Seguridad e higiene en la industria del envase plástico
4 de marzo de 2010
El reglamento entiende como ‘buenas prácticas de fabricación’: “todo aspecto de aseguramiento de calidad que garantiza que los materiales y objetos se producen y controlan de forma coherente, para asegurarse de que sean conformes a las normas aplicables y a los estándares de calidad adecuados para el uso previsto y no pongan en peligro la salud humana o causen un cambio inaceptable en la composición de los alimentos o un deterioro de sus características organolépticas”.
¿A qué empresas afecta el reglamento?
El campo de aplicación del reglamento abarca a las empresas que fabrican, procesan o distribuyen materiales que van a estar en contacto con los alimentos, incluyendo todos los sectores posibles: plásticos, materiales y objetos activos e inteligentes, vidrio, metales y aleaciones, papel y cartón, cerámica, corcho, caucho, siliconas, adhesivos, tintas de imprenta, resinas de intercambio iónico, celulosa regenerada, productos textiles, barnices y revestimientos, ceras y madera, siempre que todos éstos vayan a estar durante algún periodo de su vida en contacto con algún producto alimentario.
¿Qué tiene que cumplir una empresa para el cumplimiento del reglamento (CE) 2023/2006?
Principalmente, la empresa debe establecer y aplicar un ‘Sistema de Control y Aseguramiento de la Calidad’ eficaz y documentado, y a su vez garantizar su cumplimiento. Como se observa en el párrafo anterior se definen dos cualidades que debe cumplir dicho sistema de control y aseguramiento de calidad. Una de ellas consiste en que el reglamento pide que el sistema de control y aseguramiento de calidad sea eficaz, de forma que las empresas garanticen que los materiales y objetos acabados satisfagan las normas de seguridad alimentaria aplicables.
Otra de las cualidades que debe tener dicho sistema es que esté documentado, comprometiendo a la empresa a mantener documentos y registros que demuestren la eficacia del mismo.
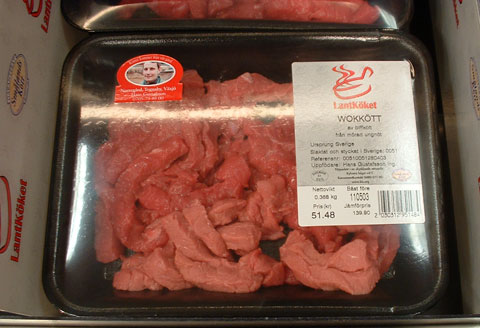
¿Cómo establece y aplica una empresa un sistema de control y aseguramiento de la calidad?
El reglamento no especifica la metodología que se debe llevar a cabo para su cumplimiento. Por este motivo, el cumplimiento va a depender de la decisión de la empresa y de la estrategia que decida llevar a cabo para su cumplimiento. Actualmente existen dos opciones: una consiste en establecer un sistema de control y aseguramiento de calidad propio y la otra opción es implantar alguno de los protocolos normalizados que existen ya adaptados a la industria del envase alimentario.
Desde la experiencia de Aimplas, y después de las auditorías realizadas sobre diversas empresas del sector, se puede decir que la primera opción es la más costosa para la empresa en cuanto a establecer los requisitos que debe cumplir, pero a su vez tiene ciertas ventajas. La ventaja principal que nos encontramos reside en que una vez implantado, suele ser un sistema mejor adaptado y menos estricto que los modelos existentes.
La segunda opción que puede elegir una empresa es implantar uno de los protocolos existentes en el mercado, como es el caso del Protocolo BRC/IoP (British Retail Consortium/ Institute of Packaging), la norma UNE-EN ISO 22000:2005 o la norma UNE-EN 15593. La ventaja principal de la implantación de uno de estos protocolos es que están definidos los puntos a cumplir, por lo que resulta más fácil la implantación y posterior auditoría. Además, son protocolos reconocidos por el sector, lo que puede llevar asociado una reducción en el número de auditorías por parte de los clientes. No obstante, su implantación lleva asociados ciertos costes externos además de ser muy exigentes en las medidas que contemplan, muy por encima de lo que exige el reglamento 2023/2006.
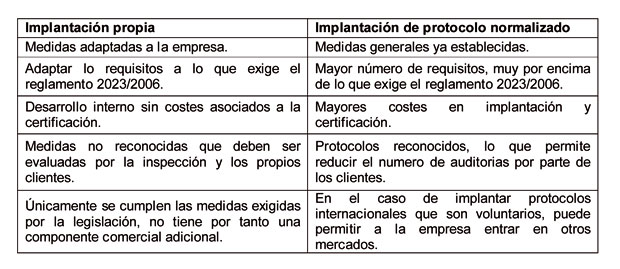
¿Qué debe contemplar un sistema de control y aseguramiento de la calidad para ser eficaz?
Un sistema de control y aseguramiento de la calidad debe contener varios aspectos para ser eficaz. Los campos sobre los que se deben marcar requisitos para mantener un sistema de calidad adecuado son varios.
Como primera premisa, el sistema debe identificar y documentar todos los procesos que se vean involucrados con la calidad e higiene del producto final. Además, el sistema debe tener como uno de los pilares fundamentales la implantación de un APPCC (Análisis de Peligros y Puntos Críticos de Control). Un APPCC ayuda a la empresa a identificar sistemáticamente todos los peligros que pueden afectar a la seguridad e higiene de los futuros alimentos que van a entrar en contacto con los materiales, estableciendo e implantando mecanismos para controlar que no sobrepasen los límites críticos, asociados a cada uno de los puntos críticos establecidos a lo largo de todo el proceso de producción y distribución de envases alimentarios.
Otro apartado que tiene que contemplar un sistema de control y aseguramiento de la calidad es el referente a unos requisitos que aseguren que las instalaciones de la empresa se mantengan con un nivel de higiene que asegure la calidad del producto final.
Por último, un buen sistema de control y aseguramiento de la calidad debe contemplar en su estructura una serie de requisitos referentes al personal, donde se definan la concienciación y formación que aseguren que el personal implicado en los procesos de fabricación y distribución de los productos es consciente de la importancia de la higiene en la cadena alimentaria.
¿Qué tipo de puntos críticos nos encontramos en la industria del plástico?
El punto crítico común en los materiales plásticos en contacto con alimentos, es sin duda, el control de la migración global y específica. Los envases plásticos por sus características pueden sufrir procesos de interacción, tanto con el alimento como con el medio que los rodea. Uno de estos procesos es la migración. La migración es el proceso por el que sustancias contenidas en el plástico pueden pasar al alimento que contienen. El control de la migración global, está enfocado a verificar la inercia del material y el control de la migración específica para descartar los problemas de toxicidad asociados a una sustancia concreta. Los materiales plásticos en función del alimento a contener y de las condiciones de uso, tiempo y temperatura de contacto, deberán ser evaluados según su migración.
No obstante, también existen otros puntos críticos de control específicos dependiendo de la industria. Uno de ellos, que además viene reflejado en el Anexo I del reglamento (CE) 2023/2006, es el que afecta al uso de las tintas de impresión de los materiales. Según este Anexo las empresas usuarias deben comprobar que las tintas no están en contacto directo con el alimento, así como asegurar que están completamente secas para evitar que existan componentes libres que puedan pasar al alimento.
Otro caso concreto es el que ocurre en las empresas fabricantes de botellas de PET para envasar alimentos. Un paso previo a la obtención de la botella, es la obtención de la preforma de PET. La preforma es un producto semielaborado que se obtiene por inyección y que es previo al soplado final de la botella. En este proceso de inyección el PET puede producir acetaldehído. El acetaldehído es una sustancia autorizada en materiales plásticos en contacto con alimentos con un límite de migración específica de 6 ppm, sin embargo, por debajo de este límite esta sustancia puede producir problemas organolépticos de olor y sabor en el alimento, por lo que su control es de vital importancia.
Por otra parte, en la obtención de estructuras multicapa en film plástico, es habitual el uso de adhesivos en base a poliuretanos para unir diferentes capas de plástico, estos adhesivos pueden producir aminas aromáticas primarias (AAPs) como consecuencia de la reacción de uno de los componentes del adhesivo, en concreto el isocianato, con el agua. Las AAPs están reguladas según la legislación vigente con un límite de contenido total de 10 ppb. Las AAPs son sustancias que van desapareciendo con el tiempo, pero es necesario que en el momento del envasado estén ya por debajo del límite establecido, sino es posible que migren al producto que contienen. En este caso concreto, es necesario un control de estas sustancias para evitar este problema.
Como resumen, las empresas deben tener mecanismos de control en los puntos críticos de su proceso. Estos mecanismos serán particulares del proceso productivo de cada empresa.