Entrevista a Jon Ander Goyenechea, general manager de Mizar
La compañía vasca especializada en fabricación aditiva Mizar Additive Manufacturing ha desarrollado los primeros modelos estructurales para un nanosatélite, producido en Euskadi, mediante tecnología aditiva. Se trata de un trabajo realizado para la empresa Karten Space, que ha confiado en Mizar para mejorar el diseño y aligerar el peso del nanosatélite, como nos explica con más detalle Jon Ander Goyenechea, general manager de Mizar.
Mizar es una empresa muy joven pero con solvencia contrastada en el mundo de la fabricación aditiva. ¿Cómo ha sido esa progresión?
Mizar arrancó en octubre de 2014 y los primeros tiempos los dedicamos a instalar tecnología, conocer a los proveedores y empezar a fabricar primeras muestras. Hoy ya podemos trabajar codo con codo con los clientes, identificar aplicaciones y desarrollar soluciones reales. Ello ha supuesto un incremento muy importante en cuanto a clientes. Y, más allá de los demostradores y prototipos, ya estamos fabricando series de 30, 40 ó 50 piezas.
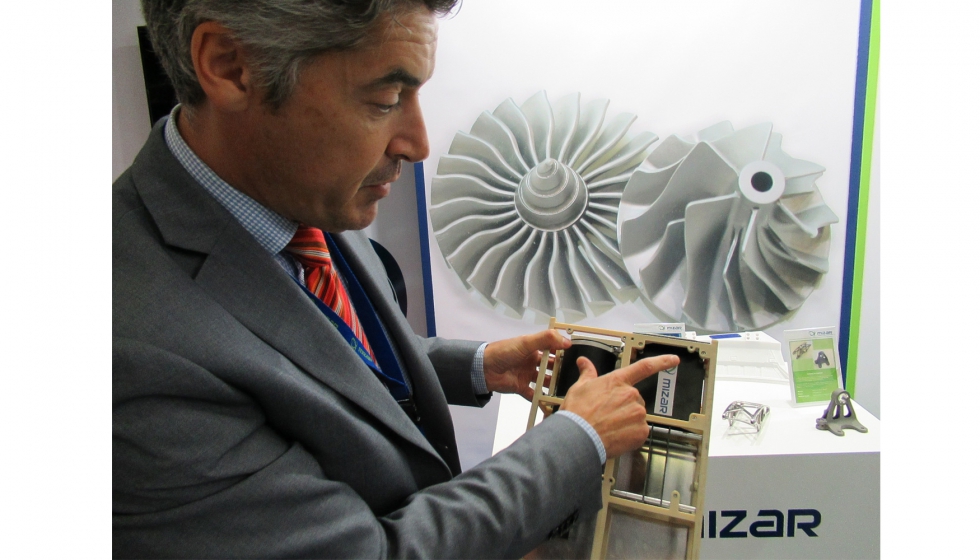
Hablamos de series cortas...
Sí. Aunque tecnológicamente la fabricación aditiva pueda realizar series largas, actualmente la economía está en la serie corta. Cuando el precio de las máquinas y los materiales bajen, habrá posibilidad de reducir el coste de la producción aditiva. Por poner un ejemplo, un kilo de forja de titanio puede estar sobre los 80-100 euros mientras que un kilo en material en polvo ronda los 400€.
Si hablamos específicamente del material la impresión 3D en metal, ¿es relativamente fácil encontrar la materia prima necesaria?
Nosotros trabajamos de manera muy ligada a la empresa suministradora de la máquina y el software. Sí hemos probado otros proveedores de material pero, por ahora, optamos por contar con el proveedor de la máquina también para el material.
¿Qué opciones existen de software para diseño en 3D?
Es evidente que no es lo mismo diseñar para aditiva que para mecanizar. Actualmente existen varias tendencias. Una es diseñar para mecanizado y adaptarlo a la fabricación aditiva, pero no aporta muchas ventajas ni en coste ni en prestaciones. La otra tendencia es diseñar la pieza directamente para la fabricación aditiva pero existe una tercera corriente que es ‘pensar qué quiero obtener’ y diseñar sin prejuicios en función de las prestaciones que quiero, explotando todas las posibilidades. Si se intenta fabricar por el mismo método no pueden esperarse resultados distintos. Lo único que se obtiene en este caso es una reducción de peso y del tiempo de puesta en el mercado, que hoy son las principales ventajas que aporta la aditiva. En cambio, la tercera tendencia va más allá y algunas empresas ya están potenciando el diseño desde cero, sin ideas preconcebidas. Es decir, obtener un resultado que quizá no tenga nada que ver con la pieza tal como sería mecanizada pero que, en cambio, cumple con las mismas funciones.
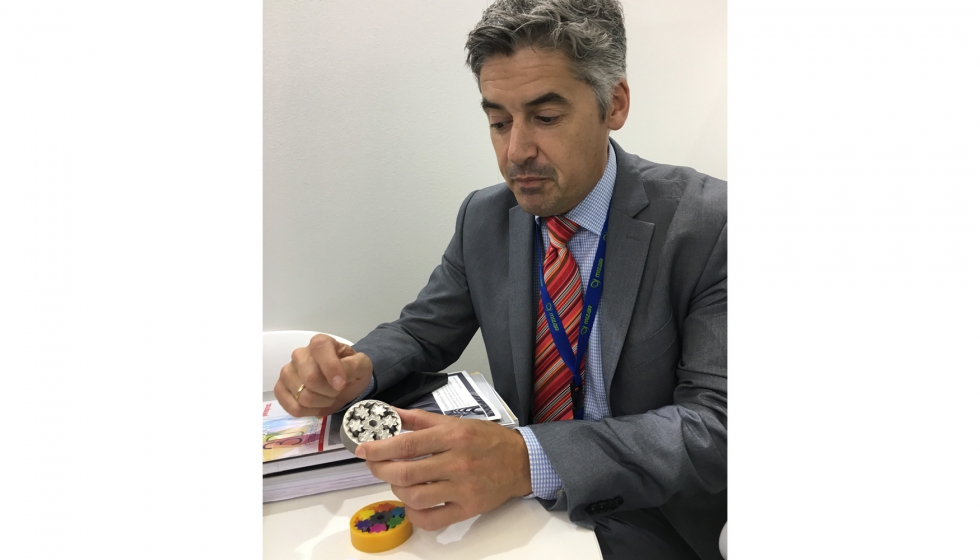
Uno de los últimos trabajos de Mizar ha sido el desarrollo de modelos estructurales para el primer nanosatélite producido en Euskadi mediante aditiva. ¿Puede explicarnos con más detalle en qué se basa el trabajo y qué aporta Mizar al proyecto?
Todo empieza con el proyecto de la empresa Karten Space. Su objetivo es dar un servicio de información a partir de la explotación e interpretación de imágenes satelitales. Por ejemplo, a empresas clientes del sector agrícola les puede reportar datos sobre plagas, necesidades de riego, estado de cosechas, etc. Dentro de este proyecto, una de las etapas era el diseño de un nanosatélite con unas prestaciones determinadas. Aquí es donde entra Mizar, poniendo a disposición de Karten la tecnología de fabricación aditiva para desarrollar un nanosatélite de avanzadas prestaciones.
Entre otras ventajas, nuestra tecnología les ha supuesto una reducción en el tiempo de desarrollo. Imprimimos un nanosatélite en horas —ellos lo tenían en días— de modo que pueden probar, decidir modificaciones, etc., de manera mucho más rápida.
De modo colateral, en Mizar hemos desarrollado también una estructura de plástico certificado por la NASA (el termoplástico Ultem 9085), más dúctil que el metal, lo que modifica la absorción de vibraciones y aporta ventajas en la fase de lanzamiento del satélite. La estructura presenta inercias térmicas menores que las de aluminio, haciendo que el satélite sea más estable en cuanto a temperatura interior se refiere. Nuestro trabajo ha sido estudiar el diseño de Karten, analizar qué podía desarrollarse mediante aditiva y construirlo.
Es decir, Mizar participa tanto en la fase de diseño como de desarrollo.
Sí. De hecho nuestro objetivo es dar un servicio de extremo a extremo. Así que participamos en la fase de diseño siempre codo con codo con el cliente, que es quien conoce qué necesita, y le acompañamos en todo el proceso. Y en función de la capacidad del cliente, de lo maduro que esté el proyecto o la tecnología que éste ya tenga, aportamos más o menos en diseño y pasamos a la fase de fabricación aditiva.
Este nanosatélite, ¿está 100% fabricado en 3D?
Su estructura sí. Solamente incluye los insertos. Básicamente por un tema de costes; desarrollar piezas seriadas en fabricación aditiva no sale rentable así que aprovechamos sus ventajas en cuanto a la libertad de diseño pero aprovechamos los elementos de fijación estándar.
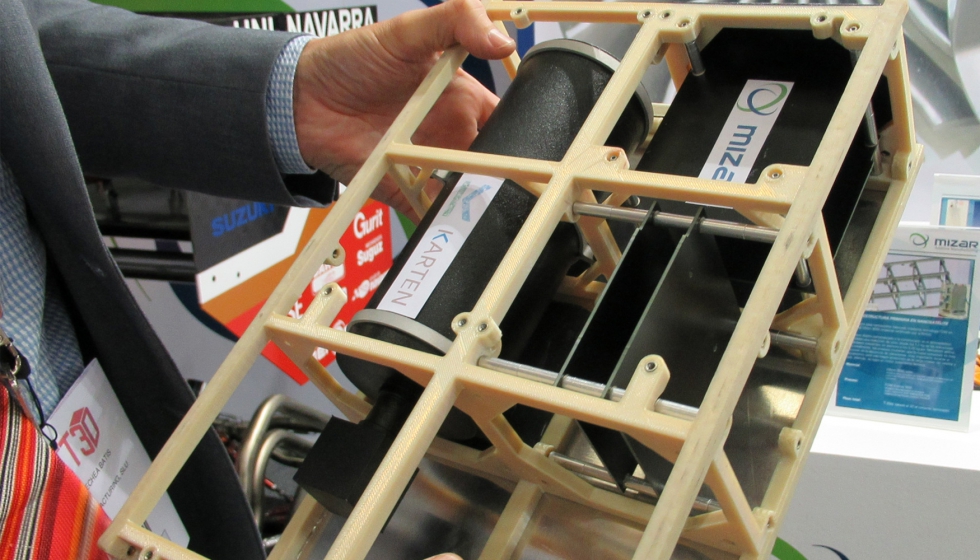
Se trata de usar la tecnología aditiva allí donde aporte ventajas...
Claro. Es el mismo caso que otra pieza realizada para, por ejemplo, ITP, para una pieza de verificación aeronáutica. La forma libre está impresa en 3D pero otras piezas, como conectores o elementos de fijación, son de tipo estándar.
Precisamente el sector aeronáutico ¿es quizá el más predispuesto a introducir la fabricación aditiva?
Es cierto. En aeronáutica hay dos factores. Uno, que los plazos de certificación y verificación son muy largos, lo que les interesa mucho acortar el tiempo de diseño; y la reducción de tiempos es una de las principales ventajas de la aditiva. Y, en segundo lugar, los kilos de material extra en el aire salen muy caros.
En automoción, por ejemplo, no hay tanta presión del peso y, en cambio, hay mucha presión del coste... y hoy existe mucha base instalada de máquinas dispuestas para trabajar a máximo rendimiento. Además, son procesos muy optimizados, con una alta rentabilidad, y cambiar esta dinámica no es sencillo.
Para Mizar, ¿cuáles son los sectores más importantes hoy día?
Aeronáutica sin duda. Industrial y médico, en segundo lugar. De hecho, en el sector médico hemos realizado proyectos muy interesantes pero son unitarios, no hay posibilidad de repetibilidad. Además, incluyen retos de certificación muy exigentes.
Participan además en el proyecto Transfon3D....
Sí, es un proyecto transfonterizo en el que colaboramos con Tecnalia, la UPV y con un centro tecnológico del Sur de Francia, Estia, junto a una serie de compañías que quieren hacer una comparativa tecnológica para desarrollar unos componentes determinados mediante un proceso de fabricación distinto. Es un trabajo de aplicación de multitecnología y multidiseño. Y Mizar se encarga de la parte de fabricación de SLM, además de ser los responsables de los prototipos.
En este tipo de proyectos, ¿cuál es el objetivo final?
Buscar las mejores tecnologías a aplicar para desarrollar una pieza concreta.. pero incluso puede suponer un cambio de diseño para adaptarlo a esta tecnología y que aporte prestaciones adicionales. Por ejemplo, hay un caso en que hemos pasado de un conjunto de siete piezas que se sueldan a realizarla en cinco piezas impresas en 3D a la vez, de las cuales una se mueve respecto a las otras cuatro. El resultado es un conjunto monolítico sin necesidad de soldadura.
Colaboración transfronteriza
El objetivo principal del proyecto Transfon3D es hacer colaborar a los centros tecnológicos, las universidades, las grandes empresas y las PME de los dos lados de la frontera, con el fin de fabricar piezas con un alto valor añadido gracias a los procesos de fabricación aditiva. Estas tecnologías están todavía en un estado de desarrollo, y requieren de conocimientos multidisciplinarios en los materiales, la simulación, los procesos de fabricación, la caracterización, etc. Actualmente, los conocimientos de cada área de especialización son distintos entre los distintos actores. Los esfuerzos conjuntos son necesarios para este nuevo reto, ya que el espacio transfronterizo Poctefa dispone de una oferta competitiva en tecnologías de fabricación aditiva.
El proyecto abordará diversos aspectos relacionados con estos métodos. Los resultados como la concepción y optimización de las piezas, la mejora de los procesos y la validación de las piezas obtenidas tras la conclusión del proyecto.
Este enfoque representa un cambio radical en los métodos de trabajo y sobre las tecnologías de fabricación. Esto ofrece ventajas como la reducción del material utilizado, la flexibilidad de diseño y la reducción del tiempo de entrega.
Por el proyecto Transfron3D, el conjunto de socios podrá disponer de distintas tecnologías, teniendo acceso a una variedad de máquinas. Estas máquinas se pueden agruparse en las siguientes tecnologías: SLM, EBM, LMD y WAAM.
La finalización del proyecto está prevista para el 31 de junio de 2019.
Para finalizar, con 3 años a las espaldas y todo el trabajo hecho, ¿qué proyectos les depara el futuro?
Tenemos muchos proyectos pero, por temas de confidencialidad del sector aeronáutico, no podemos darlos a conocer. Pero estamos haciendo mucho desarrollo de componentes por ejemplo con refrigeración interna, de formas muy complejas.. pero que por el propio acuerdo entre las empresas aeroespaciales es secreto. Así que sí existen proyectos muy potentes en este ámbito.
En la parte industrial, por otro lado, estamos desarrollando, entre otros trabajos, geometrías complejas con conductos interiores y existe un gran campo de trabajo como es el desarrollo de recambios realizados mediante tecnología aditiva y que suponen acortar los tiempos de reposición de piezas muchas veces descatalogadas, entre otros.
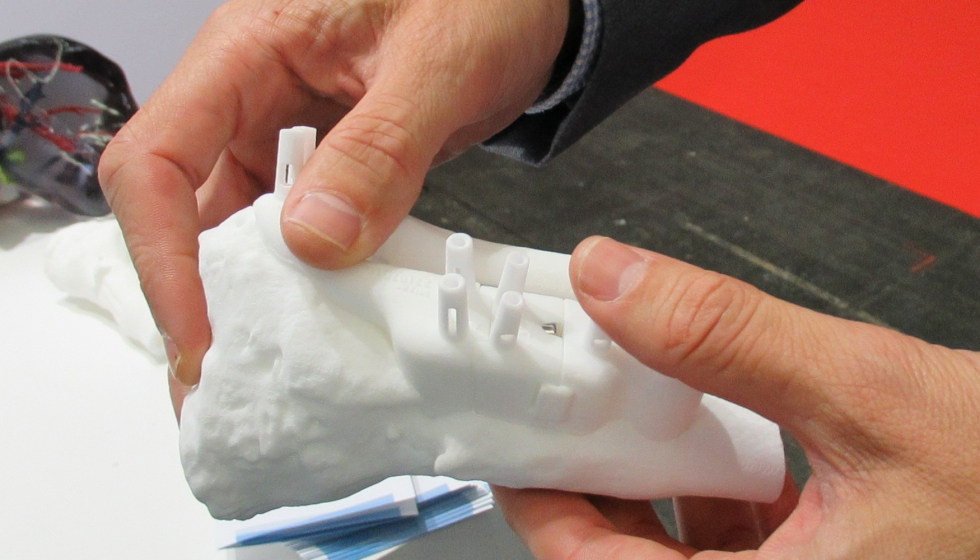
Más allá del sector aeronáutico, Mizar ha realizado importantes proyectos en el sector médico.
¿Metal o plástico?
En Mizar tienen claro que la ventaja competitiva vendrá de la mano de la fabricación aditiva con metal: “Las prestaciones añadidas son mucho mayores. En plástico la tecnología se basa en fusión de éste, lo que da lugar a prestaciones estables. En cambio, en metal, según cómo se trabaje, en qué orden se funde, se obtiene una estructura metalográfica u otra, así que supone un plus de calidad”.