Plásticos en automóvil: agradables al tacto, resistentes al calor… lo mejoran todo
Fíjese en su automóvil con atención. Hay plásticos por todos lados: en el exterior, en el interior, en los elementos de iluminación y en el espacio del motor. En el interior, por ejemplo, aunque los poliuretanos aromáticos no son resistentes a la luz y requieren por ello una capa de pintura, pueden competir perfectamente contra otros materiales debido al bajo precio del poliuretano. La pintura no solo mejora la duración de la pieza sino que tiene una importante función en la creación de dureza y de la sensación agradable al tacto, como resultado de la combinación de la fórmula de poliuretano, pintura y sistema de espumación.
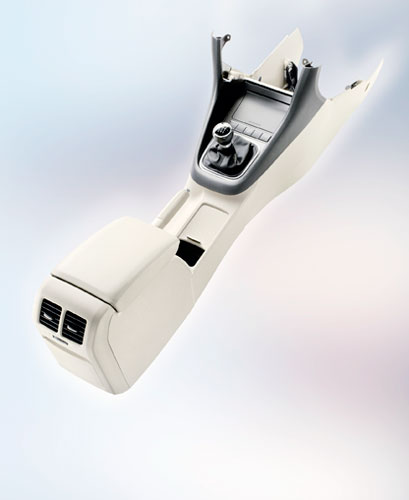
Veamos algunos ejemplos de aplicaciones interesantes. El interior del Golf GTI, un modelo todavía en fase de proyecto, llama la atención por su iluminación. Diversos componentes en 3D iluminan todo el interior en color cuando el sistema de iluminación está en marcha. Para ello se ha utilizado una película electroluminiscente bajo la premisa de que la luz del interior de los coches irá adquiriendo una importancia creciente. Este tipo de componentes se han diseñado para poner de manifiesto la amplia gama de opciones de diseño que estas películas ofrecen para crear un amiente determinado en interiores de automóviles. Por ejemplo los revestimientos decorativos de las puertas y de los salpicaderos incorporan este efecto iluminador. Además de su función decorativa, las películas electroluminiscentes son útiles para la iluminación indirecta de la guantera y el panelado del cuadro de mandos.
El exterior de los componentes está hecho con un grado de Makrofol transparente y de alto brillo. Se utiliza un proceso de serigrafía para imprimir la película con elementos gráficos y diversas capas de varios componentes del sistema electroluminiscente, como los electrodos y las capas aisladas eléctricamente, y luego se recurre a un proceso de conformado por presión para darle forma a la película por debajo de la temperatura en la que se ablanda.
Luego los componentes se recubren con una capa auto-reparadora de poliuretano de dos componentes. Lo que más destaca es la resistencia de esta capa al rayado. Las marcas leves simplemente desaparecen bajo el sol.
Los pigmentos inorgánicos en las capas no conductivas del film emiten luz en cuanto se les aplica un voltaje de 110 V a los electrodos a través de un inverter, recurriendo a la electricidad del coche. La intensidad de la luz se controla mediante el voltaje aplicado. Las piezas moldeadas de esta no requieren mantenimiento y duran mucho. Por eso se puede prescindir de bombillas, LED y fibra óptica forma. Según el pigmento electroluminiscente usado, el rango de colores puede ser desde azul, naranja y verde, hasta blanco.
Otra de las grandes ventajas de este sistema es que puede ser utilizado para crear componentes en dos y tres dimensiones, en cualquier forma, y que iluminan toda la superficie, incluyendo curvas y bordes.
El proceso de fabricación de piezas de plástico electroluminiscente es muy automático. La impresión, conformado, recorte y, si es necesario, inyección trasera con termoplásticos como PC y PC+ABS puede realizarse en un solo proceso, recurriendo al moldeo por inyección con inserción de film, un método muy habitual en la producción en serie de gran escala. El resultado son módulos completos y funcionales que son muy fáciles de ensamblar.
Más tecnología en el interior
Pero el de la iluminación es solo uno de los actuales aspectos que se tienen en cuenta a la hora de diseñar un interior de vehículo. En BASF Polyurethanes GmbH, por ejemplo, se han desarrollado dos soluciones de poliuretanos a la medida: una de ellas es el recubrimiento dentro del molde mediante el rociado de una piel de Elastoskin y el otro el poliuretano termoplástico alifático modificado Elastollan. Ambos sistemas tienen un alto valor estético. El primero de ellos, además, es blando, porque recibe una espumación adicional, por lo que se utiliza en reposabrazos, paneles de instrumentos o revestimientos de interiores de puertas. El otro sistema proporciona una agradable sensación al tacto y se utiliza en tiradores de puertas, cubiertas de consolas o dispositivos para sujetar vasos.
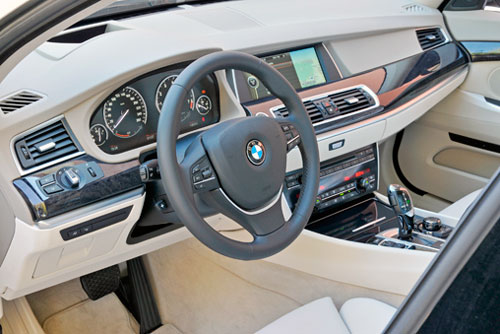
Con las limitaciones a las emisiones en el fondo, la mayoría de los fabricantes de automóviles y suministradores están trabajando bajo presión en el desarrollo de nuevos motores, como los eléctricos. Los nuevos coches eléctricos e híbridos están poniendo sobre la mesa nuevas exigencias para los cables y conductos, que tienen que soportar temperaturas muy superiores. En respuesta a ese requerimiento BASF Polyurethanes GmbH ha añadido la nueva variante Elastollan 785 A 10 HPM a su gama de poliuretanos termoplásticos para revestimientos de cables (HPM se refiere a ‘high performance material’).
Bajo el capó también se encuentran muchos plásticos mejorados, como las poliamidas desarrolladas específicamente para soportar elevadas temperaturas y mantener la propiedad de una larga vida. Por ejemplo, Stanyl Diablo OCD2300 amplía la vida útil de los componentes en comparación con otras poliamidas destinadas a resistir altas temperaturas, limitando la degradación causada por la oxidación térmica. Soporta más de 3.000 horas a temperaturas de 230°C antes de que su resistencia a la tracción quede en la mitad de la que tenía inicialmente.
Los requerimientos para las aplicaciones que se encuentran en la zona del motor cambian constantemente. Las exigencias medioambientales, como la ley EURO V y VI y la llamada a un menor consumo de combustible han como consecuencia cambios importantes, como el uso de motores más pequeños con mayores presiones de turbo y sistemas de depuración de gases de escape. La consecuencia es que los componentes que se encuentran bajo el capó, como conductos de aire, colectores de admisión y otros, están expuestos a temperaturas que cada vez son más altas. Con unas temperaturas en ascenso y exigencias más severas en relación con la duración de los componentes, la vida útil de los termoplásticos corrientes se ve amenazada. Es por eso que los progresos de las poliamidas se encaminan a una mayor resistencia a las temperaturas, manteniendo e incluso mejorando las propiedades mecánicas.
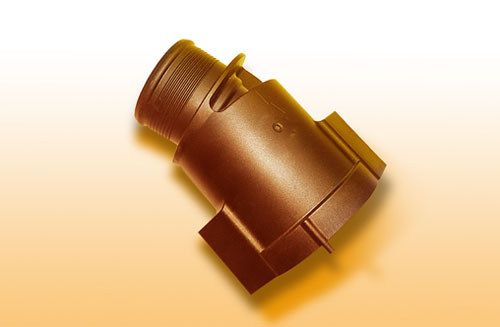