‘Ilia’, un nuevo centro de formación superior deportiva con soluciones estandarizadas
Para el proyecto de final de grado, se nos planteó a los estudiantes de 5º de Arquitectura de la Universitat Internacional de Catalunya – UIC Barcelona el reto de crear propuestas en el límite entre Barcelona y Badalona: en la zona del río Besós. Esta es una zona de gran desconexión dada la historia de la zona, que con el tiempo ha ido generando distintos barrios y espacios que, aunque han llegado a conectar físicamente, no lo han hecho demográficamente. Esto ha provocado que esta zona se convierta en un espacio residual, aun teniendo un gran potencial.
La zona actualmente está ocupada por la Ciutat Esportiva Dani Jarque del RCD Espanyol, que será desmantelada bajo la condición de mantener parte del uso en deportivo. Por esta razón, mi propuesta es crear un centro de formación profesional deportiva y una remodelación urbana de la zona con carácter deportivo.
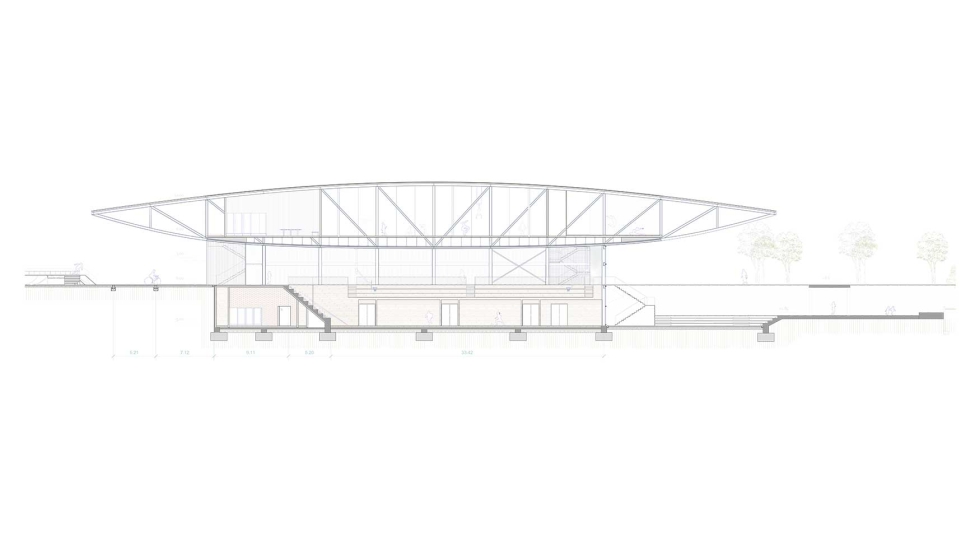
Remodelación urbana en la Ciutat Esportiva Dani Jarque
El espacio se diseña a partir de los ejes establecidos por la preexistencia: los campos de futbol. El terreno no se desmantelará de una vez, la propuesta es generar un programa de desmantelación progresiva de los campos deportivos en que se puedan reacondicionar pequeños espacios por etapas, de manera que la intervención no sea tan agresiva para los usuarios y habitantes de la zona, y el espacio se pueda ir ‘acondicionando’ a las necesidades y respuestas de los usuarios.
Los ejes de las distintas partes de los campos generan unos boulevard que comunican toda la zona y generan subespacios con equipamientos variados que mezclan las áreas de plaza, parque y deporte.
La franja de actuación principal de mi proyecto trabaja con el edificio y la topografía. El edificio se hunde y genera un acceso principal para el espectador a cota de calle y un nuevo espacio a -5 m, que va recuperando altura a través de una serie de plataformas y espacios, llegando hasta la topografía que conecta con la ronda.
El terreno es mayoritariamente plano, con variaciones de un máximo de 10 cm de un punto a otro. Esto permite que en la propuesta se puedan situar pistas y juegos a nivel llano, sólo con pendiente para la evacuación de aguas.
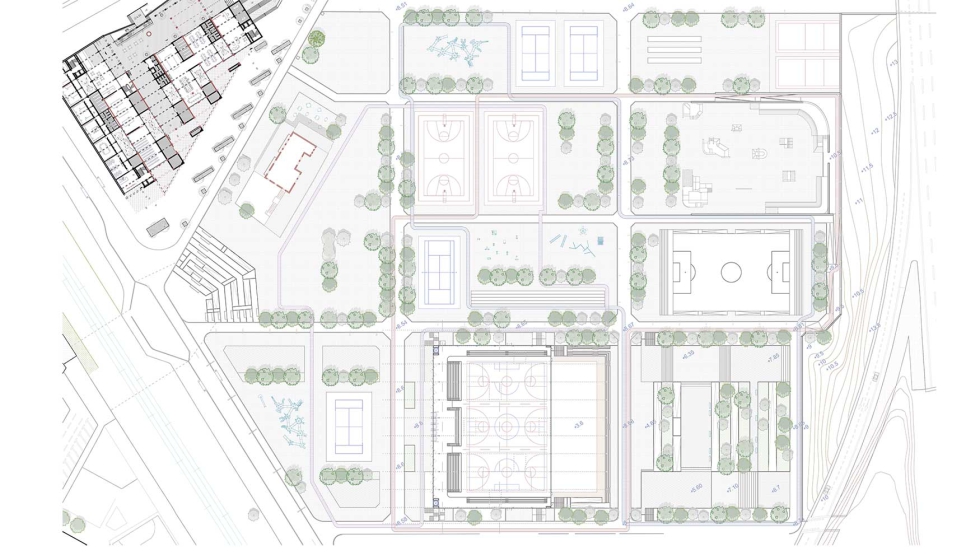
La razón de hundir el edificio surge del entorno principalmente. El pabellón y la estructura requieren de unas alturas mínimas para cumplir con el reglamento de espacios deportivos y tener unas dimensiones que proporcionen confort al usuario. En la zona de intervención prácticamente no hay edificios, de manera que hundir el edificio evita generar una barrera y se genera un espacio urbano nuevo.
Estructura industrializada
La parte más esencial del proyecto es la estructura, mediante una macro cercha que tiene dimensión suficiente para albergar uso dentro de la misma. Esta estructura tiene unas dimensiones de 84 metros de ancho y 8 de alto.
Dadas las dimensiones de la estructura y para facilitar el montaje, el traslado y la creación del edificio, he diseñado la estructura para que se pueda industrializar el proceso y generar el ensamblaje en el lugar de la intervención.
Durante el proceso de creación de la estructura, uno de los mayores retos fue plantear la construcción, el ensamblaje y el traslado de las cerchas de grandes dimensiones. Por este motivo, en el proceso de creación de la estructura, tanto la estabilidad como la construcción fueron esenciales para el diseño. Una vez definida la forma principal de la cercha, se fueron generando cálculos estructurales y ajustes en la misma para que la estructura fuese estable, siempre teniendo en cuenta las dimensiones y piezas que cambiaban en cada variación y cómo la formación de la gran cercha podía dividirse en grupos de piezas que se pudiesen ensamblar en fábrica.
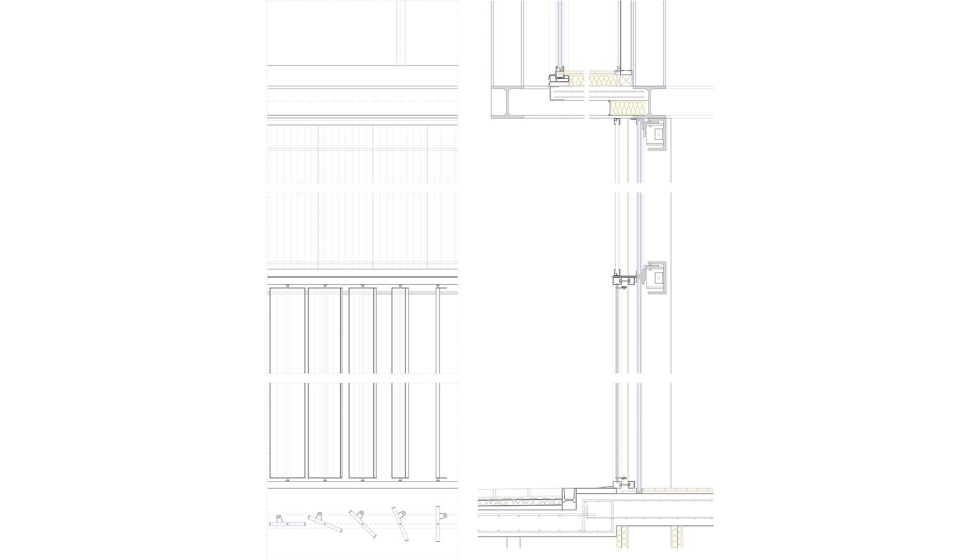
La idea partió de la forma principal de la estructura: además de las dos vigas curvas principales que forman el cordón superior e inferior, la cercha está formada por montantes que dividen la pieza en 12 ‘sectores’. Estos grupos de piezas, formados por secciones de los cordones, medios montantes laterales y un tirante diagonal, se diseñan de manera que se puedan ensamblar en fábrica y trasladar al lugar, para realizar la unión entre ellas y formar la totalidad de la cercha ‘in situ’.
La idea es descomponer las vigas por partes: los montantes verticales, que son perfiles tipo HEB, se ‘separan’ en perfiles UPN que, al enfrentarse, formarían un perfil que se asemeja en forma y comportamiento al originalmente calculado.
La idea era usar perfiles HEB y UPN extruidos en fábrica con medidas estándar, además de unos perfiles extruidos y curvados a medida, que conformarán los cordones superior e inferior. Se realizarán en el taller una serie de perforados a lo largo del alma de la viga, que permitirán la unión entre los dos perfiles a través de atornillamientos a la hora de formar la viga final en el lugar. La formación de los distintos grupos será realizada en taller.
Segregada la estructura en estas subpiezas, he realizado un último cálculo contando con los nuevos tipos de perfiles, para una la última comprobación estructural y asegurar la funcionalidad de la cercha. Aún con los perfiles conformados, el comportamiento de la estructura final será parecido.
El último paso de unión y refuerzos entre grupos de piezas en obra serán esenciales y, además del atornillamiento, las piezas se soldarán entre ellas por el perímetro para reforzar la unión. La fusión de piezas por soldadura provee de una junta mucho más resistente y rígida, necesaria a pesar de las uniones atornilladas, que se realizan rápidamente, pero no son tan resistentes a los movimientos internos de la cercha. De esta manera, se ensamblarán las piezas entre ellas y se formarán todas las cerchas de la estructura.
Impacto en las emisiones de CO2
La sostenibilidad siempre fue un aspecto clave en el proyecto. La construcción industrializada de estas piezas no sólo facilita el proceso constructivo, sino que además mejora el transporte dadas sus dimensiones, disminuyendo así el tiempo dedicado a la estructura en obra. Esto también implica un gran cambio en el impacto climático de la obra, siendo el ensamblaje de la estructura uno de los principales generadores de CO2 en el proceso de construcción. Mientras que el coste en CO2 que implicaría ensamblar toda la estructura en obra tendría un valor del 37% del valor del gasto original en obra (equivalentes a 1.851.698 kg CO2/m2). Con el sistema de preensamblaje en fábrica se reduciría hasta un 14% de impacto (equivalentes a 618.475 kg CO2/m2).
El segundo aspecto esencial para el proyecto fue el cerramiento del edificio. La idea principal es generar una imagen de transparencia, creando la ilusión de que la estructura y el programa que contiene flotan. Por ello, toda la fachada es acristalada, cosa que permite la entrada de luz natural al edificio, complementada por un sistema de control solar de láminas de policarbonato norte y sur, que permiten la entrada de luz difusa al interior. Para la proyección a este y oeste, la misma segunda planta contenida en la estructura genera un voladizo, respecto a las dimensiones de la primera planta.
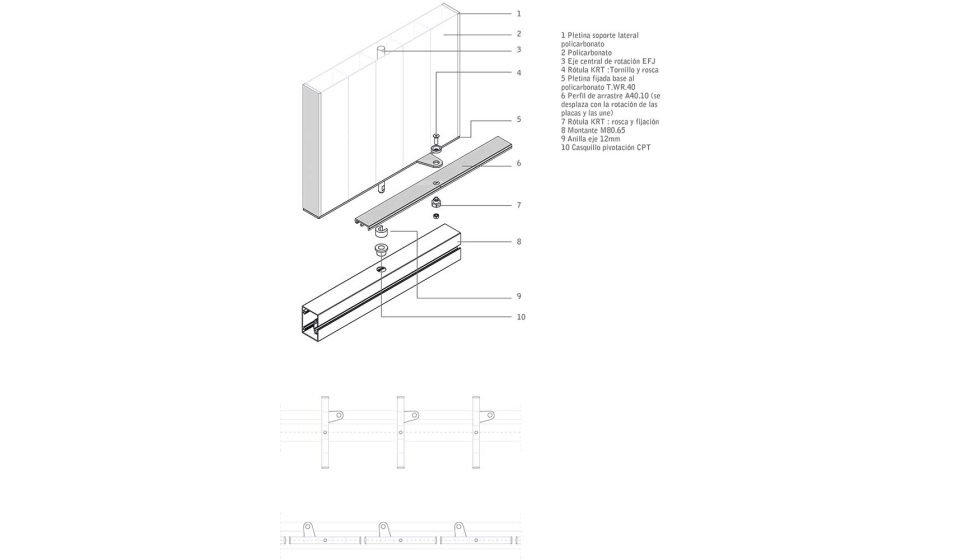
Fechada con sistema de láminas ensambladas
Para el diseño de la fachada he querido crear una franja de lamas rotatorias y otra de lamas fijas. Esto da la opción a los usuarios del polideportivo a abrir las lamas para permitir mayor entrada de luz a la sala.
El diseño del control solar es un marco metálico que sostiene las distintas piezas de tamaño estandarizado que contienen las lamas. Al crear varias piezas, el ensamblaje de las lamas y los marcos y soportes se pueden realizar en fábrica, con el sistema estándar de ensamblaje que se usaría con otro tipo de materiales como lamas de madera, cerámica, etc. Es así como, tomando la medida de agrupaciones de 5 láminas de policarbonato, he podido generar un módulo estándar que, una vez ensamblado en taller y trasladado a obra, solo tendría que colgarse en el edificio antes de realizar la fachada acristalada.
Precisamente, la fachada acristalada se situará entre los pilares estructurales, permitiendo ensamblar los montantes soporte verticales por delante de esta fachada, de manera que queden enrasados a estos pilares estructurales, garantizando que los soportes horizontales del control solar estén apoyados tanto en los montantes como en los pilares. Al fijar los soportes horizontales, y una vez realizadas las piezas que conforman la fachada, el último paso es colocar las piezas en obras y realizar el ensamblaje atornillado.
Los perfiles horizontales tienes unas perforaciones que encajan con las piezas de control solar, de manera que se apoyan, cuya colocación de la propia pieza es mediante enganche en la perforación, solo siendo necesario pasar un tornillo y tuerca para fijar el sistema por detrás. Es importante que el control solar se fije antes de realizar la fachada, dado que la fijación es más sencilla de realizar por detrás de las piezas.
Este sistema, aplicable a otros edificios o proyectos en el caso de que se quisiese realizar posteriormente a la construcción de un edificio, dejando fuera la posibilidad de ensamblar las piezas antes que la fachada, también permitiría una opción de ensamblaje, realizando el montaje desde el exterior con las lamas abiertas.
Esta manera de ejecutar la fachada permitirá reducir considerablemente el coste de CO2 en obra, reduciendo el valor de montaje en obra de 22.774 kg CO2/m2, hasta unos 5.465 kg CO2/m2, siendo esto una reducción de un 76% del valor original.
De esta manera, y a través de sistemas de construcción industrializada, se consigue una mayor precisión, rapidez en la construcción y una gran aportación a la sostenibilidad y la eficiencia en este proyecto, aun manteniendo el diseño del edificio, facilitando la construcción y el transporte y mejorando los sistemas.
El proyecto ‘Ilia’ de María Eggert Roig fue uno de los TFG que participaron en la convocatoria organizada por la UIC Barcelona, para estudiantes de arquitectura, que intervenían de forma coordinada en una propuesta para regenerar los barrios situados en el área del Besós (Barcelona).