Vreugdenhil Dairy Foods automatiza y controla su nueva planta de leche con Rockwell Automation
GEA es uno de los mayores proveedores tecnológicos del mundo para la industria alimentaria, que representa el 70% de sus ingresos. Con unos 17.000 empleados en más de 50 países, la compañía está especializada en la construcción de plantas de procesamiento de alimentos de todo tipo, entre los que destaca el sector lácteo. En palabras de Alejandro Nectalí, ingeniero de automatización de GEA España: “Proporcionamos una solución integral, que va desde el diseño y el desarrollo del proceso, la ingeniería y la tecnología; hasta la entrega, la instalación y la puesta en marcha de la planta”.
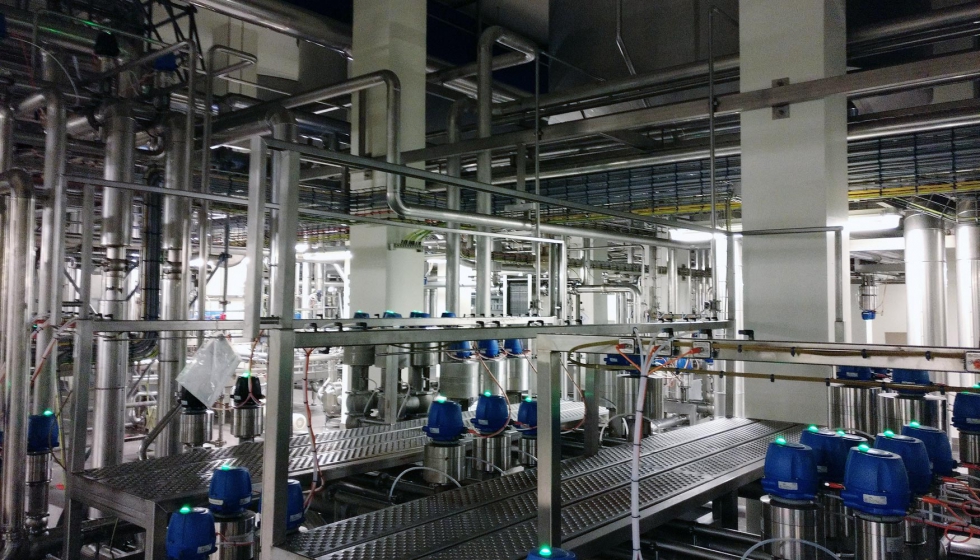
La compañía está especializada en suministrar plantas diseñadas para operar continuamente en régimen 24/7. “Esto permite que los productores maximicen el aprovechamiento de la capacidad instalada”, apunta Nectalí, quien añade: “Nuestras plantas se diseñan para cumplir con los requisitos específicos de cada cliente, de acuerdo con los estándares del sector lácteo, e incorporando siempre los avances tecnológicos más recientes”.
Uno de sus clientes es Vreugdenhil Dairy Foods, una empresa con sede central en Nijerk y tres plantas de producción en Holanda, que lleva en el mercado desde 1954. Es el mayor productor de leche entera en polvo en Europa. Con tres fábricas y 900 granjeros holandeses que entregan el producto en bruto, produce leche en polvo para la industria alimentaria y para millones de consumidores en todo el mundo.
El desafío
La filial holandesa de GEA se enfrentó a un complicado reto: construir de cero una nueva planta de producción de leche en polvo de 13.000 metros cuadrados para la compañía Vreugdenhil Dairy Foods en Gorinchem.
Esto requería la confluencia de varios procesos, que van desde la separación de la leche cruda en leche desnatada y crema, hasta la evaporación y secado por atomización, así como el manejo y envasado de la leche en polvo.
Ante la magnitud del desafío, la filial holandesa de GEA decidió recurrir a otras sucursales de la compañía en otros países ya que al tratarse de una compañía multinacional su know-how está descentralizado. En este sentido, GEA Holanda proporcionó tanto el top management del proyecto como el equipo de ingeniería de proceso de leche líquida; GEA España suministró la ingeniería de automatización; GEA Francia, la ingeniería de evaporación; GEA Dinamarca, la ingeniería de secado; GEA Nueva Zelanda, la ingeniería de manejo de polvo; y GEA Alemania, la ingeniería de separación. Así el proyecto pasó a ser internacional y multidisciplinar y requirió de varios equipos de trabajo de distintas compañías colaborando conjuntamente en varios países para asegurar el éxito del proyecto.
Sin embargo, había una parte común a todos ellos: los Sistemas de Control y la automatización. Esta área fue realizada y supervisada por el equipo de GEA España. “En este ámbito, uno de los desafíos planteados era implementar una solución única para toda la planta que incluyera el hardware, software y redes de control de todas las áreas de la planta, desde la recepción de materiales al envasado”, explica Nectalí. “Se decidió desplegar una plataforma común basada en productos y soluciones de Integrated Architecture de Rockwell Automation gracias a la buena experiencia con la solución Rockwell Automation en otra planta de producción de Vreugdenhil Dairy Foods”.
Así también lo confirma Hans van der Heijden, ingeniero de proyecto de esta empresa láctea: “Nuestra actual fábrica tiene instalados 17 controladores Allen-Bradley PLC 5 (25E, 40E y 80E, y 80 SLC 5/04) de Rockwell Automation y a nuestros ingenieros les resultaba familiar el entorno de programación. De hecho, cada año enviamos a varios de nuestros técnicos a Rockwell Automation para mejorar sus conocimientos”.
La solución
GEA fue capaz de sacar adelante el proyecto gracias a su experiencia en implantaciones anteriores, el conocimiento adquirido y el trabajo conjunto con Rockwell Automation, que fue capaz de proporcionar un soporte global para el proyecto interviniendo localmente tanto en España como en Holanda. Según van der Heijden, “ambas filiales nos ayudaron mucho a establecer las primeras definiciones de arquitecturas, y nos ofrecieron en todo momento un buen soporte durante el proceso de implantación”.
Una vez hecho el estudio inicial, GEA procedió a la implementación de las soluciones de Rockwell Automation. Desde los dispositivos de campo al sistema de reporting, todos los elementos están conectados mediante Ethernet/IP lo que facilita enormemente las comunicaciones y el flujo de datos.
Los variadores Allen-Bradley PowerFlex y los relés de protección E300 están integrados en el sistema, facilitando la configuración y diagnóstico de los motores con la distribución de señales por campo Allen-Bradley Flex I/O. Todos estos elementos de campo se conectan mediante switches Stratix 5700 y 1783-ETap a los controladores de automatización programables Allen-Bradley ControlLogix, a los terminales gráficos Allen-Bradley PanelView Plus 6 y a los diferentes PCs del sistema.
El software del sistema de control se implementó en una infraestructura de virtualización VMWare utilizando únicamente dos servidores físicos. El software FactoryTalk, plataforma de aplicaciones orientada a Servicios (SOA) fue usada para este objetivo dado que permite compartir elementos como permisos y roles de usuario, comunicaciones, logs, etc. entre los diferentes softwares que la componen.
Se utilizaron los softwares de supervisión y control Scada FactoryTalk View SE, con captura de datos e historización a través de FactoryTalk Transaction Manager y FactoryTalk Historian. El reporting se realizó a través de FactoryTalk Vantagepoint, y gestión de activos, incluyendo control de versiones, audits y disaster recovery con FactoryTalk AssetCentre. Todo esto, a juicio de Van der Heijden, “permite a su empresa configurar los parámetros en los propios instrumentos, lo que facilita la gestión”.
Los resultados
Gracias al diseño de sistema realizado por los ingenieros de GEA que utilizaron sistemas de Rockwell Automation, la nueva fábrica de leche en polvo de Vreugdenhil Dairy Foods es capaz de producir 8 toneladas a la hora de leche en polvo y cuenta con una capacidad de procesar 1.600.000 litros de leche cruda al día, con la ventaja de que estos parámetros son totalmente escalables.
Precisamente, ésta es una de las grandes ventajas que, a juicio de Nectalí, supone trabajar con Rockwell Automation: “La ventaja de usar Rockwell Automation es la de disponer de una única plataforma para la planta donde todo está preparado para trabajar conjuntamente. Todos los elementos son fácilmente interconectables, y no hemos tenido problemas para integrarlos entre sí. Simplemente se añade un nuevo componente y el propio sistema lo reconoce al instante. Es mucho más amigable trabajar con una solución única de Rockwell Automation”, comenta.
Esto, a su vez, repercute también en el propio cliente, según Nectali. “Cuando terminamos el proyecto y nos marchamos de la fábrica, nosotros ya no somos necesarios, puesto que el cliente puede hablar directamente con los expertos de Rockwell Automation para la formación de su personal o consultarles una duda o resolver cualquier incidente. Esto es muy bueno para el cliente, porque al disponer de soporte local por parte del fabricante y poder formar a su propio equipo, no depende de un integrador para futuras modificaciones; y también para nosotros ya que podemos cerrar el proyecto y entregar el mantenimiento de la fábrica a nuestros colegas del Servicio Local de GEA”.
Incluso, gracias al software de Rockwell Automation, los operarios de Vreugdenhil Dairy Foods pueden extraer sus propios informes de producción personalizados utilizando una herramienta tan común y generalizada como Microsoft Excel. Estos informes se pueden consultar a través de un explorador web y utilizando terminales móviles como smartphones o tablets.
Por otro lado, la adopción de una solución de control única para toda la planta permite mejorar el uso y optimización de los activos de planta con una reducción de costes de la propiedad, se reduce la cantidad de repuestos y se simplifica la formación del personal de producción y mantenimiento. El sistema de Control de Rockwell Automation proporciona controladores multidisciplinares que pueden utilizarse en las diferentes áreas de la planta unidos con una única red de comunicaciones basada en Ethernet que permite el flujo de información en tiempo real entre las diferentes áreas y departamentos de la fábrica.
Otra ventaja importante es la conexión directa con la otra fábrica de Vreugdenhil Dairy Foods, que se encuentra muy cercana. “Todas las comunicaciones son mucho más sencillas y compatibles, porque se hacen a través de redes y protocolos de comunicación estándard”, apunta Nectalí, quien no esconde las ventajas que ha supuesto para su empresa haber trabajado en este proyecto: “Para nosotros, el desarrollo realizado en este proyecto con la tecnología de Rockwell Automation nos ha permitido estrechar lazos con esta empresa y reutilizarlo en proyectos futuros. De hecho, todo el esfuerzo realizado y la experiencia ganada los estamos aprovechando ya en nuevos proyectos de menor escala que tenemos en marcha en México, Puerto Rico, España y Francia, y en los que contamos exclusivamente con la tecnología de Rockwell Automation”, afirma Nectalí.
Por su parte, van der Heijden confirma que se encuentra “muy satisfecho” no sólo con Rockwell Automation, sino también con el trabajo llevado a cabo durante la implementación por parte de GEA.