Una rodilla de repuesto para todo el mundo
7 de julio de 2009
Se ha convertido, por tanto, en un desafío para la industria proveer a los pacientes de productos de alta calidad a un precio asequible que puedan mejorar efectivamente la calidad de vida.
El proyecto europeo Custom-Fit aceptó el reto mediante la consecución de un nuevo paradigma de fabricación capaz de generar productos totalmente personalizados a un precio asequible. En líneas generales, el proceso Custom-Fit empieza con la captura de las características geométricas del paciente utilizando MRI (resonancia magnética) y escáneres CT (tomografía computerizada). Un programa de CAD (diseño asistido por ordenador) especializado adapta el diseño de un implante estándar a los rasgos individuales del paciente, teniendo en cuenta además otra información adicional requerida para personalizar el implante, tales como la distribución de carga específica del paciente. Finalmente, la parte personalizada se elabora con las nuevas técnicas aditivas (Rapid Manufacturing) desarrolladas, perfectamente aptas para la fabricación de productos exclusivos.
En la actualidad, el campo de aplicación de los productos Custom-Fit es bastante amplio, no solamente para aplicaciones médicas sino también para productos de consumo. El proyecto utilizó diversos casos de estudio además del implante de rodilla: un implante mandibular y una prótesis transfemoral, en el ámbito de aplicación médico, y otros productos de consumo inusuales donde la customización ha demostrado aportar valor añadido, como los casos de motoristas y los asientos de moto.
Réplica exacta
En el caso de sustitución de rodilla se diseña un componente específico: el plato base tibial, una parte de metal que reemplaza la parte superior final del hueso de la tibia (ver Imagen 1).
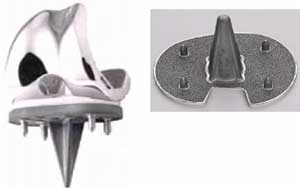
El perfecto ajuste geométrico de esta parte del hueso de la tibia mejora la estabilidad del paciente. Ésta se obtiene con una herramienta de diseño apropiada (desarrollada por el socio del Custom-Fit Delcam) la cual automáticamente cuestiona el escáner CT en 3D de la tibia del paciente, aporta el corte quirúrgico más apropiado del hueso y diseña el plato base tibial que mejor se ajusta a la sección del hueso.
La tecnología Custom-Fit permite igualmente la fabricación de un plato de metal con material graduado, optimizado para soportar las cargas específicas de la rodilla en función del paciente. Esto es posible gracias a una nueva tecnología de ‘rapid manufacturing’ denominada MPP (proceso de impresión en metal, desarrollada por el socio del Custom-Fit Sintef), la cual es capaz de realizar una parte graduada mezclando Ti y Co-Cr. Por motivos de biocompatibilidad, es preferible tener titanio en la parte del plato vueltas hacia la tibia, en tanto en cuanto la aleación cobalto-cromo en la parte opuesta garantiza su resistencia.
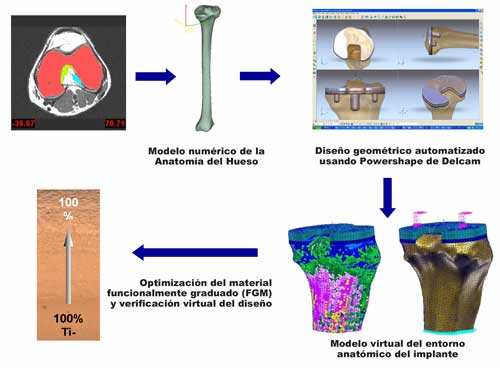
Todavía queda un largo camino antes de su aplicación real sobre un paciente, pero los resultados del diseño y las pruebas fabricadas son muy prometedores. La aproximación Custom-Fit parece ser la solución adecuada para realizar los implantes de rodilla del futuro.