Es una herramienta muy útil y versátil para las empresas moldistas y transformadoras del plástico
La termografía en la industria del plástico
Alrededor de 1880 Samuel P. Langley inventó el primer detector de radiación infrarroja (bolómetro) que captaba la radiación por el aumento de temperatura producido en un cuerpo absorbente de calor. En la década de los 80 aparecieron los microbolómetros, que actualmente se emplean como detectores en cámaras termográficas.
Todos los objetos que tenga una temperatura superior al cero absoluto (0 Kelvin ó -273,15 °C), emiten ondas en la banda infrarroja. Al aumentar la temperatura de un objeto, éste emite más energía a menor longitud de onda. La radiación infrarroja, la luz visible y la luz ultravioleta son formas de energía en el espectro electromagnético que difieren en la longitud de onda.
En la figura 1 se pueden observar las diferentes formas de energía en el espectro electromagnético:
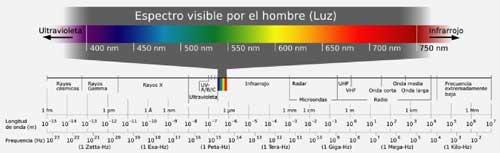
Las cámaras termográficas
Como hemos podido observar en la figura 1, el ojo humano solo puede ver un pequeño rango de longitudes de onda (desde 0,4 a 0,75 µm), en cambio las cámaras termográficas pueden detectar la energía infrarroja imperceptible para el ojo humano. El rango normal de temperaturas que las cámaras pueden registrar va desde -20 hasta 500 °C, y puede extenderse hasta -40 °C por debajo y hasta 2.000 °C por arriba. La cámara transforma la energía infrarroja en una imagen con un mapa de colores que nos muestra la temperatura del objeto en cada punto. Esto las hace muy versátiles y con infinidad de aplicaciones tanto en el sector de los plásticos como en el resto de sectores.
Uno de los parámetros más importantes a la hora de realizar una medición de temperatura con una cámara termográfica es la emisividad. La emisividad nos indica la capacidad que tiene un objeto de emitir radiación infrarroja. Esta capacidad se puede medir y sus valores van desde 0 para los materiales que no emiten nada hasta 1 para el cuerpo negro. Existen numerosas variables que afectan a la emisividad de un objeto, como la longitud de onda, el campo de visión, la forma geométrica y la temperatura.
En la figura 2 se puede ver una tabla con los valores de emisividad de algunos materiales:
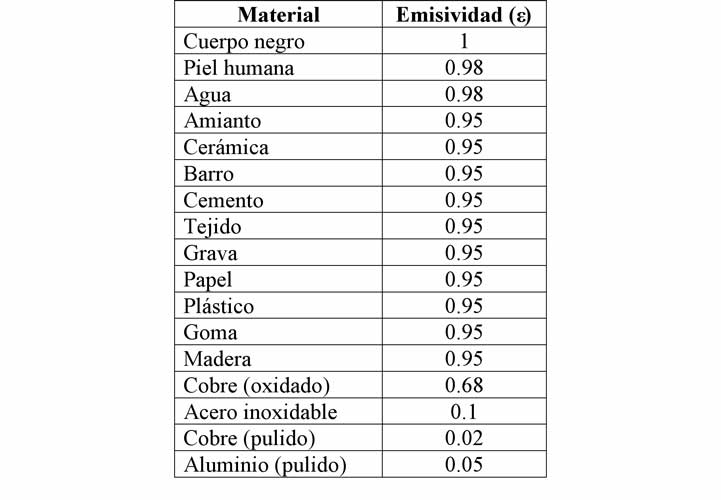
Si se requiere una elevada precisión en la medición de la temperatura de un objeto, necesitaremos introducir el valor de la emisividad de dicho objeto en la cámara termográfica o en el software de análisis. Éstos ya tienen los algoritmos necesarios para corregir los valores de la temperatura en función de la emisividad.
Aplicaciones en la industria del plástico
La termografía infrarroja es una técnica que se puede emplear en la industria del plástico para la optimización de procesos y mejora de la calidad, así como en el desarrollo de nuevos utillajes.
En el proceso de inyección de termoplásticos, mediante imágenes termográficas sobre piezas recién inyectadas aún en el molde o recién extraídas, o sobre la propia superficie del molde, se puede obtener una amplia información del proceso de transformación:
• Desviaciones de temperatura en puntos críticos (puntos de inyección, insertos, zonas más gruesas de la pieza, etc.).
• Detección de puntos calientes causados por la fricción del material termoplástico en alguna zona del molde.
• Efectividad del control de temperatura.
• Efectividad del sistema de atemperación del molde.
• Distribución del calor apropiada, tanto en la pieza como en el molde.
• Estudiar la evolución de la temperatura en la superficie del molde hasta que se estabiliza el proceso.
• Optimización de tiempos de enfriamiento.
• Validación de los resultados obtenidos con programas de simulación.
Como caso práctico, para ver las posibilidades que nos ofrece la termografía, en Aiju se realizó un estudio termográfico del proceso de inyección sobre el molde de un caballito de juguete.
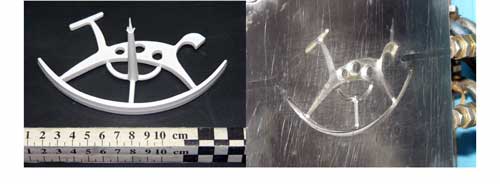
Como se puede ver en la figura 3, el molde es de una cavidad con el sistema de alimentación por colada fría con tres puntos de entrada en la pieza. Las pruebas se han realizado en una máquina Demag Ergotech de 110 t, con un equipo de atemperación Wittmann.
En la figuras 4, 5 y 6 se puede observar como varía la temperatura superficial de las piezas obtenidas en función del tiempo de enfriamiento establecido. En las imágenes se aprecia que las zonas más anchas de la pieza, tienen una temperatura más elevada que el resto. En función del material empleado y las condiciones de inyección se puede determinar el tiempo de enfriamiento necesario para poder desmoldear la pieza sin dificultad, validar el sistema de refrigeración del molde y determinar la causa de algunos problemas en las piezas como alabeos o rechupes. En este caso práctico se ha estudiado la influencia del tiempo de enfriamiento para optimizar las condiciones de proceso, pero se puede hacer un estudio similar para otras variables como son la temperatura de la masa, temperatura del molde, velocidad de inyección (cizallamiento del material), etc.
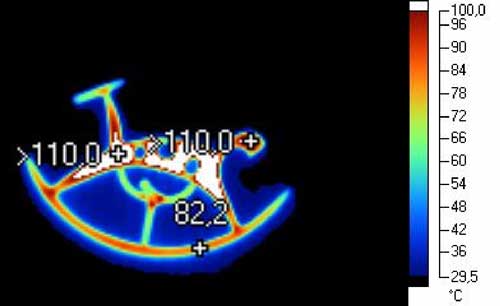
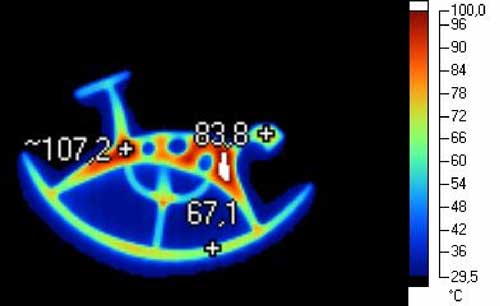
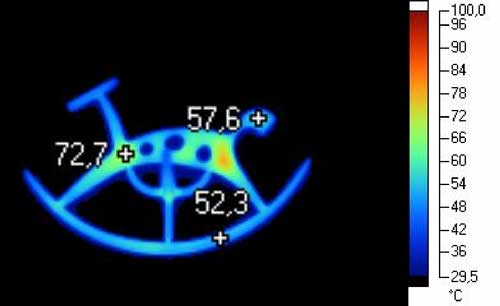
En la figura 7 podemos observar la evolución de la temperatura superficial del molde tras varios ciclos de inyección, de modo que se puede determinar el tiempo que tarda el molde en estabilizarse y por lo tanto en obtener piezas con las mismas propiedades, aspecto fundamental en piezas técnicas con elevados requisitos de calidad.
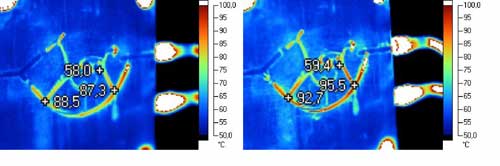
La termografía puede ser una herramienta muy útil y versátil para las empresas moldistas y transformadoras del plástico, ya que permite obtener una amplia información sobre el comportamiento del binomio molde- material, y por lo tanto la optimización del proceso. En este sentido, Aiju está colaborando estrechamente en diversos proyectos de I+D con empresas interesadas del sector.