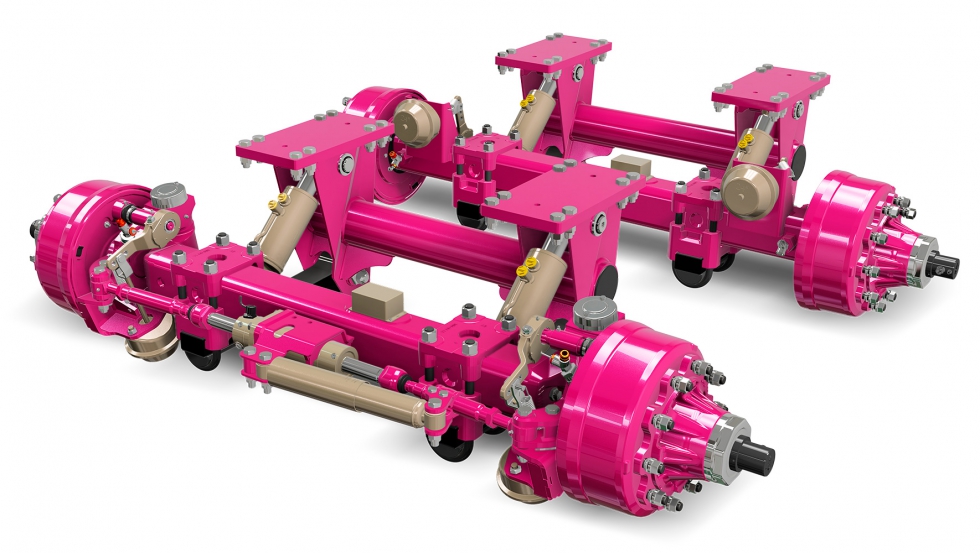