Desarrollo de polvos ad-hoc para recubrimientos monocapa en Laser Cladding
Dr. Xabier Lasheras, Tecnologías de Conformado. Centro de Investigación Metalúrgica Azterlan
14/10/2024Problemática de dilución substrato-recubrimiento
Como es sabido, la tecnología L-DED se basa en la adición de polvo metálico sobre un substrato al mismo tiempo que se funde el polvo añadido y la superficie del substrato mediante energía aportada por un láser. De esta fusión se genera una unión metálica entre el material aportado y el substrato. Una de las principales aplicaciones de la técnica L-DED es la de producir piezas bimetálicas, es decir, componentes que posean un núcleo de un material, con sus propiedades correspondientes, y un material de recargue diferente, con sus propias características.
En estos casos, las propiedades superficiales de la pieza producida dependerán, principalmente, de la composición química del metal añadido en formato polvo, que se pretende que sea el material superficial de la pieza final. No obstante, al igual que sucede en procesos de soldadura, la aportación de energía mediante láser y la consecuente fusión parcial de la superficie del substrato induce que el material en polvo aportado como recargue se mezcle parcialmente con el primero, resultando en un material mixto. A este fenómeno se le denomina efecto de dilución y su dimensión es dependiente de la parametrización empleada durante el proceso y de los materiales (substrato y material de recargue) involucrados en el proceso. El efecto de dilución se visualiza en la micrografía mostrada en la imagen 1.
Esta mezcla causada por el efecto de dilución modifica la composición química del material de recargue, alterando las propiedades superficiales que se pretendía aportar a la pieza, pudiendo llegar a quedar fuera de las especificaciones buscadas.
El método actualmente existente para contrarrestar este efecto de dilución es el de añadir capas sucesivas del material de recargue. De esta manera, al aportar la primera capa del material, este se diluye con el substrato; al añadir una segunda capa, esta se diluirá con la primera capa añadida, acercándose más a la composición química deseada. Con capas sucesivas irá sucediendo lo mismo, es decir, el efecto de dilución irá atenuándose hasta casi anularse completamente. Sin embargo, esta solución no resulta eficiente ya que implica el uso de una cantidad excesiva de material de recargue, mayor tiempo de fabricación y mayor tiempo de mecanizado posterior.
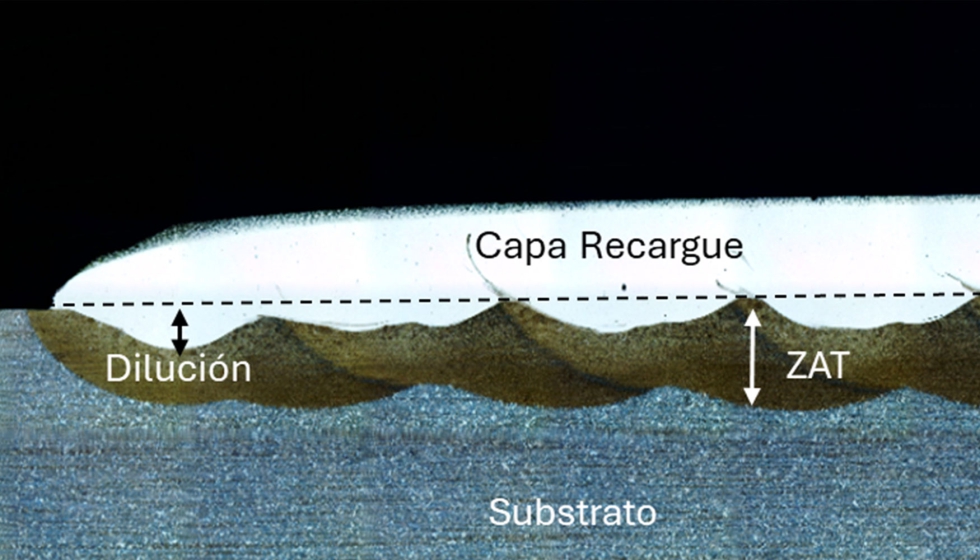
Solución alternativa: polvo de compensación
La solución alternativa desarrollada por Azterlan para contrarrestar el efecto de dilución pasa por añadir un polvo de compensación juntamente con el material de recargue durante el proceso de L-DED. El objetivo de este polvo no es otro que aportar al recargue los elementos que se van a perder a causa de la dilución, consiguiendo como resultado una composición química en el recargue igual a la del polvo metálico añadido inicialmente, aportando una única capa de recargue.
El propósito de este método es evitar tener que aportar múltiples capas para contrarrestar la dilución, reduciendo de esta manera de forma considerable los tiempos de fabricación en este paso crítico, y minimizando también la cantidad de material de recargue empleado y el tiempo de mecanizado final.
Sin embargo, como es lógico, no existe un polvo con composición química universal que permita contrarrestar el efecto de dilución en cualquier proceso de L-DED. Este polvo de compensación (CP) ha de ser diseñado ad-hoc para cada proceso de fabricación específico, ya que la dilución a contrarrestar será dependiente de los materiales de substrato y de aporte, y de la parametrización usada en el proceso de L-DED.
En este artículo se presenta el proceso de diseño y fabricación de dicho polvo para un proceso de fabricación específico, concretamente, diseñar el polvo de compensación para recubrir un acero estructural (42CrMo4 (BS)) con un acero inoxidable (316 (SS)), aportándole así propiedades superficiales anticorrosivas a un acero que, inicialmente, no tiene.
Diseño del polvo de compensación
El proceso de diseño del polvo metálico de compensación para un proceso de fabricación específico consiste en tres pasos principales (imagen 2):
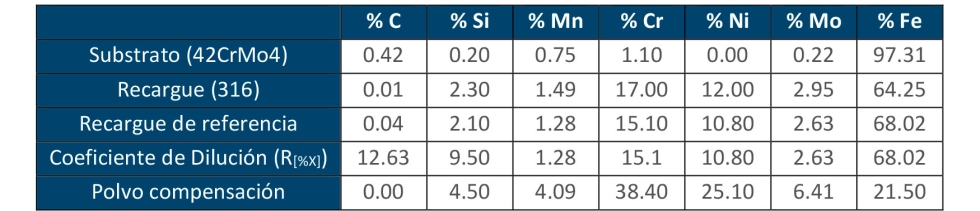
Tabla 1. Composiciones químicas del substrato (BS), polvo de recargue (SS), recargue de referencia (SSC), coeficientes de dilución para cada elemento y polvo de compensación (CP).
1. Optimización de parámetros de L-DED
La parametrización en un proceso de L-DED es muy sensible y tiene un efecto directo sobre el resultado del proceso. Modificaciones en estos parámetros pueden ocasionar aparición de poros, grietas, cambios en el espesor del recargue y, por supuesto, distintos grados de dilución. Por ello, condiciones como la potencia de láser, tamaño del spot, velocidad de paso de láser, flujo de polvo, etc. han de ser optimizadas y fijadas previamente para el proceso específico que se va a realizar.
2. Cálculo de coeficientes de dilución
Una vez fijada la parametrización óptima para el proceso de L-DED específico, el próximo paso es el de medir el grado de dilución que se da en este proceso. Para ello se realiza un proceso de L-DED de referencia, recargando un substrato con el material de recargue en las condiciones optimizadas para el objetivo perseguido. La muestra resultante es empleada para medir la dilución ocurrida. Con este fin, pueden aplicarse dos estrategias: por una parte, es posible tomar una micrografía (corte perpendicular respecto a la dirección de recargue) de la pieza fabricada para medir el área de dilución: muestra de ello es la imagen 1. Por otra parte, también se puede determinar el grado de dilución midiendo la composición química de la capa de recargue obtenida. En este caso, a través de un balance de masas con las composiciones del material de recargue (316 (SS) en el caso de estudio concreto) y el substrato (42CrMo4 (BS)), se calculan los coeficientes de dilución (R[%X]) obtenidos para cada elemento (ver ecuación 1 e imagen 2).
3. Cálculo de la composición química del Polvo de Compensación
En este punto ya es posible calcular la composición química del polvo de compensación para contrarrestar la dilución en este proceso específico. Para ello, y en base a la ecuación 2, se calcula la composición química para cada elemento a partir de su coeficiente de dilución. Previamente, es necesario establecer el parámetro Z, es decir, el ratio entre el material de recargue (316) y el polvo de compensación que se va a emplear en el proceso de fabricación final. Para este caso de estudio, se ha fijado un ratio del 10%; sin embargo, en casos con coeficientes de dilución muy altos puede ser necesario aumentar este ratio para contrarrestar la dilución de forma efectiva. En la tabla 1 se muestra la composición de polvo de compensación calculada.
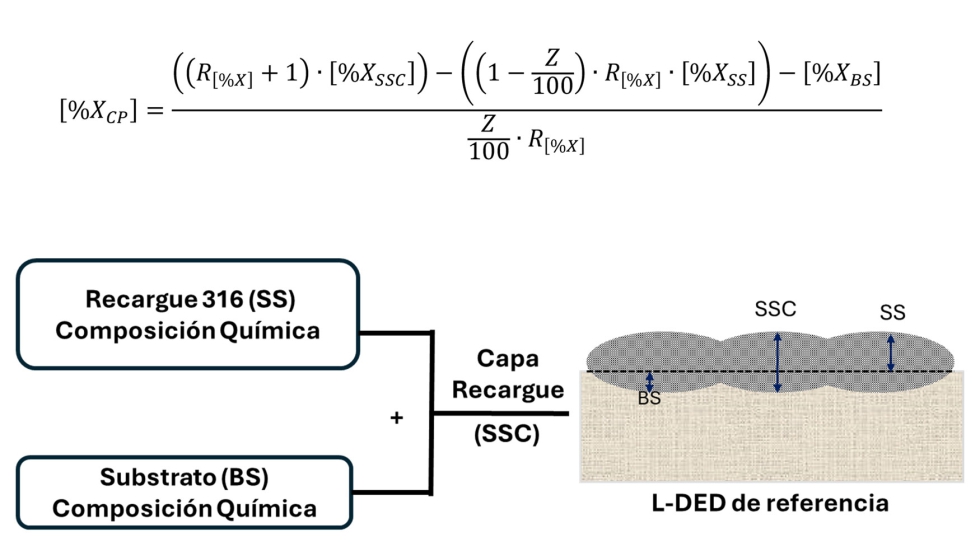
Imagen 2. Esquema del proceso de L-DED de recargue para cálculo de coeficientes de dilución (ecuación 1) y diseño de composición química del polvo de compensación (ecuación 2).
Fabricación del Polvo de Compensación
Una vez diseñada la composición química objetivo del polvo de compensación, el siguiente paso consiste en fabricar la cantidad necesaria de este polvo. En el presente caso, el polvo de compensación ha sido fabricado en las instalaciones de Azterlan, siguiendo los pasos que se detallan a continuación.
El primer paso consistió en fundir la aleación con la composición química definida. Dado que en este caso es crítico asegurar la composición química exacta, y con el fin de minimizar las pérdidas y contaminaciones, la fusión se realizó en el horno de inducción en vacío ubicado en la Planta Piloto de Fundición de Azterlan (Imagen 3).
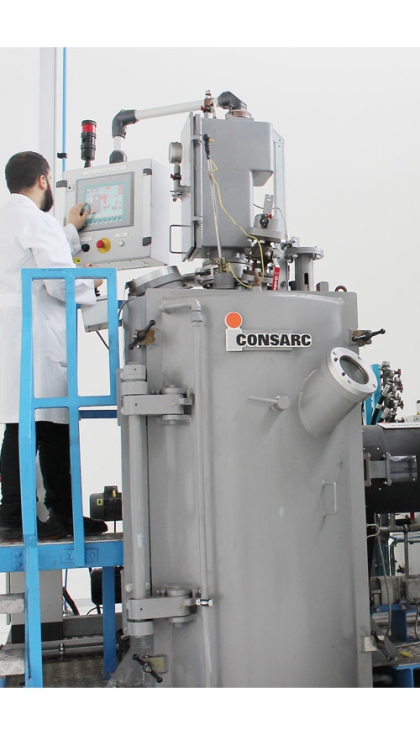
Imagen 3. Horno de vacío en la Unidad de Tecnologías Avazadas de Azterlan.
Posteriormente, esta aleación fue atomizada en la Unidad de Atomización de Polvos Metálicos, en las mismas instalaciones de Azterlan (Imagen 4). Puesto que este sistema solo acepta materiales de partida en formato de hilo, barra o viruta, el lingote de material obtenido de la colada fue previamente transformado en barras cilíndricas mediante mecanizado.
El equipamiento de atomización de polvos metálicos es un sistema de atomizado ultrasónico, el cual es idóneo para conseguir polvo metálico de alta calidad (alta esferoidicidad, sin porosidad ni satélites y distribución de tamaños estrecha), ofreciendo además gran flexibilidad para atomizar distintas aleaciones. Si bien cuenta con una productividad inferior a la de los sistemas de atomización por gas empleados habitualmente en la fabricación industrial de polvos metálicos, los tamaños de partícula obtenidos (20-120 µm) son idóneos para procesos de fabricación aditiva. Aunque es posible fabricar el polvo metálico por otras tecnologías, el tamaño de partículas resultantes para su aplicación vía laser ha de encontrarse en ese rango.
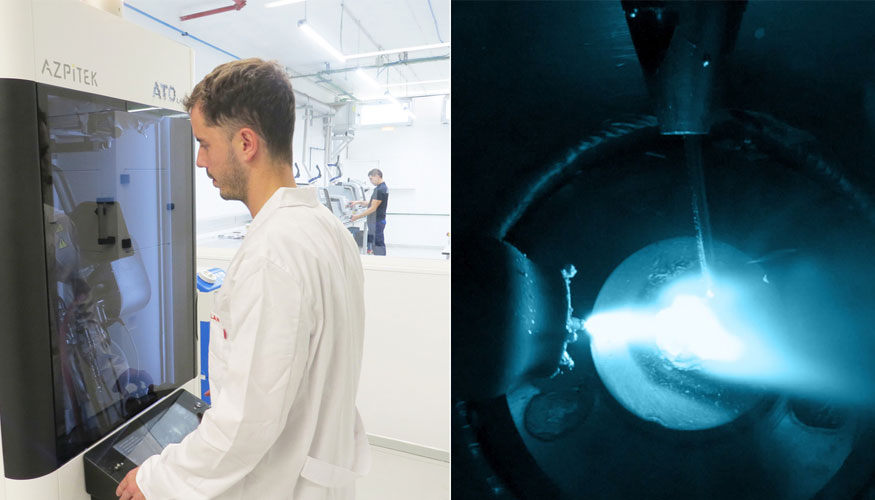
Una vez terminado el proceso de diseño y fabricación del polvo de compensación, la última fase consiste en realizar el proceso de L-DED en los parámetros optimizados, esta vez, añadiendo una mezcla de polvos entre el 316 (90%) y el polvo de compensación (10%) como se muestra en la imagen 5.
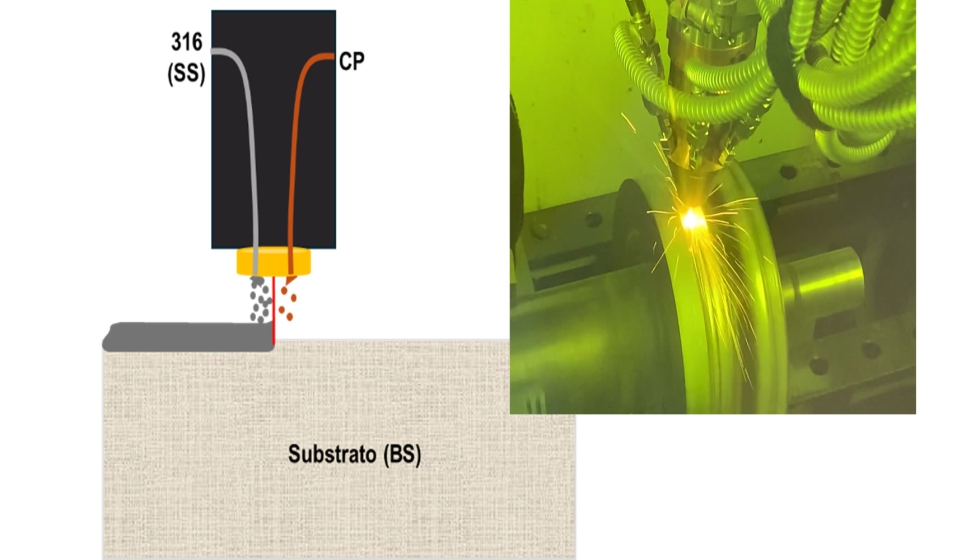
Como conclusión, se puede afirmar que el proceso desarrollado es válido para contrarrestar el efecto de dilución que se da en la fabricación L-DED; además, este mismo proceso puede ser empleado para ajustar la composición química de recargues a la composición deseada, más allá de la composición original del material aportado. Como alternativa a este proceso, es posible directamente fabricar un polvo de recargue con composición química ajustada para compensar el efeto de dilución, añadiendo de esta forma un solo polvo en el recargue. No obstante, compensar la dilución con la fabricación del polvo de compensación aporta mayor flexibilidad, ya que puede adecuarse a distintos grados de dilución ajustando el parámetro Z, es decir, el ratio entre el polvo de compensación y el polvo de aporte que se añade durante el proceso de L-DED. Ello permite adaptarse a distintas variaciones en los procesos de fabricación y posibilita la adaptación a distintos procesos mediante un único polvo de compensación. Se trata, por tanto, de un desarrollo con un amplio rango de aplicación.