Efecto del aporte térmico en las propiedades mecánicas de la aleación del aluminio
Dr. Alberto Echeverría: director tecnológico Lortek-IK4.
Msc. Egoitz Aldanondo: Ingeniero de investigación Lortek-IK428/12/2012
El objetivo del presente trabajo fue estudiar el efecto del aporte térmico en las propiedades mecánicas de la soldadura FSW en una aleación de aluminio AW6082 de 5 mm de espesor. Se realizó la caracterización microestructural de las uniones soldadas, se realizaron perfiles de microdureza y se evaluaron las propiedades mecánicas a través de ensayos de tracción y fatiga. Se obtuvieron uniones libres de defectos con buenas propiedades mecánicas para las dos configuraciones analizadas.
Introducción
El proceso de soldadura por fricción mediante agitación o batido (FSW, Friction Stir Welding) fue inventado en 1991 y patentado por el centro The Welding Institute (Reino Unido) [1]. Se trata de un proceso de unión en estado sólido y sin aporte de material [2, 3], cuyos excelentes resultados de calidad y gran rango de aplicación en diversos materiales, incluso en algunos considerados hasta ahora insoldables, lo convierten en una tecnología muy atractiva para numerosos e importantes sectores industriales. Este proceso ha sido capaz de eliminar defectos en aleaciones de aluminio difícilmente soldables por fusión (2xxx y 7xxx) [4-6] tales como agrietamiento o microporosidad y también se ha aplicado con éxito en otras aleaciones de aluminio endurecibles por precipitación (6xxx), en otros materiales como pueden ser aceros al carbono, aleaciones de cobre, titanio, magnesio, etc. [7-14] y últimamente se está utilizando para unir materiales de diferente naturaleza o materiales disimilares [15, 16].
Los procesos convencionales de soldadura por fusión, tales como MIG/MAG, TIG, soldeo láser o por haz de electrones presentan diversos tipos de problemas característicos del proceso: gran cantidad de calor generado por el arco; necesidad de empleo de fundentes; incompatibilidad (en ocasiones) de las propiedades mecánicas del metal de aporte y el metal base. Estos problemas conducen a la aparición de diferentes tipos de defectos tales como, elevadas distorsiones de los elementos soldados, inclusión de escorias en la unión soldada, excesivas salpicaduras durante el proceso y excesiva porosidad.
La técnica se centró inicialmente en aleaciones de aluminio pero ya se ha extendido a otros materiales como los aceros al carbono para distintas aplicaciones en los sectores de automoción, ferrocarril y construcción naval, las aleaciones de titanio (sector aeronáutico), las aleaciones de magnesio (sector de automoción), otros materiales (cobre, plomo, níquel, etc.). En el Simposio Internacional de FSW y en la reunión anual de la Comisión III del Instituto Internacional de Soldadura (IIW), se han identificado las áreas de trabajo en las que se debe profundizar para que esta tecnología se pueda diseminar y aplicar de manera extensa en los sectores de las industrias aeroespacial, aeronáutica, automoción o de defensa. Las temáticas claves que requieren un esfuerzo de investigación para que se favorezca de esta tecnología son: Fatigue properties, True lightweight construction, Coatings of the FSW tools, Surface contamination of the workpieces, Modelling, Tolerances, FSW specific design, Cost factors and models, Normalisation (Quality standards), Development of NDT techniques, Microstructural Development y Life in service (mechanics and corrosion).
Teniendo en cuenta estas directrices se optó por realizar el proyecto de investigación ‘Optimización de procesos de unión mediante Friction stir welding para elementos de alta exigencia sometidos a fatiga en el transporte (composolda V2)’ con expediente Nº IMDEEA/2011/168 (subvencionado por el Instituto de la Pequeña y Mediana Empresa, Impiva), dependiente a su vez de la Conselleria de Empresa, Universitat i Ciencia de la Comunidad Valenciana), en colaboración con el Centro de Investigación en Tecnologías de Unión (Lortek-IK4), con el que se pretendió estudiar la soldadura FSW en la aleación de aluminio AW6082-T6 y analizar los mecanismos que controlan las propiedades mecánicas (dureza, tracción, fatiga), la corrosión, las características microestructurales de las uniones por FSW y su correlación con los parámetros de soldeo.
En lo que respecta a las propiedades mecánicas de aleaciones de aluminio soldadas por FSW, Von el Strombeck et al. [17] y Mishra et al. [18], realizaron estudios de FSW en una aleación 7075 para determinar las propiedades a tracción en distintas zonas de la unión utilizando miniprobetas de tracción. Se obtuvo una resistencia casi constante en la zona nugget, el esfuerzo de fluencia alcanzó un valor equivalente al 80% del material base, la resistencia última esta cerca del 100% y la ductilidad se mejora significativamente. Un esfuerzo último, relativamente alto, y una alta ductilidad en esta zona se atribuyen a la microestructura de grano fino generada. Por otro lado, cerca de la región de transición de nugget/ZACM, la resistencia permanece igual a la de la zona del nugget, pero la ductilidad empieza a dirigirse hacia la del metal base. La disminución en ductilidad comparada con la del centro del nugget puede ponerse en correlación al hecho que la ZACM retiene la estructura deformada.
Elangovan et al. [19], realizó una aproximación mediante un modelo matemático para predecir los valores de resistencia a tracción en función de las variables del proceso FSW (perfil, velocidades de avance y rotación, fuerza axial aplicada por parte de la herramienta) en juntas a tope en aleaciones de aluminio AA6061. La resistencia máxima se logró con una adecuada combinación de las variables, dada una velocidad de rotación de 1.200 rpm y una velocidad de avance de 1,25 mm/s, realizando pruebas con diferentes geometrías de pin, donde la geometría de pin cilíndrico roscado fue la que mejor presentó un comportamiento mecánico.
James et al [20], realizó estudios para predecir las propiedades de fatiga de uniones tipo FSW en aleaciones 5083-H321. Se evaluó la influencia de la velocidad de avance, la población de defectos y la curva S-N de fatiga. El trabajo sugiere que las variables principales que afectan a la vida a fatiga son las tensiones residuales, la relación microestructura/dureza y la presencia de pequeños defectos.
En otro trabajo muy interesante relacionado con el comportamiento a fatiga y fractura, Lockyer [21] analizó resultados de ensayos de fatiga S-N en muestras con y sin defectos. La conclusión principal es que las uniones por FSW tienen resistencia estática y dureza inferior que la del material base pero resistencia a fractura o desgarro superior. A diferencia de las soldaduras convencionales, los ensayos de fatiga indican propiedades de fatiga similares al del material base si hay ausencia de defectos.
Ghidini y Dalle Donne [22] estudiaron el efecto de las tensiones residuales en la velocidad de crecimiento de grietas por fatiga en uniones FSW. Explicaron como análisis simplistas de ensayos obtenidos a bajas relaciones de tensión, R, indican propiedades de fatiga mejores que el material base si el efecto de las tensiones residuales no se tiene en cuenta. Han desarrollado una técnica simplificada de medida de tensiones residuales, ‘cut compliance’, que demuestra que la velocidad de crecimiento de grietas en FSW están dentro de la banda de dispersión del material base si se utiliza la fuerza impulsora efectiva, en la que se incluyen las tensiones residuales.
Desarrollo experimental
En primer lugar se buscó una aleación de aluminio envejecible (por las características mecánicas), de fácil conformado plástico (extrusión, laminado) y de buen comportamiento frente a la corrosión y fatiga. Con estas características nos encontramos con la familia de aleaciones AA 6XXX de las cuales destacan la 6063, 6061 y 6082 todas ellas en estado de tratamiento térmico T6. La seleccionada para este proyecto fue la AW6082-T6 de 5 mm de espesor con la composición química que se muestra en la tabla 1.

El centro de investigación en tecnologías de unión, Lortek-IK4, realizó dos tipos de soldaduras FSW con los siguientes parámetros de soldeo:
• 10-1500
- Velocidad de rotación: 1.500 rpm
- Velocidad de avance: 10 ipm = 254 mm/min
- Relación de soldeo: 0,17 mm/revolución (aporte térmico alto)
- Fuerza axial: 1.350 lbf = 6 kN
- Ángulo de inclinación: 1,5º
• 20-900
- Velocidad de rotación: 900 rpm
- Velocidad de avance: 20 ipm = 508 mm/min
- Relación de soldeo: 0,56 mm/revolución (aporte térmico bajo)
- Fuerza axial: 2.700 lbf = 12 kN
- Ángulo de inclinación: 1,5º
La herramienta utilizada se observa en la figura 1 y tiene las siguientes características geométricas:
- Diámetro hombro: 15 mm
- Diámetro del pin: 4 mm
- Longitud del pin: 4,8 mm
- Tipo de pin: roscado
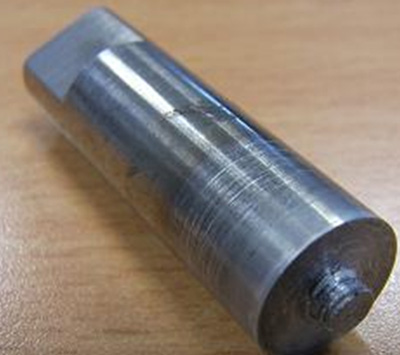
Se realizó un análisis microestructural de las distintas muestras soldadas, previamente preparadas según los métodos descritos en la norma ASTM E3 – 95: corte de la probeta, embutición de la muestra, desbaste manual, pulido manual y ataque con agente reactivo. Para obtener la microestructura se utilizó el reactivo de ataque a color Weck’s (100 ml H2O, 4 g KMnO4, 1 g NaOH) a temperatura ambiente y con un tiempo de inmersión de aproximadamente 20 segundos. Para la caracterización de las uniones soldadas se empleó la técnica de microscopía óptica (OM). Para la caracterización mecánica se realizaron ensayos de tracción de acuerdo con la norma ASTM E8M-04, ensayos de fatiga según la norma ASTM E466-02 (para el diseño de la probeta de ensayo) y ASTM E739-91 (para el análisis de los datos) con una relación de carga R=0,1, una función carga-tiempo sinusoidal (amplitud constante) y una frecuencia de oscilación de 7 Hz. El área real de interés de las soldaduras era la vida infinita (>106 ciclos) pero las aleaciones de aluminio, generalmente, no muestran un límite de fatiga asintótico [23]. Finalmente se realizaron barridos de microdureza según UNE-EN ISO 9015-2:2011.
Resultados y discusión
1. Caracterización microestructural
En la figura 2 se presentan las macrografías, en estado de pulido, de las soldaduras realizadas donde no se revelan ningún tipo de fisuras o poros a partir de las líneas de unión que indiquen alguna falta de penetración por parte del pin, por lo que se trata de soldaduras sanas. Tampoco se observa la presencia de defectos típicos de la soldadura FSW conocidos como: tunnel defect, pin hole, kissing bond, worm hole o piping defect [24].
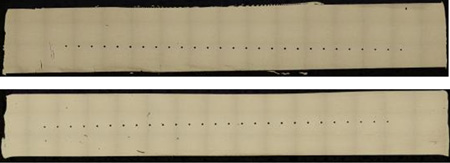
En las figuras 3 y 4 se presentan las micrografías en estado de ataque, obtenidas a través de microscopía óptica, para la muestra 10-1500 (aporte térmico alto) y 20-900 (aporte térmico bajo), respectivamente. Los parámetros microestructurales a que se refiere este estudio, corresponden a las diferentes zonas encontradas en la soldadura por fricción-agitación: metal base (MB), zona afectada térmicamente (ZAC), zona afectada termomecánicamente (ZACM), zona nugget (ZN).
En el MB los granos son alargados debido a su proceso de fabricación (laminación) y en la ZN son equiaxiales y finos. Este refinamiento es resultado de la recristalización dinámica, es decir, una acción combinada de alta velocidad de deformación y elevada temperatura. Dicha estructura recristalizada se caracteriza por un nivel muy bajo de tensiones residuales, excelente ductilidad y propiedades mecánicas superiores a las de la ZAC [25].
Para obtener el tamaño de grano de la ZN se aplicó la relación empírica obtenida por S. Rajakumar, et. al [24], donde relacionan la resistencia a tracción con el tamaño de grano de la ZN a partir de resultados experimentales en una aleación AA6061-T6 soldada por FSW:
ợb = 252.4 – 1.339G (1)
Donde:
ợb: Resistencia a tracción [MPa]
G: tamaño de grano de la ZN [µm]
Se obtuvo un tamaño de grano de la ZN de 24.94 µm para la configuración con alto aporte térmico y de 17.47 µm para la configuración de bajo aporte térmico, lo que implica que a medida que aumenta el tamaño del grano, la resistencia a la tracción disminuye.
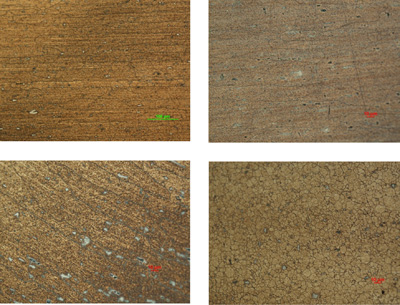
La zona TMAZ tiene los granos deformados, alargados y curvados debido a la deformación a la que fueron sometidos (figuras 3b y 4b) y en ocasiones alguna recristalización local. La microestructura de la ZAC es similar a la del MB, los granos son un poco más grandes como resultado de la exposición al calor de la soldadura (figuras 3b y 4b).
Se observan precipitados que varían en tamaño y morfología a lo largo de las diferentes zonas FSW. En placas soldadas por FSW de AA6082-T6, se reportó que la fase β” se encuentra dispersa homogéneamente en el material base, pero se disuelve en la ZN, la ZATM y en la parte principal de la ZAC [26, 27]. Durante el enfriamiento de la soldadura, la precipitación de partículas, que son menos eficaces en el endurecimiento, como la fase β’, se lleva a cabo rápidamente en la región ZAC de dureza mínima. En la ZN, con altas temperaturas pico, todos los precipitados β” se disuelven, pero la precipitación β’ no tiene lugar debido a la velocidad de enfriamiento. En las regiones donde se produce la disolución, un envejecimiento natural puede provocar algunas precipitaciones de las zonas GP [28].
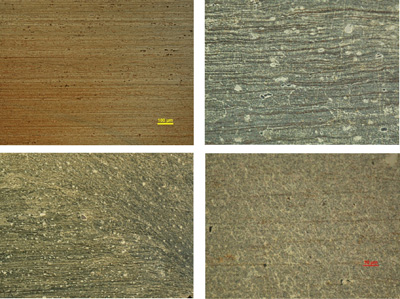
Figura 4. Imágenes de microscopía óptica de la muestra 20-900 atacada: a) MB 100X, b) ZAC 500X, c) ZACM 100X, d) ZN 1000X.
i. Ensayos de microdureza
En los perfiles de microdureza obtenidos para las dos configuraciones la dureza disminuye desde el metal base hacia el centro de la soldadura, llega a un valor mínimo en la ZAC, luego aumenta en la ZN quedando finalmente con un valor por debajo del material base. En la figura 5 se observa que la dureza aumenta con la disminución del aporte térmico, posiblemente porque se disuelve menos cantidad de precipitados (también se genera un tamaño de grano más pequeño). En aleaciones endurecidas por envejecimiento, el nivel de dureza tiende a disminuir en la ZAC, lo que indica que el ciclo térmico durante el proceso de soldadura tiene una influencia significativa, ya sea por sobre-envejecimiento o al disminuir la densidad de dislocaciones, probablemente por ambos factores en aleaciones completamente envejecidas. Mientras que el endurecimiento por trabajo es el efecto dominante cerca de la ZN. También es posible que se pueda alcanzar una temperatura suficientemente alta áreas locales que permitan la disolución parcial de precipitados, especialmente en el ZATM.
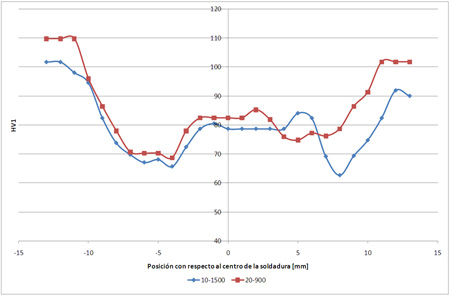
ii. Ensayo de tracción
En la tabla 2 se presentan los resultados obtenidos de las probetas sometidas al ensayo de tracción. Los parámetros de proceso con fuerte influencia en las propiedades mecánicas son la velocidad de rotación de la herramienta y la velocidad de avance de la herramienta, los cuales definen el calor específico suministrado a la soldadura (aporte térmico). En los dos casos las muestras presentaron el fallo en la ZAC por el lado de avance, similar a lo reportado en [25].
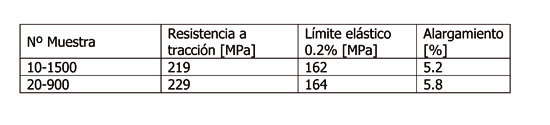
Se puede observar que disminuyendo la velocidad de rotación (1500 a 900 RPM) y aumentado la velocidad de desplazamiento (de 254 a 508 mm/min) la resistencia mecánica de la unión aumenta. Esto se puede atribuir a la disminución del aporte térmico y el ablandamiento limitado relativo del material en la ZAC [26].
iii. Ensayos de fatiga
La figura 6 muestra las gráficas de fatiga obtenidas para las dos condiciones de FSW, donde se observa que la configuración con parámetros de procesado FSW de alto aporte térmico tiene una mayor resistencia a fatiga, además muestran un comportamiento clásico que revela una tendencia del aumento de resistencia a la fatiga a medida que disminuye la amplitud de la tensión cíclica.
Los resultados de los ensayos muestran que el comportamiento a fatiga de las uniones FSW disminuye con una velocidad de avance mayor y menor velocidad de rotación, es decir, un aporte térmico bajo. Cavaliere y Panella [30] también comunicaron que la resistencia a fatiga de las aleaciones más comunes disminuye a medida que la relación velocidad de avance/velocidad de rotación es mayor. Por otra parte, Ericsson y Sandström [31] reportaron que con una velocidad de avance baja obtuvieron los mejores resultados a fatiga en una aleación de aluminio 6082 soldada por FSW debido a que la cantidad de calor suministrado a la región de la soldadura fue mayor y por lo tanto el flujo de metal y la creación de la soldadura podría haber sido más eficaz. Esto podría explicar el comportamiento a fatiga relativamente alto de la soldadura FSW con un aporte térmico alto (velocidad avance baja y velocidad de rotación alta).
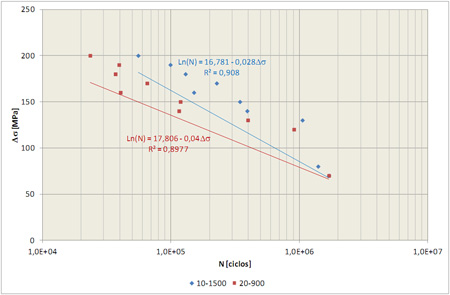
iv. Análisis fractográfico de los ensayos de fatiga
Las figura 7 muestra las fracturas obtenidas en el ensayo de fatiga para la condición con alto aporte térmico. Las imágenes se han ordenado de menor a mayor tensión aplicada. En las dos primeras se puede observar cómo la iniciación de grieta se da en una pequeña zona del borde y ésta va extendiéndose por toda la superficie, haciéndolo en mayor medida cuanto menor es la carga, hasta que se produce la rotura. En las dos últimas imágenes por el contrario se observa cómo se inician grietas alrededor de gran parte de la sección creciendo éstas muy poco antes de que se produzca la rotura. Se observa la presencia de un crecimiento de grieta estable y un crecimiento inestable final. Cuanto mayor sea la carga aplicada más violento es este crecimiento inestable.
Las fracturas de fatiga de las uniones FSW se produjeron entre la TMAZ y la ZN por el lado de retroceso. Para soldaduras FSW, la fractura durante la carga de fatiga se propaga en la raíz de las soldaduras debido a la baja entrada de calor o una orientación de la herramienta inadecuada y defectos del tipo ‘kissing bond’ en la raíz del lado de retroceso [32].
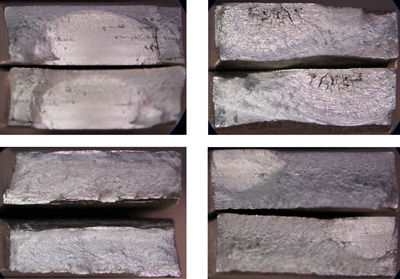
Figura 7. Macrografías de las roturas del ensayo de fatiga para la muestra 10-1500: a) ∆ợ =180 MPa, b) ∆ợ=170 MPa, c) ∆ợ =160 MPa, d) ∆ợ =150 Mpa.
Para la misma velocidad de avance a una mayor velocidad de rotación, la característica de fractura dúctil es más evidente [32].
Conclusiones
Las propiedades mecánicas de la aleación de aluminio AW6082-T6 soldada por FSW cambian con los parámetros de proceso. La resistencia a tracción es directamente proporcional a la relación de soldeo, es decir, con un bajo aporte térmico tenemos una mejor resistencia a tracción, sin embargo, para la resistencia a fatiga el alto aporte térmico presenta mejor comportamiento.
Esta mejora en la vida de fatiga de la FSW con alto aporte térmico puede estar asociada con la mayor cantidad de calor suministrado a la soldadura por unidad de longitud.
Agradecimientos
Los resultados presentados en este artículo hacen parte del desarrollo del proyecto IMDEEA/2011/168 (subvencionado por el Instituto de la Pequeña y Mediana Empresa, IMPIVA), dependiente a su vez de la Conselleria D’Empresa, Universitat I Ciencia de la Comunidad Valenciana), en colaboración con el Centro de Investigación en Tecnologías de Unión (LORTEK-ik4).
Referencias
[1] W.M. Thomas, E.D. Nicholas, J.D. Needham, M.G. Murch, P. Templesmith and C.J. Daws: Friction stir butt welding, International Patent Appl. N° 9125978.8, Diciembre 1991, U.S. Patent N° 5,460,317.
[2] R.S. Mishra, Z.Y. Ma. Friction Stir Welding and Processing. Materials Science and Engineering R: Reports, 50 (1-2), 2005, p. 1-78.
[3] R.S. Mishra, M.W. Mahoney. Introduction in Friction Stir Welding and Processing. (R.S. Mishra, M.W. Mahoney, Ed). ASM International, 2007, p. 1-5.
[4] K.V. Jata. Friction Stir Welding of High Strength Aluminum alloys, Materials Science Forum, 331(II), 2000, p 1701-1712.
[5] A.P. Reynolds, W.D. Lockwood, T.U. Seidel. Processing-Property Correlation in Friction Stir Welds. Materials Science Forum, 331(II), 2000, p 1719-1724.
[6] E. Aldanondo, A.A.M da Silva, P.Alvarez, A. Lizarralde, A. Echeverria. Dissimilar Friction Stir Welding of AA2024-T3 and AA7075-T6 Aluminium Alloys. Proceedings of Friction Stir Welding and Processing V – TMS2009 Annual Meeting, 15-19 Febrero 2009, San Francisco, EE UU.
[7] M. Cabibbo, H.J. McQueen, E. Evangelista, S. Spigarelli, M. Di Paola, A. Falchero. Microstructure and Mechanical Property Studies of AA6056 Friction Stir Welded Plates. Materials Science and Engineering A, 460-461, 2007, p. 86-94.
[8] A. Denquin, D. Alleaux, M.H. Campagnac, G. Lapasset, Microstructural and mechanical evolutions within friction stir welds of precipitation hardened aluminium alloys, Materials Science Forum, 426-432, 2003, p 2921-2926.
[9] Woong-Seong Chang, Yun-Mo Yeon, Joint properties and thermal behaviors of friction stir welded age hardenable 6061 Al alloy, Materials Science Forum, 426-432, 2003, p 2953-2958.
[10] C.D. Sorensen, T.W. Nelson. “Friction Stir Welding of Ferrous and Nickel Alloys”. In: Friction Stir Welding and Processing. (R.S. Mishra, M.W. Mahoney, Ed). ASM International, 2007, p. 111-121.
[11] T.J. Lienert. “Microstructure and Mechanical Properties of Friction Stir Welded Titanium Alloys”. In: Friction Stir Welding and Processing. (R.S. Mishra, M.W. Mahoney, Ed). ASM International, 2007, p. 123-154.
[12] T.R. McNelley, K. Oh-Ishi, A.P. Zhilyaev. “Microstructure and Properties of Copper Alloys after Friction Stir Welding/Processing”. In: Friction Stir Welding and Processing. (R.S. Mishra, M.W. Mahoney, Ed). ASM International, 2007, p. 155-173.
[13] R. Zettler, J.F. dos Santos, A. Blanco, A.A.M. da Silva. 7th International Conference on Trends in Welding Research, 16-20 Mayo 2005, Pine Mountain, EE.UU.
[14] R. Zettler, A.A.M. da Silva, S. Rodrigues, A. Blanco, J.F. dos Santos. “Dissimilar Al to Mg Alloy Friction Stir Welds”. Advanced Engineering Materials 8, 2006, p. 415-421.
[15] V. Firouzdor, S. Kou. Al-to-Mg Friction Stir Welding: Effect of Positions of Al and Mg with Respect to the Welding Tool. Supplement to the Welding Journal, 2009, 123-224.
[16] YAN Yong, ZHANG Da-tong, QIU Cheng, ZHANG Wen. Dissimilar friction stir welding between 5052 aluminum alloy and AZ31 magnesium alloy. Trans. Nonferrous Met. Soc. China, Vol. 20, 2010, 619-623
[17] A. von Strombeck, J.F. dos Santos, F. Torster, P. Laureano, M. Koc. Proceedings of the first international symposium on friction stir welding, thousand Oaks. 1999.
[18] R. S. Mishra, S. R. Sharma, N.A. Mara, M.W. Mahoney. Proceedings of the international conference on jointing of advanced and specialty materials III. ASM international, 2000, p. 157.
[19] K. Elangovan, V. Balasubramanian, S. Babu. Predicting tensile strength of friction stir welded AA6061 aluminium alloy joints by a mathematical model. Materials and Design 30 (2008). p. 188-193.
[20] M.N. James, P.J. Webster, D.J. Hughes, D.G. Hattingh, G. Bradley, G. Mills. “Residual Stress Field in Friction Stir Welded Marine Grade Aluminium Alloy”. Internal Report. Febrero 2002.
[21] S. Lockyer. Fracture and Fatigue Performance of Friction Stir Welds. Dissemination Report EUREKA project EUROSTIR.
[22] T. Ghidini, C. Dalle Donne. Fatigue crack propagation assessment based on residual stresses obtained through cut-compliance technique. Fatigue and Fracture of Engineering Materials and Structure 30(3), 2006, p. 214-222.
[23] ZHOU Car-zhi, YANG Xin-qi, LUAN Guo-hong. Comparative study on fatigue properties of friction stir and MIG-pulse welded joints in 5083 Al-Mg alloy. Trans Nonferrous Met. Soc. China, Vol. 15, Nº 4, 2005, 789-794.
[24] S. Rajakumar, C. Muralidharan, V. Balasubramanian. Establishing empirical relationships to predict grain size and tensile strength of friction stir welded AA6061-T6 aluminium alloy joints. Trans Nonferrous Met. Soc. China, Vol. 20, 2010, 1863-1872.
[25] J. Adamowski, M. Szkodo. Friction Stir Welds (FSW) of aluminium alloy AW6082-T6. Journal of Achievements in Materials and Manufacturing Engineering, Vol. 20, 2007, 403-406.
[26] J. Adamowski, C. Gambaro, E. Lertora, M. Ponte, M. Szkodo. Analysis of FSW welds made of aluminium alloy AW6082-T6. Journal of Achievements in Materials and Manufacturing Engineering, Vol. 28, 2007, 453-460.
[26] Peel, M.J., Steuwer, A., Withers, P.J. Dissimilar Friction Stir Welds in AA5083-AA6082. Part II: Process Parameter Effects on Microstructure. Met. and Mat. Trans. A, Vol 37, 2006, 2195-2206.
[27] K. Mroczka, A. Pietras. FSW characterization of 6082 aluminium alloys sheets. Archives of Materials Science and Engineering, Vol. 40, 2009, 104-109.
[28] D. Carron, P. Bastid, Y. Yin, R.G. Faulkner. Modelling of precipitation during friction stir welding of an Al-Mg-Si alloy. Technische Mechanik, Vol. 30, 2010, 29- 44.
[29] Svennson, L.E., Karlsson, L., Larsson, H., Karlsson B., Fazzini, M., Karlsson, J. Microstructure and mechanical properties of friction stir welded aluminium alloys with special reference to AA 5083 and AA 6082. Sci. Tech. Weld. Join, Vol. 5, 2000, 285-296.
[30] Cavaliere P., Panella F. Effect of Tool Position on the Fatigue Properties of Dissimilar 2024-7075 Sheets Joined by Friction Stir Welding. Journal of Materials Processing Technology, Vol. 206, 2008, 249 – 255.
[31] Ericsson M., Sandström R. Influence of Welding Speed on the Fatigue of Friction Stir Welds, and Comparison with MIG and TIG. International Journal of Fatigue, Vol. 25, 2003, 1379 – 1387.
[32] Hakan A., Ali B., M. Tahir Y., Kurtuluş Y. Influence of Welding Parameters on the Fatigue Behaviours of Friction Stir Welds of 3003-O Aluminum Alloys. Materials Science (Medžiagotyra), Vol. 16, No. 4, 2010, 311-319.