Desarrollo de un prototipo para el marcado láser de grandes superficies
En este trabajo se ha desarrollado un prototipo de máquina de marcado 3D de superficies extensas integrando un láser de fibra, sistema óptico de guiado y cabezal de espejos galvanométricos en un centro de mecanizado. En este sistema se ha sincronizado el movimiento de los ejes de la máquina con los propios del escáner, de manera que se pueden marcar componentes de grandes dimensiones y de geometría 3D compleja de forma continua, evitando errores de solapamiento y reduciendo tiempos de ciclo. Esta publicación describe el prototipo realizado e incluye resultados experimentales que comparan la nueva técnica propuesta con el proceso convencional de marcado mediante posicionamiento discreto.
1. Introducción
El marcado láser es un proceso en auge. Una de las aplicaciones con más proyección futura es el marcado de componentes de automoción con fines decorativos y estéticos. Las nuevas herramientas de diseño y los avances en los procesos de fabricación permiten que estos componentes sean cada vez de mayor tamaño y con formas más complejas por lo que su tratamiento presenta mayores dificultades.
Hoy en día, este proceso se lleva a cabo direccionando el haz láser mediante dos espejos galvanométricos integrados en lo que se denomina escáner [1, 2]. El tamaño y configuración de estos espejos, junto con las lentes situadas a la salida del escáner, determinan las características del mismo: área de trabajo, distancia focal, velocidad del proceso, tamaño de la huella o spot, etc.
La gran ventaja de estos dispositivos es que permiten marcar texturas complejas a gran velocidad gracias a la elevada dinámica de los espejos. Sin embargo, una de sus limitaciones reside en que el área de trabajo y la profundidad de foco están definidas por el sistema óptico, lo que genera problemas a la hora de procesar piezas de tamaño mayor a su área de trabajo o superficies que nos sean planas (curvadas, escalonadas, etc.). En la actualidad, para abarcar piezas de este tipo es necesario dividir el área de marcado en secciones más pequeñas y marcar dichas partes de forma individual, solapando áreas de trabajo [3]. Esto genera errores de continuidad de textura en las transiciones entre secciones que no son aceptables en aplicaciones decorativas.
En los últimos años se está intentando dar solución a este problema [4], aunque no existe un producto que lo solvente completamente. Así, por ejemplo, la empresa norteamericana Aerotech [5] ofrece un sistema que combina un escáner con ejes lineales, sincronizados mediante un controlador propio, para aumentar el área de trabajo. Sin embargo, este sistema solo está disponible para el marcado de superficies planas. Por otro lado, los principales fabricantes de escáneres, ya han lanzado sistemas de marcado 3D [6] en el que añaden un dispositivo óptico adicional al escáner para modificar la distancia focal. Sin embargo, dichos fabricantes no presentan soluciones con respecto al marcado continuo de grandes áreas, más allá del uso de lentes de enfoque f-theta de muy alta focal, limitadas por la precisión de posicionado de las mismas y el aumento del spot de láser así como en el tratamiento de campos de trabajo de grandes dimensiones. En este documento se presenta el trabajo realizado en el desarrollo de un prototipo de máquina de marcado láser para componentes de grandes dimensiones y geometrías (superficies) complejas. Se muestra a su vez la validación de la etapa de marcado de superficies extensas 2D de forma continua. Este trabajo es fruto de la colaboración de Construcciones Mecánicas José Lazpiur, como fabricante de la máquina, Maier S.Coop., como usuario de la misma, e IK4-Tekniker como soporte para el desarrollo de la nueva máquina/proceso.
2. Trabajo preliminar
El presente trabajo se ha centrado en el desarrollo de una máquina de marcado láser de superficies extensas de geometría 3D, capaz de sincronizar los tres ejes de un escáner con los tres ejes lineales de una máquina estándar, que sirva además para un amplio rango de aplicaciones. Para ello se han utilizado la capacidad de marcado al vuelo (‘Marking-On-The-Fly’) del propio escáner que ya ofrecen los principales fabricantes. El concepto de ‘Marking-On-The-Fly’ se aplica para marcar componentes que se desplazan en una cinta transportadora en continuo movimiento. La tarjeta controladora del escáner recibe la señal de lectura de encóder de la cinta transportadora y corrige las consignas para conseguir la geometría correcta. Usando las señales de encóder de los ejes lineales adicionales en lugar de los de una cinta es posible sincronizar su movimiento con un escáner y ampliar el área de trabajo efectiva de la máquina. En primer lugar se ha llevado a cabo la elección de la fuente láser y el sistema óptico de guiado. Para ello, se han estudiado los requerimientos en cuanto a potencia, duración de pulso y frecuencia de repetición necesarios para realizar el marcado adecuado sobre los materiales a tratar (metales y polímeros). Además de las especificaciones en cuanto a la interacción radiación-materia se ha introducido el requerimiento relativo a la integración industrial y tiempos de ciclo. Tras el estudio se ha seleccionado un láser pulsado de duraciones de pulso del orden de nanosegundos, de 40 W de potencia media máxima emitiendo en una longitud de onda λ=1.070 nm y de frecuencias de repetición de pulsos f ϵ [0-1.000] kHz. La radiación de dicho láser es guiada hasta la pieza de trabajo a través de una escáner galvanométrico 3D compuesto por un sistema de espejos galvanométrico 2D y un sistema óptico que actúa como tercer eje y que permite modificar la posición del plano focal dependiendo de la geometría de la pieza real, objeto del proceso de marcado.
Para validar el proceso, se han realizado varias series de ensayos preliminares sobre una pieza polimérica cromada. El objetivo perseguido ha sido encontrar el rango de frecuencias de repetición, duraciones de pulso, número de pasadas y potencia promedio mediante el que se consigue la ablación del cromo sin producir degradación en el polímero.
3. Desarrollo del prototipo
Como base para el desarrollo del prototipo de grabado/marcado láser 3D se ha elegido una máquina Deckel Maho modelo DML60HSC de tres ejes lineales de movimiento, con control Heidenhain, y carenado y ventanas de protección preparadas frente a la radiación láser (nivel de seguridad clase I). En ella se han integrado los siguientes módulos (véase la figura 1):
- Sistema óptico. Formado por el sistema de escaneado 3D seleccionado en la etapa anterior, basado en un escáner de espejos galvanométricos combinado con un variador de distancia focal y comandado por una tarjeta y software de control. El sistema óptico lo completa un objetivo de 255 mm de focal para dirigir el haz laser sobre la zona de trabajo.
- Fuente láser. Se ha integrado en la máquina una fuente láser pulsada de ns, de potencia media máxima de 40 W y frecuencias de repetición hasta 1.000 kHz. Los parámetros característicos del láser se controlan a través de la tarjeta de control mencionada anteriormente.
- Cámara de posicionamiento. Se ha integrado en la máquina una cámara CCD integrada en el eje Z para poder posicionar de forma precisa el haz láser sobre la zona de interacción. A su vez se ha integrado un sistema de aspiración adosado al cabezal tipo escáner.
- Sistema de aspiración. Necesario para la absorción de vapores o partículas que se desprendan durante el proceso de marcado y evitar así ensuciar la lente de proceso, que puede derivar en posibles defectos (microgrietas, partículas de polvo fundidas, quemaduras, etc.) en la propia lente de proceso así como pérdidas de potencia.
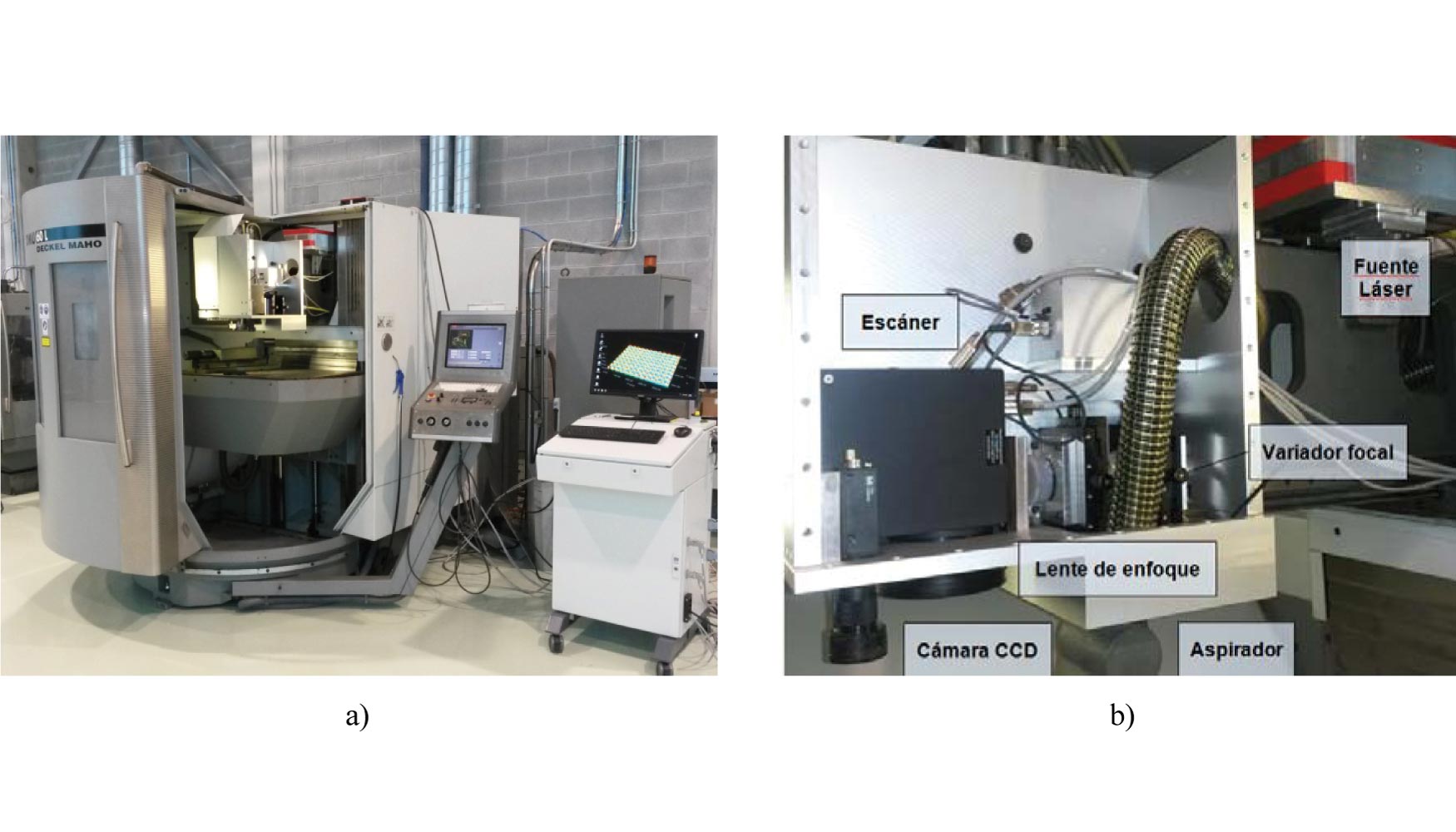
La tabla 1 muestra las principales características del sistema resultante de combinar los distintos módulos presentados.
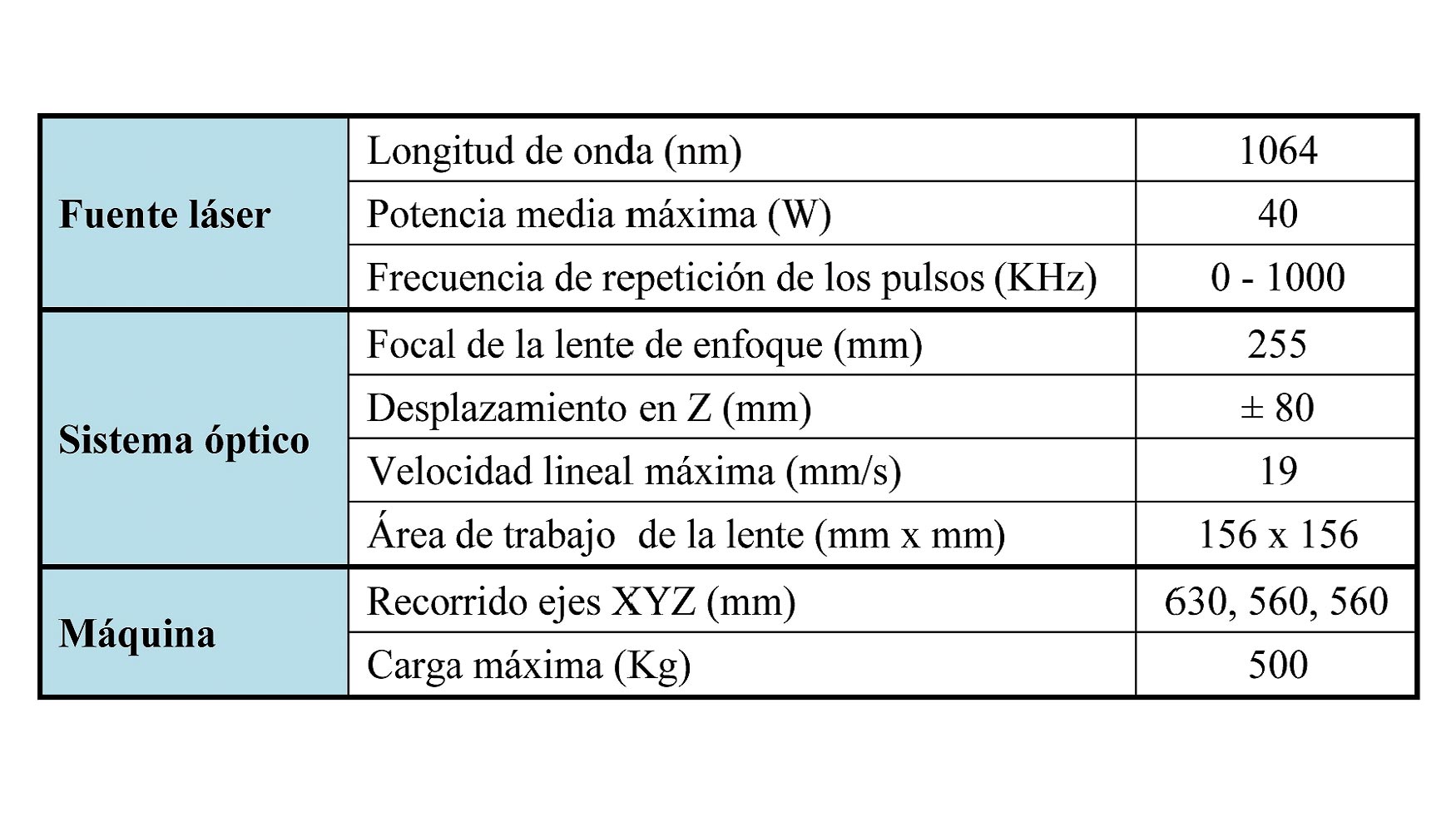
La targeta de control integrada es un elemento clave en este sistena ya que se encarga de comandar los movimientos a los espejos del escáner. También se encarga de encender el láser de manera sincronizada con el porpio escáner. Asimismo, la tarjeta proporciona la posibilida de tener en cuenta movimientos de la pieza a la hora de realizar el marcado (capacidad ya nombnrada anteriomente como ‘Marking-On-The-Fly’). Dispone a su vez de unas entradas adicionales a través de las cuales se alimentan señales de encóder apopiadamente tratadas para determinar desplazamientos de la pieza y aplica correccines en los movimientos de los espejos para que la geometría marcada sea correcta.
Con el fin de sincronizar los ejes lineales de la máquina con los del escáner se han vampirizado las señales de las reglas de dichos ejes y se han adaptado al tipo de señal requerido por la tarjeta de control del escáner. Las reglas Heidenhain LS486 instaladas en la máquina proporcionan una señal de 1 Vpp mientras que la nueva tarjeta requiere de una señal TTL en su entrada de encóder. Se ha utilizado un interpolador Heidenhain IBV6000 para cad uno de los ejes de movimientos. Este dispositivo permite convertir señales del tipo Vpp a TTL o a otra Vpp de diferente amplitud. Al tener dos salidas, se ha configurado una igual que la entrada (1 Vpp) para conectarla al CNC y otra como TTL para alimentar la tarjeta de control. Se han realizado cableados específicos para cada conexión (ver figura 2). El sistema desarrollado se aplica a dos ejes de movimiento, por lo que el esquema superior se duplica, incluyendo un interpolador adicional para el segundo eje. Las señales de salida configuradas como TTL de cada uno de los interpoladopres se han conectado con los pines de encóder de la entrada de ‘Marking-On-The-Fly’ de la tarjeta de control.
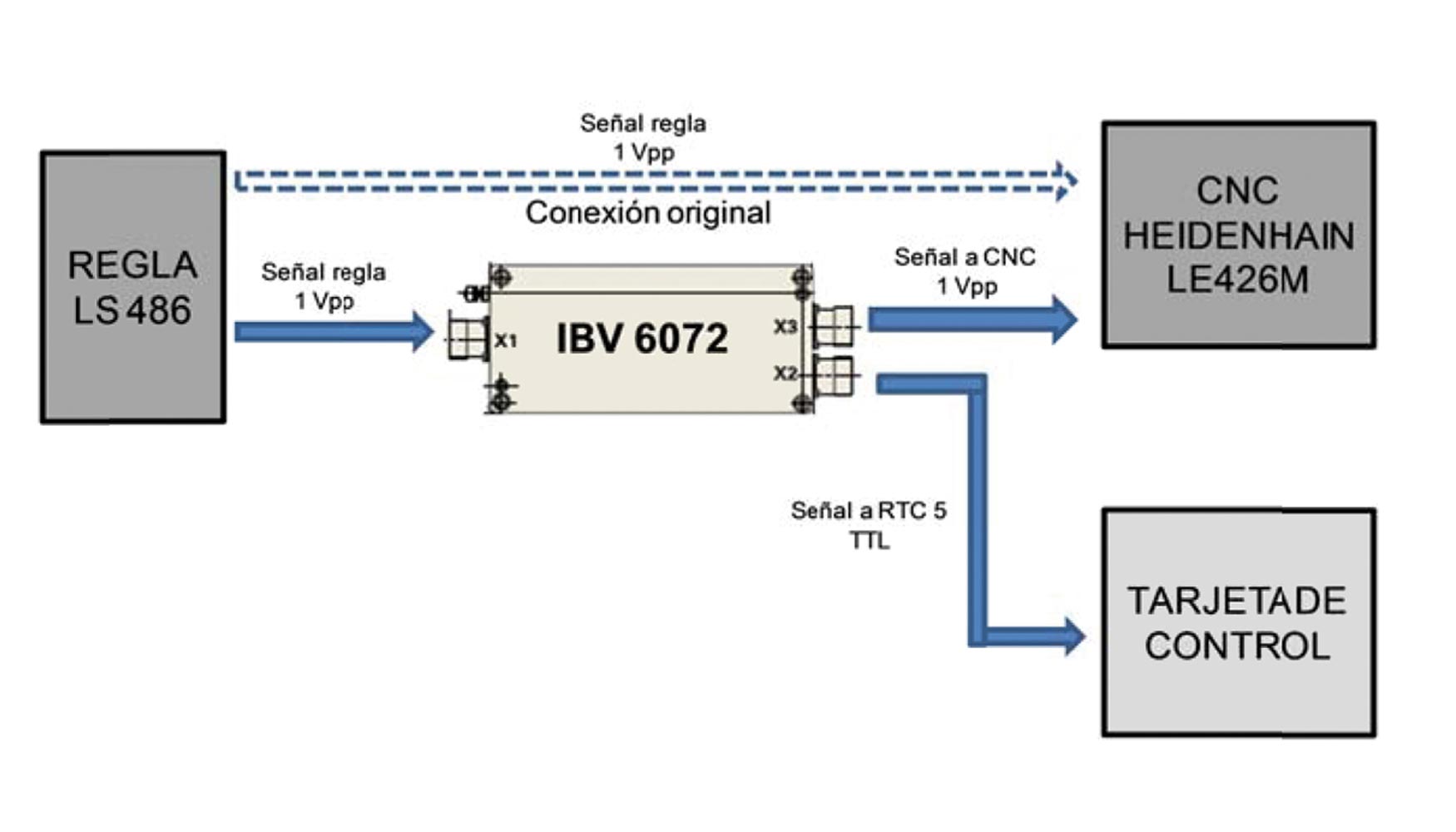
La textura a marcar se programa en su totalidad en el software de marcado compatible con el sistema de escaneado. El software se encargará de generar las consignas de los diferentes espejos del escáner para realizar dicha textura correctamente. En cuanto al movimiento de los ejes lineales, estos deben acompañar al spot láser durante el proceso de marcado de forma que este se mantenga en todo momento dentro del área de trabajo del escáner. En la figura 3 se muestra un ejemplo simple de este fenómeno, donde se muestra por un lado el caso dónde los ejes están sincronizados y la trayectoria se ejecuta correctamente y por otro cuando el eje lineal se mueve de manera descoordinada respecto al movimiento del spot láser. En este caso se puede observar en la figura que la trayectoria seguida por el haz láser no se corresponde con la referencia.
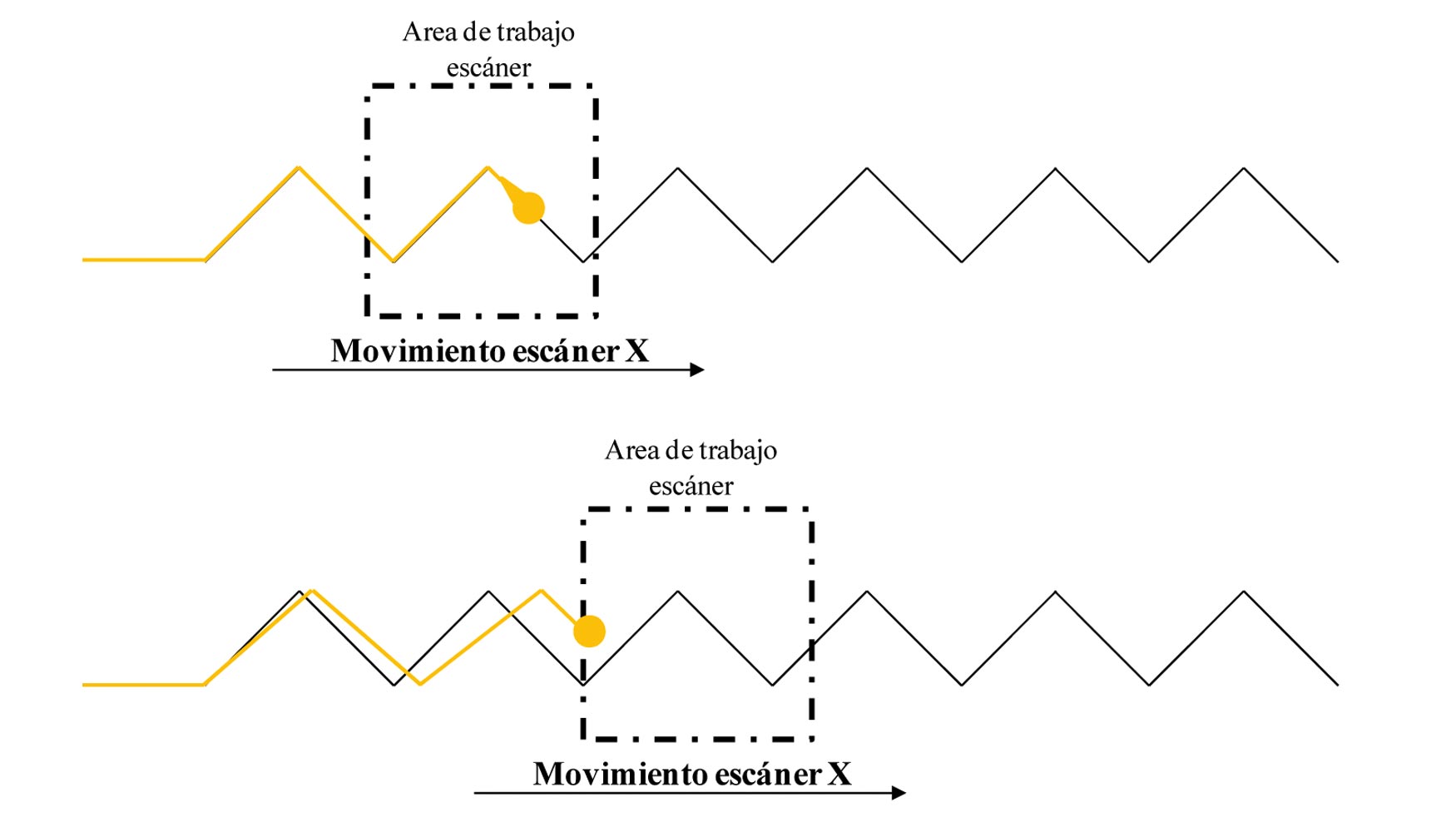
4. Validación experimental
Se ha realizado una validación preliminar del sistema realizando una textura continua de un área mayor que la propia área de trabajo del escáner sobre una chapa de Aluminio. Concretamente, se ha seleccionado una textura continua de un área de 400 x 200 mm2, tal y como se muestra en la figura 4. La textura y estrategia de marcado completa se ha programado en el software del sistema de escaneado, donde también se configuraron los parámetros de marcado correspondientes: potencia media máxima de 40 W, frecuencia de repetición de pulsos de 30 kHz y velocidad lineal de proceso combinada de 100 mm/s. Los ejes lineales se han programado de manera independiente de manera que el haz láser pueda seguir la trayectoria marcada (flechas naranjas en la Figura 4) sin salirse del área de trabajo del escáner.

La sincronización del escáner con los ejes lineales resultó satisfactoria y se consiguió marcar la superficie sin discontinuidades y manteniendo la geometría original (Figura 5).
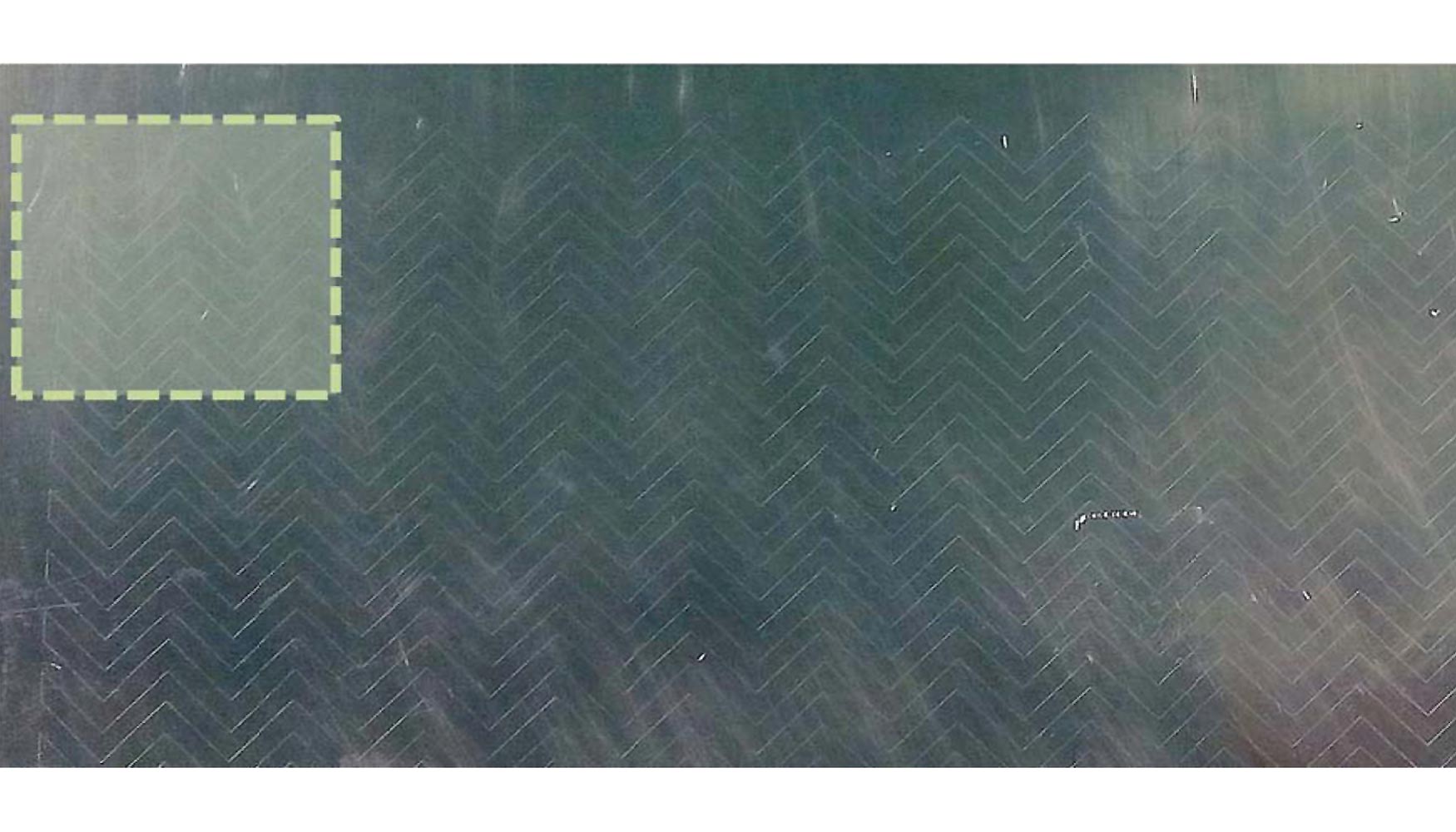
5. Conclusiones y líneas futuras
Se ha diseñado y fabricado un prototipo para marcado láser que permite procesar superficies grandes y complejas garantizando un marcado continuo. El prototipo realizado combina un escáner 3D con los ejes lineales de una máquina de manera sincronizada. Se han realizado unas primeras pruebas para validar el funcionamiento del prototipo y verificar la capacidad de marcar superficies 2D mayores que el área de trabajo del escáner de manera continua. Los resultados han sido satisfactorios. o La validación de esta plataforma da pie a la realización de nuevas actividades en un futuro próximo como:
- Marcado de texturas reales con fines estéticos aplicadas en piezas de automoción
- Marcado de superficies de geometría 3D en los que se necesite una sincronización del foco dinámico con el resto del sistema.
Agradecimientos
Este trabajo ha sido financiado por el Gobierno Vasco a través del programa Etorgai (Proyecto μlantegi 2013-2015) y mediante el presupuesto del Fondo Europeo de Desarrollo Regional (Feder).
Referencias
[1] W. Steen, J. Mazumder, Laser Material Processing, 4ª Edición, Springer, 2010.
[2] Sintec Optronics Technology Pte Ltd; Laser Marking Heads (Laser Scanners, Scan Heads), http://www.sintecoptronics.com/catalog/markinghead.pdf
[3] J. Diaci, D. Bracun, A. Gorkic, J. Mozina; Rapid and flexible laser marking and engraving of tilted and curved surfaces, Optics and Lasers in Engineering 49 (2) 195–9, 2011.
[4] K. Kim, K. Yoon, J. Suh, J. Lee; Laser Scanner Stage On-The-Fly Method for ultrafast and wide Area Fabrication, Physics Procedia, 12, 452-458, 2011.
[5] Aerotech; NMark - Integrated Galvo and motion Control; Documento Técnico/comercial
[6] Scanlab; RTC5 Control board; Catálogo comercial; Diciembre 2014