Sistema flexible para el mecanizado de pieles aeronáuticas
En este trabajo se presenta un sistema flexible de mecanizado que permite el fresado de piezas tipo piel dentro de las tolerancias requeridas por la industria. Este concepto innovador se basa en la utilización de un utillaje universal combinado con un desarrollo capaz de adaptar la trayectoria de la herramienta para el correcto mecanizado de las piezas. Por un lado, el utillaje flexible es capaz de ser adaptado a la geometría requerida, amarrando toda la superficie de los paneles de forma uniforme. Por otro lado, esta solución incluye una implementación que puede adaptar la trayectoria del mecanizado por medio de la medición online del espesor de la pieza. La integración de estos dos dispositivos innovadores permite mecanizar una gran variedad de paneles de baja rigidez, incluyendo diferentes tamaños, geometrías y curvaturas. Además, este sistema permite trabajar intercalando etapas de fresado, de taladrado e incluso de recanteado en la misma atada de pieza, optimizando así la etapa de puesta a punto.
Cabe destacar que la tecnología se ha desarrollado en términos de eficiencia de proceso, por lo que permite afrontar el mecanizado de pieles reduciendo drásticamente la inversión en equipamiento. Además, el desarrollo se ha realizado teniendo en cuenta la integración de tecnologías IT alineándolo así con el paradigma Industria 4.0.
1. Introducción
A pesar de la crisis económica global de la última década, el tráfico aéreo de pasajeros continúa aumentando cada año, alcanzando los 34 millones de vuelos en 2014 [1]. De hecho, varios estudios predicen que el número de vuelos seguirá aumentando durante los próximos 20 años. En Europa, por ejemplo, se espera pasar de 8,85 millones de vuelos en 2014 a más de 12,8 millones en 2035 [2].
Es evidente que este incremento de tráfico aéreo tiene influencia directa en los fabricantes aeronáuticos. Hace tres años, los mayores fabricantes entregaron aproximadamente 1.000 nuevos aviones comerciales, teniendo otros 2.000 más en producción [1].
Esa cantidad de aviones se va a incrementar en los próximos años. En Norteamérica, por ejemplo, entre 2015 y 2036 se espera que la flota de aviones en activo se incremente un 0,2% al año. Este dato, en términos de aeronaves fabricadas significa un incremento de 7.000 unidades en la flota americana [3].
Este incremento se refleja en la fabricación de distintos tipos de aviones, de los cuales el más demandado es el de pasillo único. De acuerdo con las previsiones de Airbus, en los próximos 20 años van a fabricar 22900 unidades de los cuales el 70% serán de este tipo de avión [4].
Por otro lado, a pesar de que se utilizan materiales compuestos en estructuras primarias (B787, Airbus A380, F35 y Typhoon) [5], el aluminio es todavía el material más empleado en la industria aeronáutica, especialmente en el caso de aviones de pasillo único [6].
De todas las partes fabricadas en aluminio, las pieles aeronáuticas son unos de los productos más exigentes y de un mayor valor añadido. Estos tipos de piezas de baja rigidez se han mecanizado históricamente mediante fresado químico [7]. Con este proceso, se reduce el espesor de la piel en las zonas deseadas mediante ataques químicos en las zonas seleccionadas. El resto de la pieza se protege del reactivo químico mediante una máscara, como se aprecia en la figura 1.
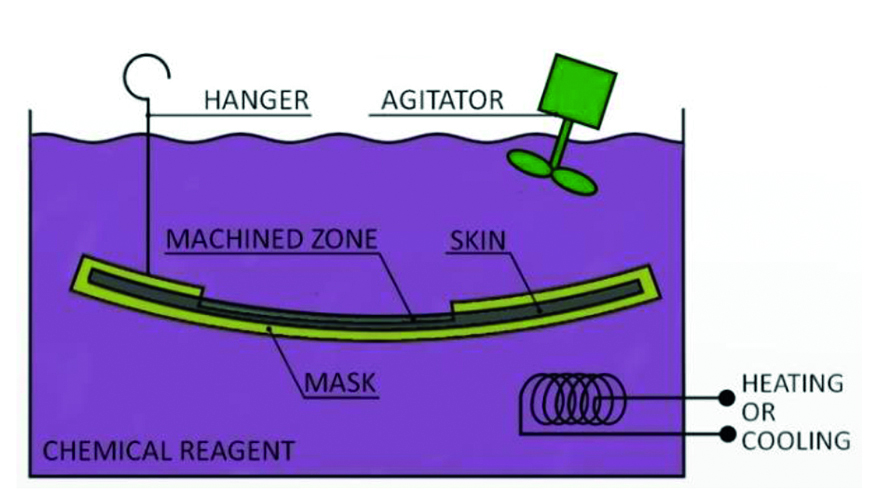
Sin embargo, esta tecnología de fabricación tiene varias desventajas ya que es un proceso lento, con un alto coste de mantenimiento y unos requerimientos de espacio en planta muy elevados. Además, el manejo de este tipo de agentes químicos es complejo y peligroso para los operarios [8]. De ahí, que durante los últimos años la industria aeronáutica haya desarrollado diferentes soluciones de fresado mecánico con el objetivo de reemplazar el mecanizado químico [9].
Estas soluciones están basadas en máquinas de doble cabezal capaces de alcanzar las exigentes tolerancias de espesor requeridas en piezas de tipo panel. Este concepto, mostrado en la figura 2, está basado en que, por un lado, uno de los cabezales fresa el espesor requerido, mientras que por la otra cara un segundo cabezal se mueve de forma sincronizada para poder evitar la flexión de la pieza.
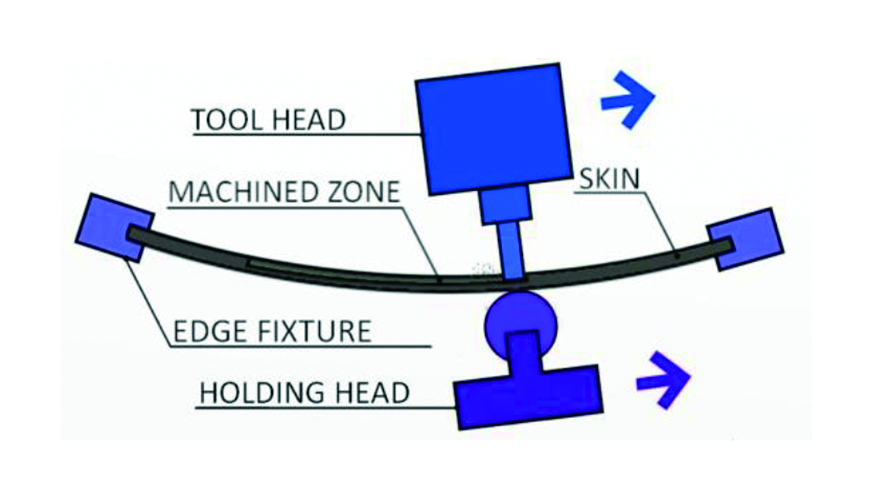
Hoy en día, el uso de este tipo de tecnología sigue siendo bastante limitado. Los altos costes de inversión reducen el mercado de este tipo de máquinas a la fabricación de las piezas más grandes del sector aeronáutico. Sin embargo, en los aviones de pasillo único, los tamaños de los paneles son menores y sus márgenes de beneficio se ven reducidos. Por lo tanto, la gran parte de la industria aeronáutica no se puede permitir acceder a esta tecnología, llevándola a seguir trabajando con fresado químico.
Mientras tanto, se han ido desarrollando otras soluciones tecnológicas para reducir el coste del fresado de pieles. Existen diferentes aproximaciones, desde el uso de un soporte esclavo [10], hasta diferentes utillajes adaptables basados en el uso de apoyos discretos automáticos en forma de copas de vacío [11]–[13], como se muestra en la figura 3. Además, existen otras soluciones que han sustituido las copas de vacío por un elemento continuo de amarre [14], [15]. Sin embargo, ninguna de estas soluciones ha llegado aún a alcanzar los resultados obtenidos tanto por el fresado químico como por las máquinas de doble cabezal.
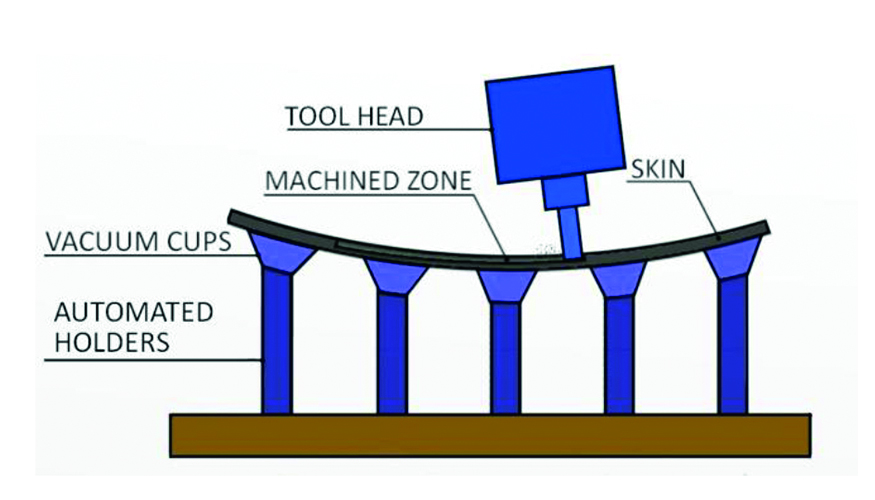
En este contexto, se ha desarrollado un sistema de mecanizado flexible capaz de fresar mecánicamente pieles de aviones de pasillo único. Este sistema es capaz de fresar paneles de baja rigidez dentro de las tolerancias requeridas por el sector aeronáutico mediante un innovador utillaje de amarre universal combinado con un desarrollo de trayectoria de herramienta adaptativo. De hecho, el objetivo de este desarrollo no está limitado a obtener un simple dispositivo para la fabricación de pieles, si no que pretende desarrollar un sistema ciber-físico (CPS) alineado con el paradigma de la Industria 4.0. Basado en la integración de las tecnologías de la información en los procesos de fabricación [16], esta cuarta etapa de industrialización presenta una gran oportunidad para alcanzar una creación de valor industrial sostenible, tanto a nivel económico, como social y medioambiental [17].
Se ha demostrado el potencial de las tecnologías de internet para mejorar la eco-eficiencia y productividad en operaciones de mecanizado. Por ejemplo, durante las operaciones de fresado, las capacidades de computación de los CNC han sido aumentadas vía Internet [18].
Por lo tanto, esta solución tecnológica está orientada a proveer una alternativa de bajo-coste asequible para el fresado de pieles aeronáuticas por medio de un CPS flexible.
2. Especificaciones de la aplicación
2.1. Especificaciones de la pieza
Las piezas objetivo para su fresado son las pieles aeronáuticas de aluminio. De acuerdo con las referencias, este tipo de piezas son curvas, con una longitud de hasta 7 m, 2 m de ancho, un espesor inicial situado entre 1,5 m y 6 mm y un espesor final mínimo de 0,8 mm. Además, entre todas las referencias de pieles, se pueden encontrar tanto pieles planas, como de curvatura simple y doble. En este caso, la curvatura se define en términos de la relación entre el ancho del panel y el valor de la deflexión. Así, la curvatura puede variar entre un 0 y un 40%.
El material seleccionado para los ensayos de mecanizado ha sido el AA2024-T3, una aleación de aluminio ampliamente utilizada en la construcción del fuselaje. Esta aleación se caracteriza por tener una alta tensión de fluencia, muy buena resistencia a la propagación de grietas y una elevada dureza contra fracturas. Por lo tanto, la aleación de aluminio 2024 se posiciona como un material importante en la estructura de los aviones debido a su extremadamente buena tolerancia frente a los daños y su alta resistencia a la propagación de roturas a fatiga, cuando se le aplica un tratamiento de envejecimiento T3 [5].
Por otro lado, las cajeras a fresar se caracterizan por ser de una gran variedad de tamaños, geometrías y profundidades. De hecho, debido a las vibraciones derivadas del mecanizado sobre una pieza tan esbelta, los requerimientos son muy estrictos, definiendo tanto rugosidad como espesor por debajo de los 50 µm.
2.2. Requisitos del proceso
Con el objetivo de evaluar y definir los requerimientos de la aplicación se han realizado unos ensayos y simulaciones de fresado. Estos ensayos preliminares proporcionan información relacionada con las condiciones más favorables de mecanizado para el fresado de pieles de aluminio.
En primer lugar, se ha analizado el efecto del perfil de la herramienta comparado con la curvatura de la piel. El análisis se ha enfocado en la optimización del tiempo de mecanizado comparado con la máxima rugosidad (Rz) obtenida sobre una cajera de 400 x 700 mm. Así, el tiempo de proceso se define por el paso entre trayectorias consecutivas hasta completar toda la superficie de la cajera. Además, en estas simulaciones se ha contrastado el comportamiento de herramientas de tipo bola y de tipo toroidal. Estos casos se han comparado para curvaturas de 10 y de 30% mientras que los diámetros de herramienta se han definido en 20 y 25 mm.
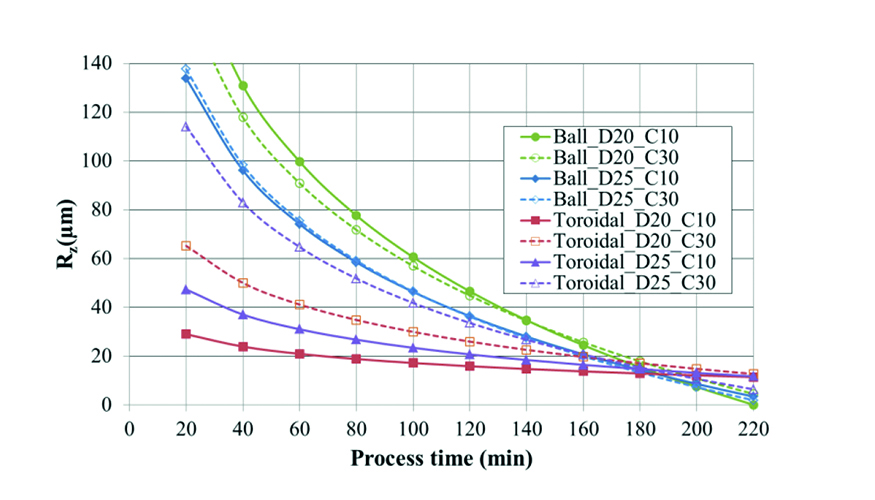
Estos resultados confirman que, para curvaturas por debajo del 30%, las herramientas toroidales proporcionan los mejores resultados. Este tipo de herramientas proporcionan menos errores geométricos para un tiempo de proceso definido y viceversa. Sin embargo, a medida que la curvatura de la piel aumenta los resultados entre la herramienta toroidal y la de punta esférica tienden a igualarse. La herramienta toroidal tiende a mejorar los resultados a medida que el diámetro disminuye y el efecto contrario sucede con la herramienta de bola. Por lo tanto, con el objetivo de realizar los ensayos de mecanizado, se ha seleccionado una herramienta toroidal de diámetro 16 mm con dos filos.
Para esta herramienta, las fuerzas de proceso han sido caracterizadas para ranuras entre 0,2 y 0,6 mm, equivalente a una etapa de acabado. Las condiciones de fresado seleccionadas han sido de un avance por vuelta de 0,12 mm/rev y un avance lineal de 1.000 mm/min. Estos ensayos han sido realizados en un panel de 2 mm de espesor amarrado sobre una mesa con célula de carga triaxial, como la mostrada en la figura 5.
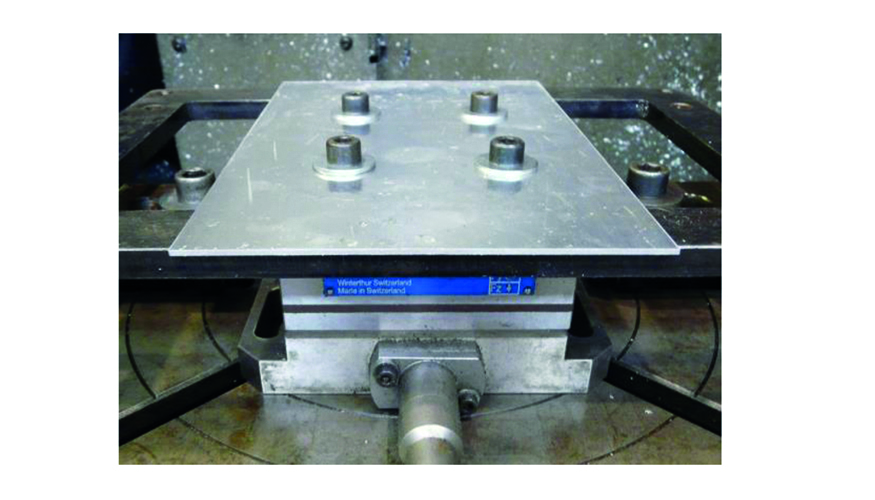
Estos ensayos indican que las fuerzas axiales están por debajo de 11 N y que las de la dirección de avance alcanzan los 163N. Sin embargo, extrapolando estos ensayos al caso del fresado de pieles sobre un utillaje de vacío, la componente de fuerza más crítica es la axial, ya que tiende a separar la chapa del utillaje. Por lo tanto, dadas las reducidas fuerzas axiales, hacen factible utilizar un material no rígido como soporte inferior de la piel durante su mecanizado.
3. Desarrollo de un utillaje flexible
Hoy en día, como se ha mencionado antes, existen en el mercado varios utillajes flexibles automatizados para el mecanizado de paneles. Este tipo de utillajes amarran la pieza de forma no uniforme mediante un número determinado de copas de vacío. Por lo tanto, la heterogeneidad en las condiciones de apoyo de la chapa durante el proceso de mecanizado lleva a vibraciones no deseadas en este tipo de piezas de baja rigidez.
Con el objetivo de obtener un utillaje flexible capaz de amarrar eficientemente las piezas tipo piel durante el proceso de mecanizado, se ha buscado desarrollar una solución de utillaje universal basado en el uso de placas elásticas como soporte y amarre, tal y como se muestra en el esquema de la figura 6.
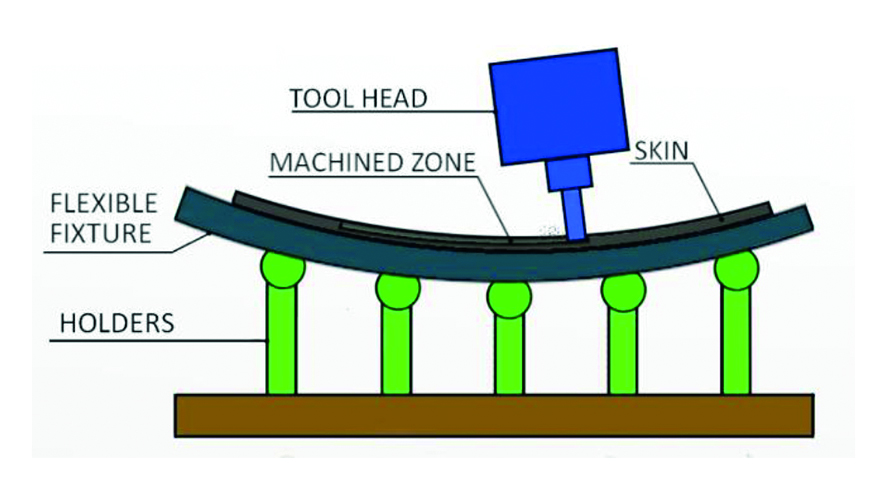
3.1. Encontrando un material flexible
En primer lugar, se han definido los requerimientos del material para la aplicación. Por ejemplo, este material tiene que ser suficientemente elástico para ser capaz de adaptarse a diferentes geometrías de piezas y para absorber las vibraciones del proceso de mecanizado derivadas del impacto de los filos de la herramienta contra el panel.
Por otro lado, debido a que este material elástico tiene que adaptarse a varias geometrías, tiene que ser suficientemente rígido como para mantener cierta continuidad en su perfil bajo los esfuerzos del proceso de mecanizado y bajo su propio peso.
Además, a diferencia de las copas de vacío utilizadas en otro tipo de utillajes, este material flexible tiene que ser no poroso y a prueba de fugas de aire para así poder mantener unas condiciones idóneas de vacío. Es más, debido a que la presión de vacío tiene que ser distribuida a lo largo de la pieza, la superficie de este material tiene que ser configurable para poder incluir en ella ciertas ranuras o canales.
Finalmente, debido a que este tipo de soluciones se utilizan en entornos industriales tienen que ser capaces de soportar un amplio rango de temperaturas además de resistir la interacción con diferentes agentes químicos, como aceites y ácidos. Existen varios elastómeros que cumplen estos requerimientos a diferentes niveles. Sin embargo, en término de flexibilidad y comportamiento bajo condiciones industriales las gomas sintéticas son la opción más adecuada como elemento de amarre. A pesar de que existen una gran variedad de gomas sintéticas con diferentes propiedades, para este desarrollo se ha definido como parámetro clave en la selección la capacidad de absorción de esfuerzos, tanto en amplitud como en frecuencia. Así, de acuerdo con los resultados de los ensayos anteriormente realizados, los esfuerzos axiales se sitúan en torno a los 10 N con una frecuencia de 300 Hz. Basándose en estos valores y en las propiedades de estanqueidad se ha seleccionado la lámina de goma sintética más adecuada para utilizarla como elemento de amarre flexible.
3.2. Transformando una lámina elástica en un utillaje de vacío
Una vez seleccionada la lámina elástica, se ha rediseñado como un utillaje de vacío para poder amarrar el panel de forma homogénea. Además, sus propiedades de estanqueidad permiten una distribución uniforme de la presión de vacío a lo largo de toda la superficie de la pieza mediante canales, tal y como se muestra en la figura 7. Las condiciones de amarre se obtienen extrayendo el aire a través de una única toma de vacío y sellando el contorno mediante el contacto entre el panel y la goma.
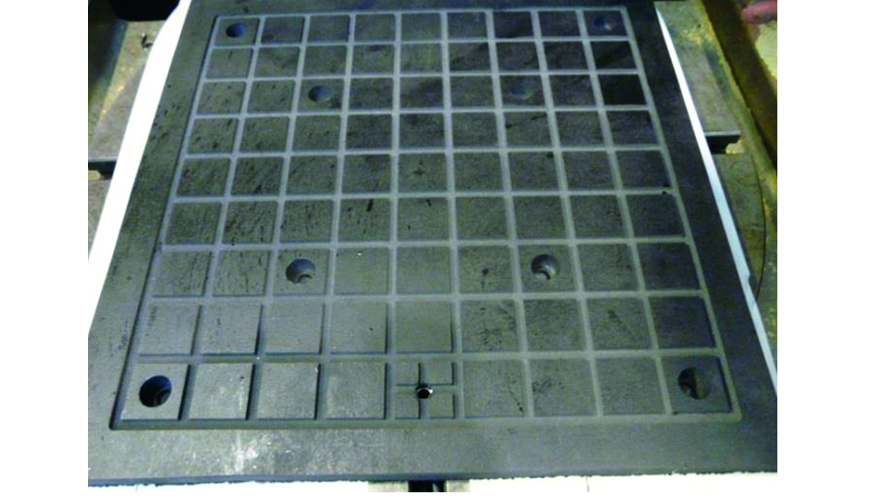
El comportamiento de esta lámina flexible se ha testeado bajo la influencia de fuerzas inducidas por el proceso de mecanizado. Este estudio ha sido ejecutado en una lámina de 300 x 300 x 14 mm, amarrado por ocho tornillos. Como se muestra en la figura 8, la medición del perfil de la ranura se ha realizado mediante un sensor LVDT, comparando así el perfil antes y después del proceso de mecanizado.
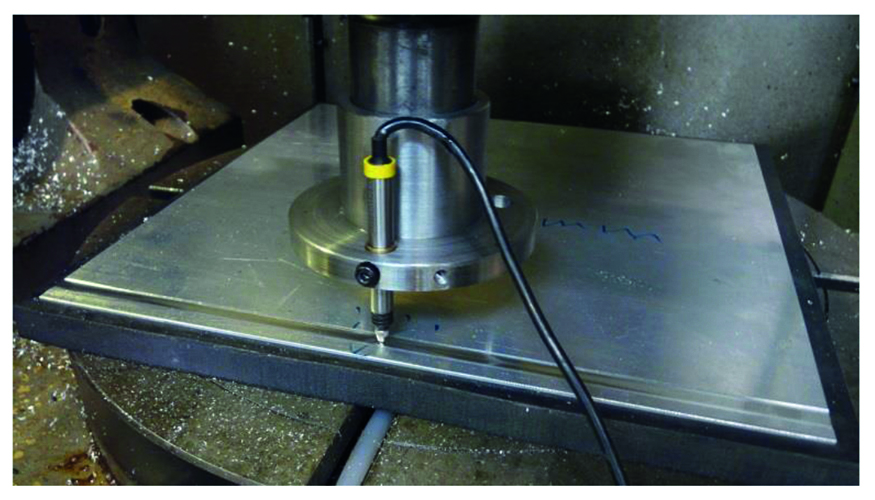
Los resultados obtenidos muestran que la tolerancia en la profundidad de las ranuras está comprendida entre ±20 μm. Estas diferencias se ven incluso reducidas a medida que la ranura se va acercando cada una de las zonas de amarre con tornillos entre la lámina flexible y la mesa de la máquina. Por ejemplo, en la figura 9, se puede observar como una ranura diagonal pasa por encima de 4 zonas de amarre entre la lámina flexible y la mesa de la máquina, y cómo, en esos puntos, la profundidad mecanizada y la medida se igualan.
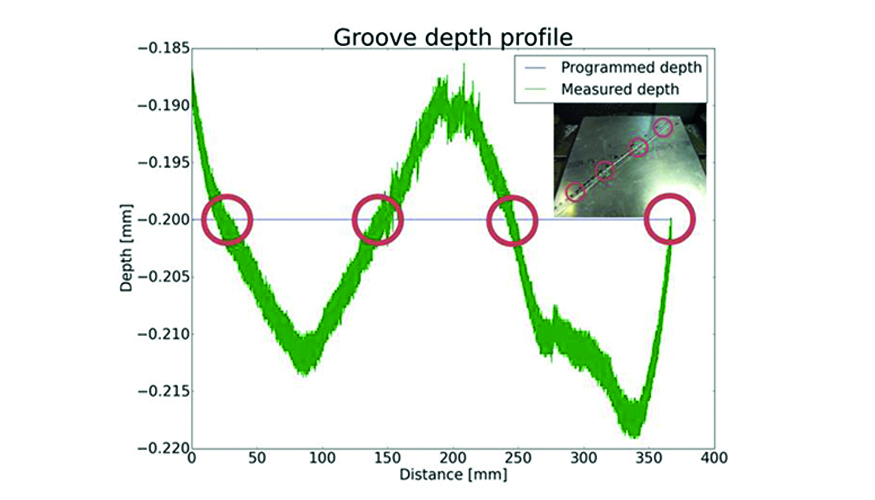
Estos resultados confirman que se puede fresar cajeras dentro de tolerancias aeronáuticas utilizando un sistema de amarre basado en un utillaje de vacío fabricado con goma. Sin embargo, la fabricación de pieles aeronáuticas incluye otro tipo de operaciones de mecanizado, como el recanteado o el taladrado.
Por otro lado, con el objetivo de poder atravesar el panel durante el mecanizado sin llegar a dañar la goma, se pueden intercalar láminas porosas entre el panel y el utillaje, como se muestra en la figura 10. Estos materiales de sacrificio son fácilmente de mecanizables y ayudan en la distribución de la presión de vacío a lo largo del área de la piel. Además, estas láminas porosas permiten trabajar con paneles más pequeños que la zona delimitada por el diseño del utillaje. Así, cualquier tamaño y geometría de panel puede ser amarrado homogéneamente.
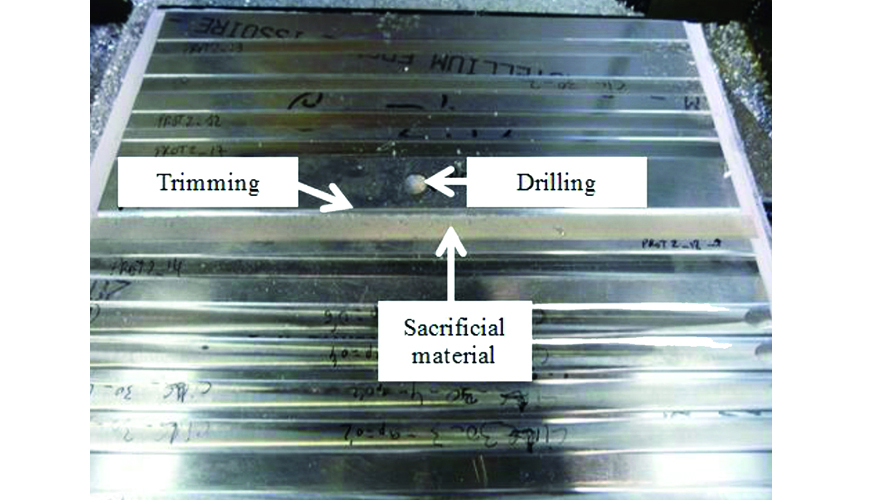
3.3. Llevando el utillaje de vacío a superficies curvas
El utillaje de vacío presentado se había probado amarrado directamente a la mesa de la máquina. Sin embargo, la solución tiene que ser adaptable a diferentes curvaturas y formas. Con el objetivo de llevar la lámina flexible a la curvatura deseada, se han utilizado un tipo de apoyo basado en travesaños, como muestra la figura 11.
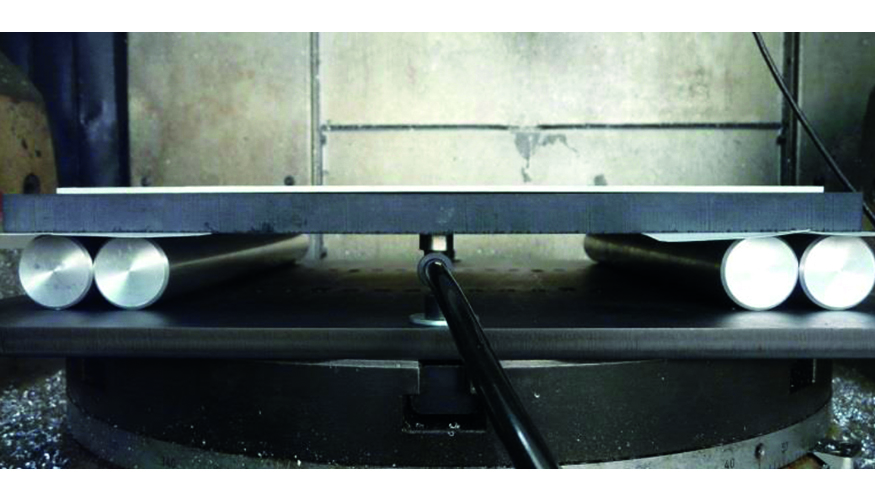
Este tipo de apoyo basado en travesaños proporciona una sujeción más amplia comparada con las obtenidas a través de copas de vacío. Así, la rigidez del conjunto se ve incrementada a la par que las vibraciones provocadas por las fuerzas del mecanizado se ven reducidas.
Además, desde el punto de vista económico, usando un apoyo basado en travesaños se tiene un doble efecto en la reducción de la inversión. Por un lado, el utillaje se simplifica ya que hay menos elementos para mover en la puesta a punto. Por otro lado, estos elementos tienen una mayor superficie que permiten a la propia máquina colocarlos para formar la curvatura deseada.
Por lo tanto, por medio de un sistema de amarre mecánico-neumático localizado en el cabezal de la máquina el utillaje puede ser adaptado a diferentes curvaturas sin la necesidad de automatizar cada uno de los apoyos, tal y como se muestra en la figura 12.
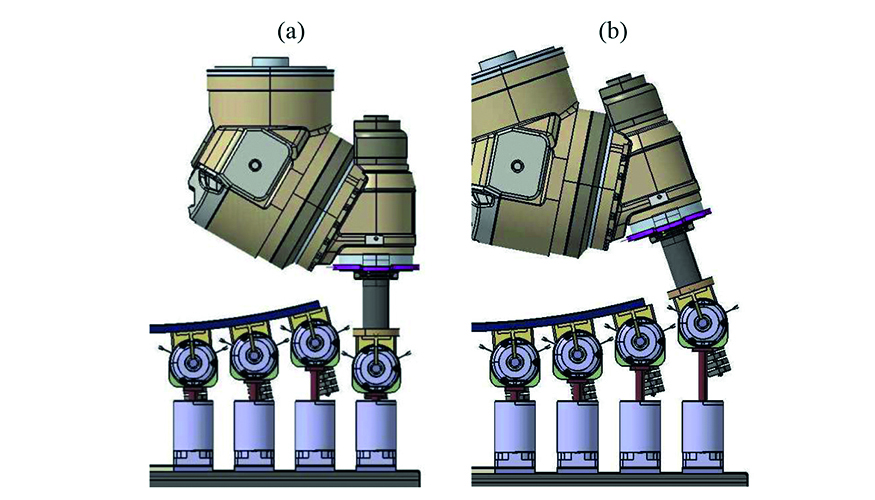
Por lo tanto, colocando cada uno de los travesaños en la posición y orientación deseada se puede obtener una curvatura simple continua como la mostrada en el conjunto de la figura 13. Además, este concepto podría llegar a estar basado en travesaños discontinuos o flexibles, posibilitando trabajar con geometrías de doble curvatura.
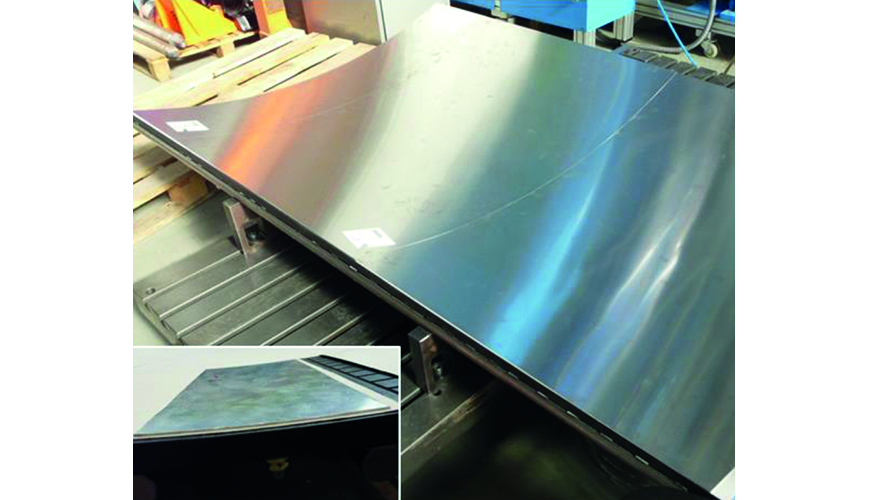
4. Integración del sistema de monitorizado
A pesar de que se ha demostrado que es posible alcanzar las tolerancias requeridas por el sector aeronáutico utilizando este tipo de utillaje flexible, estos resultados se han obtenido bajo unas condiciones muy concretas. Con el objetivo de extrapolar estos resultados a los procesos de mecanizado en condiciones industriales, se presenta la necesidad de desarrollar ciertos aspectos.
El principal reto es controlar el espesor a fresar para cumplir con las tolerancias requeridas en las industrias aeronáutica y aeroespacial. Por lo tanto, es necesario incluir en el proceso un sensor que monitorice el espesor de la pieza.
4.1. Seleccionando el sensor adecuado
Existen dos aspectos críticos a la hora de seleccionar un sensor de medida de espesor para esta aplicación: el rango de tolerancia y la integración del equipo en el proceso.
Como se ha mencionado antes, los requisitos de espesor son extremadamente exigentes, acotando la variación de la medida dentro de 50 µm. Además, en función del dispositivo de medida, las tolerancias del dispositivo pueden cambiar a medida que el espesor de la placa se reduce.
Cabe destacar que, debido al concepto de utillaje, el acceso para la medición de la pieza se limita al lado del mecanizado, por lo que los sistemas de medición por láser se ven descartados. Así, las únicas soluciones de medida factibles son las basadas en las tecnologías de monitorización por ultrasonidos.
Hoy en día existen principalmente tres tecnologías de medida basadas en ondas ultrasónicas: Eddy Current (EC), Dry-Coupled Piezoelectric Ultrasound (DCUT) y Electro Magnetic Acoustic Transducers (EMAT).
La tecnología EC se basa en la distribución de ondas ultrasónicas desde un transductor piezoeléctrico a la pieza a través de un líquido acoplante, como agua o aceite, tal y como se muestra en la figura 14. Así, a través del tiempo de vuelo (TOF) de la onda ultrasónica se puede conocer el espesor de la pieza.
![Figura 14. Comparación entre EC y EMAT [19] Figura 14. Comparación entre EC y EMAT [19]](https://img.interempresas.net/fotos/1679614.jpeg)
Esta tecnología de no contacto puede alcanzar las tolerancias requeridas en el fresado de pieles en ciertas condiciones, ya que puede medir con una precisión de menor de 100μm. Sin embargo, aunque la tecnología EC se emplea en ambientes muy exigentes, no se recomienda su utilización en esta aplicación. La principal razón se debe a que este tipo de tecnología demanda un flujo continuo de acoplante líquido. Debido a la generación de virutas y polvo durante el proceso de fresado, el flujo de acoplante puede ser inadecuado e incluso verse interrumpido [20]. Por lo tanto, esta tecnología sería únicamente adecuada para una medición de la pieza antes del mecanizado, y no para usarla en la adaptación on-line de la trayectoria de mecanizado.
Otra opción es el uso de la tecnología DCUT, la cual evita el uso de cualquier acoplante líquido. En este caso, las ondas de ultrasonidos son generadas por un piezoeléctrico elástico de Fluoruro de Polivinilideno (PVDN) y distribuido a través de un acoplante sólido polimérico.
El sensor tiene forma de rueda por lo que permite inspeccionar las piezas a medida que el dispositivo va rodando por su superficie. En la figura 15 se puede observar como la compresión del piezoeléctrico elástico genera la onda de ultrasonidos que es transferida a través del contacto entre la rueda y la cara superior del panel.
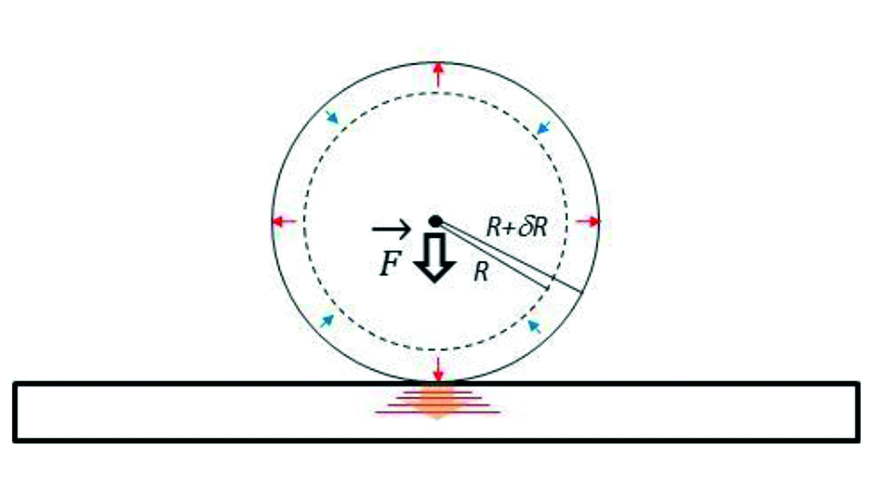
El rango de trabajo y las tolerancias obtenidas por el equipo DCUT son mejores incluso que las obtenidas por la tecnología EC, ya que puede alcanzar mediciones con una tolerancia de hasta 13 μm. Estos valores se han obtenido con unas buenas condiciones de contacto a lo largo de una superficie continua.
Sin embargo, en el caso del fresado de pieles se presentan varias discontinuidades debido a la existencia de polvo, viruta y escalones localizados en las zonas de mecanizado. Por lo tanto, esta tecnología también sería adecuada para una medición previa al mecanizado pero no para un escaneo on-line de la pieza.
Una vez descartadas tanto la tecnología EC como la DCUT, para asistir un control adaptativo de la herramienta de corte sólo queda una tecnología basada en el uso de ondas ultrasónicas adecuada para la aplicación, los sistemas EMAT. Esta solución de no contacto está basada en la generación de ondas ultrasónicas dentro de la pieza metálica por medio de ondas electromagnéticas enviadas a través del aire por el transductor, como se muestra en la figura 14. Asimismo, gracias al efecto combinado de la ley de inducción de Faraday-Lenz y la fuerza de Lorentz, la medida del espesor del panel se puede obtener sin la necesidad de contacto ni acoplante.
La única restricción para este tipo de dispositivos es que, para obtener una medida adecuada, el transductor tiene que ser mantenida cerca de la superficie del material. Esta distancia puede fluctuar hasta los 2mm, dependiendo de las propiedades del material, del espesor del panel y de la precisión con la que se quiera medir.
De hecho, debido a que las ondas ultrasónicas son generadas dentro del material, la medición del espesor se realizará correctamente a pesar de que el transductor no esté perfectamente perpendicular a la superficie de la pieza. Esta característica del equipo es crítica para el mecanizado de piezas curvas o de zonas previamente mecanizadas, como se ve reflejado en la figura 16.
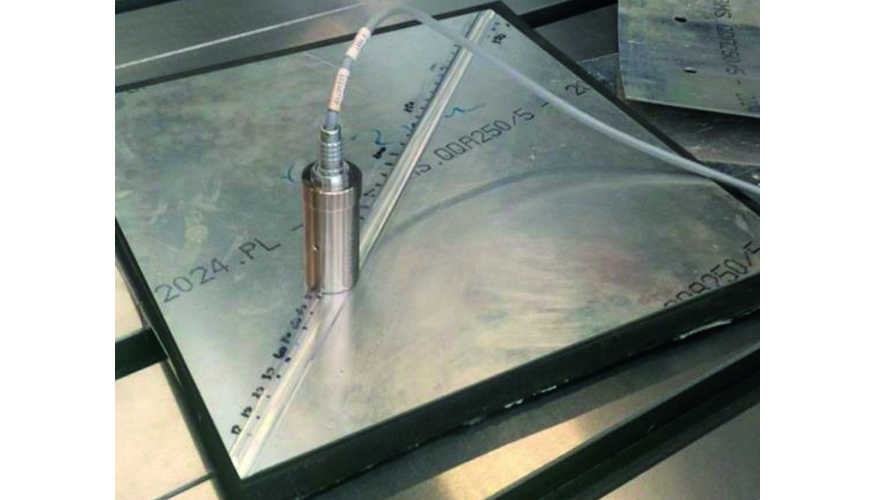
4.2. Integrando el sensor en la máquina
En primer lugar, para obtener una medición on-line del espesor el sensor EMAT tiene que moverse de tal forma que siempre esté localizado delante de la herramienta de fresado, como se muestra en la figura 17.
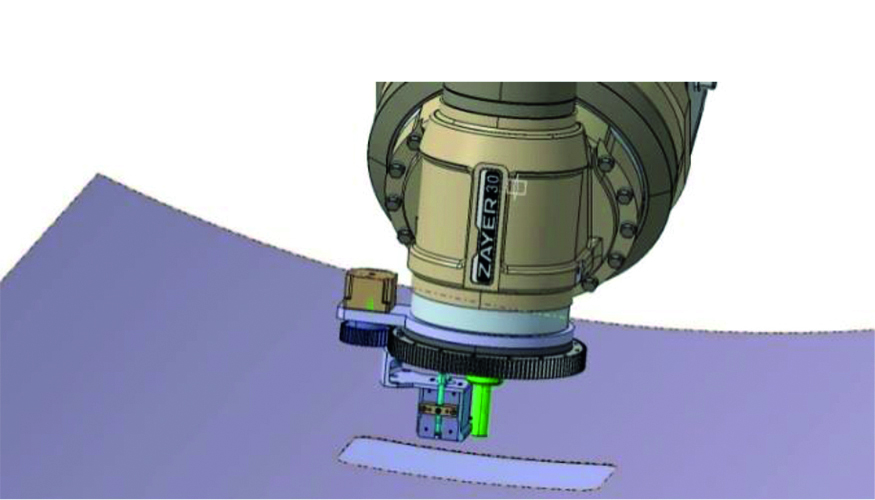
El movimiento del sensor puede verse limitado a una rotación en torno a la herramienta de mecanizado. Sin embargo, con el objetivo de garantizar una distancia mínima entre el sensor y la piel se ha de añadir otra fuente de control. Se pueden plantear dos opciones: se puede añadir un eje extra o bien se puede obligar al sensor a seguir la forma de la piel mientras se monitoriza su posición. Dado que la segunda opción simplifica la integración de la medición del espesor durante el proceso de fresado, se ha escogido como diseño de integración.
4.3. Adaptando la trayectoria de la herramienta
Tras obtener una medición precisa con el sensor EMAT, la trayectoria original tiene que ser adaptada a la situación real de la piel y a la distribución de espesores. En la figura 18 se presentan los diferentes pasos del proceso para adaptar la trayectoria de la herramienta con el objetivo de fresar las pieles dentro de las tolerancias requeridas.
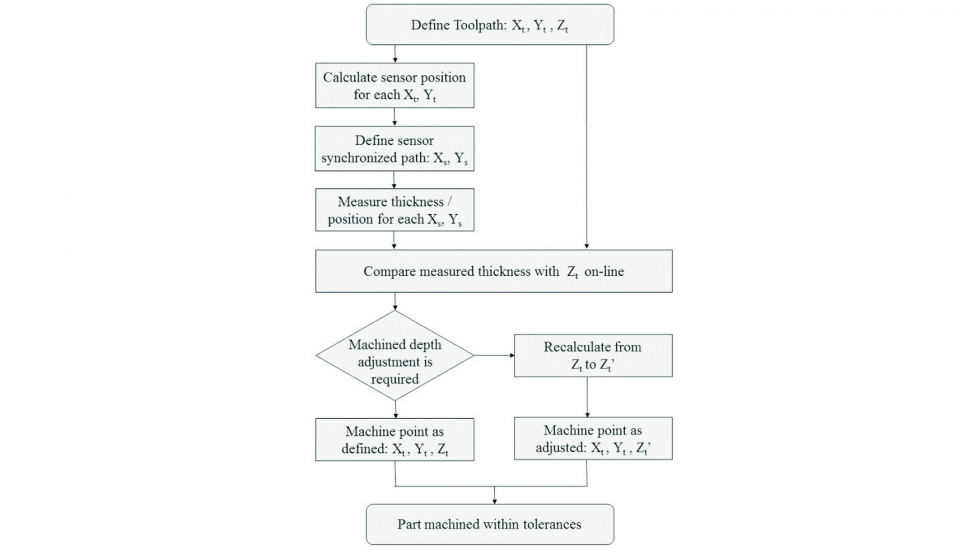
El proceso comienza con la definición de la trayectoria de la herramienta basado en el modelo CAD de la máquina. Debido a que este tipo de piezas son curvas, se necesitan como mínimo cinco coordenadas para definir la posición y orientación de la herramienta a lo largo del proceso de mecanizado: Xt, Yt, Zt y dos ángulos para garantizar la perpendicularidad respecto del panel en todo momento.
Sin embargo, los ángulos de orientación pueden ser evitados en términos del monitorizado ya que se puede asumir que el sensor está tan cerca de la herramienta de corte que puede medir en todo momento perpendicularmente al panel. Consecuentemente, de acuerdo a esta premisa, la trayectoria de la herramienta se puede implementar teniendo en cuenta únicamente Xt, Yt, Zt.
Por lo tanto, simulando el proceso como un mecanizado en tres ejes, la localización del sensor en cada momento se puede calcular usando Xt e Yt. Además, regulando el ángulo entre la dirección de avance de la herramienta y la posición del sensor, se puede calcular el espesor del panel para cada punto Xs y Ys por donde el sensor pase.
Para cada punto Xs, Ys el espesor medido es evaluado y comparado con el Zs original. Por lo tanto, si la profundidad mecanizada tiene que ser ajustada la herramienta fresara hasta Zt’ en vez de hasta Zt. Como resultado, extrapolando este ajuste para cada punto a mecanizar, la pieza se podrá fresar dentro de las tolerancias requeridas.
5. Hacia la Industria 4.0
Los valores de espesor obtenido se utilizan para obtener un proceso de fresado de precisión. Sin embargo, utilizando esta información junto a otros parámetros de monitorizado del proceso se puede optimizar el resto de procesos productivos de la pieza. Por ejemplo, las inspecciones de calidad pueden verse drásticamente reducidas a la vez que la etapa de montaje puede optimizarse. Por lo tanto, con el objetivo de mejorar la trazabilidad del proceso y optimizar el proceso de mecanizado se ha integrado en la máquina una plataforma de adquisición de datos diseñada para el sector de la máquina herramienta. Así, con las posibilidades que ofrece esta plataforma, se lleva el desarrollo hacia un concepto de sistema ciber-físico (CPS). Por medio de esta tecnología, alineada con el paradigma de la Industria 4.0, la conectividad entre la pieza, la máquina, el fabricante y el usuario final se ve mejorada [21].
Esta plataforma de adquisición de datos está basada en un sistema de almacenamiento de datos que procesa la información registrada tanto desde la memoria del control como la obtenida a través del sistema de medición del espesor de la pieza. Además, este sistema puede manejar datos procedentes de otros sensores externos o embebidos con el objetivo de optimizar el proceso.
Por otro lado, la plataforma de adquisición de datos también incluye un servidor remoto al cual se pueden subir todos los datos registrados. Así, es posible el acceso a estos datos a través de internet, permitiendo un análisis remoto de las señales.
6. Conclusiones
El sistema flexible desarrollado para el fresado de pieles aeronáuticas representa una alternativa al fresado químico y a las altas inversiones en máquinas de alta complejidad. Esta solución está basada en el uso de un utillaje de amarre flexible para piezas de grandes dimensiones y baja rigidez, a la vez que es capaz de adaptar la trayectoria de la herramienta gracias a la información extraída de un sensor que mide el espesor. Además, estas mediciones y otros datos obtenidos del proceso son gestionados y transmitidos mediante una plataforma con el objetivo de optimizar la cadena de producción del producto.
En primer lugar, se han recopilado las principales especificaciones de la aplicación. Con esa información, se ha realizado un análisis de la geometría de la herramienta en función de la curvatura del panel. Los resultados muestran que para curvaturas por debajo del 30%, las herramientas más eficientes son las de tipo toroidal, y esa eficiencia mejora en términos de rugosidad y tiempo de proceso a medida que el diámetro disminuye.
Una vez que se han definido la herramienta y las condiciones de mecanizado, se han caracterizado las fuerzas del proceso. Tomando estas fuerzas como referencia se ha identificado una goma sintética capaz de absorber esas fuerzas de fresado. Además, debido a que esta lámina elástica tiene propiedades de estanqueidad, se ha utilizado para fabricar un prototipo de utillaje de vacío.
Por otro lado, con el objetivo de llevar el utillaje a la curvatura deseada se ha diseñado un sistema de apoyos basado en travesaños. A diferencia de otros sistemas automatizados de apoyos discretos, este desarrollo está basado en la optimizada puesta a punto del utillaje por medio del propio cabezal de la máquina.
Dado que las tolerancias del sector aeronáutico son muy exigentes, se ha integrado en la solución un novedoso sistema de medición de espesores de tal forma que la trayectoria de la herramienta puede ser ajustada durante el proceso de fresado. El sensor de ultrasonidos de no-contacto monitoriza el espesor existente delante de la herramienta por el mismo lado de la pieza por el que se produce el mecanizado. Además, por medio de una plataforma de adquisición, los datos del proceso quedan registrados y se pueden utilizar para poder mejorar la cadena de valor del producto.
Por lo tanto, este sistema ciber-físico es capaz de mecanizar pieles aeronáuticas dentro de las tolerancias requeridas por el sector aeronáutico y aeroespacial además de mejorar la eficiencia a lo largo de la cadena de valor del producto.
Referencias
[1] http://www.icao.int/airnavigation/Documents/ICAO_Air_Navigation_Report_2015_Web.pdf
[2] http://ec.europa.eu/transport/modes/air/aviation-strategy/documents/european-aviation-environmental-report-2016-72dpi.pdf
[3] ‘FAA Releases 2016 to 2036 Aerospace Forecast’. [En línea]. Disponible en: https://www.faa.gov/news/updates/?newsId=85227. [Accedido: 05-abr-2016].
[4] ‘Global Market Forecast 2015-2034 | Airbus, a leading aircraft manufacturer’, airbus. [En línea]. Disponible en: http://www.airbus.com/company/market/forecast/. [Accedido: 06-abr-2016].
[5] ‘Recent developments in advanced aircraft aluminium alloys - 1-s2.0-S0261306913011357-main.pdf’
[6] A. S. Warren, ‘Developments and Challenges for Aluminum - A Boeing Perspective’, Mater. Forum, vol. 28, 2004.
[7] J. R. Davis, Aluminum and Aluminum Alloys. ASM International, 1993.
[8] H. A. Youssef, H. A. El-Hofy, y M. H. Ahmed, Manufacturing Technology: Materials, Processes, and Equipment. CRC Press, 2011.
[9] ‘Airbus evaluates the mechanical milling of fuselage panels in a European programme’, airbus. [En línea]. Disponible en: http://www.airbus.com/presscentre/pressreleases/press-release-detail/detail/airbus-evaluates-the-mechanical-milling-of-fuselage-panels-in-a-european-programme/. [Accedido: 06-abr-2016].
[10] A. Mahmud, J. R. R. Mayer, y L. Baron, ‘Magnetic attraction forces between permanent magnet group arrays in a mobile magnetic clamp for pocket machining’, CIRP J. Manuf. Sci. Technol., vol. 11, pp. 82-88, nov. 2015.
[11] ‘Liné Machines Flexitool’, 07-ene-2016. [En línea]. Disponible en: http://metal-cutting-composites.fivesgroup.com/products/composites/finishing-trimming/line-machines-flexitool-finishing.html. [Accedido: 05-abr-2016].
[12] ‘Universal holding fixture - HGS Aerospace, Inc.’ [En línea]. Disponible en: http://www.freepatentsonline.com/8079578.html. [Accedido: 05-abr-2016].
[13] ‘Holding Fixture Skin’. [En línea]. Disponible en: http://www.modig.se/products/uhf-skin/. [Accedido: 05-abr-2016].
[14] M. Torres Martínez, ‘Sistema de sujeción para mecanizado de paneles de reducido grosor’, ES2258893 A1, 01-sep-2006.
[15] J. Baigorri Hermoso, ‘Soporte para el mecanizado de chapas y otros elementos de reducido espesor’, ES2354793 A1, 26-ene-2012.
[16] C. Faller y D. Feldmüller, ‘Industry 4.0 Learning Factory for regional SMEs’, Procedia CIRP, vol. 32, pp. 88-91, 2015.
[17] T. Stock y G. Seliger, ‘Opportunities of Sustainable Manufacturing in Industry 4.0’, Procedia CIRP, vol. 40, pp. 536-541, 2016.
[18] A. Gajate, A. Bustillo, y R. E. Haber Guerra, ‘Transductive neurofuzzy-based torque control of a milling process: results of a case study’, Int. J. Innov. Comput. Inf. Control, vol. 8, n.o 5 (B), pp. 3495-3510, may 2012.
[19] ‘EMAT Technology - Innerspec Technologies’. [En línea]. Disponible en: http://innerspec.com/knowledge/emat-technology. [Accedido: 26-abr-2016].
[20] A. Mahmud, ‘Design of a Grasping and Machining end Effector for Thin Aluminium Panel’, phd, École Polytechnique de Montréal, 2015.
[21] A. Bustillo, J. Negre, y I. Lazcanotegui, ‘Towards higher machine-tool eco-efficiency with an Information Sharing Platform’, 2013, pp. 7548-7553.
Agradecimientos
Los autores quieren expresar sus agradecimientos al CDTI y a la SPRI por su apoyo a lo largo del desarrollo del sistema. Además, este desarrollo no habría sido posible sin la colaboración de otros compañeros de proyecto como: Arantxa Apaolaza, Jokin Lekunberri, Benjamín Rubio, Iñigo Lazkanotegi, Julien Nègre, Jon Borha Fernández, Txomin Ostra and Aitor Lasa de Tecnalia.