Bomag presume de maquinaria en sus Innovation Days
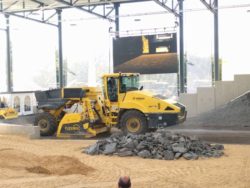
Bomag ha celebrado la edición 2017 de sus Innovation Days en las instalaciones que la firma especializada en maquinaria para el asfalto posee en Alemania, evento que se encuadra además en los actos de celebración del 60 aniversario de la compañía. Durante toda una semana y a razón de 400 invitados diarios entre clientes, distribuidores y periodistas de todo el mundo, la firma hizo una demostración de portfolio y tecnología y nos abrió las puertas de su sede central en la localidad germana de Boppard.
Ralf Junker, presidente de Bomag desde el pasado mes de mayo, fue el encargado de dar la bienvenida a los asistentes, en una intervención en la que relató brevemente su andadura en la compañía desde su incorporación en 1988 hasta la posición que ocupa en la actualidad. Apuntó, además, que “mi lema no es Estados Unidos primero, ni Alemania primero. Tampoco Bomag. Mi lema es que los clientes siempre son lo primero”.
A continuación dio paso a Jean-Claude Fayat, presidente de grupo Fayat, que destacó que a pesar de la longevidad de los 60 años que cumple la firma, “las personas son las que hacen las compañías jóvenes y dinámicas”.
Para el presidente del Grupo Fayat, “60 años de experiencia son una señal de nuestra capacidad de recuperación y de adaptación a los cambios de este mundo tan rápido”. Entre las claves señaladas por el máximo accionista del grupo “mantener la filosofía familiar en el grupo ha favorecido a la empresa. Hemos creado lazos y mantenemos la cercanía con el cliente”.
A continuación Jonathan Stringham, vicepresidente de Marketing de Bomag realizó en repaso por la historia de Bomag, deteniéndose en varios de los hitos de la compañía y haciendo hincapié en sus valores, que resumió en innovación, rentabilidad y facilidad de uso.
El gran reto del aeropuerto de Estambul
La construcción del nuevo aeropuerto de Estambul ocupó la parte central de las intervenciones de este tramo de los Innovation Days. Rukiye Demiral, responsable de İGA, empresa constructora del aeropuerto, explicó varias de las características de la construcción de esta gran obra en la que el uso de maquinaria Bomag para las labores de asfaltado y su tecnología están teniendo un protagonismo especial.
Las cifras de la construcción dejan claro que estamos ante una obra de gran envergadura. Proyectado como el mayor aeropuerto del mundo, su construcción supondrá una inversión de más de 10.000 millones de euros y empleará a unas 100.000 personas. Las empresas también asumirán la gestión del aeropuerto durante 25 años a partir de este año, para lo cual pagarán al Estado turco más de 22.000 millones de euros.
La terminal albergará 6 pistas de aterrizaje, 1,37 millones de metros cuadrados de área total en las terminales y 271 áreas de aparcamiento para las aeronaves. Se espera que por el aeropuerto de Estambul transiten entre 90 y 150 millones de pasajeros al año, ampliables a 200 millones.
Los trabajos de construcción suponen un desafío de ingeniería y logístico como en pocas ocasiones en la historia de la aviación. En la primera fase de construcción se mueve una media de un millón de metros cúbicos de tierra cada día, para lo cual la maquinaria desplegada sobre el terreno incluye 2.200 camiones, 255 excavadoras, 158 rodillos compactadores, 65 motoniveladoras, 116 dozers y 95 grúas torre.
En lo que se refiere al asfaltado de las pistas, diariamente se llevan a cabo entre 500.000 y 750.000 metros cúbicos de colocación de relleno y compactación. Asimismo, entre 1,7 y 2,5 millones de metros cuadrados de superficie de capa son realizados para ser probado por controles de calidad.
Para su ejecución iGA ha implementado un sistema de control de compactación continua integrado en los rodillos. Esta operación se realiza con 40 rodillos de tambor equipados con sistemas de medición de compactación y GPS. Con este modo de trabajo, cada rodillo tiene una capacidad de compactación mediante este sistema de entre 95.000 y 110.000 metros cuadrados cada día.
Exhibición de maquinaria
Tras la sesión de ponencias, fue el turno de ver las máquinas de Bomag en acción. Así, durante tres horas, todo el portfolio de la sexagenaria compañía desfiló ante los asistentes, realizando demostraciones tanto de su capacidad de producción (en apenas tres horas se llevó a cabo la construcción de un tramo de asfalto) como las innovaciones tecnológicas que incorporan sus equipos.
Dos ejemplos dan buena muestra de la innovación constante de que hace gala la compañía alemana. Así, pudimos comprobar cómo funciona un proyecto piloto de asistencia que se está llevando a cabo en Sudamérica, mediante el uso de unas Google Glasses, que permiten escanear a distancia la máquina, y el envío de las piezas de reparación mediante un drone. Por otro lado, la facilidad de mantenimiento quedó patente con el cambio in situ del tambor de una fresadora en 10 minutos.
Visita a las instalaciones
La tercera pata de estos Bomag Innovation Days estuvo en la visita a las instalaciones de Boppard. 2.500 personas trabajan en todo el centro, con unos 1.500 empleados directos en fábrica. Las instalaciones en la localidad germana incluyen la planta del montaje de fresadoras, el centro de formación, el centro de servicios, el sector de montaje de máquinas ligeras, el centro de logística, la planta de fabricación de tambores, las instalaciones de fabricación de rodillos y la sala de control de calidad.
Los responsables de Bomag que guiaron la visita explicaron que en la planta se montan tres tipos de fresadora, con tiempos de producción que oscilan entre las 130 horas (BM500/600), 300 horas (BM1000/1300) y 500 horas (BM2000/2200).
En el centro de formación es donde mejor queda reflejado el origen alemán de la compañía, incorporando la educación dual a sus procesos. Así, los jóvenes estudiantes tienen un tiempo de formación teórica y práctica de entre 3 y 4 años en los que van rotando por todos los departamentos de la compañía. Bajo este sistema, Bomag forma entre 20 y 25 alumnos por año.
En cuanto al centro de logística, sus 5.400 metros cuadrados de superficie albergan 44.000 partes de maquinaria distintas, con total de 2,3 millones de componentes. Con este enorme stock, dan salida a 500 pedidos diarios a unas 2.000 localizaciones diferentes. Los procesos están automatizados, de modo que los robots localizan los componentes en filas de palés de hasta 30 metros de altura y los depositan para su posterior distribución.
Como no podía ser de otro modo, todos los procesos de producción pasan por un control de calidad que garantiza el perfecto montaje de las máquinas. Este control está compuesto de 14 estaciones de test y en él trabajan más de 60 testadores, que controlan más de 100 parámetros distintos en cada máquina. Desde aquí, las máquinas ya están listas para su envío.
Pincha sobre las imágenes para verlas a tamaño completo