Desafíos del mecanizado de superaleaciones: propiedades excepcionales en condiciones extremas
En la era moderna de la ingeniería y la fabricación, las denominadas superaleaciones han surgido como un pilar fundamental en sectores críticos como la aeronáutica, la energía y la industria química. Estos materiales son reconocidos por su capacidad para mantener propiedades mecánicas excepcionales a altas temperaturas y en ambientes corrosivos, representando así un avance significativo en la ingeniería de materiales. Sin embargo, detrás de estas impresionantes características y aplicaciones yace un desafío técnico formidable: el mecanizado. Este proceso es crucial para dar forma y preparar componentes de precisión a partir de superaleaciones como el Inconel 718, el Waspaloy o el Haynes 282. Requiere no solo habilidades especializadas y herramientas avanzadas, sino también abordar las complejidades inherentes que hacen de estas aleaciones materiales tan valiosos, ya sea empleando técnicas avanzadas de refrigeración o estrategias novedosas de mecanizado.
El presente artículo explora los desafíos únicos del mecanizado de superaleaciones, destacando las técnicas actuales, las áreas que requieren mejoras y las innovaciones que podrían allanar el camino hacia una manufactura más eficiente y efectiva de estos materiales de vanguardia.
Superaleaciones
Las superaleaciones son materiales metálicos de alta resistencia, diseñados para funcionar en condiciones extremas de temperatura, presión y corrosión. Las superaleaciones suelen estar compuestas por una matriz de níquel, cobalto o hierro, reforzada con elementos de aleación como cromo, tungsteno, molibdeno, titanio, entre otros para alcanzar las características deseadas. Algunas de las más conocidas son el Inconel 718, el Waspaloy, el Haynes 282, el Nimonic, el Incoloy entre otras pertenecientes al grupo de superaleaciones, que se clasifican bajo el grupo S de la normativa ISO de materiales utilizada en la industria del mecanizado. Estos materiales son conocidos por sus excelentes características, especialmente su capacidad para mantener altas propiedades mecánicas a altas temperaturas durante su funcionamiento en servicio en comparación con otros materiales más fáciles de trabajar y conformar. En la categoría ISO S, además de las superaleaciones, se incluye también las aleaciones de titanio por su dificultad de mecanizado.
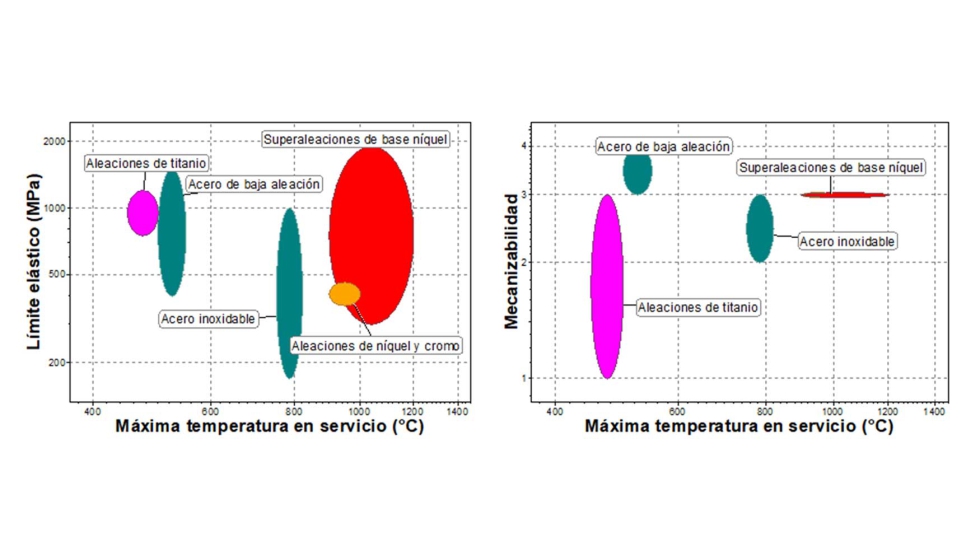
La distribución de los materiales a lo largo de la estructura de la turbina obedece principalmente a dos características: ligereza y resistencia a la temperatura. Las aleaciones de titanio son ligeras y resistentes a temperaturas bajas, por lo que forman parte de las etapas frías de compresión, mientras que las superaleaciones son más pesadas pero resistentes a altas temperaturas, por lo que aparecen en las etapas calientes de las turbinas, a partir de la cámara de combustión.
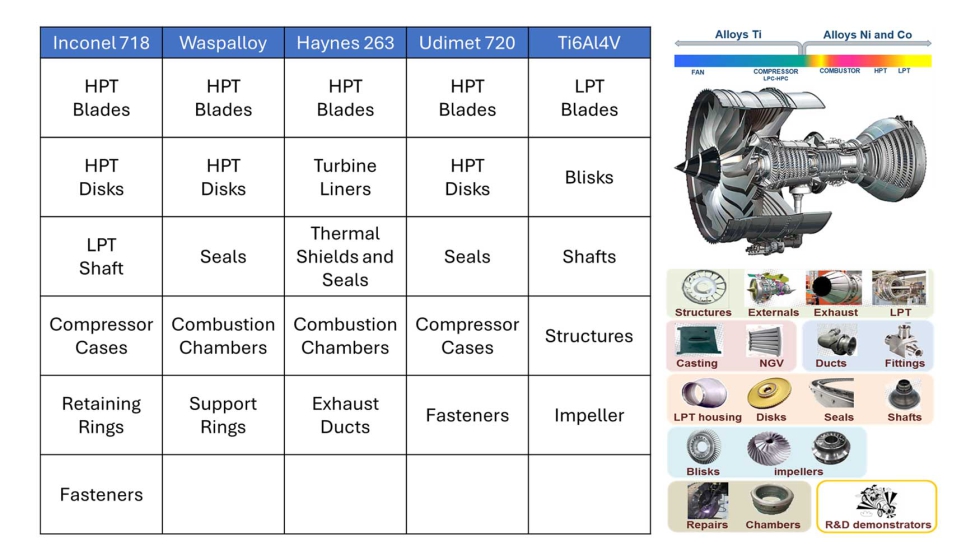
Superaleaciones termorresistentes
Las superaleaciones tienen su origen en la década de 1940, debido a la necesidad de encontrar materiales más fuertes y resistentes que los aceros para ser utilizados en la mayor contienda bélica de la historia. Desde entonces se han ido desarrollando de manera continua hasta la actualidad. Pueden identificarse cuatro etapas o grupos importantes que han ido mejorando sus prestaciones:
- Superaleaciones forjadas, tenían elevados costes de producción y grandes desperdicios.
- Superaleaciones fundidas, con mucho mejor rendimiento de producción y coste bajo.
- Superaleaciones de grano columnar, enfocadas a la fabricación de álabes de turbina debido a su solidificación direccional que aumenta su resistencia a cargas axiales.
- Superaleaciones monocristalinas, con la mayor resistencia posible al eliminarse los límites de grano.
![Evolución histórica de las superaleaciones [1] Evolución histórica de las superaleaciones [1]](https://img.interempresas.net/fotos/4864958.jpeg)
Suelen clasificarse metalúrgicamente en función de su componente mayoritario, como base hierro, base cobalto y base níquel. Estos tres elementos son consecutivos en la tabla periódica y poseen características similares, por lo que los precipitados de refuerzo son similares en los tres grupos de superaleaciones. Su uso es propicio en las zonas calientes de los motores aeronáuticos debido a su resistencia bajo fluencia y corrosión, especialmente las aleaciones de níquel [2].
- Las superaleaciones base níquel son las más utilizadas en los motores aeronáuticos debido a la plasticidad y estabilidad de la estructura cristalina centrada en las caras (fcc) del níquel. Un alto porcentaje de cromo le aporta una gran resistencia a la oxidación. La clave de estas aleaciones es la combinación de diferentes estructuras resistentes, como la matriz de austenita gamma, la presencia de carburos metálicos o la estructura gamma prima de precipitados. Algunas aleaciones como el Inconel® 718 constituyen una fase gamma prima segunda, por la presencia de niobio.
- Las superaleaciones base cobalto, a diferencia de las de níquel, no se refuerzan por precipitación de fase gamma, por lo que es importante combinar el endurecimiento por solución sólida con la formación de carburos metálicos precipitados en una fina distribución dentro de los granos para aumentar su resistencia. Al no poder soportar esfuerzos tan grandes como las superaciones de níquel, se emplean principalmente en piezas estáticas y su contenido en cromo, las hace resistentes a la corrosión.
- Las superaleaciones con base hierro tienen bastante similitud con las de base níquel debido a su alto contenido de este elemento, de, al menos, un 25% para estabilizar la matriz fcc.
Aleaciones de titanio
Las aleaciones de titanio son muy apropiadas para su uso aeronáutico debido, principalmente, a su ligereza y a su gran resistencia a la corrosión a temperaturas inferiores a 400 °C, no así a temperaturas elevadas donde su resistencia empeora considerablemente, debido a su afinidad por elementos intersticiales como el oxígeno o nitrógeno. Por tanto, se emplean en la zona fría de los motores aeronáuticos. Su mecanizado es complejo, ya que posee una alta reactividad a temperaturas elevadas y una muy baja conductividad térmica. La aleación más común es la Ti6Al4V, de tipo α + β debido a su combinación de propiedades mecánicas y baja densidad [3].
Superaleaciones de grano columnar
La solidificación en la dirección axial hace que este tipo de piezas sean ideales para su empleo en álabes. Los límites de grano son paralelos a la carga de tracción, lo cual mejora la resistencia de fluencia.
![Álabes de turbina con estructuras granulares equiaxial, grano columnar y monocristalina [4] Álabes de turbina con estructuras granulares equiaxial, grano columnar y monocristalina [4]](https://img.interempresas.net/fotos/4864959.jpeg)
Superaleaciones monocristalinas
Las superaleaciones monocristalinas presentan mayor capacidad de resistencia y una mejor combinación de propiedades a temperaturas elevadas que cualquier otro material estructural, por lo que algunos elementos de las turbinas, como los álabes, se fabrican con estos materiales. Estas prestaciones se deben a la solidificación orientada unidireccionalmente, que mejora la resistencia a la fatiga térmica y a la ausencia de límites de grano, que actúan como lugares de iniciación de fallo. Estas altas propiedades hacen aumentar su dificultad de mecanizado. Uno de los objetivos con estos materiales es aumentar aún más el contenido de aleación refractaria para mejorar la resistencia a la fluencia [5].
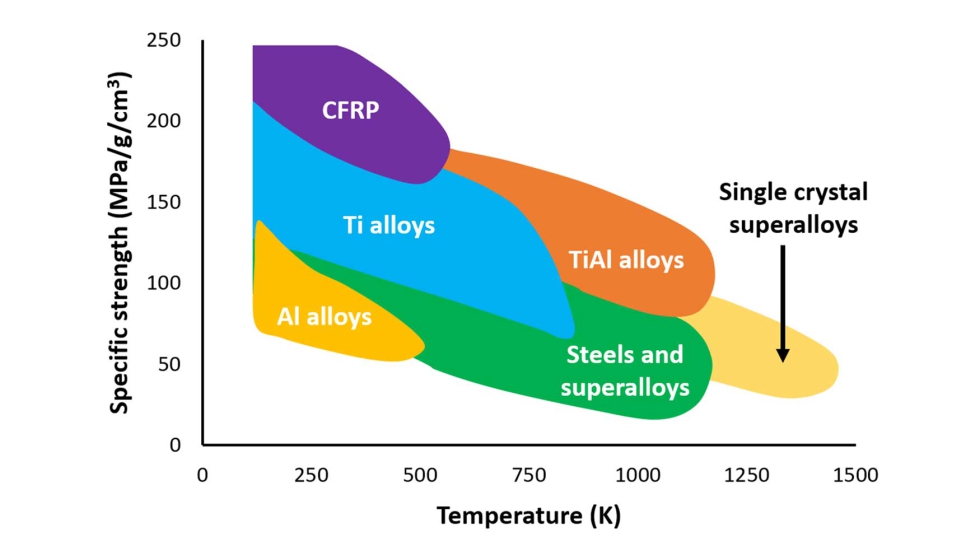
Es interesante apuntar que las superaleaciones base níquel han ido mejorando su resistencia en lo que se ha considerado en clasificar como sucesivas generaciones evolutivas. Esta mejora de la resistencia con la temperatura ha sido posible, en parte, gracias a la adición de pequeñas cantidades de elementos como el renio (Re) y el rutenio (Ru), sin embargo, estos elementos son de los más escasos en la corteza terrestre, por lo que, en la actualidad, la quinta y sexta generaciones se centran en reducir los porcentajes de estos elementos, ya que su utilización presenta un alto riesgo estratégico para la producción industrial debido a su escasez y consiguientes dificultades de suministro, coste elevado y fluctuante [6].
Propiedades de los elementos principales
Las superaleaciones termorresistentes están formadas fundamentalmente por elementos que forman parte del bloque de los llamados metales de transición, que son aquellos cuyos electrones ocupan los orbitales d. Haciendo un breve recordatorio, en los orbitales s caben 2 electrones, en los orbitales p caben 6 electrones y en los orbitales d caben 10 electrones. El elemento con número atómico 20, el calcio, es el último cuyos electrones se limitan a orbitales s y p. La configuración electrónica del calcio, siguiendo las flechas del diagrama de Moeller, es 1s2, 2s2, 2p6, 3s2, 3p6, 4s2 o abreviadamente [Ar] 4s2. A partir del elemento 21, el escandio, se empiezan a ocupar los orbitales d y a medida que aumenta el número atómico nos encontramos además con el bloque de los lantánidos y actínidos, denominados metales de transición interna, que son elementos cuyos electrones empiezan a ocupar los orbitales f, donde caben 14 electrones [7].
Dentro de un mismo grupo los elementos tienden a tener similares características debido a la configuración en sus últimas capas electrónicas. Así, por ejemplo, el cobre, la plata y el oro, considerados metales nobles por su brillantez, resistencia a la corrosión y otras propiedades, pertenecen al mismo grupo. Las configuraciones electrónicas de cobre, plata y oro se abrevian utilizando el símbolo del gas noble inmediatamente anterior, argón, kriptón y xenón respectivamente. Las terminaciones deberían ser d9 s2, sin embargo, obtienen mayor estabilidad donando un electrón del orbital s al d, quedando d10 s1.
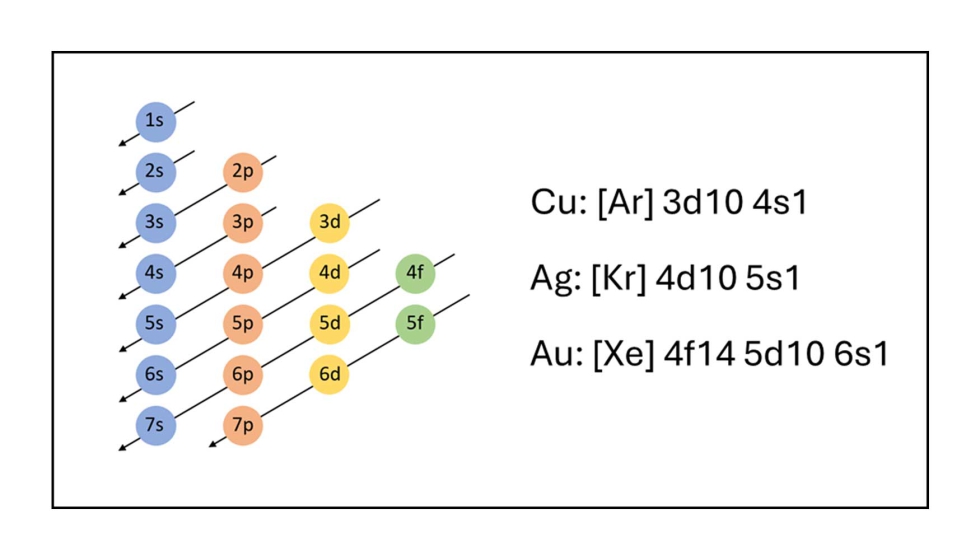
Pero no solo existe una similitud entre elementos del mismo grupo, sino que dentro del mismo periodo algunos elementos pueden tener características similares. La existencia de los orbitales d hace que existan saltos de electrones entre diferentes capas, lo que permite que exista una similitud en sus estados de oxidación y una buena reactividad entre ellos, permitiendo que se puedan alear con facilidad. Este es el caso del hierro, el cobalto y el níquel que encabezan los grupos 8, 9 y 10 respectivamente.
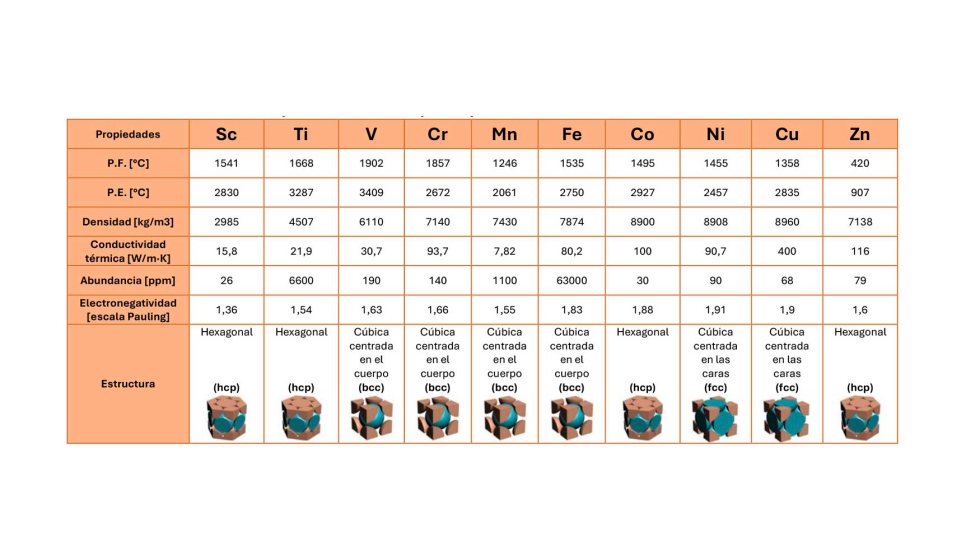
Los tres elementos son ferromagnéticos y disponen de valencias +2 y +3. Además, presentan similitudes en sus puntos de fusión y ebullición, densidad, conductividad térmica o electronegatividad. Sin embargo, existe una diferencia muy notable entre ellos, la abundancia en la naturaleza. De los diez metales de transición del periodo de cabecera, el 4, el metal más abundante con gran diferencia es el hierro, por lo que su disponibilidad es grande y su coste bajo y es el metal más utilizado para la mayoría de los propósitos. Con mucha probabilidad esta abundancia se debe a que es el último elemento que puede ser creado en una reacción de fusión con liberación de energía [8]. En el gran reactor nuclear que es una estrella, se fusionan núcleos de hidrógeno liberando energía que es contenida por la propia fuerza gravitatoria del astro. A medida que el hidrógeno se va agotando, se fusiona helio, litio, berilio, etc. El último elemento en fusionarse liberando energía es el hierro, por lo que en ese momento la estrella pierde energía y es comprimida por la fuerza gravitatoria. En este punto, algunas estrellas explotan y expulsan material al convertirse en una supernova. La energía de esa expulsión de material es aprovechada para la creación de otros elementos mediante reacciones de fisión. En definitiva, se puede decir que, si se dispone de materiales tan valiosos como los metales de transición, esto se debe a la muerte de las estrellas.
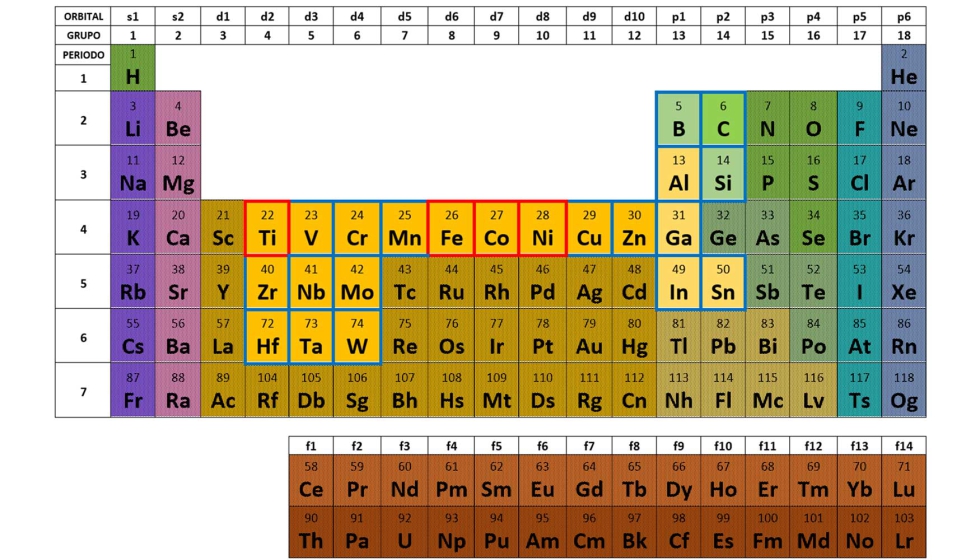
En la tabla periódica de la figura se resaltan los elementos principales de aleación de las superaleaciones. Entre ellos se encuentran, remarcados en rojo, los ya mencionados hierro, cobalto y níquel como elementos principales de las aleaciones termorresistentes y el titanio. El resto de los elementos remarcados en azul son aleantes utilizados en mayor o menor medida. Como se puede observar, no solo encontramos metales de transición, sino también elementos de los grupos 13 y 14, entre ellos, algún metal no ferromagnético como el aluminio, galio, indio o estaño; metaloides como el boro o el silicio y no metales como el carbono. Aunque todos estos son los más representativos, puede haber otros elementos minoritarios.
Desafíos del mecanizado de superaleaciones
El mecanizado de piezas aeronáuticas limita los tiempos de producción debido a sus especiales características e influye en factores como la productividad, el calentamiento de la pieza y herramienta, los desgastes, la estabilidad del proceso o la calidad de los componentes fabricados. El elevado valor añadido de los componentes fabricados para el sector aeronáutico, hacen necesario alcanzar un profundo conocimiento de los procesos y los materiales e implican una necesidad de mejora ante los diferentes desafíos que supone el mecanizado de este tipo de materiales:
- Dureza y resistencia al desgaste: la dureza de las superaleaciones termorresistentes está en el orden de unos 40 HRc por lo que son necesarias herramientas de corte con elevados índices de dureza, que muestren una gran resistencia al desgaste. Resumidamente, los materiales típicos en las herramientas de corte, ordenados de menor a mayor resistencia al desgaste, son el acero rápido, metal duro, metal duro con recubrimientos y cerámicas. Por lo general, una mayor resistencia al desgaste va acompañada de una menor tenacidad, por lo que en cada caso concreto hay que analizar la posibilidad de utilizar unas herramientas u otras.
En el mecanizado de carcasas aeronáuticas, las operaciones de ranurado son críticas, ya que suelen ser de las últimas operaciones, cuando la pieza ya ha adquirido un gran valor añadido. Por otro lado, la aspiración del sector hacia los procesos de fabricación avanzada conlleva una mejora constante de la productividad, reduciendo los tiempos de mecanizado y mejorando la vida útil de las herramientas. Teniendo en cuenta que el ranurado es un proceso de corte continuo y estable, se ha realizado una investigación de ranurado en Inconel 718 con plaquitas de alúmina con refuerzos, que permiten una gran velocidad de corte de 300 m/min.
![Situación de algunas ranuras en carcasa aeronáutica y ensayos de ranurado en barra [9] Situación de algunas ranuras en carcasa aeronáutica y ensayos de ranurado en barra [9]](https://img.interempresas.net/fotos/4864964.jpeg)
El estudio se ha centrado, concretamente, en la influencia del radio de filo, ya que cuanto mayor sea este radio, mayor será la deformación y aplastamiento del material, pero, por el contrario, contribuye a reforzar el filo de corte, haciéndolo más resistente. Por lo tanto, la preparación de los filos se ha realizado teniendo en cuenta que un filo más afilado es frágil para mecanizar una superaleación, mientras que un filo poco afilado aumenta considerablemente las fuerzas de corte. Los resultados mostraron que todas las herramientas tuvieron un bajo desgaste de flanco, que asegura la tolerancia geométrica del corte y se comprobó un ligero efecto de reducción del desgaste al utilizar radios de filo mayores. Por otro lado, los radios de filo mayores presentan mayores fuerzas radiales, pero la variación del radio de filo parece no afectar a las fuerzas tangenciales.
- Conductividad térmica baja: uno de los problemas que se presentan al mecanizar las superaleaciones es la degradación del material de la herramienta de corte por las altas temperaturas del proceso, el calor durante el mecanizado no se disipa debido a la baja conductividad térmica del material. El principal modo para combatir este problema es el uso de refrigeración a alta presión, aunque la refrigeración criogénica muestra cada vez mayores ventajas.
En un estudio reciente se ha comprobado la influencia de la presión y el volumen de taladrina sobre la vida de la herramienta de torno en una aleación de titanio. Los resultados son favorables tanto al aumento de la presión como del volumen, aunque no en la misma medida dependiendo de las condiciones de ensayo, como se muestra en el ejemplo de este artículo: “La importancia de una buena refrigeración en el mecanizado de Ti6Al4V”.
- Formación de virutas continuas y largas: la adecuada fragmentación de la viruta repercute positivamente en la vida de la herramienta y en la estabilidad de las operaciones de mecanizado. El torneado es un proceso de corte ininterrumpido, por ello la viruta generada durante el mecanizado de materiales de alta ductilidad, como pueden ser las aleaciones empleadas en los motores aeronáuticos, tiende a ser continua y a no fraccionarse, originando problemas de calidad superficial o en la propia vida útil de la herramienta [10]. Además, la viruta juega un papel fundamental a la hora de extraer el calor que se genera durante el proceso de corte, ya que si se elimina de manera fraccionada se evita que dicha energía se transfiera a la herramienta. Los rompevirutas cumplen esta función ya que, al poder redirigir y facilitar la extracción de la viruta, existe una menor fricción entre pieza y herramienta, haciendo que la vida útil de esta última aumente en comparación con una herramienta desprovista de rompevirutas.
Por medio de ensayos en Inconel 718 realizados con una herramienta de torneado dinámico se ha comprobado la efectividad del rompevirutas. El torneado dinámico plantea mayores retos que un torneado convencional, ya que la viruta se evacua en direcciones distintas y con dimensiones diferentes según se disponga el ángulo de posición Kr. En el siguiente cuadro se muestra cómo el rompevirutas moldeado sobre la cara de la herramienta cumple su cometido cuando se utilizan ángulos de posición elevados y profundidades de corte mayores. Para los casos restantes sería necesario un rediseño del rompevirutas o bien hacer variar otros parámetros de corte como la velocidad de avance, que está directamente relacionada con el espesor de viruta.
![Morfología de virutas en función del ángulo de posición y la profundidad de corte con herramienta de torneado dinámico [11]... Morfología de virutas en función del ángulo de posición y la profundidad de corte con herramienta de torneado dinámico [11]...](https://img.interempresas.net/fotos/4864965.jpeg)
- Tendencia a la deformación y endurecimiento: en el mecanizado de materiales dúctiles, como las superaleaciones, el cizallamiento se produce al entrar el material en régimen plástico. Sin embargo, debido a la resistencia con la temperatura, son necesarias elevadas fuerzas de corte que acortan la vida de la herramienta. Además, la deformación produce un endurecimiento de las capas de la superficie del material mecanizado, tanto más cuanto más desgastada está la herramienta, generando tensiones residuales en la pieza. Esta capa endurecida dificulta aún más el proceso de corte y genera entallas en la herramienta en un proceso acelerado de degradación. El concepto ‘Near Net Shape’ surge como posible solución a este tipo de problemas. La forja, la fundición y más recientemente la fabricación aditiva, son procesos con los que se pueden alcanzar buenas preformas. Fabricando piezas con tamaños y geometrías lo más cercanas posible al componente final se consigue no solo reducir la cantidad de residuos, sino disponer de un material poco afectado superficialmente. Esto permite trabajar con demasías pequeñas, sin embargo, el nivel de precisión que se requiere es muy alto ya que el material sobrante es mucho menor, las tolerancias son pequeñas y no hay margen para correcciones, por lo que es fundamental un correcto posicionamiento en máquina [12]. La sensorización y la simulación de procesos y máquinas y la incorporación de gemelos digitales son cada vez más útiles para trabajar con precisión en este tipo de piezas.
El CFAA colabora en proyectos de desarrollo de elementos de utillaje para la sujeción de piezas en procesos de mecanizado que ayuden en la precisión de las operaciones de acabado. Uno de los elementos en desarrollo son las garras sensorizadas, que permiten obtener información en tiempo real sobre la presión a la que está sometida la pieza por el amarre. En análisis preliminares, previo a su introducción en procesos de mecanizado, se aplicó una fuerza puntual conocida a través de una roldana a distintas alturas sobre la pieza. La pieza está apoyada y sujeta por dos garras sensorizadas dispuestas a 90º y otras dos garras no sensorizadas en los lados opuestos.
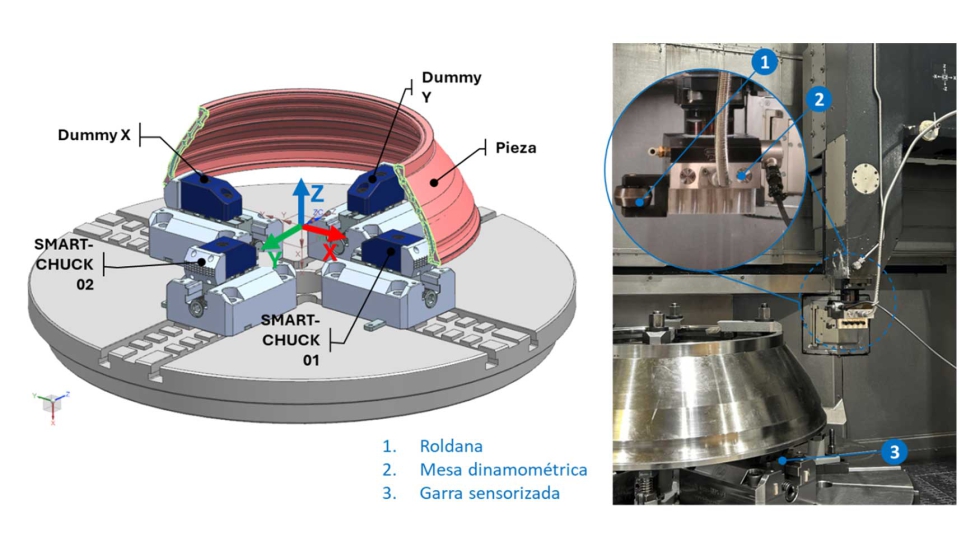
Los valores más bajos se obtuvieron en la zona alta, ya que la distribución de esfuerzos se reparte por la estructura de amarre. La mayor diferencia entre las dos fuerzas se produce cuando la garra sensorizada y la fuerza están alineadas en sentidos opuestos. A través de la sensorización del amarre se persiguen dos objetivos: por un lado, monitorizar el proceso de mecanizado, el cual puede servir como indicador de desgaste de la herramienta según su evolución; y por otro lado, controlar el estado de la pieza, analizando sus condiciones antes y después de cada operación para identificar posibles relajaciones de tensiones, dilataciones térmicas o desajustes en el posicionamiento de esta.
Proyectos de relevancia
El CFAA, en su compromiso con la innovación y la mejora continua, ha focalizado varios de sus proyectos en la investigación y solución de los problemas asociados con el mecanizado de superaleaciones. A través de una combinación de enfoques teóricos y aplicados, el CFAA busca desarrollar métodos y tecnologías que permitan un mecanizado más eficiente y preciso de estos materiales, reduciendo costos, mejorando la calidad de las piezas y prolongando la vida útil de las herramientas de corte. Algunos de estos proyectos son:
[CORTEX] Precision in critical Ultra Near Net Shape components obtained by 2030 processes. HAZITEK ZE-2022/0029 financiado por el Gobierno Vasco.
[CRESCENDO] Sistemas de producción para control exhaustivo de calidad en componente mecanizados desde nuevos procesos primarios. Proyecto CPP2021-008932 de acrónimo CRESCENDO, financiado por MCIN/AEI/10.13039/501100011033 y por la Unión Europea ‘NextGenerationEU’/PRTR.
[ERAGIN] Una nueva ERA en la fabricación avanzada de módulos de presión intermedia para la Generación de INnovación y conocimiento. HAZITEK ZE-2024/00024 financiado por el Gobierno Vasco.
[HATASU] High Breakout Rate Tooling with Surface Integrity Safeguarding: New Designs and Comprehensive Process Monitoring. HAZITEK ZE-2024/00024 financiado por el Gobierno Vasco y la Unión Europea a través del Fondo Europeo de Desarrollo Regional 2014-2020 (FEDER).
Conclusiones
Las superaleaciones fueron concebidas como materiales altamente resistentes, tanto a los efectos de la corrosión, como para soportar las altas temperaturas. El precio a pagar a cambio de esas características es la dificultad en la manufactura de piezas mediante cualquier tipo de tecnología, siendo especialmente complejo el mecanizado.
Actualmente el conocimiento en el mecanizado de superaleaciones es bastante profundo, se conocen bien las características de los materiales, los elementos químicos principales son lo suficientemente abundantes para disponer de ellos con cierta facilidad y los elementos aleantes, aunque algunos muy escasos en la naturaleza, se utilizan en diferentes proporciones de las que se han obtenido gran cantidad de superaleaciones con características diferentes, y se sigue investigando para encontrar elementos que refuercen la estructura del material sin perjudicar otras propiedades y que sean de abundancia suficiente en la naturaleza para una fácil obtención.
Sin embargo, a pesar de toda la ciencia acumulada, la experiencia nos dice que todo lo que sabemos no es más que el punto de partida, el primer escalón a superar. Cada vez que se acomete el mecanizado de una pieza concreta, con unas características geométricas determinadas, el proceso cambia, se necesitan nuevas herramientas y una superaleación muy específica, por lo que sólo se dispone de una primera aproximación de lo que puede suceder. Es necesario realizar muchas pruebas que ajusten y optimicen el comportamiento esperado, se hace necesario probar velocidades de corte y avance que minimicen el desgaste de las herramientas, evitar vibraciones y chatter en paredes delgadas, encontrar precisión en las operaciones de acabado para trabajar con piezas cercanas a la geometría final y generar pocos residuos o utilizar refrigerantes adecuados para cada proceso, además, cada innovación tecnológica abre la puerta a un gran universo de posibilidades que es necesario explorar.
La importancia de una buena refrigeración en el mecanizado de Ti6Al4V
El Centro de Fabricación Avanzada Aeronáutica realiza pruebas de vida útil de insertos de torneado para superaleaciones con el fin de optimizar el rendimiento de diferentes operaciones. Se ha comprobado cómo influyen la presión y el volumen de taladrina sobre la vida de la herramienta de torno en una aleación Ti6Al4V. Con el fin de intentar aumentar la vida útil de las herramientas se ha aprovechado la posibilidad del aporte de taladrina externa disponible en el cabezal de la máquina. Para ello se ha desviado el flujo externo del cabezal, de manera que incida sobre el inserto al mismo tiempo que el flujo de taladrina interno.
Los resultados muestran que el aumento de la presión de taladrina interna tiene un efecto positivo en los ensayos de acabado, con un aumento de hasta el 42% en la duración de la herramienta. Sin embargo, el efecto no es tan claro en los ensayos de semiacabado, con un aumento del 63% en la duración de la herramienta a presiones intermedias pero un descenso al 53% a altas presiones. La presión de taladrina y el caudal son variables parcialmente dependientes, ya que a mayor presión también aumenta el caudal, por lo que a presiones intermedias aumenta el rendimiento. Sin embargo, a presiones más altas se produce una dispersión del flujo producida por un mayor diámetro de salida, ya que el portaherramientas de semiacabado dispone de orificios de refrigeración de 2 mm mientras que los de acabado son de 1 mm.
Por otro lado, la adición de taladrina externa tiene un efecto positivo en todos los casos, ya que el aporte de taladrina externa es constante y no depende del nivel de presión. En condiciones de acabado la mejora oscila entre un 41% y un 67%. En semiacabado los resultados son más drásticos, entre un 198% y un 145%. Los márgenes de mejora son en este caso mucho más grandes debido a que la profundidad de corte es mayor y se genera más calor que se disipa con el refrigerante. Con taladrina interna, el mejor rendimiento en semiacabado se encontraba a presiones intermedias, sin embargo, al añadir el flujo externo hay una buena refrigeración desde las presiones bajas y al ir aumentando la presión, la dispersión del flujo interno va reduciendo el rendimiento.
En resumen, en acabado, donde el calor puesto en juego es menor, el mayor beneficio viene de un aumento de la presión y en menor medida del aporte de refrigeración externa. En cambio, en semiacabado, el aumento del caudal es muy beneficioso ya que retira mucho calor, pero presiones altas de taladrina dispersan el flujo, por lo que la solución idónea es optar por presiones bajas y aporte de taladrina externa.
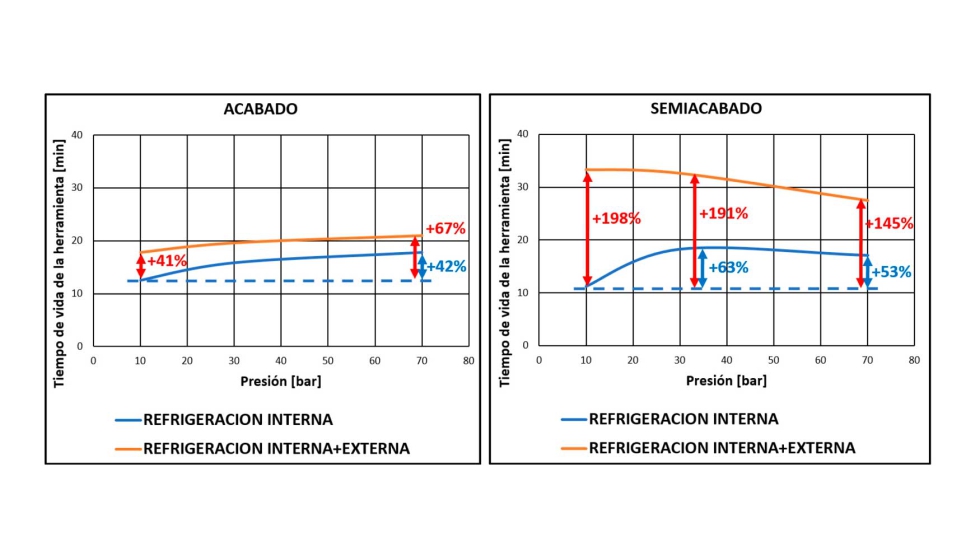
Bibliografia
[1] Haibo Long, Shengcheng Mao, Yinong Liu, Ze Zhang, Xiaodong Han, Microstructural and compositional design of Ni-based single crystalline superalloys - A review, Journal of Alloys and Compounds, Volume 743, 2018, Pages 203-220, ISSN 0925-8388.
[2] John K. Tien, Thomas Caufield, Superalloys Supercomposites Superceramics, Academic Press, 1989, Pages ibc1-ibc2, ISBN 9780126908459, https://doi.org/10.1016/B978-0-12-690845-9.50030-0.
[3] C. Leyens, P. Manfred. Titanium and Titanium Alloys, Vol. 1:, Wiley-VCH (2003)
[4] Reed, Roger. The Superalloys Fundamentals and Applications, Cambridge University Press, 2006
[5] M. Perrut, P. Caron, M. Thomas, A. Couret. High temperature materials for aerospace applications: Ni-based superalloys and γ-TiAl alloys. Comptes Rendus Phys., vol. 19 (8) (2018), pp. 657-671, 10.1016/J.CRHY.2018.10.002.
[6] Jean-Yves Guédou, Luc Rémy, Chapter 1 - Past, present, and future of SX superalloys, Editor(s): Georges Cailletaud, Jonathan Cormier, Gunther Eggeler, Vincent Maurel, Loeïz Nazé, Nickel Base Single Crystals Across Length Scales, Elsevier, 2022, Pages 3-19, ISBN 9780128193570, https://doi.org/10.1016/B978-0-12-819357-0.00008-1.
[7] Raymond Chang, Kenneth A. Goldsby, Química, México D.F.: McGraw-Hill Education, 2013 Edición: 11ª ed. 1 v. (pag. var.): il.; 27ISBN: 9786071509284
[8] Bernas, R.; Gradsztajn, E.; Reeves, H.; Schatzman, E. On the nucleosynthesis of lithium, beryllium, and boron. Ann. Phys. 1967, 44, 426–478, doi:10.1016/0003-4916(67)90100-5.
[9] Fernández-Lucio, P., Urbikain-Pelayo, G., Plaza, S., Pereira-Neto, O. (2024). Influence of the cutting-edge preparation in ceramic tools for grooving of Inconel® 718 and force prediction. Engineering Science and Technology, an International Journal, Volume 54, ISSN 2215-0986. (https://www.sciencedirect.com/science/article/pii/S2215098624001125)
[10] Amigo, F.J., Urbikain, G., de Lacalle, L.N.L. et al. On the effects of cutting-edge angle on high-feed turning of Inconel 718© superalloy. Int J Adv Manuf Technol 125, 4237–4252 (2023). https://doi.org/10.1007/s00170-023-10974-5
[11] Francisco Javier Amigo, Asier Fernandez Valdivielso, Pablo Fernandez De Lucio, Octavio Pereira Neto, Gorka Urbicain Pelayo, Freddy Corrales Lacayo, Luis Norberto Lopez de Lacalle Marcaide. ‘Influence of side Cutting Edge angle on the design of the chipbreaker: study of dymanic and high feed turning tools in Inconel718’. DYNA 98, no. 4 (2023). DOI: https://doi.org/10.6036/10876