Una apuesta sólida por superar los microdefectos
James Thorpe, jefe global de productos de Sandvik Coromant
27/01/2021El mecanizado de agujeros es el más común de todos los procesos de mecanizado, pero también es al que menos atención se presta. Muchos talleres ven poco motivo en cambiar o actualizar su reglaje de mecanizado de agujeros existente y han estado usando las mismas herramientas y parámetros de corte durante años. Pero, con los impredecibles efectos de la COVID-19, esto está a punto de cambiar.
El reciente memorando COVID-19: Briefing note de McKinsey & Company denomina la actual situación de la industria como la “siguiente normalidad”, donde los fabricantes deben estar preparados para cambios impredecibles y duraderos en los mercados de clientes. El informe aconseja que “los fabricantes muestren resiliencia si quieren navegar una vía social y económicamente viable”.
La mayoría de fabricantes, por ejemplo, están explorando nuevas bases de vendedores y productos. Los talleres que antes se especializaban en áreas específicas ahora están adaptando sus tornos y fresadoras para acomodar una mayor variedad de materiales tenaces y exigentes. A la vez, los fabricantes deben examinar nuevas formas de incrementar sus beneficios y reducir los tiempos de ciclo, sin sacrificar la calidad del producto.
En otras palabras, ha llegado la hora de que los fabricantes se replanteen sus procesos de mecanizado de agujeros.
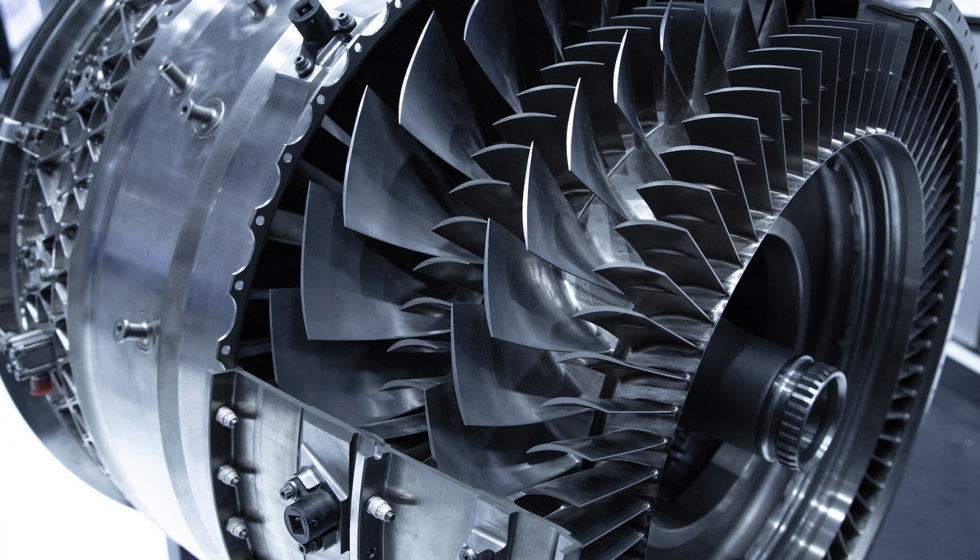
La integridad superficial del agujero es una auténtica preocupación de los fabricantes aeroespaciales o de ingeniería general diversificándose a la industria de la automoción.
La materia blanca
La integridad superficial del agujero es una auténtica preocupación para los fabricantes aeroespaciales o las empresas de ingeniería general que quieren diversificarse y entrar en la industria aeroespacial. Mejorar la calidad del agujero es de vital importancia para evitar el fallo de la pieza y viene, en gran medida, definido por el proceso de fabricación utilizado para mecanizar o acabar los agujeros.
Las soluciones de herramientas y las geometrías del filo de las brocas evolucionan continuamente para satisfacer los más altos estándares de fabricación y calidad de la pieza. El uso de refrigerante también mejora para reducir la acumulación de calor en la herramienta. Y las pruebas llevadas a cabo han demostrado que cada uno de estos factores puede ayudar a controlar el conocido efecto de “capa blanca” en los materiales de trabajo.
El término capa blanca fue acuñado por un líder mundial de la industria de la manufactura aeroespacial que además es cliente de Sandvik Coromant. Este hace referencia a una estructura delgada de grano ultra fino que se observa tras taladrar el componente y que es provocado por el calor de la broca. La capa blanca no solo puede cambiar las propiedades de la superficie del material, sino que es considerada inaceptable en los procesos de gestión de calidad del cliente.
El fabricante aplica estrictos procesos de acabado del agujero a los agujeros taladrado en los componentes aeroespaciales, entre los que se incluyen discos de turbina, compresores, tambores y ejes. Ese es el motivo por el que decidió colaborar con Sandvik Coromant para investigar por qué se formaba la capa blanca y cómo podía controlarse.
Es importante recordar que estas pruebas no solo se realizaron para gestionar la calidad del componente. Entre sus altos cargos, el objetivo era reducir su tiempo operativo total e incrementar los beneficios, eliminando todo un proceso secundario de mecanizado.
Segundo acto
El proceso secundario se produce tras haber creado el agujero con una broca de metal duro, y puede implicar escariado, ranurado o fresado en plunge para acabar el componente. La fase secundaria se produce principalmente para satisfacer los requisitos de calidad superficial —reduciendo problemas como la capa blanca— más que la precisión dimensional, a excepción del mecanizado de agujeros de tolerancia estrecha.
Desde una perspectiva de costes general, el proceso secundario es incluso más caro que mantener datos de corte bajos, que es la otra forma de conservar la integridad superficial. Ese es el motivo por el que el cliente de Sandvik Coromant se planteaba eliminar el proceso completo. Un proveedor con un producto capaz de producir un agujero de conformación al tamaño deseado, sin procesos secundarios, ocupa una posición comercial muy favorable para reducir radicalmente su coste por pieza.
La investigación sobre las causas, y posibles prevenciones, de la capa blanca se realizó en cuatro pruebas de taladrado de Inconel 718 níquel-cromo de gran resistencia, un material popular en la industria aeroespacial. Era la primera vez que el cliente llevaba a cabo una investigación de este tipo.
Las pruebas estudiaron el taladrado con dos brocas de metal duro enterizas de Sandvik Coromant, CoroDrill R840 y CoroDrill R846. Cada una se aplicó con dos conjuntos de parámetros de corte diferentes: 58 mm/min y 98 mm/min, respectivamente, y la velocidad de husillo de 829 ver/min y 757 ver/min, respectivamente. Los datos de la fuerza de corte y el par se midieron en varios tests, al igual que el grosor de la capa blanca.
Desde que se llevaron a cabo estas pruebas, R840 ha sido sustituida por la broca CoroDrill 860 con la geometría -GM y R846 por la broca CoroDrill 860 con la geometría -SM. Cada una de estas herramientas de siguiente generación ha sido diseñada para ampliar más si cabe la duración de la herramienta, sin comprometer la calidad del agujero.
Los resultados ofrecieron una visión detallada sobre qué determina el grosor de la capa blanca. Lo más llamativo fue que R846 generó menos capa blanca debido a la preparación de sus filos radiales y curvados. Mientras que los filos rectos y con chaflán de R840 se cree que están relacionados con el incremento de la fuerza de corte, par y grosor de la capa blanca. De ahí la conclusión de que el diseño de la broca determina la posibilidad de alcanzar una gran calidad del agujero sin sacrificar los datos de corte.
Las pruebas del fabricante aeroespacial con Sandvik Coromant no solo revelaron unos cuantos secretos sobre la capa blanca sino que la empresa también logró eliminar algunos procesos secundarios como el escariado y el fresado en plunge, lo que les ha permitido ganar tiempo y reducir costes. Es más, los resultados han validado el diseño de la gama de brocas de metal duro CoroDrill 860 de Sandvik Coromant.
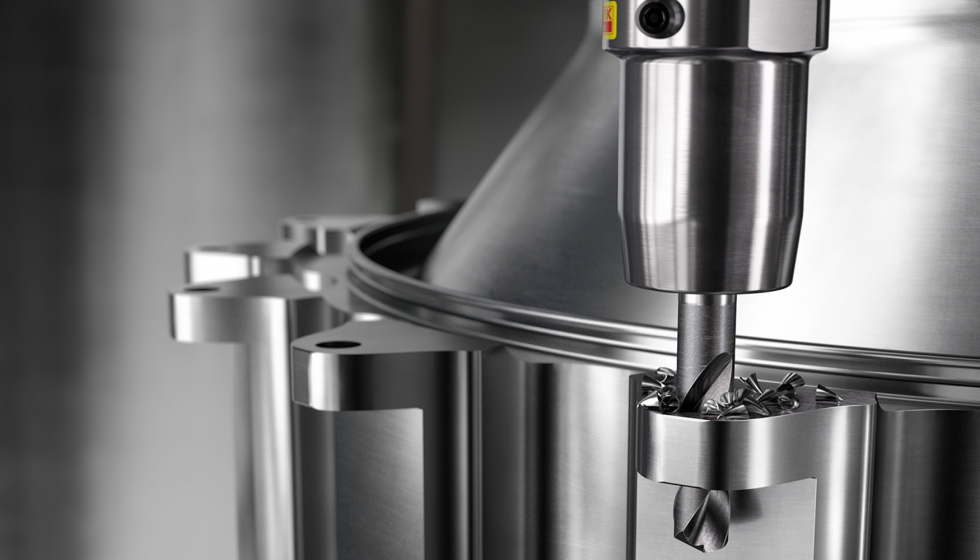
Con CoroDrill 860 con la geometría -SM, la mayor duración de la herramienta y la mayor calidad del agujero depende del diseño de la broca. www.sandvik.coromant.com/es
Diseño optimizado
La gama incluye la citada CoroDrill 860 con la geometría -GM (CD860-GM), diseñada como geometría universal para taladrado de materiales ISO P, M, K y H exigentes en todos los sectores industriales. También está la broca CoroDrill 860 con la geometría -SM (CD860-SM), para mecanizado de calidades ISO-S como superaleaciones termorresistentes (HRSA, por sus siglas en inglés), titanio e Inconel. Esta última ha demostrado ser especialmente popular en la industria aeroespacial.
Al crear CD860-GM y CD860-SM, los ingenieros de Sandvik Coromant pusieron en práctica su convicción de que una herramienta más duradera y una calidad del agujero optimizada dependen del diseño de la broca. CD860-GM presenta un diseño de canal pulido innovador que mejora la evacuación de la viruta y ofrece mayor resistencia del núcleo y fuerzas de corte reducidas al taladrar.
La broca CD860-SM, a su vez, tiene una nueva calidad y una geometría de punto optimizada y perfeccionada, que mejora más si cabe la duración de la herramienta al trabajar con materiales de superaleaciones termorresistentes difíciles de mecanizar. El resultado son agujeros de mayor calidad.
CoroDrill 860 ya ha sido probada en pruebas preventa en una serie de sectores. Una empresa de ingeniería mecánica francesa puso a prueba CD860-GM en acero para estructuras AISI 4140. Logró un mecanizado de agujeros de alta calidad con la entrada cóncava y convexa de la broca, con buena rectitud y tolerancia. Desde entonces, la empresa ha establecido una nueva relación comercial con Sandvik Coromant.
Otro cliente de Sandvik Coromant, un fabricante de ingeniería general italiano, logró un incremento superior al 45% de la productividad al usar CD860-GM en una robusta aleación de acero 34CrNiMo6 frente al uso de la broca de la competencia. También consiguió una duración de la herramienta un 100% superior. Además, la broca CD860-SM ha ofrecido unos resultados impresionantes al mecanizar Inconel 718. En particular, las pruebas llevadas a cabo en Katowice, Polonia, logró conseguir una vida útil un 180% superior con CD860-SM frente al uso de CoroDrill R840.
Sea cual sea el sector —aeroespacial, ingeniería general u otras áreas—, si la broca ha sido diseñada específicamente para ese fin, el alto rendimiento está garantizado. Además, otras herramientas online como CoroPlus Tool Guide de Sandvik Coromant puede ofrecer soporte complementario. Al acceder a la herramienta a través del navegador web e introducir el material de la pieza, diámetro y profundidad del agujero, los usuarios pueden encontrar la mejor herramienta rotativa enteriza y los datos de corte para sus requisitos.
Aunque aún no podemos hacer realidad el dicho ‘medir dos veces, cortar una’, el rendimiento de CD860-GM y CD860-SM ayuda a los fabricantes a replantearse sus métodos de mecanizado de agujeros.