Nuevas tecnologías de inyección para la fabricación de piezas grandes
19 de mayo de 2009
Vamos a comentar dos temas relacionados con lo mencionado: la utilización de materiales compuestos de madera y termoplásticos, y el moldeo con ayuda de vapor para aplicaciones concretas.
Moldeo por inyección de compuesto de madera y plástico
La mezcla de madera y plástico (WPC), disfruta ya de una reputación en el campo de la extrusión. Actualmente está llegando también al sector de la inyección. Muchos transformadores tienen una cierta resistencia a experimentar con este tipo de materiales y aquellos que lo han efectuado han encontrado una serie de obstáculos tales como la calidad no constante, problemas de aprovisionamiento, etc. y en general, mayores dificultades en el empleo de estos materiales con respecto a los termoplásticos habituales.
Sin embargo, recientes desarrollos en estos compuestos, han mejorado significativamente la calidad, consistencia y capacidad de este material ecológico. Las últimas generaciones de WPC pueden ser procesadas con ajustes mínimos en el proceso, sin modificar el equipo de la máquina.
Los WPC pueden producirse con diversos tipos de resina, tales como polietileno, polipropileno y poliestireno. Los WPC son solo una de las categorías de materiales emergentes que pueden ser denominados como ‘biocomposites termoplásticos’. Además de la madera, estos composites pueden utilizar otras fibras naturales como la corteza del arroz, descartes de fibra de palma, e incluso lino. Las condiciones de transformación a las que vamos a referirnos, se concretan a la mezcla madera/PP, pero los principios pueden aplicarse en líneas generales a los restantes biocomposites termoplásticos.
¿Porque utilizar los biocomposites?
Existen muchas razones para utilizar biocomposites para la producción de diversos productos. Siendo su contenido de fibras naturales superiores al 50%, ofrecen a los transformadores una opción mas ecológica con respeto a los polímeros derivados del petróleo. Además del ‘factor verde’, los biocomposites reducen el riesgo para el transformador respecto al aumento del precio del petróleo, requieren menos energía para la fabricación y proporcionan productos con una óptima rigidez estructural, un agradable acabado estético y un importante atractivo para el mercado.
Los biocomposotes madera/termoplástico tienden a disfrutar de un menor paso con respecto a las resinas no cargadas o con fibra de vidrio. Son competitivos en términos de coste, características mecánicas y desarrollo del proceso con respecto al PP con carga de talco o de carbonato cálcico. Tiene además la ventaja de una menor densidad, que reduce su coste efectivo y pueden ser ventajosos en los costes de transporte debido a su ligereza. Su aplicación es posible en el sector del automóvil, construcción, juguetes, y otros productos de consumo.
Buenos candidatos para la utilización de estos materiales son las piezas con paredes gruesas y aquellas que necesitan una óptima rigidez y estabilidad dimensional. Si bien resultan muy apropiados para piezas con paredes gruesas, los transformadores pueden utilizarlos también para paredes mas finas, aumentando la proporción del termoplástico en la mezcla.
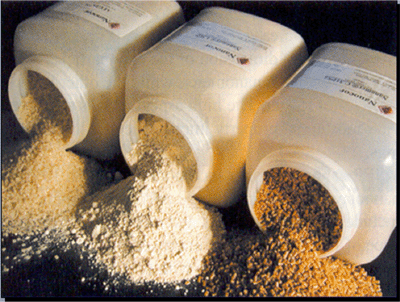
Nota: este artículo está basado en la presentación del trabajo que Negri Bossi presentó en las jornadas de innovación que el CEP organizó en la pasada edición de Equiplast.
Para asegurar la calidad del producto acabado, es necesario el uso de termoplásticos de alta calidad de la granza. Existen dos aspectos a los que hay que dedicar especial atención:
- La humedad: la humedad superficial debe ser inferior al 1,5%, mientras que en el interior no debe sobrepasarse el 1%. Un grado de humedad no controlado aumenta la fragilidad del producto terminado.
- La calidad de la granza: la granza debe ser limpia y uniforme en sus dimensiones y forma. No debe haber residuos de polvo, que es una responsabilidad del fabricante del compound.
Por medio de la variación de los porcentajes de los componentes de la mezcla, se pueden variar las características del material, por ejemplo mejorando la resistencia al desgaste de los parachoques aumentando el porcentaje de plástico o mejorar la rigidez aumentando el porcentaje de madera.
Cuando se moldea con la temperatura justa, velocidad y flujos bien distribuidos, las piezas de WPC presentan colores uniformes y una buena dispersión de la fibra, mínimas deformaciones, superficies pulidas y ninguna evidencia de rechupados. Los dos factores mas importantes para la inyección de este material son el calentamiento y las tensiones excesivas.
En un principio se puede pensar que la fibra de madera puede actuar como un inhibidor del flujo, y sin embargo es todo lo contrario. La mezcla de madera/PP fluye con facilidad con baja velocidad y presión (igual que el PP con carga mineral). Como resultado tenemos un menor consumo energético. Se pueden obtener mejoras de productividad por un menor tiempo de ciclo por un llenado y enfriamiento mas rápidos.
Las temperaturas habituales del cilindro van de 170 a 190 °C en la parte posterior, 180-200 en la parte central y 200-210 en la zona de la boquilla.
La presión depende de la geometría de la pieza, así como de los canales y puntos de inyección. Habitualmente se requiere una presión inferior a la de los materiales tradicionales.
La velocidad de llenado requiere una atención especial ya que, si bien es cierto que el material fluye fácilmente, es importante evitar tiempos de llenado muy bajos porque el material es sensible al stress. El calentamiento causado por una velocidad excesiva de llenado pueden causar posibles defectos superficiales. Se eliminan fácilmente estos defectos disminuyendo la velocidad de inyección.
Dadas las bajas temperaturas empleadas, el tiempo de presión posterior es inferior al de los materiales habituales.
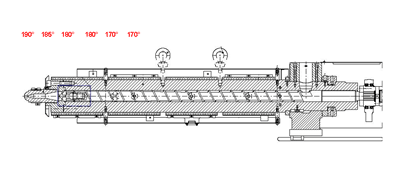
La boquilla debe tener un orificio de salida con una dimensión lo mas parecido posible al diámetro de la colada.
Las piezas fabricadas con WPC presentan una finura de acabado homogéneo y un color marrón claro. Con este tipo de acabado es muy fácil proceder a su barnizado o pintura.
Resultan apropiadas las máquinas de inyección estándar para este tipo de transformación, si bien son necesarias algunas precauciones. Es crítico el control del grado de humedad y no tener un calentamiento excesivo.
Las recomendaciones para transformar este material y evitar un exceso de stress, son:
- El husillo debe tener una sección de compresión larga u un laminación corta.
- Una puntera con mezclador puede romper la fibra. Se recomienda el uso de husillos de tres zonas, con relación L/D entre 20 y 24 y una relación de compresión de 2:1 a 2,5:1.
- Mantener bajas las revoluciones del husillo. Debe preverse un cilindro con una capacidad de 3-4 inyectadas.
- Inyectar a baja velocidad.
- Evitar obturadores en el molde y punteras con válvula en el husillo.
- Prever el mayor número posible de puntos de inyección y con dimensiones n inferiores a 2,5 mm.
- Emplear una baja contrapresión.
- Mantener una temperatura interna del cilindro inferior a los 200 °C. El material debe ser calentado preferentemente por conducción y no por fricción.
- Usar boquillas con el orificio igual al diámetro de la colada.
- Proyectar coladas con canales lo mas grandes posibles, para poder tener bajas velocidades de inyección.
- Atención a los canales calientes: pueden causar un calentamiento excesivo de la fibra.
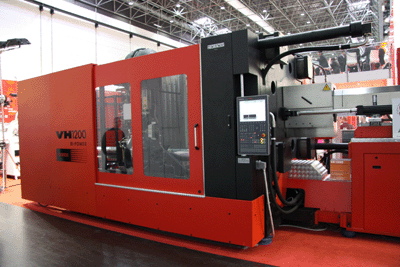
Moldes
Los moldes deben tener canales amplios de distribución del material con mínimas obstrucciones para evitar tensiones en el material. Los puntos de inyección deben ser los más dimensionados. Los puntos de inyección inapropiados producen decoloraciones y ráfagas en las piezas. Preferiblemente los puntos de inyección deben estar situados en las paredes gruesas de la pieza. En caso de espesores finos, el punto de inyección debe ser como mínimo 2/3 del espesor de la pared. Deben estar posicionados de forma que no haya zonas de unión de flujo o soldadura en zonas sujetas a esfuerzos, ya que podrían resultar mas frágiles.
Moldeo con vapor
La colaboración con un importante transformador plástico, nos ha permitido desarrollar en dos años este tipo de tecnología y hacer que pueda ser utilizada en un elenco importante de máquinas.
Si bien no se trata de una novedad absoluta, esta técnica de moldeo es todavía poco conocida y encuentra su aplicación especial en las carcasas para televisores.
Sustancialmente se trata de calentar algunas partes del molde con una inyección de vapor a una temperatura próxima a los 180 °C, utilizando canales RHCM, para pasar inmediatamente de la fase de llenado a un brusco enfriamiento de esas mismas partes.
El resultado es un brillo muy particular, con efecto espejo de la superficie en PC/ABS y con la total eliminación de las antiestéticas líneas de unión.. La incidencia sobre el ciclo de la inyectora varia entre el 10% al 30% en función de la geometría de la pieza.
Esta tecnología está suplantando en la fabricación de muebles de TV, a la fase de acabado y pintura, con evidentes ventajas tanto en coste como de impacto medioambiental.
El vapor está suministrado por dos potentes equipos capaces de generar respectivamente 1600 y 2000 kcal/h, mientras que el sistema de control (en las máquinas Negri Bossi), está integrado gracias a una innovadora solución.
Gracias a la colaboración con ese transformador, se ha desarrollado un nuevo software de gestión para las electroválvulas de mando que permiten reemplazar completamente las voluminosas centralinas actualmente situadas al lado de la inyectora.