Recubrimientos PVD en el procesado de chapa y plástico
El material elegido y los tratamientos que se le apliquen tendrán una incidencia directa en los fallos y fenómenos de desgaste que ocurran en su superficie. La búsqueda de una solución a los fallos en los útiles implica el estudio de las cargas mecánicas y el análisis de los tipos de degradación que sufren. (Fig. 1).
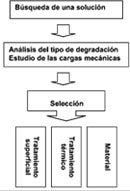
Características de los recubrimientos PVD
La utilización de los recubrimientos PVD para extender la vida útil de las herramientas ha crecido fuertemente en los últimos 20 años. El proceso de recubrimiento ha mejorado continuamente y hoy en día existen multitud de recubrimientos innovadores que se depositan mediante un proceso seguro y reproducible (Tabla 1).
BalinitA | BalinitB | BalinitD | Balinit FUTURA NANO | Balinit X.TREME | Balinit HARDLUBE | Balinit DIAMANTE | BalinitC | Balinit DLC | |
Material de recubrimiento | TiN | TiCN | CrN | TiAIN | TiAIN | TiAIN/WC/C | Diamante Policristalino | WC/C | a-C:H |
Microdureza HV (HV 0,05) | 2.300 | 3.00 | 1.750 | 3.300 | 3.500 | 3.000 | 8.000 | 1.000 | 4.000 |
Coeficiente de fricción | 0,4 | 0,4 | 0,5 | 0,9-0,95 | 0,4 | 0,2 | 0,2 | 0,2 | |
Grossor de la capa (mm) | 1-4 | 1-4 | 1-4 | 2-5 | 1-3 | 2-6 | 6-30 | 1-4 | 0,5-3 |
Temperatura màx. de trabajo | 600º C | 400º C | 700º C | 900º C | 800º C | 1.000º C | 300º C | 300º C | |
Color de la capa | Amarillo-Oro | Azul-Gris | Plata-Gris | Gris-Violeta | Gris-Violeta | Gris-Oscuro | Negro-Gris | Gris-Oscuro | Negro |
Además de los recubrimientos de alta dureza como el nitruro de titanio, en los últimos años se han desarrollado sobre todo recubrimientos llamados “tribológicos” con propiedades optimizadas contra la fricción. El objetivo de estos recubrimientos es evitar la abrasión y fricción y ahorrar, o incluso suprimir, lubricantes. Hoy en día, muchos procesos de conformado pueden hacerse en seco gracias a los recubrimientos tribológicos. Como consecuencia, se pueden evitar las costosas limpiezas de componentes, reducir costes y minimizar la contaminación medioambiental.
Procesado de chapa
Las modernas tecnologías de conformado nos permiten fabricar piezas de dimensiones más exactas, con una mayor calidad superficial y con formas más complejas.
Las altas cadencias de producción, conseguidas con un número de golpes por minuto elevado, generan altas solicitaciones en el útil de conformado.
Para optimizar la vida de estos útiles es necesario estudiar los fenómenos de degradación que ocurren en la superficie de trabajo. Dos de los tipos de degradación que afectan a la superficie del útil son la abrasión y la adhesión.
Abrasión
Ocurre cuando las duras partículas del material a conformar rayan la superficie del útil. Para evitar este problema, el útil tiene que tener una alta dureza superficial.
Adhesión
Es el resultado de la soldadura en frío del material de la pieza a conformar y la superficie del útil. Para evitar este problema, necesitamos un bajo coeficiente de fricción y una baja afinidad entre los materiales en contacto.
Los distintos tipos de degradación y la forma de actuar para evitarlos se muestran en la tabla 2.
TIPO DE GRADACIÓN | PROPIEDADES REQUERIDAS | LOCALIZACIÓN DE DEGRADACIÓN | ACTUAR EN... |
Deforma plástica | Resistencia a la compresión | Sustrato | Acero+ tratamiento térmico |
Rotura | Tenacidad | Sustrato | Acero+ tratamiento térmico |
Abrasión | Dureza | Superficie | Acero+ trat.térmico+ recubrimiento |
Adhesión (soldadura en frío) | Bajo coeficiente de fricción | Superficie | Acero+ trat.térmico+ recubrimiento |
Aplicaciones en el procesado de chapa
En la foto 2 se puede apreciar la pieza embutida y la matriz utilizada para ello. La chapa a conformar era AP-33 de 24-40 kg/mm2.
Esta pieza debe tener unas dimensiones muy precisas y no puede tener ningún arañazo en la superficie de fuera. En el proceso de embutición el grosor de la chapa se reduce de 4mm a 3,8 mm. Antes utilizaban cromo duro y conseguían 3000-5000 piezas. Utilizando el recubrimiento Balinit A el número de piezas conseguido fue 120.000.
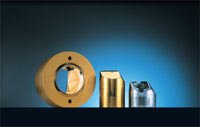
Hoy en día una de las mayores preocupaciones de la industria del conformado, además de reducir costes, es reducir la cantidad de lubricantes utilizados y conseguir así un “conformado ecológico”.
En el proceso de fabricación de la pieza de la foto 3 había constantes problemas de soldadura en frío entre el útil y la chapa. Además, después del conformado, la pieza tenía que limpiarse y soldarse (foto 4). Se probó el cromo duro para intentar solucionar el problema y, utilizando lubricante, se consiguieron fabricar 10.000 piezas. En la actualidad, usando el recubrimiento Balinit A se están fabricando más de 100.000 piezas en seco. Sólo se utiliza la lubricación contra la corrosión que lleva la chapa.
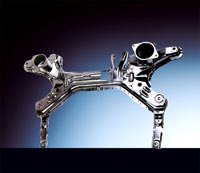
Las paradas de producción en la inyección de plástico, cuando son causadas por el molde, pueden tener su origen bien en problemas de desgaste o bien en problemas de perturbaciones.
En la figura 2, se muestran los distintos problemas de desgaste y perturbaciones que pueden darse en un molde de inyección de plástico.
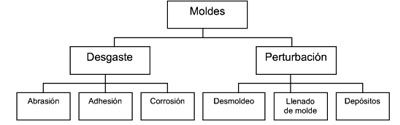
La abrasión tiene lugar cuando se procesan plásticos con aditivos como fibra de vidrio o fibras de refuerzo. La alta dureza de los recubrimientos PVD protegen el molde contra este tipo de desgaste.
La adhesión ocurre cuando dos piezas de acero deslizan una contra otra. Las inmejorables propiedades tribológicas de los recubrimientos PVD (tabla 1) permiten la producción en seco de sofisticados componentes de plástico para aplicaciones farmaceúticas, médicas y envasado de alimentos. Los recubrimientos PVD combinan las excelentes propiedades de deslizamiento con altas durezas y protegen contra el agarrotamiento a piezas deslizantes como eyectores, elementos de guía, correderas y machos de desenroscado.
Los recubrimientos PVD, además de su alta dureza, son prácticamente inertes. Esto hace posible producir un alto número de inyectadas sin aparición de depósitos y, en el caso de que se den, son más fáciles de limpiar.
Los recubrimientos PVD facilitan el desmoldeo. Esto es ventajoso principalmente en las piezas que deben ser procesadas sin desmoldeantes. En los casos en los que sean necesarios, se puede reducir su cantidad.
Los recubrimientos PVD también mejoran el llenado del molde, especialmente en piezas de paredes delgadas. Esto es debido al cambio en el comportamiento de la masa inyectada. Las fotos 5 y 6 muestran la microestructura de la capa límite sólida en el material POM. La foto 5 muestra el material POM inyectado en una cavidad sin recubrimiento y la foto 6 el material POM inyectado en una cavidad con Balinit A.
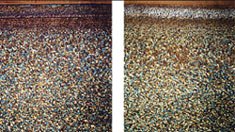
(izqda.)10mm . Lado interior de un anillo en POM.Macho sin recubrir (dcha.)10mm.Macho recubierto con BALNIT A
Cuanto menor es la “capa límite sólida”, mayor es la sección de flujo y, por tanto, se puede conseguir una mayor longitud de flujo. La reducción del espesor de la capa límite sólida reduce las tensiones internas de la pieza inyectada, lo que consigue minimizar las deformaciones producidas durante el desmoldeo.
Aplicaciones en procesado de plástico
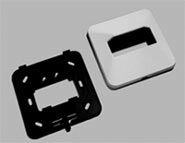
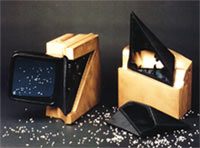
Molde: Material DIN 1.2767, 44 HRc. Material: EPDM. Sin recubrir: Los moldes necesitan ser limpiados por granallado, 2 a 3 horas, cada 2.000 ciclos. La calidad superficial de la pieza se va deteriorando debido a los depósitos. Ratio de rechazos, 12%. Recubierto con Balinit A: Es suficiente una limpieza con ultrasonidos cada 36.000 ciclos. Mejor calidad superficial debido a la reducción de depósitos. El ratio de rechazos se reduce un 5%.
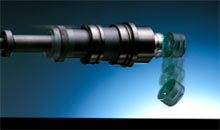
Conclusiones
Desde los pioneros recubrimientos TiN, los recubrimientos PVD han evolucionado constantemente para cumplir con los exigentes requerimientos de la moderna ingeniería. Actualmente, el estado del arte en el mundo de los recubrimientos PVD es la nueva generación, G6, desarrollada por Balzers. La primera capa de esta nueva generación es el BALINIT ALCRONA, que lleva una composición libre de titanio patentada por Balzers.
También se puede subrayar la contribución de estos recubrimientos en la fabricación de moldes y matrices. El mecanizado a alta velocidad y de materiales templados sería impensable hoy en día sin la utilización de recubrimientos PVD.
Por lo tanto, se ha podido demostrar que los recubrimientos PVD ofrecen beneficios sin par en cuanto a la reducción de costes y mejora de la productividad, pero además, han causado un impacto significativo en el concepto de sostenibilidad global. Podríamos decir que la sostenibilidad es el crecimiento económico que beneficia a las generaciones presentes y futuras, sin causar daños en los recursos naturales y los sistemas biológicos en el mundo.
Por un lado, la tecnología PVD es un proceso limpio y, por otro lado, los útiles recubiertos con PVD permiten utilizar procesos más limpios como el mecanizado y conformado en seco. Además, permiten la reducción de lubricantes o la utilización de lubricantes menos dañinos para la salud y el medioambiente.