Retos para el mecanizado mecánico de materiales compuestos de fibras destinados a la construcción ligera
Los nuevos programas de aeronáutica como el Airbus A350, el Boeing 787 o la serie C Bombardier apuestan principalmente por conjuntos de capas de plástico de fibras por carbono y titanio cuando se trata de seleccionar el material para los componentes estructurales sometidos a enormes esfuerzos. De este modo es posible evitar un peso excesivo de los componentes, la corrosión, así como una dilatación térmica de la longitud. Los componentes estructurales que principalmente están sometidos a esfuerzos tridimensionales se siguen fabricando con aluminio por motivos económicos. Esta compleja combinación de materiales también ha implicado unos laboriosos procesos de mecanizado para permitir un mecanizado y montaje económicos y seguros para el proceso. Para la unión de estos diferentes materiales incluso hoy en día sigue predominando el procedimiento de remachado. En consecuencia, es muy importante que el taladrado de todos los materiales con una mecanizabilidad muy heterogénea sea preciso, pero al mismo tiempo productivo y económico [1]. Las especificaciones de tolerancia para los taladros de agujeros remachados en la industria aeronáutica varían según su aplicación entre H7 y H10. En función de la posición de montaje del agujero remachado en el avión y por motivos de accesibilidad, es necesario utilizar diferentes máquinas-herramienta o incluso máquinas guiadas a mano. Diferentes conceptos de máquina que a su vez impliquen diferentes estabilidades y características en lo que a la amortiguación de las vibraciones se refiere.
Este artículo trata las diferentes soluciones específicas para diferentes conceptos de máquina, desde grandes máquinas Gantry hasta máquinas guiadas a mano. Además de los diferentes pares de giro, deben tenerse en cuenta también las condiciones inestables de temperatura y las fuerzas axiales [2]. Por lo tanto, el mayor reto lo supone el control de las extremas diferencias físicas de los materiales durante el mecanizado.
Fresado de materiales plásticos de fibras por carbono
Se han analizado y verificado los diferentes comportamientos físicos de los materiales durante el mecanizado de plástico de fibras por carbono, metal y sus materiales compuestos (‘stacks’). A tal fin se ha fresado y taladrado aluminio 7050, titanio TiAl6V4 y plástico de fibras por carbono (IM-M21E). El plástico de fibras por carbono empleado en la serie de ensayos que se describe a continuación, estaba formado únicamente por fibras posicionadas unidireccionalmente (capas unidireccionales en un solo sentido). El punto de partida teórico desarrollado para el mecanizado mecánico de plástico de fibras por carbono se ha verificado mediante experimentos en base a estas placas unidireccionales. La foto 1 muestra el resultado y describe las diferencias fundamentales entre el mecanizado de metal y el de plástico de fibras por carbono (ver la foto 1).
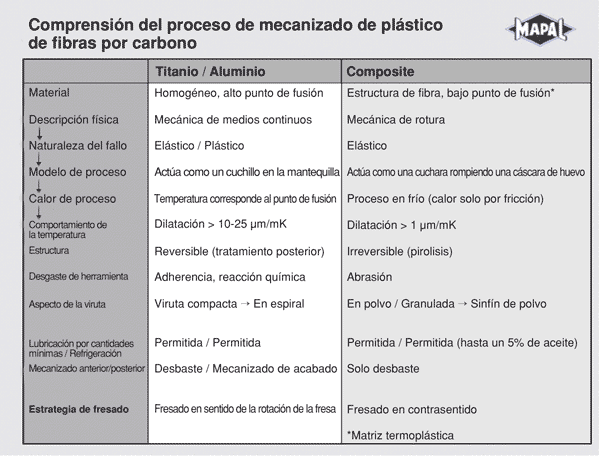
Aproximadamente en el 9% de los mecanizados se ha utilizado la combinación de taladrado y fresado en forma de fresado circular u orbital [3]. En estos casos se han podido aprovechar las ventajas del fresado en cuanto a fuerzas axiales y mínima formación de rebabas para el taladrado.
Los metales muestran un comportamiento homogéneo, tienen habitualmente una alta resistencia térmica y carecen de estructuras de fibra de diferente resistencia y dureza. Los materiales plásticos de fibras por carbono tienen unas características completamente diferentes. Los metales fallan elástica o plásticamente. En cambio, los compuestos se rompen de forma elástica y frágil, lo que también puede calcularse físicamente. Mientras que el mecanizado por arranque de viruta de los metales se puede describir con la fórmula de la mecánica continua, los compuestos fallan por rotura. Los compuestos se deforman y se rompen como espaguetis secos y fallan según las reglas de la mecánica de rotura.
Durante el mecanizado mecánico de metales se genera un calor en la zona de cizallamiento primaria cuya temperatura corresponde aproximadamente a la temperatura de fusión. En caso de rotura de un material plástico de fibras por carbono, tan solo se genera calor muy reducido. La conocida generación de calor durante el mecanizado por arranque de viruta del plástico de fibras por carbono es provocada principalmente por la fricción. El motivo radica en que el granulado de la rotura del plástico de fibras por carbono se debe eliminar siguiendo un procedimiento diferente al que se emplea para las virutas de metal que, en comparación, son bastante más grandes o más largas.
Además, la estructura de los metales es reversible y puede ser reproducida o reciclada todas las veces que se quiera. Gracias a un tratamiento posterior mecánico o térmico, es posible modificar la estructura física del borde de la superficie para adaptar la misma a las futuras exigencias frente al componente. Por el contrario, los compuestos no son reversibles. No hay vuelta atrás cuando la superficie está dañada [4]. Es por ello que los compuestos están predestinados para los mecanizados de inyección, hecho muy importante a favor del mecanizado económico de los materiales plásticos de fibras por carbono (ver apartado Taladrado de materiales plásticos de fibras por carbono).
La estrategia de mecanizado más apropiada para el fresado de plástico de fibras por carbono es el fresado en contrasentido. En el mecanizado de metal se utiliza por defecto el fresado en sentido de la rotación de la fresa. La foto 2 muestra que desde el punto de vista del desarrollo de fisuras, la evacuación de atasco y el efecto de la temperatura, el fresado en contrasentido resulta más ventajoso para el mecanizado de plástico de fibras por carbono que el fresado en sentido de la rotación de la fresa. En caso del fresado en sentido de la rotación de la fresa, la fisura generada transcurre verticalmente por la superficie. De forma similar a la hendidura de madera, en el fresado en contrasentido la fisura se desarrolla en el sentido del avance por lo que apoya la abrasión de material.
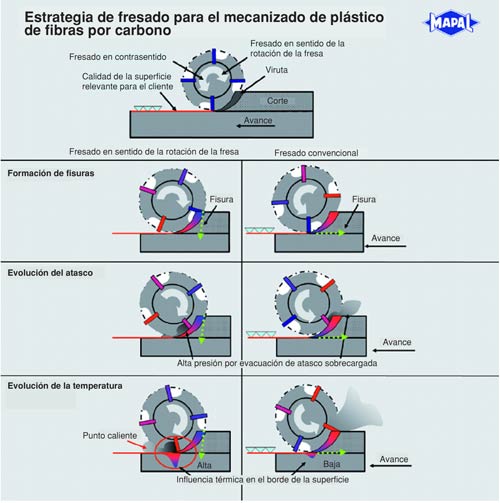
En caso del fresado en sentido de la rotación de la fresa con elevados volúmenes de arranque de viruta, el polvo a presión se introduce en el borde de la superficie recién generada en cuanto se excede la evacuación de atasco. De este modo, el avance queda limitado durante el fresado en sentido de la rotación de la fresa. En cambio, en el fresado en contrasentido puede eliminarse el polvo fácilmente en el lado opuesto.
Durante el fresado en sentido de la rotación de la fresa, la temperatura en los cantos cortantes alcanza un máximo absoluto que además se produce en el punto en el que se genera la superficie del componente. En este sentido existe el riesgo de que el canto cortante exceda la temperatura de pirólisis del plástico de fibras por carbono. Por el contrario, durante el fresado en contrasentido puede refrigerarse el canto cortante por lo que el mismo trabaja con la mínima temperatura de proceso posible.
Esta teoría se ha afirmado gracias a diferentes series de pruebas realizadas en ensayos y en aplicaciones de los clientes [5]. Asimismo, se han obtenido los siguientes conocimientos en lo que al mecanizado de plástico de fibras por carbono se refiere:
- Las ranuras de las herramientas deben ser lo suficientemente grandes como para prevenir la rotura de la herramienta debido a una sobrecarga en caso de avances elevados.
- Además de la estrategia apropiada, es posible aumentar el avance mediante un mayor número de dientes. Este sentido, se exige que la máquina tenga suficiente estabilidad y rigidez.
Además de unas geometrías de herramienta adecuadas y recubrimientos con diamante CVD, el mecanizado en húmedo supone una alternativa frecuente para contrastar la generación de calor. Es por ello que debe darse preferencia a los lubricantes refrigerantes no engrasantes.
Taladrado de materiales plásticos de fibras por carbono
Los modelos de proceso resultan adecuados para dividir un hecho complejo y discutir con mayor facilidad cada una de sus partes. Conocidos tecnólogos apoyan con sus conocimientos análogos estos procesos y los describen de forma aritmética. En este sentido, por ejemplo, el ángulo de punta del taladro de plástico de fibras por carbono sigue siendo el foco de las pruebas exhaustivas. El siguiente modelo muestra que, por lo general, debe darse preferencia a un pequeño ángulo de punta para el taladrado de compuestos.
La foto 3 muestra la vista lateral de dos taladros con un diferente ángulo de punta en la última capa de plástico de fibras por carbono, directamente delante de la salida del taladro. Para ello se ha idealizado la superficie de plástico de fibras por carbono mediante una capa con tres subcapas unidireccionales. Cada capa se describe por medio de un roving (mecha) que incluye aproximadamente 25.000 fibras. La parte de fibras y volumen (proporción de fibras y resina) dentro de los rovings es varias veces superior a la de entre los rovings. Entre los rovings se encuentra únicamente el material de matriz con una resistencia claramente inferior. Bajo el esfuerzo producido por el ángulo de punta del taladro se realiza una rotura a lo largo de esta capa de matriz con una baja proporción de fibras [6].
Cuando el taladro se acerca a la última capa, en función del ángulo de punta se genera una tensión de flexión en el roving. Cuanto mayor es ángulo de punta, se produce más carga de superficie y, por lo tanto, más fuerza de extensión y un mayor par de reacción en los lados del roving. Al aumentar la fuerza de extensión en el roving, se generan una fisura y el par de reacción la delaminación. Si se utiliza un ángulo de punta más pequeño, se reduce el par de reacción y el riesgo de la delaminación.
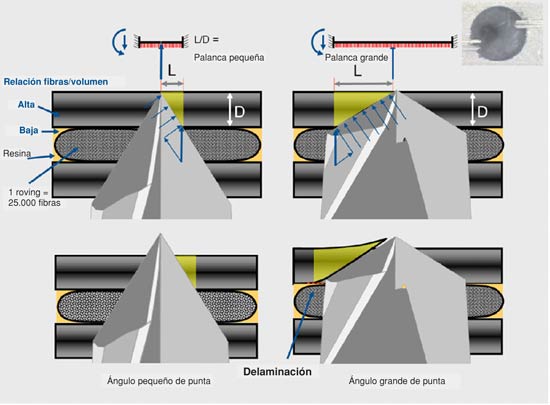
Taladrado de stacks de titanio de aluminio y plástico de fibras por carbono
En el taladrado macizo, no son las fuerzas en la punta de la broca, sino las temperaturas en los cantos de la misma las que hacen que se formen rebabas. La temperatura máxima se alcanza en la punta de la broca [7]. La onda de calor delante de la broca se va acumulando en la salida del taladro y ablanda el material. La presión axial es entonces suficiente para deformar plásticamente el metal ablandado y formar la rebaba.
Estos modelos utilizados para describir los fundamentos de mecanizado por arranque de viruta de metal y compuestos, así como las ventajas resultantes han podido ser confirmados repetidamente en diferentes series de ensayos prácticos. Las brocas que tienen en cuenta estos conocimientos no muestran ningún tipo de problema con respecto a la delaminación y salientes de fibras y alcanzan una formación de rebabas muy reducida [8].
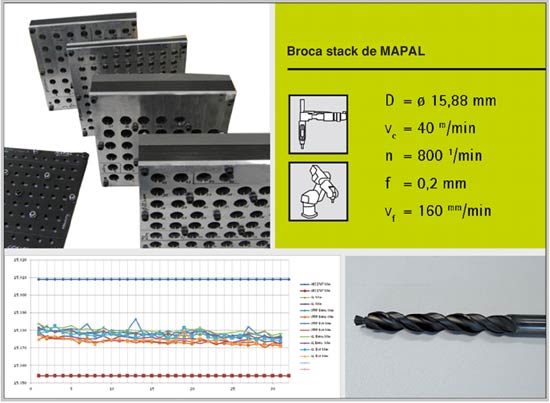
El taladrado de plástico de fibras por carbono o metales requiere unas geometrías de herramienta configuradas de forma completamente diferente. Los compromisos en base a estas configuraciones como, por ejemplo, valores medios o intermedios resultan ser insuficientes para el mecanizado de compuestos como el titanio de plástico de fibras por carbono o el aluminio de plástico de fibras por carbono. Se recomienda concentrarse en los estándares de calidad críticos que varían según el punto de vista. Por lo general no supone ningún problema si el taladro se introduce en plástico de fibras por carbono o en metal. En cambio, al sacar el taladro pueden producirse salientes de fibras en el plástico de fibras por carbono o formarse rebabas en el metal. La geometría de broca es capaz de evitar tanto la delaminación como la formación de rebabas.
Al taladrar stacks de titanio de plástico de fibras por carbono debe tenerse en cuenta no solo la formación de rebabas, sino también la evacuación de viruta en lo que a la configuración de la herramienta se refiere. Al sacar el taladro, en ningún caso deben quedar virutas adheridas a la sensible superficie de plástico de fibras por carbono. Por lo tanto, como la ranura de viruta se ha configurado claramente con un tamaño más grande que el de la viruta, se evita que se produzcan rasguños en el material compuesto. Si la viruta se queda atascada en la ranura en la zona de plástico de fibras por carbono, se produce una fricción extrema y se calientan tanto el componente como la herramienta. Consecuencia de ello son profundos rasguños en el plástico de fibras por carbono y una mayor formación de rebabas.
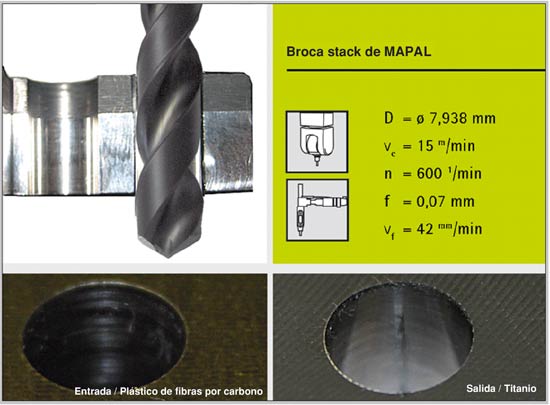
Habitualmente el taladro se introduce en el material plástico de fibras por carbono y a continuación se taladra el titanio. Para este caso es posible optimizar la geometría de broca con respecto a la formación de virutas y rebabas [9]. Los mejores resultados se han obtenido con una refrigeración de alta presión y herramientas remachadas en recto (ver la foto 5). Por el contrario, con MMS o incluso con mecanizados en seco a bajas velocidades y elevados avances, al ser un estándar para las instalaciones semiautomáticas, las herramientas remachadas en espiral obtienen unos mejores resultados en lo que a la generación y evacuación de viruta se refiere. A fin de conseguir una vida útil optimizada de la herramienta, así como un rendimiento óptimo del proceso, deben adaptarse las condiciones de mecanizado a las exigencias del material de la pieza de trabajo en cuestión. Para reducir el tamaño de viruta, se ha comprobado con éxito la estrategia de avance intermitente (pecking / hiccup). Gracias a la nueva geometría de broca de Mapal, puede realizarse esta interrupción del avance, sin resultar estrictamente necesaria.
Otra posibilidad para aumentar la vida útil y la eficiencia es el empleo de recubrimientos con diamante PKD o CVD. En este sentido, no deben excederse las velocidades máximas de corte de 30 m/min [10]. De lo contrario, el diamante reaccionaría con el titanio y se convertiría en TiC [11].
Herramientas óptimas para cualquier concepto de máquina
Las máquinas-herramienta grandes tienen una estabilidad máxima y propiedades amortiguadoras. No obstante, a lo largo del casco del avión las piezas grandes de los componentes están fuera del alcance de las máquinas-herramienta. Aquí se utilizan las unidades de avance de taladrado que se enclavan en un dispositivo como puede ser, por ejemplo, un cierre de bayoneta. Estas máquinas semiautomáticas están equipadas con unos casquillos fabricados a medida para el guiado de la broca. Esta guía ayuda a evitar vibraciones en la herramienta al entrar en el componente. De este modo es posible utilizar incluso herramientas muy largas. Incluso con PCD pueden obtenerse calidades H8 con una sola operación.
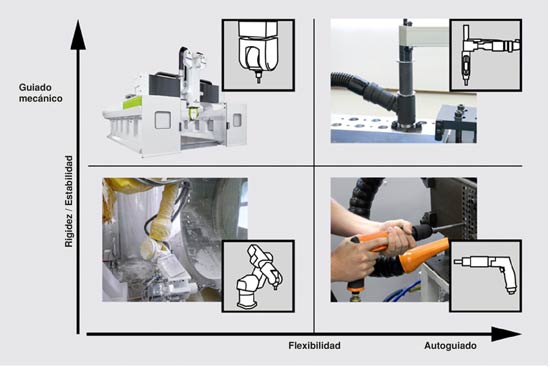
Para el taladrado macizo por medio de robots se utilizan unos efectores especiales con casquillo de pisón de presión. En caso del mecanizado con el efector final de robot no existen casquillos de guía que puedan impedir la trayectoria de la broca durante el inicio de corte. Por lo tanto, es necesario que la herramienta disponga de sus propias estrategias de guía, estabilización y amortiguación. Así esta tecnología permite realizar taladros de muy alta calidad incluso con un robot. También en este caso es posible realizar incluso taladros H8 en una sola operación.
Las zonas más críticas en el momento de realizar los agujeros remachados son las accesibles solo con la mano. A tal fin se utilizan pequeñas máquinas guiadas a mano. En estos casos, la posición del taladro queda definida por los orificios pretaladrados en las cuadernas que se han realizado durante el mecanizado de las mismas en el centro de mecanizado. Esto quiere decir que en un primer paso este taladro sirve de ayuda para el posicionamiento y como casquillo de guía para el taladrado inicial. En un segundo paso se abre el orificio taladrando y se realiza el escariado para obtener la calidad y el tamaño finales. En un tercer paso se realiza el avellanado. Estas máquinas no ofrecen ninguna estabilidad ni amortiguación, más bien todo lo contrario. Tal y como se ha mencionado anteriormente, también en este caso es necesario que las herramientas tengan sus propias características de guía, estabilización y amortiguación. A pesar de ello, la tecnología de mecanizado permite un taladrado de muy alta calidad.
En todos los posibles conceptos de máquina es necesario que los costes por cada taladro se encuentren en un nivel equiparable. Las tecnologías de herramienta descritas aquí permiten que incluso las herramientas con recubrimiento de PCD o CVD puedan cumplir estos criterios.
El procedimiento descrito aquí con estos modelos de proceso permite desarrollar soluciones específicas para el cliente de forma rápida y con un mínimo trabajo de ensayo. Además, el número de consultas durante la fase de cualificación y especialmente durante la FAI (first article inspection o inspección del primer artículo) es muy reducido. La localización de fallos durante la producción de serie resulta menos problemática cuando las personas involucradas pueden comprender la relación entre la causa y el efecto en el mecanizado de compuestos.
La gama de productos de herramientas de Mapal está disponible en todo el mundo y puede utilizarse para los más diversos conceptos de máquina. Las herramientas especiales de Mapal pueden emplearse especialmente para el taladrado y fresado de materiales plásticos de fibras por carbono y sus compuestos de materiales como titanio y plástico de fibras por carbono o aluminio y plástico de fibras por carbono.
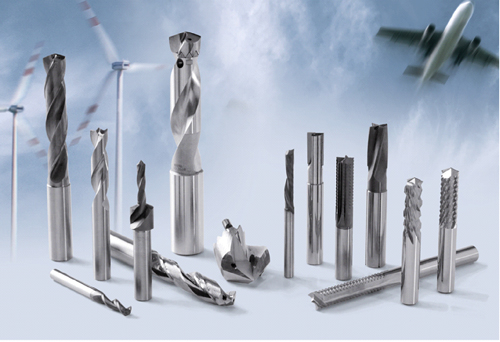
Referencias:
[1] HINTZE, W.: Wirtschaftliche Zerspanung von Leichtbaustrukturen durch den Einsatz innovativer Hartmetallschneidstoffe und Diamantbeschichtungen. In: Laser Focus. März 1982, S. 49-54.
[2] STÖVER, E.: Untersuchungen zum Bohren des Faser-Metall-Laminates Glare sowie von Glare-Schichtstrukturen. In: Dissertationsmanuskript TU Hamburg-Harburg, Institut für Produktionsmanagement und –technik, Hamburg 2006.
[3] FANGMANN, S., ET AL.: Orbitalbohren geschlossener Strukturteile erfordert optimierte Werkzeuge In: Maschinenmarkt 06/07-2007.
[4] WACHINGER, G., THUM, C., SCHEID, P.: CFRP Repair Methods. Hannover, Neue Fertigungstechnologien in der Luft-und Raumfahrt, IFW 19/20.11.2008
[5] RICHTER, J., MÜLLER-HUMMEL, P.: Bearbeitung von CFRP-Bauteilen im Flugzeugbau. Schmalkalden, Schmalkalder Werkzeugtagung 2008.
[6] MATTHEWS, F. L., DAVIES, G. A. O., HITCHINGS, D., SOUTIS, C., Finite Element Modelling of Composite Materials. Woodhead Publishing Limited, Cambridge, England, 2000.
[7] MIN, S.; DORNFELD, D.; KIM, J.; AND SHYU, B.: Finite Element Modeling of Burr Formation in Metal Cutting. Proc. 4th CIRP Int’l Workshop on Modelling of Machining Operations, Delft, August, 2001, pp.
[8] MÜLLER-HUMMEL, P.; RICHTER, J.; MÖLLER, B.: Neue Werkstoffe fordern neue Allianzen; Werkstatt und Betrieb, Carl Hanser Verlag, München WB 10/2008.
[9] VIJAYARAGHAVAN, A.; DORNFELD, D.: Challenges in Modelling Machining of Multilayer Materials. Proc. of 8th CIRP Int’l Workshop on Modelling of Machining Operations”, pp 17-24, 2005.
[10] MÜLLER-HUMMEL, P.; LAHRES, M.: Infrared Temperature Measurement on Diamond-Coated Tools during Machining. In: Bachmann, P. K.; Bruckley-Golder, I.M.; Glass, I. T.; Kamo, M.: Proc. of 4th European Conference on Diamond, Diamond-like and Related Materials; Albufeira, Portugal, Elsevier Sequoia S.A., Lausanne, SSDI 0925-9635(93)05111-0, S.: 765, 1993.
[11] MÜLLER-HUMMEL, P.; LAHRES, M.: A New Instrument to optimize cutting Processes: In Situ Temperature Measurement on Diamond-coated Tools. In: Innovations in Material Research, World Scientific Publishing 1996, Vol. 1, No. 1, S.: 1-9, 1996.