Verificación de las prestaciones de una máquina de medición por coordenadas
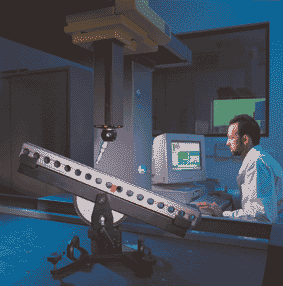
En los últimos años la ISO 10360 ha sido el estándar más importante, con una mayor difusión. La Organización Internacional para la Estandarización (ISO) es una federación mundial de organismos de estandarización nacionales. Los Estándares Internacionales los redactan comités técnicos.
La ISO 10360 regula las pruebas de aceptación y la verificación de las prestaciones de las máquinas de medición por coordenadas, conocidas como MMC.
El conjunto de las normas ISO 10360 define los criterios de aceptación y de reverificación de las máquinas de medición y las adoptan las autoridades nacionales europeas de estandarización.
Consta de varias partes, cada una se encarga de tests y pruebas específicos:
- Parte 1: Vocabulario
- Parte 2: MMC para medir dimensiones lineares
- Parte 3: MMC con cuatro ejes y mesa giratoria
- Parte 4: MMC con funciones de medición por digitalización
- Parte 5: MMC con sistemas de toma de datos con múltiples puntas
Las pruebas de certificación y aceptación según la ISO 10360-2
MPEE y MPEP
El Error Máximo Permitido (MPE) debe estar especificado por el fabricante y define los errores máximos E y P del sistema de medición.
E = error de indicación de la medición longitudinal
P = error de toma de punto
Estos dos parámetros permiten establecer las prestaciones de la máquina de medición relativas a la longitud medida (MPEE) y a la toma de un punto (MPEP).
Los dos parámetros pueden estar declarados por el fabricante para el volumen de medición completo o para un volumen reducido del cual se han especificado los límites.
Error de indicación de la longitud medida MPEE
MPEE = +/-(A+L/K)
Donde:
A= inexactitud constante de la máquina o del sistema expresada en micras
L= longitud expresada en milímetros
K= constante positiva
La prueba se debe realizar con 5 componentes certificados (bloques patrones o pies de rey) de diversas longitudes, orientándolos en 7 direcciones distintas en el volumen de medición, medir cada uno 3 veces para obtener un total de 105 mediciones (Fig.1).
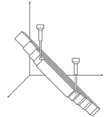
Error de toma de punto MPEP
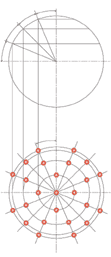
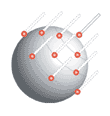
Verificación de las prestaciones de digitalización
Las prestaciones de digitalización está determinada por los parámetros Ti,j y t:
T= error de digitalización
i= intensidad de los puntos, alta (H), baja (L)
j= trayecto predefinido (P), no predefinido (N)
t= tiempo empleado para la prueba en segundos
El fabricante de MMC puede especificar el Error Máximo Permitido para las prestaciones de digitalización según las siguientes combinaciones:
MPETHP, MPETLP, MPETHN, MPETLN
Densidad de puntos | Trayecto predefinido | Trayecto no predefinido |
Alta | THP | THN |
Baja | TLP | TLN |
La digitalización con alta densidad de puntos es particularmente significativa en las digitalizaciones para definir el error de la forma, por ejemplo en el caso de las redondeces.
El error de digitalización se verifica digitalizando una bola de calibración por cuatro secciones definidas en el tiempo establecido por el fabricante. Los resultados de la digitalización definen el centro y el radio de la bola. El error Ti,j se calcula como la banda de dispersión del radio de la bola definido por todos los puntos de digitalización.
a es el ángulo que define la inclinación del palpador respecto al eje Z de la máquina de medición. Se aconseja coger un ángulo de 45º.
Las prestaciones de digitalización de la MMC se aceptan si:
- el error Ti,j no es superior al MPETi,j especificado por el fabricante
- la diferencia entre los radios calculados y la mitad del diámetro certificado de la bola no es mayor al MPETi,j
- el tiempo total empleado para la prueba no es superior a t como se especifica (Fig.4).
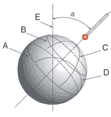
Verificación de las prestaciones de una MMC según la ISO 10360-5
En el caso de un cabezal fijo con múltiples puntas los parámetros son:
MPEMF, MPEMS, MPEML
Donde:
MF = error de forma (esfericidad)
MS = error de dimensión (diámetro)
ML = error de posición (X Y Z del centro)
El procedimiento de verificación consiste en medir la bola de calibración con las 5 puntas que forman el cabezal (que han de tener la misma longitud) tomando 5 puntos cada una. El cálculo de los tres errores MF, MS y ML tiene que utilizar los 125 puntos medidos (Fig. 5).
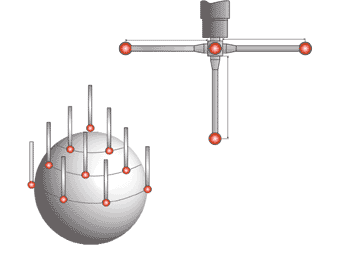
MPEAF, MPEAS, MPEAL
Donde:
AF = error de forma (esfericidad)
AS = error de dimensión (diámetro)
AL = error de posición (X Y Z del centro)
El procedimiento de verificación consiste en medir la bola de calibración en 5 posiciones del cabezal (perpendiculares entre ellas) tomando 5 puntos de cada una. El cálculo de los tres errores AF, AS y AL tiene que utilizar los 125 puntos medidos (Fig. 6-7-8).
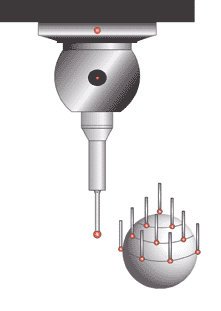
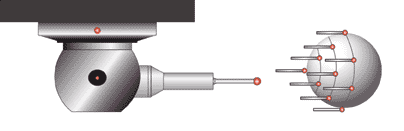
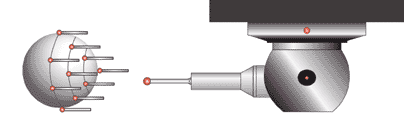