¿Cómo puede mejorar la calidad de la producción un sistema de fabricación basado en la nube?
Durante muchos años, a pesar de la desaceleración económica y el cambio continuo de los entornos de trabajo, el sector manufacturero ha sido el principal creador de puestos de empleo y ha generado unos ingresos sustanciales en todo el mundo. Sin embargo, aunque durante los pasados años se ha logrado avanzar mucho para garantizar la calidad de los componentes y mejorar la eficiencia de todo el proceso de producción en conjunto, todavía quedan fuentes de improductividad importantes que no se han abordado de manera efectiva. El resultado final es que los niveles de gastos operativos en el sector de la fabricación continúan siendo demasiado elevados, pero Sandvik Coromant cree que existen oportunidades reales de dar un giro a esta situación mediante soluciones digitales basadas en la nube.
Es indiscutible que la información, los conocimientos y los datos desempeñan un papel fundamental en el proceso de planificación y de evaluación de la calidad. Si se logra gestionar dichos elementos de forma más precisa y exhaustiva a la vez que se amplía el acceso a los mismos (y se consigue controlarlos de forma remota), será posible optimizar el proceso de fabricación hasta el punto de poder reducir los costes de manera significativa. Al mismo tiempo, al poder analizar grandes volúmenes de diferentes clases de información a gran velocidad y recibir información exacta sobre las características del proceso de mecanizado, los fabricantes estarán en disposición de mejorar la precisión y calidad de todas las piezas que produzcan. Además, los errores y procesos fallidos se eliminarán en futuras implementaciones, lo que significa que una vez que se hayan subsanado los factores problemáticos del proceso de fabricación, estos jamás se repetirán. De hecho, el objetivo último es construir sistemas que puedan optimizarse por sí mismos con el mínimo nivel de programación o sin necesidad de reprogramar o de intervención del operario.
Una de las principales fuentes de pérdidas en la actual industria manufacturera que trabaja principalmente con componentes metálicos es la mala calidad de los datos de entrada, que impide la optimización del proceso de producción. Esto implica que las máquinas individuales pueden llegar a presentar niveles de uso por debajo del 50 % y que tan solo se aproveche el 33% de la energía que fluye a través de las máquinas-herramienta de la fábrica para la producción de las piezas. Por último, solo se guarda una pequeña parte de los datos de proceso disponibles; y la cantidad que se analiza y utiliza para realizar predicciones e introducir mejoras es incluso menor.
No hay duda de que la planificación actual del proceso presenta varios problemas relacionados con los datos. Entre ellos se encuentran el suministro discontinuo de los datos del proceso, que subraya una necesidad evidente de contar con un sistema de transferencia de datos semiautomático. Además, existe una falta diferenciada de ciclos de realimentación sobre la planificación del proceso, lo cual tiene un impacto directo sobre la calidad y la eficiencia de todo el proceso de fabricación en su conjunto. Resulta igualmente obvio que garantizar la calidad de los datos, de la información y de los conocimientos es un enorme reto, ya que la preocupante carencia de transferencia de conocimiento basada en el modelo dificulta el acceso en el momento oportuno. De hecho, la compartición del conocimiento por sí misma es especialmente deficiente, al igual que el nivel de colaboración entre los equipos implicados en el proceso de fabricación, independientemente de dónde se encuentren.
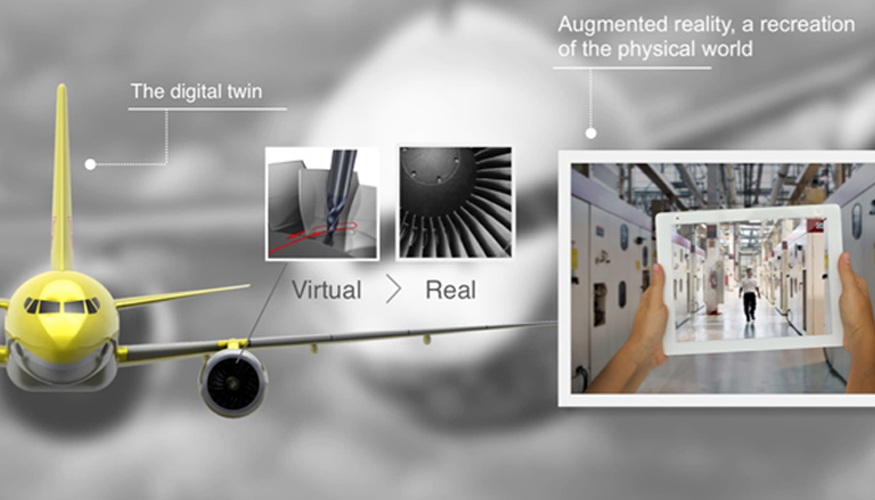
Reconfigurar la cadena de valor para que el grado bajo de aprovechamiento de la máquina sea cosa del pasado es una de las funciones principales de un enfoque centrado en la red respaldado por una solución TIC basada en la nube.
Paso de la TI a la ITC
Si la gestión de los datos, del conocimiento y de la información es la respuesta para minimizar la ineficiencia y maximizar la productividad durante el proceso de fabricación, es indudable que la tecnología de la información (TI) ya no es suficiente y que debe haber una tendencia deliberada hacia el uso de tecnologías que permitan esta gestión, como la tecnología de la información y la comunicación (TIC) en combinación con un sistema de gestión de datos basado en la nube. Este nivel de transformación digital —que realmente cumple la perspectiva de la compilación y compartición inteligente de los datos— permitirá hacer realidad un proceso de producción ‘más inteligente’. Reconfigurar la cadena de valor en este sentido para que el grado bajo de aprovechamiento de la máquina sea cosa del pasado es una de las funciones principales de un enfoque centrado en la red respaldado por una solución TIC basada en la nube.
Para que la fábrica inteligente pueda ser realmente operativa es esencial que no se ponga en riesgo en modo alguno la disponibilidad de los recursos. Para ello, los actuales sistemas de planificación de recursos corporativos (ERP), sistemas de gestión del ciclo de vida del producto (PLM), sistemas de ejecución de la producción y otros tipos de sistemas operativos corporativos deben estar totalmente integrados con todas las máquinas y todos los trabajadores de la empresa (y externos, en caso necesario). Este grado de integración total no se aproxima en la actualidad hasta el punto necesario, pero si los datos se gestionaran con un sistema basado en la nube sería posible crear verdaderas soluciones integrales que garanticen la precisión, consistencia y conectividad entre humanos, humanos y máquinas y entre diferentes máquinas. En definitiva, las soluciones de conectividad digital permitirán a las empresas mejorar todos los aspectos del proceso de producción integral.
Interfaces de programación de aplicaciones abiertas y sensores integrados
Al igual que la nube es esencial para lograr una fábrica inteligente, existen otros dos elementos clave para conseguir un control óptimo de la calidad y la retroalimentación del proceso. Se trata de las interfaces de programación de aplicaciones (API) abiertas, que permiten que diferentes máquinas y sistemas puedan comunicarse e interactuar constantemente entre sí, y de sensores sofisticados y otras unidades de compilación de datos que deben integrarse en todas las etapas funcionales del proceso de producción por las que deba pasar un componente. Solo si contamos con estas herramientas esenciales en el lugar apropiado es posible que un entorno de fabricación basado en la nube garantice realmente el seguimiento y la gestión de los recursos, además de la capacidad de todos los implicados en el proceso de producción de acceder a los datos y analizarlos para facilitar la supervisión del rendimiento y el diagnóstico en pro de la mejora continua de la calidad de todos los productos fabricados en la planta.
Este ciclo continuo de los datos del proceso de fabricación abarca el diseño asistido por ordenador, la planificación del proceso y la fabricación asistida por ordenador en la fase de mecanizado previo, así como la monitorización del proceso durante el mecanizado y la evaluación de la calidad en la fase posterior al mecanizado. Al integrar los datos de las fases de mecanizado previo, mecanizado y postmecanizado, determinados por la retroalimentación y el control del proceso, obtenemos como resultado un grado máximo de optimización general y en todas las etapas de la producción. La retroalimentación y el análisis continuos del proceso conduce al aprendizaje, y el aprendizaje conduce a una mejor eficiencia y, en última instancia, a la reducción de costes.
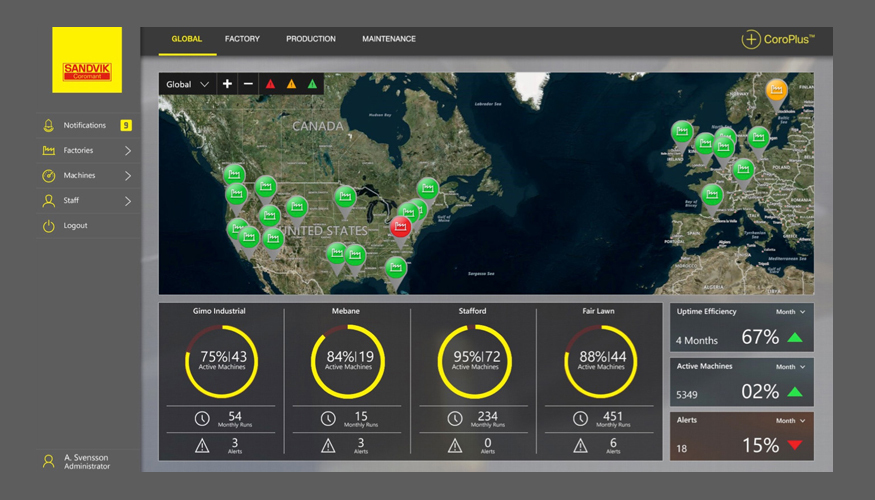
Tecnología integrada de la información y la comunicación
Únicamente la integración de tecnología de la información y la comunicación global permitirá a los fabricantes lograr una cadena de valor interconectada y colaborativa en todos los pasos del proceso. En términos de logística de los recursos/materiales/productos, los factores específicos que conducen a este objetivo se reducen al seguimiento, la gestión y el control autónomo. Por tanto, los futuros ajustes en la producción tendrán que proporcionar soluciones de producto y procesos personalizados que sean al menos igualmente eficientes con independencia de las variaciones de material y de las adaptaciones del centro de mecanizado necesarias.
Otros factores que influirán en el futuro en la adopción de entornos de fabricación integrados basados en la nube serán el moldeado virtual, el diagnóstico predictivo, el control de calidad autónomo, la realimentación y el ajuste, el diagnóstico y soporte remotos, además de un aprendizaje efectivo del proceso.
Las ventajas de este enfoque de integración total en la fabricación y las posibilidades de mejora de la calidad del proceso que pueden introducir los sistemas de producción basados en la nube están muy bien documentadas en cuanto al efecto general, pero Sandvik Coromant también se preocupa en cómo podrían determinados factores individuales mejorar el rendimiento en ciertas fases del proceso de fabricación en su conjunto.
Al igual que es posible recopilar y compartir los denominados «macrodatos» de múltiples líneas de producción o incluso de varios emplazamientos de producción, resulta igualmente importante la capacidad de examinar a fondo y tener acceso a información precisa al instante acerca de cuestiones más locales, como la eficiencia de una sola máquina o el desgaste de una determinada herramienta. Por ejemplo, Sandvik Coromant ha identificado un método novedoso que combina diferentes fuentes de datos y la monitorización durante el proceso para realizar un análisis completo e introducir mejoras y optimizaciones de forma continua. De este modo se evitarán las fuerzas de corte excesivas en la herramienta, los fallos del rodamiento del husillo debido a la sobrecarga, la rotura de la herramienta, los errores de control de las dimensiones y de la forma de la pieza debido a la flexión estática de la herramienta, se prolongará la vida útil de la herramienta y se obtendrá un acabado superficial uniforme, además de engrosar continuamente los conocimientos necesarios para continuar optimizando los procesos.
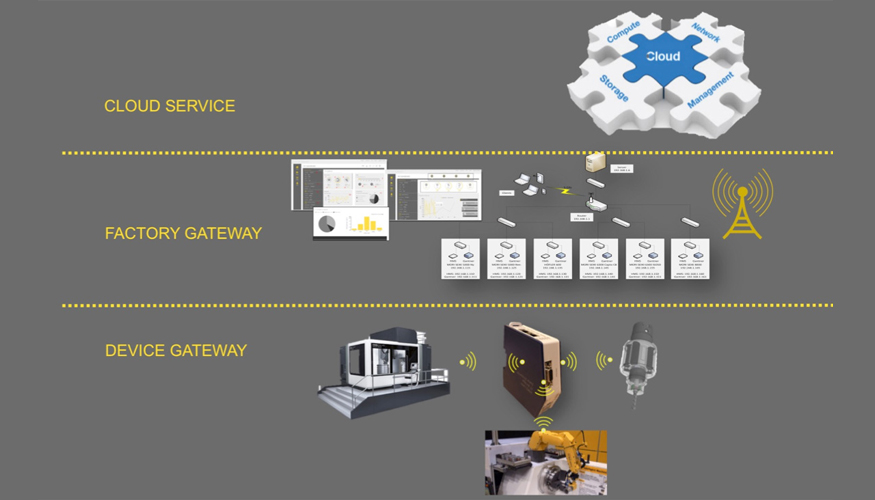
Internet de las cosas industrial
El término que describe lo que Sandvik Coromant considera la panacea de las soluciones basadas en la nube para resolver los problemas actuales en la fabricación descritos anteriormente sería un ‘internet de las cosas industrial’ o IIoT (por sus siglas en inglés). Esto consta básicamente de tres áreas clave que serán esenciales en cualquier fábrica inteligente del futuro donde todo esté integrado: computación en dispositivos, computación en la fábrica y computación en la nube.
Si se analizan individualmente, la computación en dispositivos abarca el procesamiento digital de señales, las interfaces de comunicación, la conectividad en la zona de producción, las interconexiones de red locales, la actualización y configuración remotas, el análisis de los datos activos y la conexión con herramientas o máquinas. En la misma línea, la computación en la fábrica se encarga también del procesamiento digital de señales y la actualización y configuración remotas, pero incorpora asimismo el análisis de datos semiactivos y la conexión con la nube. Por su parte, la computación en la nube cubre la integración nube a nube, la monitorización de la zona de producción, la conectividad en la nube, la seguridad, el análisis y los procesos de mecanizado previo, de mecanizado y de posmecanizado.
Conclusión
En el camino hacia la fabricación basada en la nube y la adopción de la innegablemente eficiente disciplina de la monitorización digital del proceso nos enfrentamos a retos inevitables e identificables, pero la industria manufacturera de todo el mundo está evolucionando en torno a este enfoque y, sin duda alguna, están avanzando en la dirección correcta.
Como resultado final de la gestión de la información, del conocimiento y de los datos de manera más efectiva durante la planificación del proyecto, durante el mecanizado y a la hora de evaluar la calidad obtendremos un proceso de fabricación optimizado hasta el punto en que los gastos de la empresa se reducirán en lugar de aumentar. Por tanto, los clientes se beneficiarán de unos componentes y productos fabricados con el máximo grado de precisión y de eficiencia, y esta garantía está adquiriendo cada vez más valor en muchos sectores industriales, como el extremadamente exigente sector aeroespacial, donde la calidad, la fiabilidad, la trazabilidad y la velocidad de los productos entregados son requisitos innegociables.
La digitalización mediante el IIoT permitirá conectar los procesos de mecanizado virtuales y en tiempo real de un modo nunca antes experimentado, hasta el punto en que los límites entre ambos procesos desaparecerán.