La fabricación rápida en aplicaciones médicas
El uso de tecnologías de ‘rapid manufacturing’ en el entorno médico ha demostrado ser desde sus inicios de gran utilidad. La necesidad de generar piezas exclusivas basadas en los datos del paciente, su alto coste y complejidad, la necesidad de imágenes para un correcto diagnostico y su idoneidad para la diagnosis autónoma de los médicos han contribuido a ello. En el proceso, se llevaron a cabo dos estudios cuyo diagrama de flujo común se detalla en la figura 1. El presente artículo explica los pasos seguidos para un implante de mandíbula.
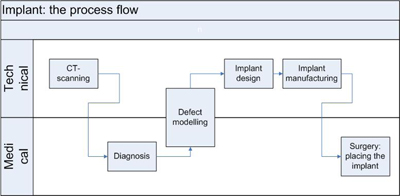
Figura 1: Diagrafma del flujo del Proceso
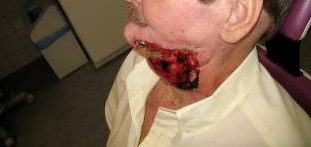
Para realizar un diagnóstico exhaustivo, se escaneó al paciente a través de tomografía computerizada (CT). La figura 3 muestra las imágenes de la mandíbula empleando el software Mimics, basado en imágenes CT. El objetivo era obtener una imagen digitalizada del hueso dañado.
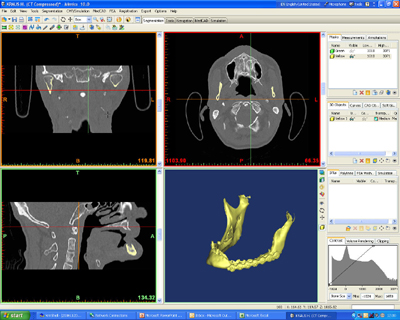
Se acometió el aspecto geométrico del problema para realizar una planificación detallada de la intervención. En el caso de la mandíbula, las imágenes demuestran claramente la infección del hueso. Con esta visualización, el cirujano planificaría el corte de la mandíbula. La imagen digital se usó para diseñar las dos guías de corte que se ajustasen perfectamente a la mandíbula (vea la figura 4).
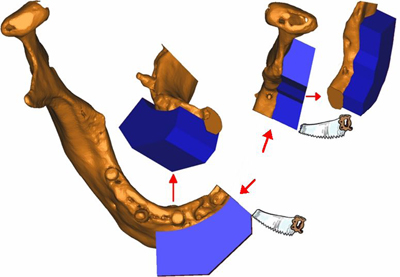
Los implantes se fabricaron con un material relativamente flexible, de forma que se pudiesen ajustar si en el desarrollo de la operación así se requiriese. Puesto que la programación pudo realizarse en el momento con una precisión controlada, fue posible diseñar implantes personalizados en base al defecto mostrado en la imagen digitalizada y la programación del cirujano (figura 5). Puesto que suele transcurrir un tiempo considerable desde el escaneo a la propia cirugía, se dejó una considerable holgura en el diseño para compensar la posibilidad de que se precisase eliminar mayor cantidad de hueso.
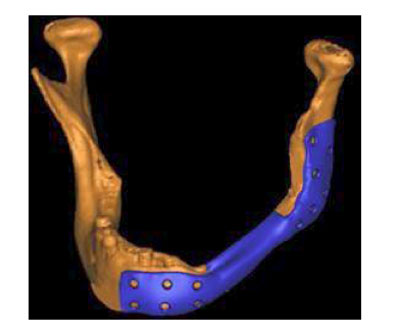
El propio diseño del implante demanda trabajar de forma fácil con los datos escaneados. Los modelos resultantes de Mimics son modelos transferidos a un fichero de lenguaje estándar de triangulación (STL) que requieren ser convertidos en modelos en tres dimensiones, lo cual es un proceso lento y difícil. Para evitar dicho problema el diseño se realizó utilizando el software 3Matic, que plasma el diseño del modelo directamente en ficheros STL. Los resultados obtenidos han demostrado que el diseño habitual en CAD del implante mandibular tarda 3 veces más que el diseño en 3Matic. Para su fabricación, los materiales de los implantes requieren cumplir estrictamente las regulaciones médicas. En el presente, el material más comúnmente utilizado para implantes es el titanio. Este no es el material fácil de procesar ni tampoco el más económico. El implante mandibular fue inicialmente realizado utilizando una fresadora común (ver Figura 6) cuyos requerimientos de procesado puede comprometer el diseño y genera deshechos. Paralelamente, fue creado un modelo de la mandíbula en ABS utilizando tecnologías de RM para realizar la cirugía (Figura 7).
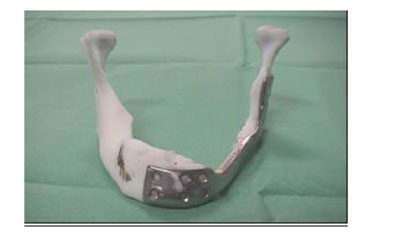
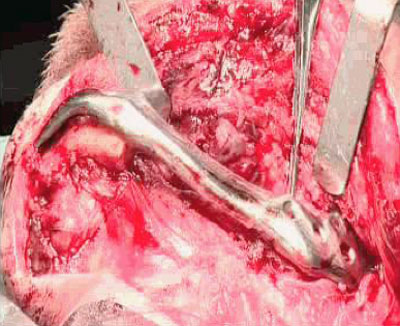
Esta nueva técnica podrá mejorar la vida del paciente. Las sorpresas potenciales durante la operación son menores debido a la precisión de la metodología y el tiempo de recuperación puede reducirse significativamente. Los tiempos de planificación, diseño y fabricación se reducen considerablemente. Finalmente, los implantes estudiados tienen mejores propiedades mecánicas e integran otros elementos anatómicos como las venas y los nervios. El objetivo ahora es mejorar la precisión de los escáneres de CT y el desarrollo de materiales para que sean tanto bio-compatibles como bio-absorbentes. En el futuro, debería ser posible perfeccionar los materiales de tal modo que se realicen de forma específica para el paciente y puedan ser reemplazados por hueso natural después de un período de tiempo.