Diseño de un utillaje para el posicionamiento preciso de un porta satélites para molinos de viento
Utillaje flexible e inteligente de piezas de gran tamaño para el mecanizado con cero defectos
En este artículo se describe el diseño de un utillaje inteligente y adaptativo para el posicionamiento preciso de un porta satélites para molinos de viento, una pieza con un alto costo de fabricación y requisitos muy estrictos de tolerancias. Este utillaje permite al fabricante reducir las inspecciones manuales, automatizar las tareas de ajuste y mejorar el tiempo de configuración de proceso de mecanizado, aumentando por lo tanto la productividad, la precisión de posicionamiento y la calidad geométrica requerida de la pieza. El desarrollo del utillaje inteligente se ha centrado principalmente en la concepción de un actuador de alta precisión capaz de mover grandes piezas con la tolerancia requerida. Se han realizado pruebas de validación experimental tanto del actuador electro-mecánico como del utillaje en su conjunto, asegurando así la aplicabilidad del concepto de fabricación con cero defectos en este tipo de piezas.
1. Introducción
El paradigma del control de calidad orientado a cero defectos busca optimizar todo el proceso de fabricación, desde el diseño de la pieza, el control del proceso y los sistemas de inspección en línea. Pero también otros elementos como los utillajes y el personal implicado. Ejemplo exitosos de esta metodología pueden ser encontrados en los proyectos MuProD [1] y Midemma [2]. Este trabajo aplica este control de calidad en los utillajes, debido a que son un aspecto esencial del proceso de fabricación, siendo cruciales para asegurar la calidad de la pieza de trabajo y la productividad del proceso.
1.1. Importancia de los utillajes
Los costes asociados al utillaje pueden rondar el 10-20% del coste total del sistema de fabricación [3]. Estos costes aumentan en aplicaciones para lotes pequeños ya que normalmente los utillajes son específicos para cada pieza. Por lo tanto, desde hace unos años se lleva realizando un esfuerzo importante en el desarrollo de equipos cada vez más flexibles y eficientes en el campo de los utillajes.
Un utillaje de mecanizado tiene que cumplir con dos requisitos fundamentales: a) posicionar la pieza a una posición correcta con la correspondiente precisión en relación a las herramientas de corte y b) mantener fijado el componente con la suficiente fuerza para evitar desplazamientos durante el proceso de mecanizado.
Debido a las tareas llevadas a cabo por el utillaje, su forma de actuación afecta fuertemente a la calidad final de la pieza. Los errores superficiales de la pieza de trabajo y los de la configuración del utillaje son inherentes a los procesos de mecanizado; la pieza posicionada en el utillaje tendrá en consecuencia errores de posición y/o de orientación que sin duda afectarán a la precisión del mecanizado final. Los procedimientos actuales de sujeción se realizan a través de diferentes pasos con métodos tradicionales de amarre en los que, generalmente, el éxito de la operación depende de la habilidad del operario. Por lo tanto, para evitar el error humano, es importante realizar la sujeción de la pieza de manera automática a través de sistemas de amarre, para lo cual, se requiere de una búsqueda de las tecnologías de accionamiento existentes con el fin de encontrar la solución más adecuada para la operación de amarre de la pieza.
1.2. Estado del arte
En la literatura se pueden encontrar diferentes soluciones de actuadores en la búsqueda de la mejor alternativa para satisfacer los requisitos de amarre de cada aplicación en cuanto a: rigidez de la solución, rango geométrico de la aplicación (amarre para pieza grande o pequeña), precisión del posicionamiento y coste total. Teniendo en cuenta su funcionamiento, los actuadores más utilizados son: actuadores electro-mecánicos, actuadores hidráulicos o neumáticos y actuadores piezoeléctricos.
En cuanto a los actuadores electro-mecánicos, se han diseñado diversos sistemas mecatrónicos con el objetivo de obtener utillajes flexibles y ajustables [4], [5]. Para el posicionamiento de precisión en tornos se presenta un amarre adaptrónico junto con un sistema de medida óptico y algoritmos de control [6], [7]. Esta solución ofrece la posibilidad de compensar la excentricidad a través de un ajuste de amarre activo. Para mejorar la precisión se utilizan habitualmente motores síncronos.
Los actuadores hidráulicos y neumáticos hacen la función de actuador a través de la energía del fluido (aceite o gas compresible). Como caso de aplicación de sistema accionado hidráulicamente, en [8], los autores proponen un sistema de fijación de control numérico basado en el principio de doble revolver con cilindros hidráulicos reposicionables que proporcionan la fuerza de sujeción, con una rigidez alta propia de este tipo de actuadores.
Por otra parte, una de las soluciones más innovadoras para el posicionamiento de piezas grandes usando actuadores neumáticos son los utillajes para el mecanizado flexible del tipo pin-array [9]. Estos utillajes se caracterizan por tener una serie de pasadores que sujetan la pieza ajustándose a su forma. Los actuadores neumáticos tienen características muy diversas como alta eficiencia energética, un funcionamiento y estructura sencilla, son fáciles de limpiar y son apropiados para trabajar en un ambiente hostil. Sin embargo no son adecuados para el posicionamiento de ultra-precisión.
Los actuadores piezoeléctricos convierten la señal eléctrica en desplazamiento físico controlado con precisión. Los nuevos actuadores piezoeléctricos integrados son controlados por micro controladores, que se comunican por Bluetooth a través de un control externo. Con estos actuadores se puede obtener un rango de posicionamiento de micras en dos grados de libertad. Para poder controlar la presión en los cilindros de sujeción de los mandriles se integran también sensores de fuerza [10]. De esta manera, se compensan las fuerzas centrípetas para fijarlo de una manera sensible. Los actuadores piezoeléctricos son extremadamente precisos, aunque no es la solución más apropiada para aplicaciones con alta carga de demanda debido a su alta sensibilidad al entorno.
En [11], los autores se centran en el posicionamiento automático y ajuste flexible con actuadores electro-mecánicos basado en las propiedades de los fluidos magnetoreológicos. El fluido está en contacto directo con la pieza y el campo magnético aplicado sobre el fluido aumenta su viscosidad lo que permite aplicar la fuerza de amarre sobre la ella. Como otro ejemplo de aplicación, en piezas rotatorias se propone un utillaje con fuerzas de amarre dinámicas [12].
Dado que en la literatura no se encuentra una solución comercial que cumpla los requisitos de la aplicación que se estudia en este trabajo (alta repetitividad, ultra-precisión y fácil mantenimiento, se ha desarrollado un utillaje compacto adaptativo basado en actuadores electro mecánicos de alta precisión que permite el posicionamiento activo de piezas de gran tamaño con muy alta precisión (menos de 10 micras en la posición de centrado).
1.3. Caso de estudio: requerimientos para el diseño de un utillaje flexible
El utillaje flexible ha sido diseñado para la fabricación de lotes pequeños de piezas grandes (porta satélites) para la caja de cambios de los molinos de viento, correspondiente al sector de la energía eólica de la empresa Gamesa. El mecanizado de componentes como el del porta satélites es un proceso con altos niveles de calidad que es cada vez más exigente debido a la demanda progresiva de piezas de mayor tamaño. Lograr tiempos rápidos de puesta a punto y alta precisión se está convirtiendo en un desafío, siendo afectado por el gran tamaño de los equipos de generación de energía eólica. La figura 1 muestra un ejemplo del porta satélites hecho en fundición. Las dimensiones de la pieza van de 1.000 a 2.500 mm de diámetro y un peso de hasta 3000 kg.
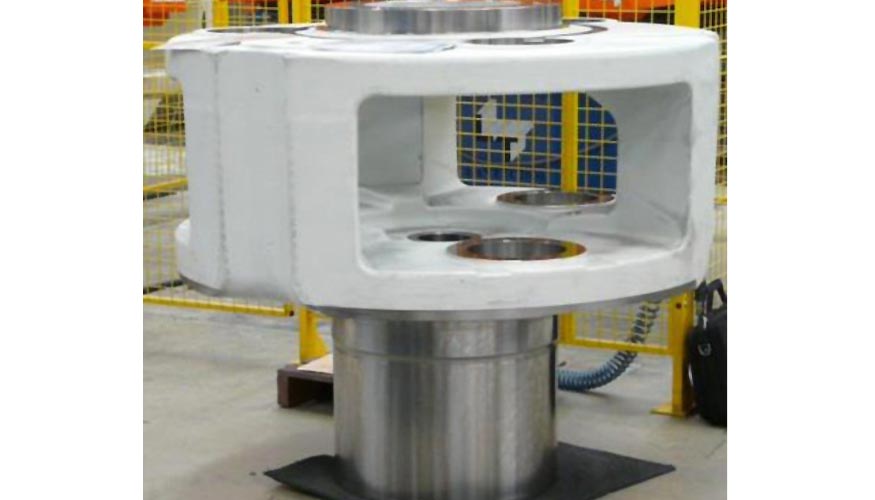
Figura 1. Porta satélites para la caja de cambios de Gamesa.
El proceso del mecanizado del porta-satélites se realiza en dos fases:
- Fase 1: El mecanizado de la cara superior de la pieza de trabajo. Su orientación respecto al utillaje actual se puede ver en la figura 2 (izquierda).
- Fase 2: Mecanizado de la zona inferior. Su orientación respecto al utillaje utilizado actualmente se muestra en la figura 2 (derecha).
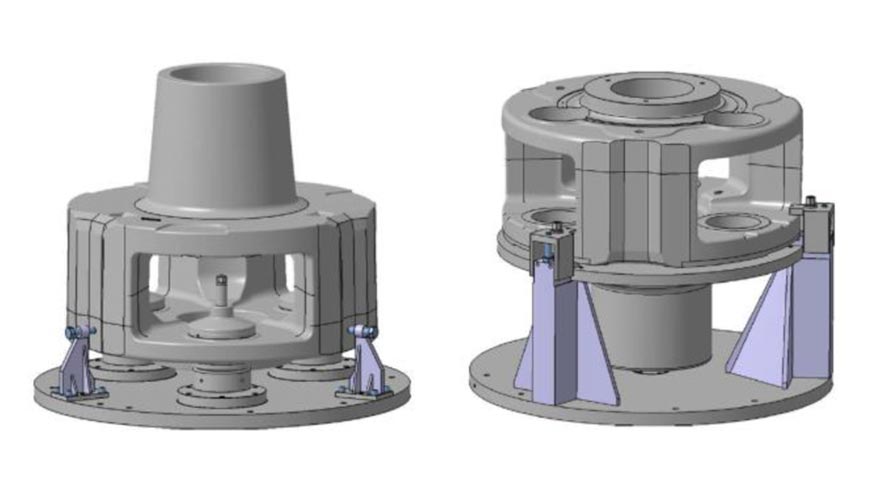
El utillaje adaptativo que se presenta se ha diseñado para realizar la fase 2, ya que es la más crítica en cuanto a las tolerancias requeridas. En este caso, el utillaje tiene que centrar la pieza respecto a la herramienta de corte con un máximo de run-out (distancia del centro de la máquina al centro de la pieza a mecanizar) diametral de 0,01 mm medido en el agujero central del porta satélites.
El torno que se utiliza para mecanizar el porta satélites tiene doble pallet por lo que mientras se está mecanizando la pieza se puede fijar una nueva pieza en el pallet exterior de la máquina a través del utillaje. Con el fin de desarrollar un utillaje flexible apropiado se ha tenido en cuenta que la tolerancia de centrado es relativa a la máquina y no a la propia fijación. Por lo tanto, la configuración del proceso tendrá un primer ajuste fuera de la máquina, en el que se pre centra la pieza con relación al utillaje, haciéndose el ajuste final dentro de la máquina mediante la medición de la desviación entre el eje vertical de la pieza de trabajo y el eje de referencia de la máquina.
Actualmente el procedimiento de fijación de la pieza es totalmente manual, consta de varios pasos y el éxito de la operación depende considerablemente de las habilidades del operario. Algunos de los inconvenientes de la puesta a punto que se dan en la actualidad son los siguientes:
- Baja productividad debido a la constante inactividad de la máquina para la medición del área de trabajo con unas tolerancias muy estrictas.
- Las operaciones de ajuste implican una gran cantidad de intervenciones manuales introduciendo la incertidumbre del factor humano.
- Se necesitan operarios con gran experiencia para los procesos de posicionamiento, amarre y medición de la pieza.
- El tiempo del procedimiento es alto: se dedica mucho tiempo a comprobar el posicionamiento y tolerancias de la pieza antes y después de amarrarla y después de cada operación de mecanizado para asegurar una pieza final válida.
Con el objetivo de resolver los inconvenientes actuales se ha diseñado un utillaje inteligente y flexible con los siguientes objetivos:
- Diseño modular adecuado para piezas de diferentes diámetros.
- Reducción del tiempo durante el proceso de centrado a través de la automatización del ajuste y medición.
- Aumento de la productividad al disponer de más tiempo de mecanizado y reducir el tiempo de fabricación de la pieza.
Teniendo en cuenta estos objetivos se ha llevado a cabo el diseño, fabricación y validación del utillaje.
2. Descripción del utilaje flexible propuesto
2.1. Diseño del utillaje
Se ha diseñado el utillaje con el objetivo de posicionar con una precisión de 0,01 mm y fijar automáticamente el porta-satélites, sin la necesidad de ninguna ayuda adicional. El diseño del utillaje puede verse en la figura 3.
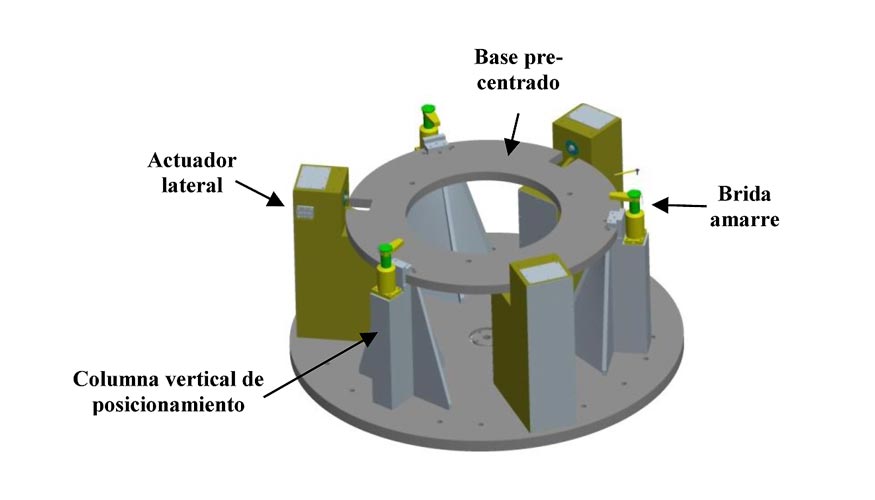
El sistema se compone de los siguientes componentes mecánicos:
- Base de pre-centrado con sistema poka-yoke para posicionar el porta-satélites en la fase 2 en una posición conocida respecto a la fase 1.
- Columnas verticales de posicionamiento. El porta-satélites se posiciona sobre estas columnas, que disponen de una parte roscada a ellas con una planitud muy precisa en las que se apoya la pieza.
- Fijación a través de las bridas de las columnas para sujetar la pieza de trabajo.
- Actuadores laterales. Actuadores electro mecánicos lineales diseñados específicamente para conseguir las estrictas tolerancias requeridas.
El proceso para la configuración de la pieza en el utillaje consta de los siguientes pasos:
- Se posiciona, se centra y se fija la base del utillaje con las tres columnas y los actuadores laterales sobre el pallet exterior de la máquina.
- El porta satélites se posiciona en el utillaje sobre las columnas. Se posiciona en una posición definida por un sistema poka-yoke.
- Las tres bridas fijan el porta satélites. Es importante que estas bridas actúen sobre los elementos de soporte para evitar deformaciones no deseadas.
- El palé exterior gira y el utillaje flexible junto con el porta satélites se introducen dentro de la zona de mecanizado de la máquina.
2.2. Tecnología de amarre: diseño del accionamiento lineal
Uno de los requerimientos más críticos a la hora de realizar el posicionamiento del porta satélites es hacerlo dentro de una tolerancia máxima de 10 μm. Por lo tanto, se ha decidido seleccionar actuadores electro mecánicos debido a sus características de precisión, alta capacidad de carga y longitud de carrera. Dados los requisitos especiales a la hora de mover una pieza de 3.000 kg con una precisión de 10 μm, se ha desarrollado un accionamiento especial para la aplicación de estudio.
Se ha diseñado un accionamiento muy preciso y fiable con el objetivo de ajustar lateralmente el porta satélites dentro de una tolerancia diametral de 10 μm, se muestra en la figura 4.
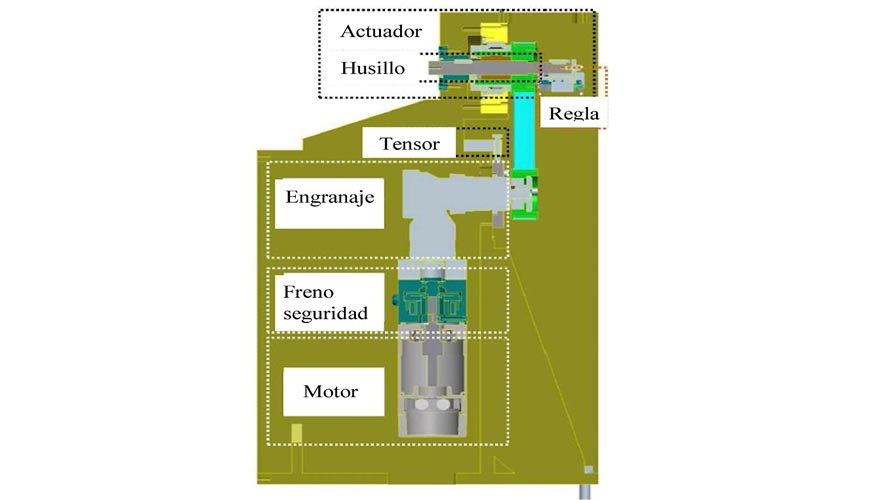
El accionamiento se puede dividir básicamente en tres secciones diferentes:
- Componentes de movimiento: motor síncrono, freno de seguridad y caja de cambios, encargados de generar el par necesario para mover la pieza.
- Sistema de transmisión: el husillo seleccionado tiene un recorrido muy pequeño de 1 mm con el fin de obtener un accionamiento muy preciso, por lo que se obtiene un alto par por unidad de volumen activo.
- Reglas: a parte de los encoder de los motores, se han incluido reglas magnéticas pequeñas adicionales para las etapas lineales de menor tamaño debido a que la tolerancia de centrado es muy crítica. Su longitud de medida es de 30 mm con una resolución de 0.1 micras.
Desde el punto de vista del control de la posición, la mejor opción es usar un motor síncrono con un encoder. La resolución del encoder y la relación entre los grados y el desplazamiento dará el algoritmo de control la relación necesaria para mover el husillo.
El utillaje tiene tres actuadores, situados en forma circular con un ángulo de 120º entre ellos. Son módulos independientes y pueden ser fijados y retirados de la base del utillaje, por lo tanto, el sistema modular puede ser adaptado fácilmente a piezas de diferentes diámetros cambiando la posición radialmente.
Una vez introducido el utillaje y la pieza en el interior de la máquina, se necesita realizar el centrado de la pieza con una precisión de run-out diametral de 0,01 mm. Para ello, el accionamiento es controlado a través de los algoritmos de control que se explican a continuación.
2.3. Utillaje inteligente: control del proceso de centrado
El centrado de la pieza consta de dos etapas. En primer lugar, cuando el utillaje está fuera de la máquina, la pieza está precentrada con las columnas verticales pasivas y las bridas sujetando la pieza en esa posición. En este paso no hay ninguna intervención activa de los actuadores. En una segunda etapa, el palé junto con el utillaje y el porta satélites se introducen en el torno siendo necesario un nuevo proceso de centrado debido a que el centro de la pieza de trabajo tiene que estar en el mismo eje vertical de la máquina. Para este ajuste se ha desarrollado un controlador utilizando un control PID para controlar el movimiento de centrado del porta satélites
Para el lazo de control, se recogen por un lado las señales del encoder del motor y la escala de cada actuador junto con el valor de la posición obtenido con la sonda dentro del torno y se comparan ambos valores hasta tener posicionada la pieza en la tolerancia requerida.
Para ajustar la pieza, los tres husillos se mueven hacia adelante hasta que cada uno de ellos toca la pieza. En ese momento, la sonda de contacto mide la posición real del centro del porta satélites en relación al eje vertical de la máquina.
El algoritmo de control de posición calcula el movimiento que cada uno de los actuadores debería aplicarle a la pieza, y después de que los actuadores hayan hecho esta operación y posicionen el porta-satélites dentro de tolerancias, las bridas amarran la pieza y el husillo de los actuadores retrocede liberando la pieza de trabajo.
Finalmente, el utillaje flexible desarrollado permite un proceso de centrado inteligente del porta-satélites gracias a los algoritmos de control programados.
Dado el peso de la pieza y que en esta operación el tiempo no es una restricción, se ha decidido que el control de los accionamientos se realice de manera desacoplada, es decir, moviéndose uno a uno. Como los accionamientos se posicionan cada 120º alrededor de la pieza, un accionamiento corresponde al eje 'y', y los otros dos tendrán componentes en los ejes la 'x' e 'y'. Por otra parte, no se fija la asignación de los accionamientos a un eje; dependerá del accionamiento más cercano a la pieza, que será asignado automáticamente al eje la 'y'.
Para la simulación, se ha programado en Matlab-Simulink un Modelo de Realidad Virtual. Está conectado al controlador con el fin de proporcionar una visualización del proceso de centrado. Por otra parte, se ha creado un modelo con el CAD final del utillaje para la interacción con los lazos de control en Simulink. Este modelo permite conocer el efecto del proceso de centrado y la variación de los parámetros del controlador en el conjunto utillaje-pieza en términos de estabilidad y reacciones que tiene que soportar cada componente.
En la figura 5 se muestra el diagrama de flujo para el ajuste de centrado de la pieza en máquina y el esquema del centrado del porta-satélites. Algunas de las variables que se presentan en la figura 5 derecha son: MC es el centro de la máquina y PC es el centro de la pieza, D1-D2-D3 son los actuadores y el algoritmo se ejecuta a través del PLC.
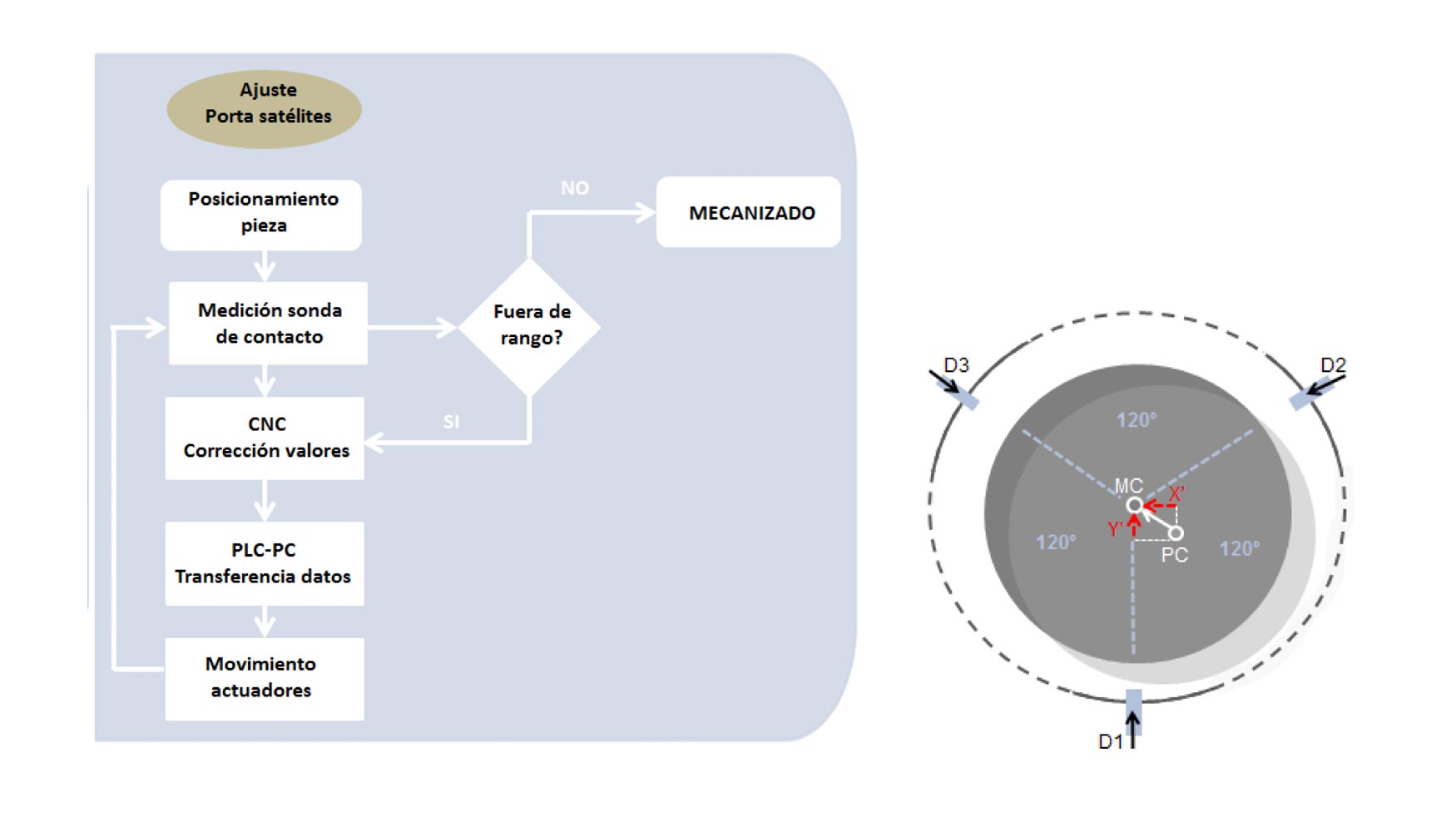
3. Validación experimental
Tras fabricar y ensamblar el utillaje, de acuerdo con el diseño antes expuesto, se ha realizado la validación mecánica del conjunto y de las estrategias de control de los actuadores. El objetivo de estos ensayos ha sido el de validar tanto la precisión como la repetitividad obtenida con los actuadores. De acuerdo con los requerimientos derivados de la producción de este tipo de piezas, la precisión del movimiento obtenida por cada actuador tiene que ser igual o menor de ±10μm. Para validar que efectivamente se obtienen estas precisiones, se han realizado individualmente en cada actuador dos tipos de ensayo:
- Ensayos en vacío: validación del actuador sin contacto con la pieza y en todo el rango de desplazamiento disponible (2.000 μm).
- Ensayos con carga: validación del actuador moviendo la pieza y en un rango de desplazamiento limitado a la corrección de posicionamiento de la pieza, esto es, 100 μm.
El programa desarrollado para controlar el actuador realiza el desplazamiento en dos etapas: controlar el desplazamiento hasta tocar la pieza y mover el porta-satélites a la distancia comandada. Las mediciones de precisión y repetitividad se han realizado mediante sondas de contacto distribuidas en diferentes zonas del conjunto. En la figura 6 se muestra el utillaje en el pallet exterior de la máquina.
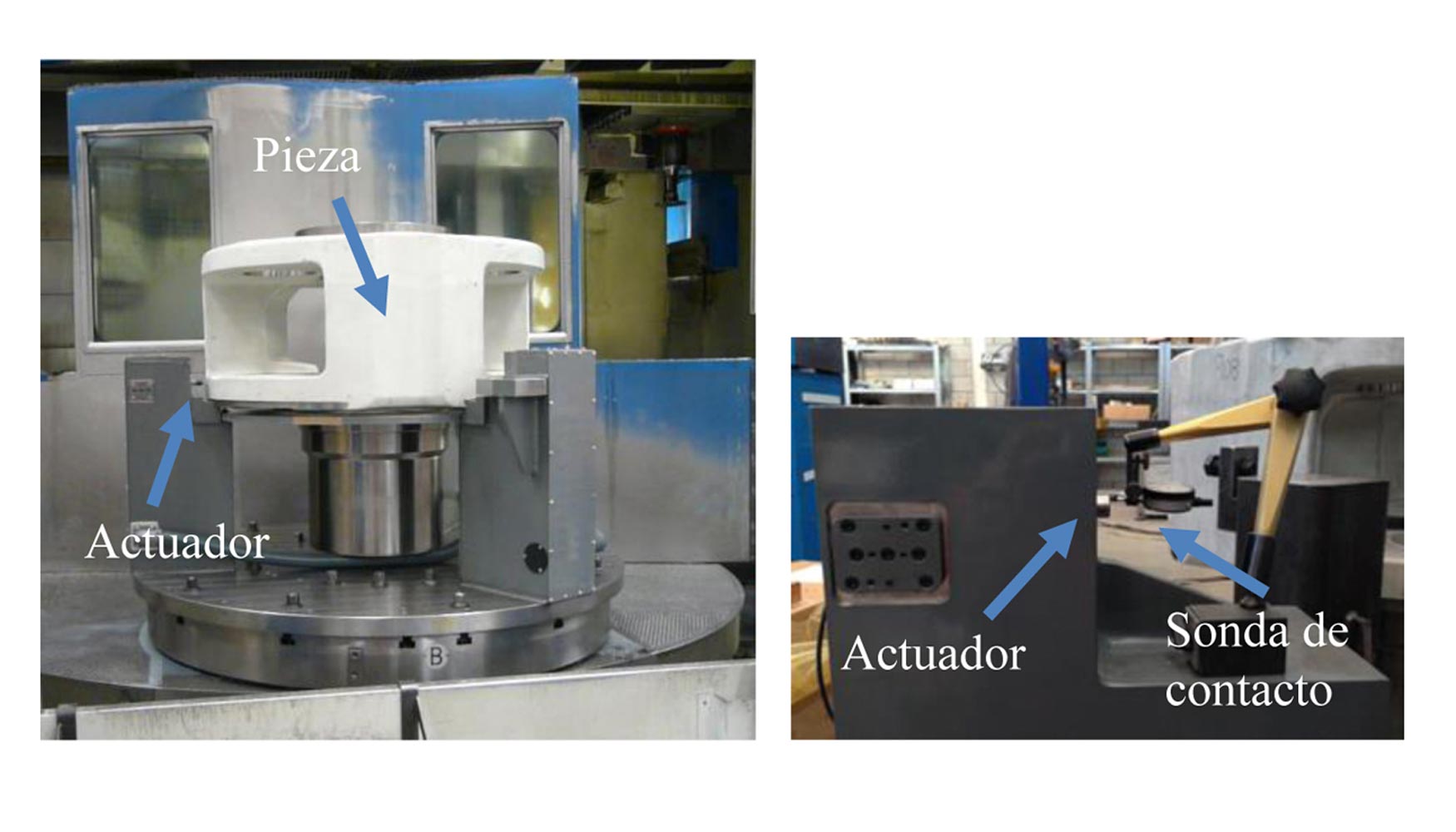
3.1. Ensayos de movimiento en vacío
El objetivo de estas pruebas ha sido evaluar la repetitividad, precisión y linealidad de todo el espacio de trabajo del propio actuador. Los movimientos en vacío compararon los valores de la regla magnética y el desplazamiento del encoder del motor con las medidas de desplazamiento de la sonda de contacto.
Debido a las características del actuador el recorrido disponible tiene una longitud máxima de 2.000 μm. Para poder adquirir adecuadamente a lo largo de esta distancia, los ensayos se han dividido en tres zonas intercaladas entre sí:
- Zona 1: entre 100 y 1000 μm
- Zona 2: entre 900 y 1800 μm
- Zona 3: entre 1600 y 2000 μm
Las zonas están intercaladas entre sí para garantizar que hay una continuidad en el desplazamiento del actuador y linealidad en el espacio de trabajo. Además, para asegurar que el desplazamiento registrado es independiente de la consigna introducida, se han implementado diferentes incrementos de desplazamientos prorrateados entre 10 y 100 μm. En la figura 7, a modo de ejemplo, se muestran los resultados obtenidos en uno de los actuadores:
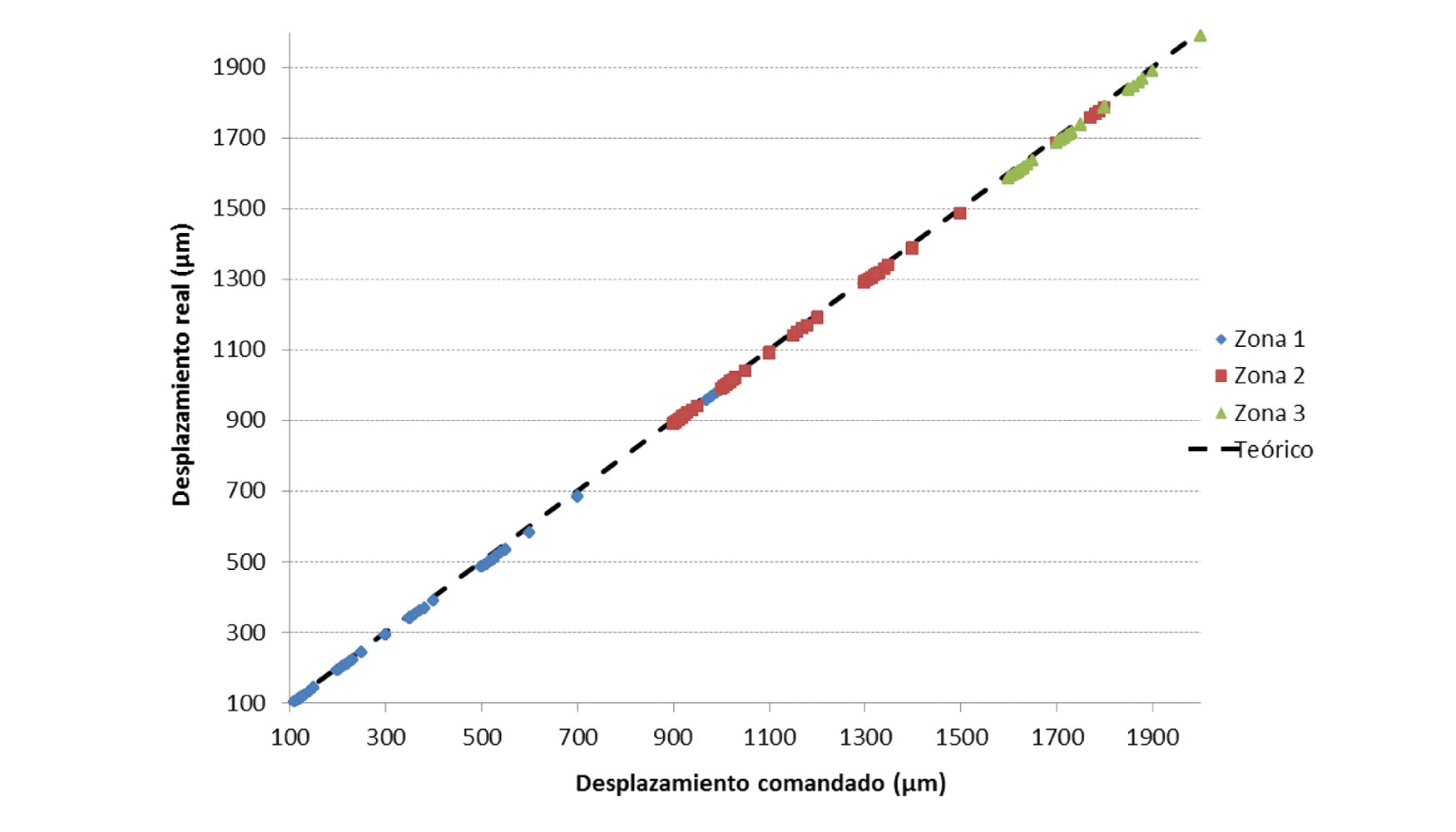
Para cada zona analizada, se muestra en forma de puntos el desplazamiento real frente al desplazamiento comandado, y el movimiento teórico a través de la línea negra. La variación máxima medida ha sido de 3 μm entre la medición de referencia y el desplazamiento real. Para comprobar que los resultados obtenidos con el actuador son repetitivos, se han repetido los ensayos varias veces, como se muestra en la figura 8:
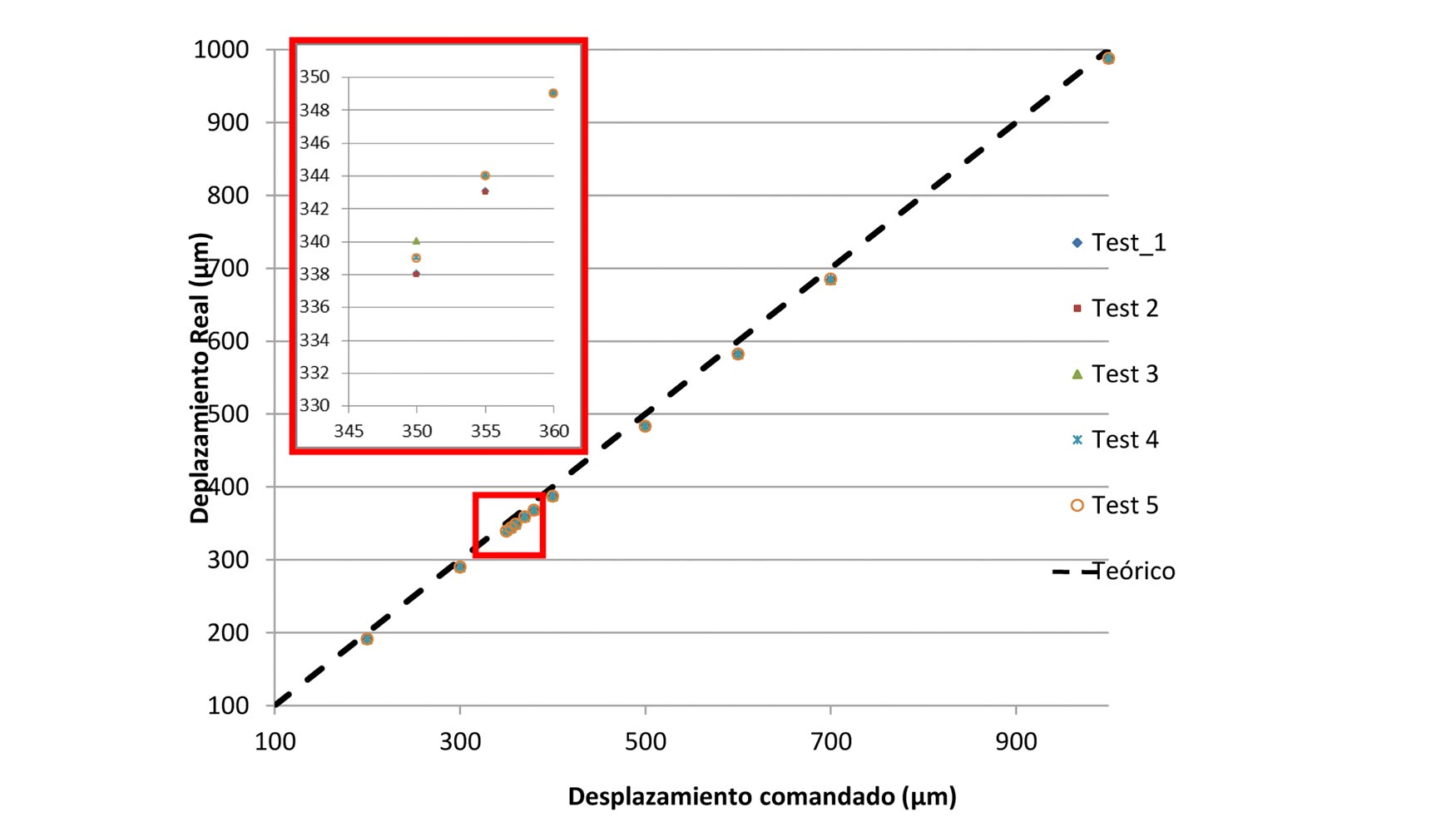
Como se puede apreciar, tras cinco repeticiones para cada caso, las distintas mediciones indican que el movimiento del actuador tiene una repetitividad de +/-1 μm.
3.2. Ensayos de movimiento en carga
Una vez validado el comportamiento mecánico sin carga, se ha evaluado el funcionamiento de los actuadores moviendo el peso de la pieza. Una vez que el husillo toca la pieza y el controlador asegura las condiciones del actuador, entonces el par permitido aumenta hasta los 0,7 Nm hasta mover la pieza. Este par es el mínimo que rompe el fenómeno de stick-slip generando un movimiento con velocidad constante.
En este caso, se ha estudiado la precisión del desplazamiento por debajo de 10 μm, por lo cual se ha limitado el ensayo de empuje de la pieza a 100 μm. Además, para cada movimiento de actuador se han hecho dos repeticiones, para verificar su repetitividad. Así, los resultados se muestran en la figura 9:
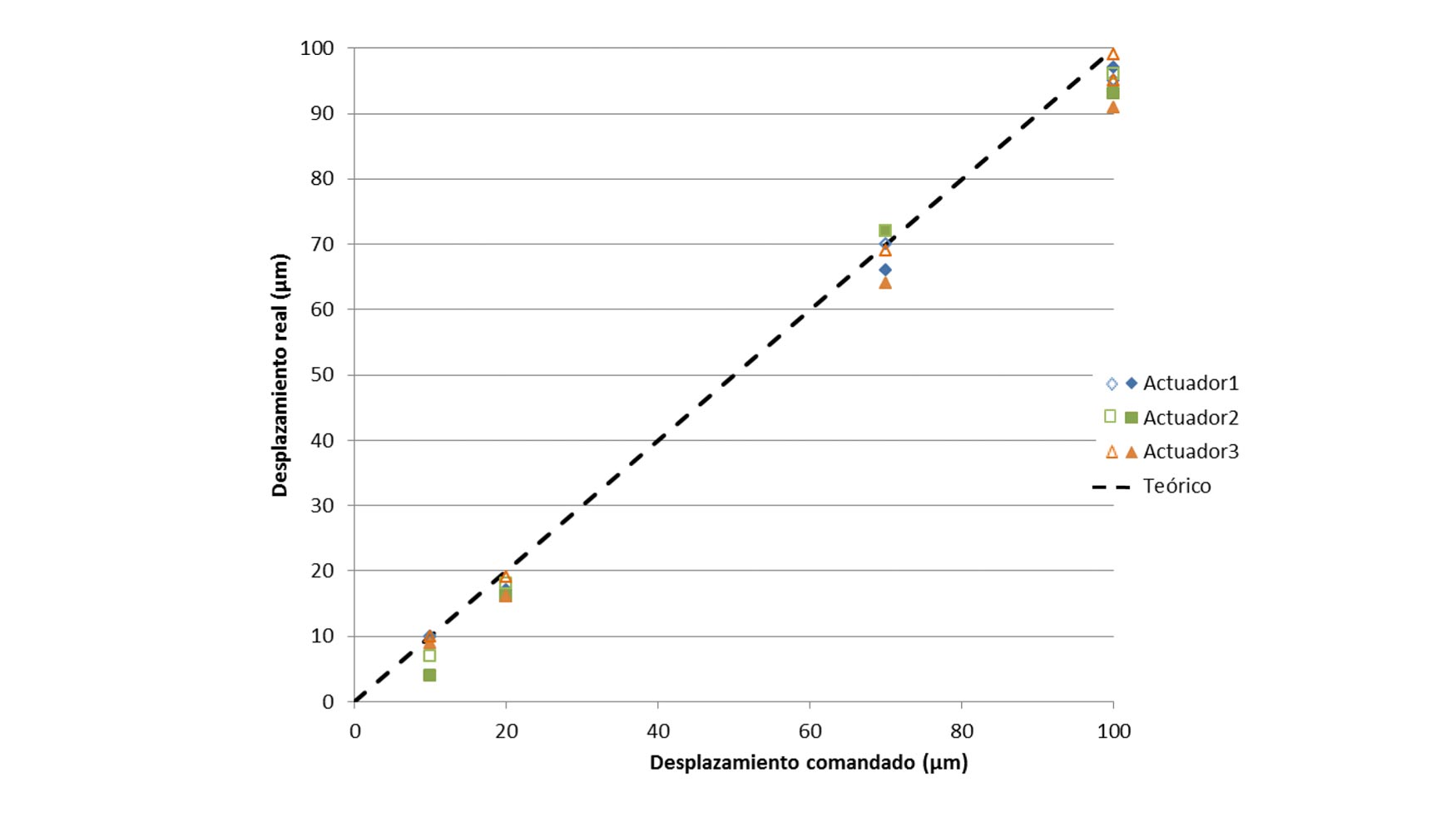
Por lo tanto, se ha comprobado que a la hora de colocar la pieza, los actuadores cumplen con los requerimientos de tolerancia y repetitividad definidos por el proceso productivo de +/-10 μm.
4. Conclusiones
Se ha diseñado un utillaje flexible e inteligente para el posicionamiento preciso de piezas de gran tamaño como el porta-satélites de Gamesa. Se han realizado varias pruebas para caracterizar el funcionamiento de los actuadores en vacío y con carga. Los resultados obtenidos han demostrado que el utillaje propuesto es capaz de centrar el porta-satélites dentro de la tolerancia exigida de +/-10 μm, y que es posible controlar este movimiento por medio de un PLC.
El desarrollo del utillaje flexible se ha centrado principalmente en la concepción de un actuador de alta precisión capaz de mover piezas grandes con la tolerancia requerida. Con la validación de estos actuadores, el nuevo utillaje modular permite al fabricante aumentar la productividad ya que el ajuste se realiza de manera automática reduciendo el tiempo utilizado por sus operarios en la misma tarea.
Una vez validado el utillaje mecánicamente, el siguiente paso es la integración del sistema de monitorización y control de posición de la pieza con el que, mediante un proceso iterativo, se centraría la pieza en pocos minutos, reduciendo así el tiempo de puesta a punto actual. Un factor importante a analizar durante éste proceso iterativo será la durabilidad de los actuadores en condiciones de producción reales.
Agradecimientos
Los autores de este trabajo quieren agradecer a la Comisión Europea por la financiación del proyecto ‘Intefix - INTElligent FIXtures for the manufacturing of low rigidity components’ bajo el acuerdo de concesión Nº 609306, dentro del 7º Programa Marco de Investigación y Desarrollo Tecnológico.
Referencias
[1] http://www.muprod.eu/
[2] http://www.midemma.eu/
[3] Bi ZM, Zhang WJ. Flexible fixture design and automation: review, issues and future direction. Int. J. of Prod. Research; 2001;39/13, p.2867–94.
[4] Mannan MA, Sollie JP. A Force-Controlled Clamping Element for Intelligent Fixturing. CIRP Annals; 1997; 46/1, p. 265–268.
[5] Papastathisa T, Bakkera O, Ratcheva S, Popov A. Design Methodology for Mechatronic Active Fixtures with Movable Clamps. 45th CIRP Conf. on Manufacturing Systems, Procedia CIRP; 2012; p323-328.
[6] Denkena B, Immel J, Götz T. Drehspannfutter mit integrierter, mechatronischer Feinpositioniervorrichtung. Int. Forum Machatronik Augsburg Deutschland; 2005.
[7] Haase R, Seewig J, Reithmeier E. Verbesserte Hartfeinbearbeitung von Zahlrädern.Werkstattstechnik online; 2006; 95:6, p. 447-452.
[8] Tuffentsammer K. Automatic loading of machining system and automatic clamping of workpieces. CIRP Annals; 1981; 30, p. 553–558.
[9] Hurtado JF, Melkote SN. A model for synthesis of the fixturing configuration in pin-array type flexible machining fixtures. Int. J. of Mach. Tool. and Manu.; 2002; 42/7; p. 837-849.
[10] Uhlmann E, Feng P, Döll, S. Dynamic clamping force for jaw-chucks for high speed turning. Prod. Eng. Res. Dev.; 2004; 11:1, p. 149-152.
[11] Andrew Y, Nee C. MAFFIX Project COP-CT-2006-032818, Completely flexible an reconfigurable fixturing of complex shaped workpieces with MRF; 2006.
[12] Chakraborty D, De Meter EC, Szuba PS. Part Location Algorithm for an Intelligent Fixturing System. Part 1: System Description and Algorithm Development. J. of Manuf. Systems; 2002; 20/2, p. 124–134.