Husky desarrolla un sistema innovador para tapas bisagra
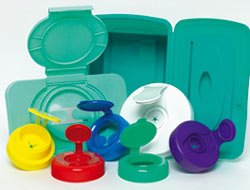
En el mercado norteamericano solo, hay más de 100 marcas de toallitas húmedas desechables diferentes, para uso doméstico, para automóvil y para higiene personal. El grupo de consultores New England Consulting calcula que el mercado americano de la toallita húmeda desechable está valorado en 2.000 millones de dólares, con una previsión de ventas de 4.500 millones de dólares para 2010.
Husky ha desarrollado un enfoque único para el moldeo de tapas de contenedores para toallitas húmedas desechables con cierre articulado o de bisagra que, comparado con los sistemas convencionales, puede significar un aumento del 10 por cien al 15 por cien de la producción y una disminución del 15 por cien al 25 por cien del espacio ocupado en planta.
La mayoría de las tapas articuladas son moldeadas por inyección y son evacuadas por caída libre o son retiradas por un robot. Las tapas son entonces cerradas fuera del área de la prensa, mediante una máquina que realiza el cierre. Aunque estos métodos funcionan, no proporcionan a los transformadores la ventaja competitiva que necesitan —la caída libre puede dañar o contaminar las piezas y puede incidir en el tiempo de funcionamiento productivo de la máquina debido a posibles atascos en la máquina que realiza el cierre. Por otra parte, la utilización de robots para la evacuación de piezas aumenta el tiempo de ciclo general, la ocupación de espacio en planta y el coste.
Los sistemas SwingChutes usan una leva o un eje motor servo accionado que gira y posiciona un brazo de evacuación justo delante de la pieza a expulsar, a la apertura del molde. Las ventosas de succión por vacío dispuestas en el extremo del brazo de evacuación tienen por función coger la pieza expulsada de forma segura. Cuando el molde se cierra, el tapón queda plegado y la pieza es colocada en una guía de evacuación montada en el lateral del molde. Un cilindro neumático cierra el tapón antes de que la pieza salga del área de moldeo. Desde la guía de evacuación, las piezas pueden ser fácilmente encaminadas hacia otros procesos de producción.
“El cierre de la tapa articulada mientras la prensa se está cerrando nos permite mejorar mucho la fiabilidad y el tiempo de ciclo del sistema”, afirma Bruce Catoen, vicepresidente de los sistemas automatizados de Husky. “Hemos modificado los sistemas SwingChutes para incorporar una función de cierre de las tapas. El mecanismo de cierre simplifica la automatización y elimina la necesidad de equipos de manipulación de producto posteriores. El resultado es un ahorro sustancial de inversión y de espacio ocupado en planta.”
Los sistemas SwingChutes pueden ser incorporados en una amplia gama de aplicaciones diversas, incluyendo tapones, contenedores y carcasas.
“Los sistemas SwingChutes ofrecen una evacuación más rápida de la pieza que el sistema de caída libre o de robot, sin ocupar un valioso espacio en planta”, añade Catoen. “Gracias a la introducción de un sistema SwingChute, hemos conseguido reducir de más de un 20% el tiempo de ciclo de un cliente que utiliza un sistema 2x8 cavidades para cierres articulados.”
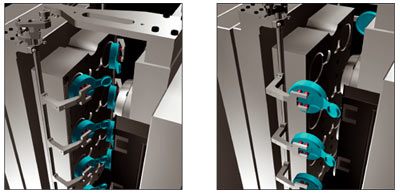
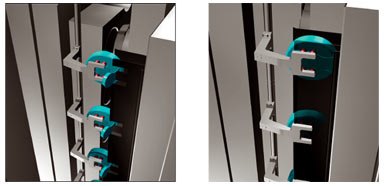