Mecanizado de un componente TIP ‘rib’ del ala de una aeronave no tripulada mediante refrigeración criogénica
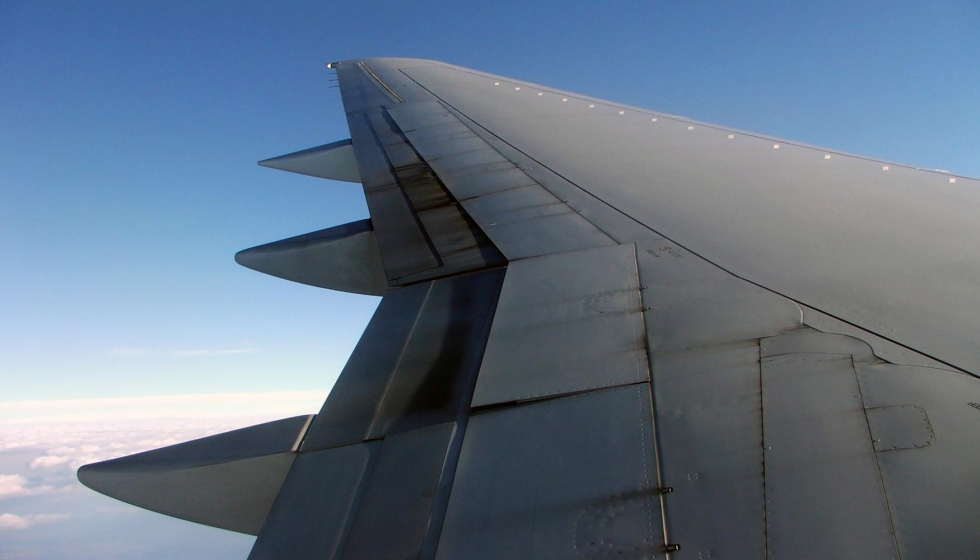
En este trabajo se presenta la metodología utilizada para la fabricación de un componente tipo ‘rib’ (costilla) del ala de una aeronave no tripulada mediante refrigeración criogénica y rigidización de sus paredes mediante el uso de sulfato de calcio. Para ello se ha utilizado aluminio 7075 debido a que, frente a otro tipo de aleaciones de la misma índole, presenta una resistencia a la rotura y corrosión mejorada que satisface las necesidades de uso durante su vida útil. En este caso, se ha portado por utilizar dióxido de carbono líquido (CO2) como fluido de corte con el fin de no eliminar el sulfato de calcio durante el mecanizado y a su vez aumentar la higiene industrial de los procesos de mecanizado. Cabe destacar que el CO2 utilizado es un gas capturado de un proceso primario, es decir, se le da un segundo uso antes de ser enviado a la atmósfera. Por tanto, se mantiene la inocuidad medioambiental inherente a la refrigeración criogénica convencional con LN2. Además, con la tecnología de refrigeración se busca también controlar exhaustivamente la temperatura de corte de tal modo que se logre aumentar la velocidad de corte sin exceder los 300 °C —temperatura en la cual el cobalto presente en las herramientas de metal duro reacciona químicamente con el aluminio provocando el embotamiento de ésta—. De este modo, no sólo se logra eliminar el uso de taladrinas durante el mecanizado sino aumentar la productividad del proceso manteniendo o incluso mejorando la integridad superficial de la pieza.
1. Introducción
El mecanizado de componentes estructurales en el sector de la aeronáutica es uno de los retos que ha sido motivo de diversos estudios en la última década. Este tipo de piezas tienen la característica de ser monolíticas con el fin de ser lo más homogéneas posible. Consecuentemente, para su fabricación generalmente se parte de un bloque en bruto al que se le fresa el 95% del material. Además, de este modo se evita la utilización de remaches u otro tipo de elementos de ensamblaje para su fabricación.
Por otra parte, un factor a tener en cuenta de este tipo de componentes son los diseños debido a que generalmente implican paredes y suelos finos a modo de nervios que les confieran rigidez. Esto se traduce en desbastes con altas tasas de eliminación de material donde las zonas menos rígidas presentan problemas causados por los efectos estáticos y dinámicos derivados del mecanizado. Concretamente, el error por flexión estática de la pieza se traduce en geometrías finales diferentes a las deseadas apareciendo habitualmente un exceso de material o paredes y suelos de espesor variable. Por otra parte, debido a los efectos dinámicos del golpeo de los filos de la herramienta sobre la pieza se provocan vibraciones forzadas apareciendo marcas y errores dimensionales. En caso de que además esta vibración sea autoexcitada, los efectos causados por dichas vibraciones se multiplican provocando un mal acabado superficial o incluso desgarros en la pieza, no pudiéndola recuperar en los procesos de acabado. Este tipo de vibración es conocida como ‘chatter regenerativo’ y es uno de los principales fenómenos a tener en cuenta a la hora de mecanizar este tipo de componentes.
Una de las soluciones que habitualmente se dan en el fresado de este tipo de componentes para evitar las vibraciones en paredes finas es el fresado de éstas mediante escalones como el mostrado en la figura 1. Gracias a este tipo de mecanizado con pasadas superpuestas se mantiene la rigidez de la pieza pudiendo mecanizar radios de altura/espesor que oscilan entre 15:1 y 30:1 [1]. Sin embargo, aplicar esta técnica en la fabricación de componentes de vehículos aéreos no tripulados - conocidos habitualmente como ‘Unmanned aerial Vehicles’ (UAV) - se hace complicado. Esto es debido a las bajas profundidades de corte que se deberían manejar debido al escalado que sufren las dimensiones de sus componentes. Dichas profundidades de corte en algunos casos magnifican el ‘efecto tamaño’ por el cual la herramienta en vez de cortar el material lo recalca produciendo un aplastamiento sobre la superficie de la pieza mecanizada.
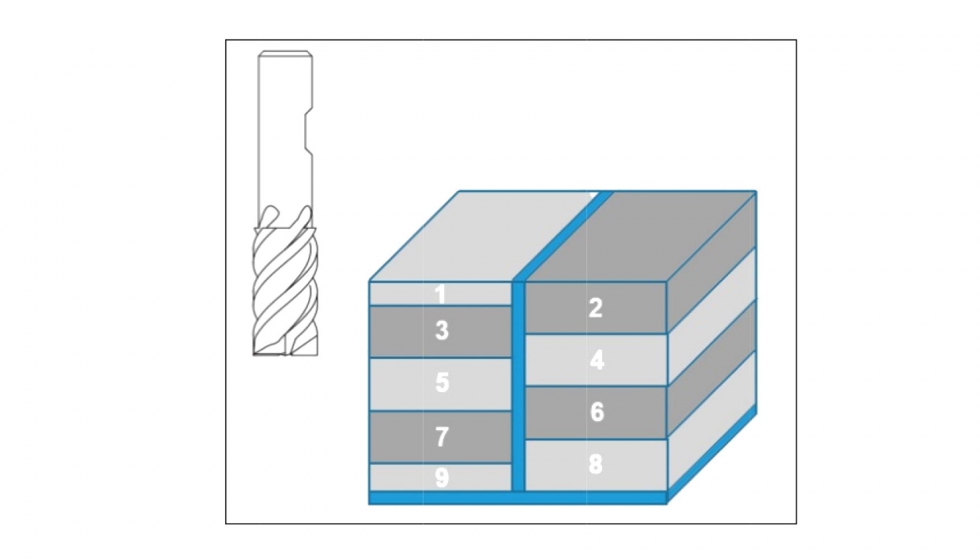
La importancia de avanzar en el mecanizado de componentes para este tipo de aeronaves es un nicho de mercado que se está abriendo debido a la demanda exponencial que está produciendo en la última década. De hecho, se prevé un impacto mundial de unos 82.000 millones de dólares [2]. Desde la UPV/ EHU son varias las alternativas prácticas que se han estudia do en los últimos años con el fin de eliminar los problemas estáticos y dinámicos durante el mecanizado de este tipo de piezas sin tener que recurrir al mecanizado de escalones [3]. En la figura 2 se resumen los estudios que se han realizado desde entonces. Cabe destacar que aunque inicialmente fueron desarrolladas para piezas del sector aeronáutico, tienen su aplicación en este tipo de componentes.
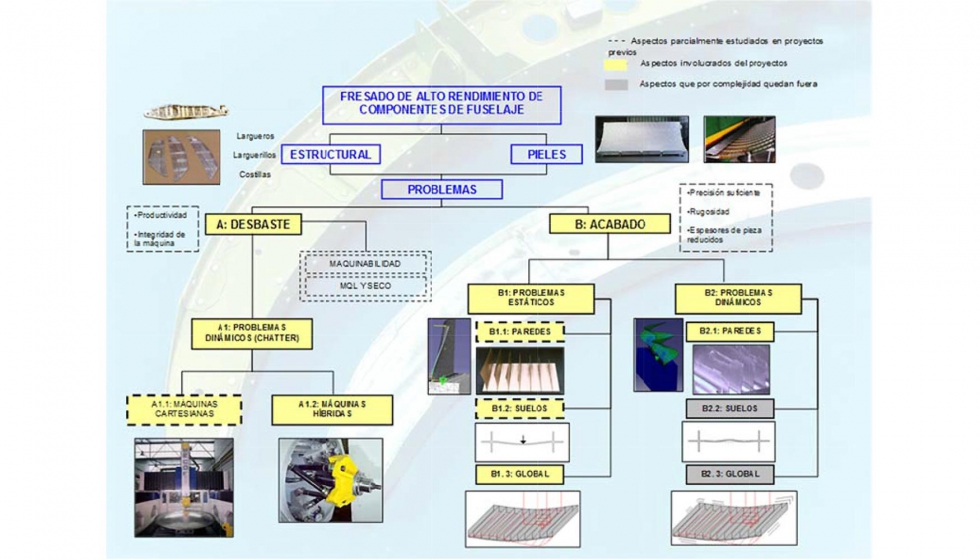
Por todo ello y con el fin de seguir avanzando en este tipo de mecanizados enfocados para componentes presentes en los UAV en este trabajo se hace un repaso de las diferentes alternativas propuestas para la eliminación de los problemas estáticos y dinámicos durante el mecanizado. Posteriormente, con el fin de aportar un caso práctico, se ha procedido a su aplicación en el mecanizado criogénico de un rib mediante la rigidización de sus paredes mediante la aplicación de sulfato de calcio.
2. Soluciones para problemas estáticos durante el mecanizado
Como se ya se ha expuesto en el apartado anterior, debido a los problemas estáticos durante el mecanizado aparecen habitualmente excesos de material o paredes y suelos de espesor variable. Este tipo de problemas surge de la flexión relativa entre la herramienta y la pieza como consecuencia de las fuerzas de corte.
Para la resolución de estos fenómenos en el caso de paredes delgadas, el planteamiento se plantea como una viga empotrada en un extremo en la cual durante su mecanizado se actúa puntualmente con la herramienta.
Consecuentemente para el caso concreto de mecanizado de componentes tipo rib para UAV se pueden aplicar tres tipos de estrategias, ya sea individualmente o de forma combinada:
La primera es la optimización de las demasías que se dejan para la finalización de las piezas. En este caso es necesario tener en cuenta que a mayor demasía, mayores fuerzas de corte. Por ello es importante alcanzar un compromiso entre ambos factores con el fin de obtener un mecanizado satisfactorio.
Otro factor a tener en cuenta es la dirección del mecanizado. Concretamente se recomienda el mecanizado en concordancia. Esto se debe a que si es realizado en oposición la componente de la fuerza de corte en dirección de la deflexión de la pared es superior a la perpendicular a ésta. Por el contrario, al mecanizar en concordancia la distribución de las componentes se invierte, razón que lleva recomendar mecanizar en esta dirección.
Por último, modificar el redondeo de las puntas de la fresa actúa favorablemente en el acabado de las paredes ya que reduce la componente normal de la fuerza de corte, trasladándose este problema a los suelos de mecanizado.
Sin embargo, a estas estrategias pensadas para paredes finas hay que sumarle la baja rigidez de todo el componente que puede inducir a deformaciones e imprecisiones dimensionales debido a las fuerzas de corte [4]. Para este tipo de problemas hay que realizar una combinación de condiciones de corte (profundidad de corte, velocidad de corte y avance) que mantengan las fuerzas de corte por debajo de dicho umbral. Esto puede ser solventado a través de un modelo de fuerzas desarrollado en [5] que estima las fuerzas de corte en función de las condiciones de corte y trayectoria de herramienta.
3. Problemas dinámicos
Durante el fresado de este tipo de paredes finas pueden aparecer vibraciones forzadas y autoexcitadas. Esto puede ser resultado de una excitación del sistema máquina-husillo-herramienta o de fenómenos dinámicos en las paredes delgadas. Por tanto, las vibraciones que se dan se pueden suponer que surgen de la excitación relativa entre la pieza y el sistema formado por la terna máquina-husillo-herramienta.
Las vibraciones forzadas se deben a la excitación producida por la frecuencia de golpeo de los dientes en la pieza. Por lo tanto, a medida que las fuerzas de corte disminuyen, lo hacen también las vibraciones forzadas. Para reducir este fenómeno, se debe tener en consideración el valor máximo de la fuerza de corte además de equilibrar cuidadosamente el montaje herramienta-husillo.
Por otra parte, las vibraciones autoexcitadas aparecen como resultado de la excitación dinámica producida por la superficie irregular periódica que genera el diente precedente de la herramienta [6,7]. La teoría clásica de chatter se plasma en la figura 3 donde se muestra un modelo de generación de chatter con 2 grados de libertad.
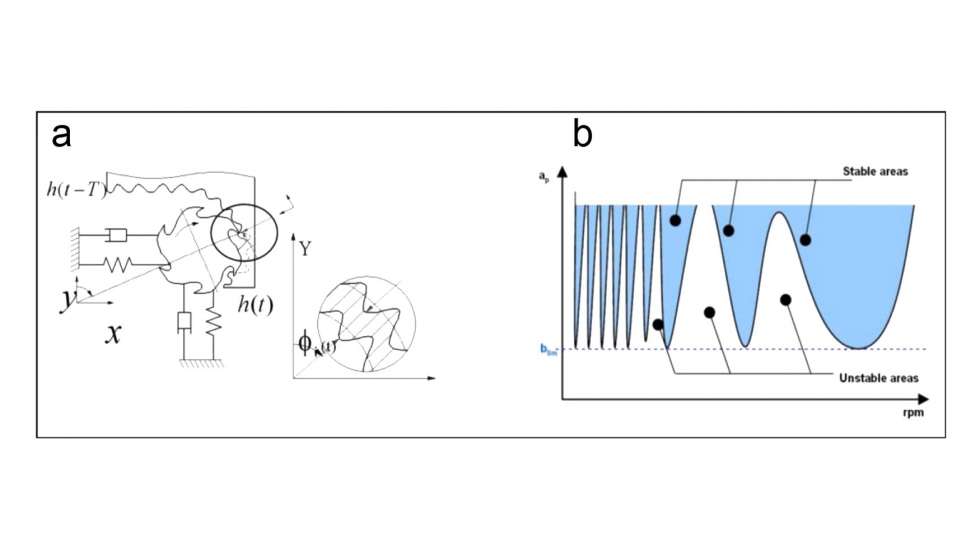
El punto de partida de este modelo se debe a la variación entre la pieza y la herramienta. Esta variación añade una componente variable a las fuerzas de corte que excitan los modos estructurales tanto de la máquina como de la pieza. En caso de que la respuesta a esta excitación no sea lo suficientemente amortiguada, se amplificará por sí misma y se generará la vibración, volviendo el mecanizado inestable.
Con el fin de evitar el chatter, se utilizan diagramas de lóbulos como el mostrado en la figura 3. Estos indican la frontera entre las condiciones de corte, estables e inestables, en función de la profundidad axial de corte, la profundidad de corte y la frecuencia de husillo. Cabe destacar que se hace necesario utilizar diferentes diagramas de lóbulos p ara cada profundidad de pasada radial, cada máquina-herramienta, cada herramienta y cada geometría y material mecanizados. Estos diagramas pueden ser calculados principalmente mediante dos métodos diferentes conocidos como el método del dominio tiempo y por el método del domino frecuencia, respectivamente [8].
De estos dos métodos, una variación del método del dominio de frecuencia es el más adecua o para lograr una estabilidad durante el mecanizado de paredes finas. Con dicha modificación se tiene en cuenta el desplazamiento relativo entre herramienta-pieza con el fin de asumir el chatter derivado del sistema máquina-husillo-herramienta. Con este método se obtiene un diagrama de lóbulos que depende únicamente de la estrategia de frenado (en concordancia y oposición). En la figura 4 se muestra una representación esquemática del proceso de fresado de paredes finas en función de si se mecaniza en concordancia u oposición.
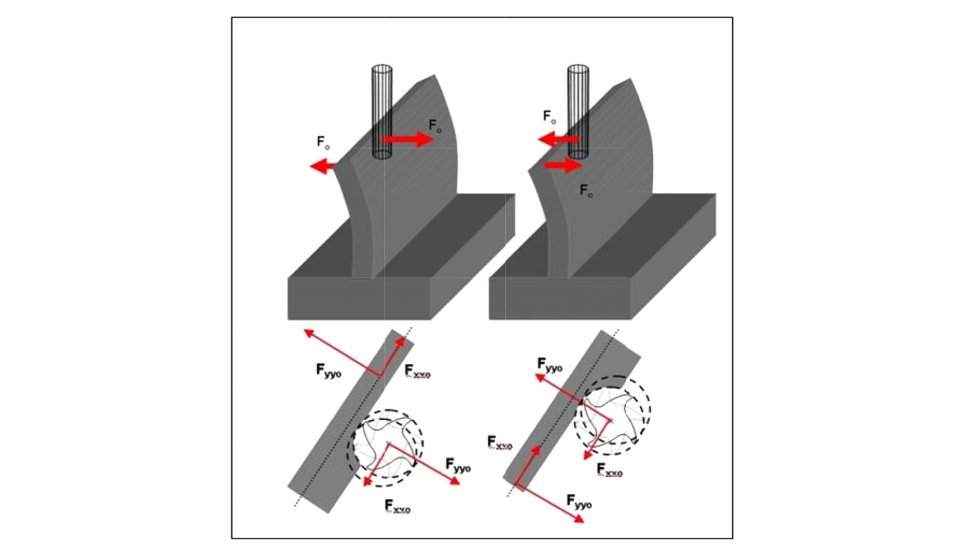
Por último, cuando el responsable del chatter es la pieza, se hace necesario un diagrama de lóbulos para cada una de etapas sucesivas debido a los cambios geométricos de ésta. Un ejemplo se muestra en la figura 5 donde se refleja un diagrama de lóbulo s discretos para las diferentes etapas de mecanizado de una pared delgada.
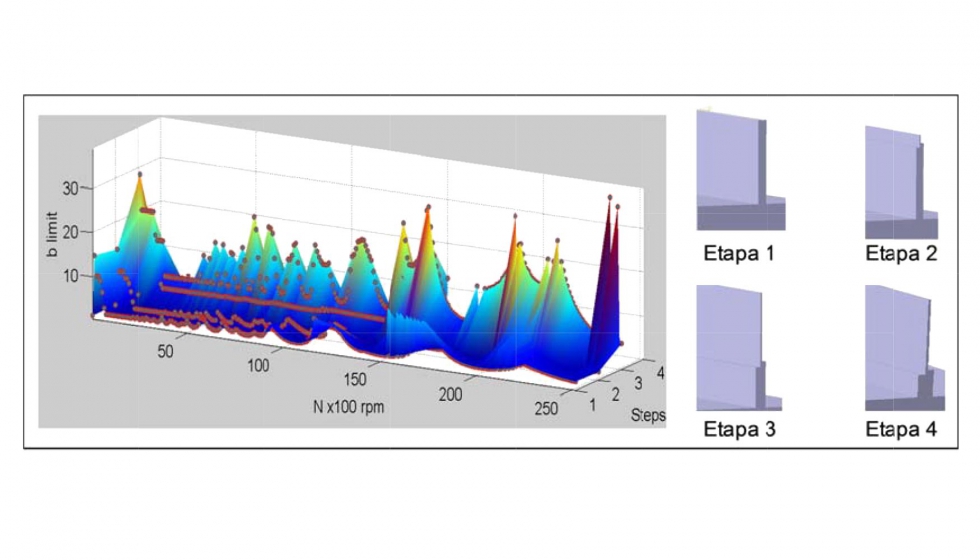
4. Mecanizado de rib para ‘unmanned aerial vehicles (UAV)
Una vez expuestos los métodos estudiados por parte del UPV/EHU hasta la fecha con el fin de resolver los problemas estáticos y dinámicos durante el mecanizado de paredes finas se ha procedido al mecanizado de un rib presentes en los UAV aplicando una nueva forma de evitar este tipo de problemáticas dado el pequeño tamaño de los componentes utilizados para la fabricación de este tipo de aeronaves no tripuladas.
En aeronáutica, se conoce como rib a las costillas estructurales presentes en las alas de las aeronaves. Éstas dan resistencia a la torsión del ala y da la forma aerodinámica de la misma. Normalmente se encuentran intercaladas de manera prácticamente perpendicular a los largueros, como se muestra en la figura 6.
![Figura 6. Esquema de rib dentro de los UA [9] Figura 6. Esquema de rib dentro de los UA [9]](https://img.interempresas.net/fotos/1566378.jpeg)
Para el mecanizado de este tipo de componentes se elimina gran volumen de material alcanzando valores cercanos al 94% presentando paredes y suelos esbeltos que dificultan su mecanizado. En el caso concreto de los UAV, además se debe tener en cuenta la reducción de las dimensiones no sólo del componente en sí sino también de las herramientas utilizadas.
Esto hace que su mecanizado presente dificultades a la hora de la obtención de la pieza final teniendo en cuenta que los problemas anteriormente descritos se magnifiquen en muchos de los casos.
En este trabajo, el material utilizado para la fabricación del rib fue aluminio 7075 utilizado habitualmente para este tipo de componentes en lo UAV. Esto es debido a que frente a otro tipo de aleaciones de la misma índole presenta una resistencia a la rotura y corrosión mucho mejor que satisfacen las necesidades de uso en este tipo de aeronaves. El diseño del rib mecanizado se muestra en la figura 7.
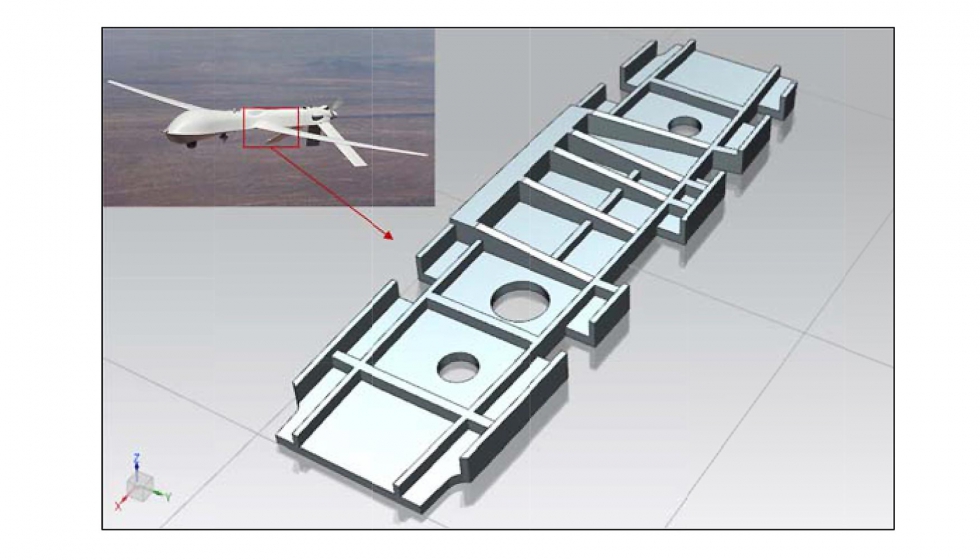
El centro de mecanizado utilizado para el mecanizado del rib fue una Kondia A6. La herramienta utilizada para el vaciado de las cajeras fue una fresa de metal duro de diámetro 4 mm con un ángulo de hélice de 45º y 4 dientes. De ido al espesor de las paredes y el tamaño de estas se ha optado por rigidizar las paredes con sulfato calcio (CaSO4) además de mecanizar en concordancia. Sin embargo, su utilización hace que se imposibilite la utilización de taladrina durante el mecanizado debido a que es fácilmente eliminable con agua. Esto hace que se haya tenido que variar la técnica de refrigeración utilizada durante el mecanizado. Por ello se ha optado por aplicar la criogenia con CO2 como técnica de refrigeración. La elección de este fluido de corte obedece además a otro tipo de razones. La primera es que debido a que el CO2 utilizado es capturado de un proceso primario, el impacto ambiental generado por el mecanizado se reduce drásticamente. Otra de las razones ha sido que su utilización implica la posibilidad de aumentar la velocidad de corte frente al uso de taladrina [10]. De hecho, las condiciones de corte utilizadas fueron: velocidad de corte de 210 m/min, avance de 0,025 mm/z, profundidad de corte axial y radial de 1 y 2 mm, respectivamente. Dichas condiciones frente a las utilizadas habitualmente en entornos industriales, su pone un incremento del 5%. Esto se debe a que el principal problema que presentan las aleaciones de aluminio durante su mecanizado es su afinidad con el cobalto que se utiliza como aglomerante en las herramienta de metal duro cuando se alcanzan temperaturas de corte por encima de los 300 °C [11]. Por otra parte, durante el mecanizado del rib se han registrado las fuerzas de corte con una mesa dinamométrica Kistler 9255 con el fin de observar la presencia de vibraciones y poder validar la utilización del sulfato de calcio como rigidizador de paredes finas. En la figura 8 se muestra un esquema del montaje realizado para el mecanizado del rib.
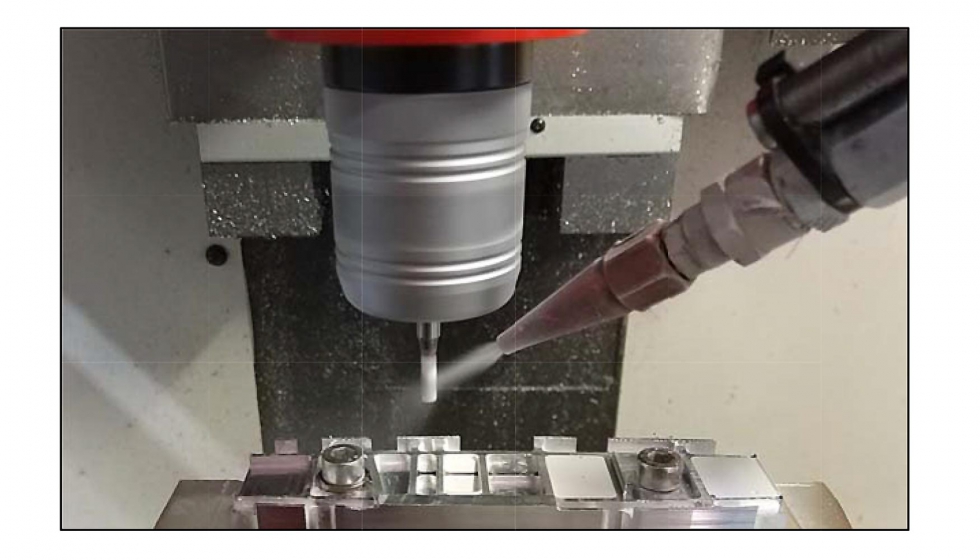
Para su mecanizado, la estrategia seguida se ha basado en el vaciado primeramente 5 cajeras para su posterior relleno con sulfato de calcio. Una vez fraguado, se ha procedido al vaciado de las cajeras restantes obteniendo un resultado satisfactorio, como se observa en la figura 9.
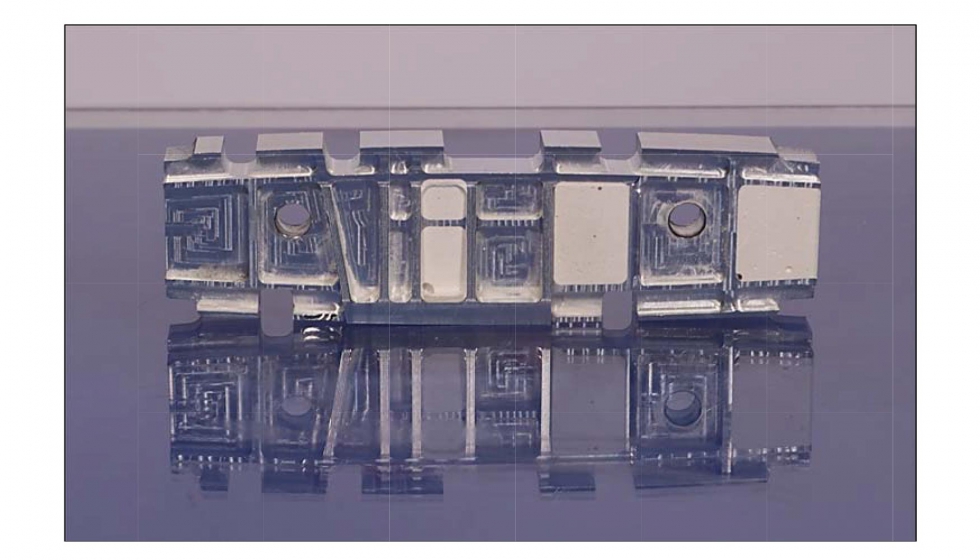
Sin embargo, gracias al registro de las fuerzas realizado se ha podido observar como la ausencia del elemento rigidizador puede inestabilizar el mecanizado del rib. En la figura 10 se muestra el valor del vector resultante de la suma de sus 3 componentes (X, Y, Z) obtenidas durante el mecanizado de dos cajeras de las cuales una de ellas tenía ambas paredes rigidizadas con sulfato de calcio (cajera 2) y la otra en cambio no (cajera 1). La comparativa de ambas muestran como el uso de sulfato cálcico como elemento rigidizador hace que se obtenga un vaciado de cajeras totalmente estable con el que poder solventar la limitación presente en el mecanizado de este tipo de paredes finas, alcanzando así un método fácilmente transferible a la industria para el mecanizado de este tipo de componentes.
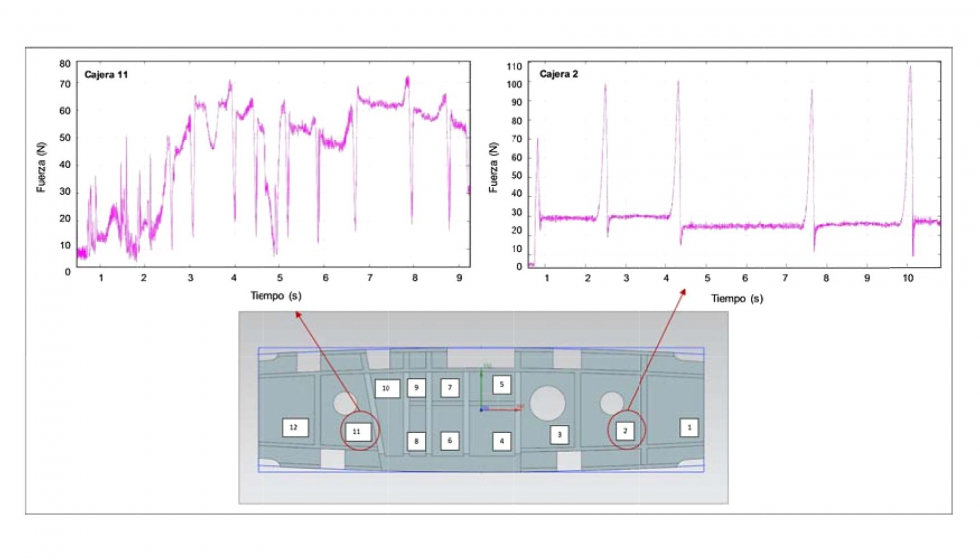
Figura 10. Fuerzas registradas durante el mecanizado de dos de las cajeras.
5. Conclusiones
Debido a las características particulares de los UAV y la demanda que se está generando hace que se deban optimizar los procesos de fabricación de sus componentes. Por ello en este trabajo se ha realizado:
- Una revisión de las causas que dificultan el mecanizado de paredes finas en aleaciones ligeras utilizadas enfocadas hacia el mecanizado de UA V y sus posibles soluciones.
- Se ha llevado una primera aproximación mediante el mecanizado de un rib en aluminio 7075 la utilización de sulfato de calcio como elemento rigidizador de las paredes combinado con la refrigeración criogénica con CO2.
- La pieza obtenida ha mostrado como dicha combinación puede tener su aplicabilidad en dicho sector simplificando sus mecanizados con el fin de ahorrar tiempos de mecanizado.
Por otra parte, se debe seguir avanzando en esta línea. Para ello y partiendo del conocimiento generado en este trabajo se plantean las siguientes líneas futuras:
- Optimización de las condiciones de corte con el desarrollo de di agramas de lóbulos que aumenten aún más la productividad del proceso.
- Desarrollo de utillajes que permitan su mecanizado en una sola atada. Evaluación económica del uso de CO2 como fluido de corte.
- Estudiar la viabilidad de utilizar sulfato de calcio en ribs en aeronaves convencionales.
Agradecimientos
Los autores agradecen el soporte económico recibido por el programa Hazitek del Departamento de Desarrollo Económico e Infraestructuras del Gobierno V aso y de los fondos europeos Feder recibidos mediante el proyecto con acrónimo Hematex. Así mismo también quieren agradecer la financiación recibida por el Ministerio de Economía y Competitividad mediante el proyecto TURBO (DPI 2013-46164-C2-1-R).
Referencias
[1] http://www.sandvik.coromant.com/es-es/industrysolutions/aerospace/aluminium/ Pages/Wing-rib.aspx visitado el 11/6/2017 a las 15:05
[2] http://www.channelbiz.es/2016/11/28/los-drones-suponen-una-mayor-oportunidad-de-la-que-puedas-pensar/ visitado el 07/06/17 a las 9:01
[3] The milling airframe components with low rigidity: a general approach to avoid static and dynamic problems. S. Herranz, F.J. Campa, L.N. López de Lacalle, A. Rivero, A. Lamikiz, E. Ukar, J.A. Sánchez, U. Bravo. Proceedings of the Institution of Mechanical Engineers, Part B: Journal of Engineering Manufacture. 2005. 219, 789-
801.
[4] A. Raghu and S.N. Melkote. Analysis of the effects of fixture clamping sequence on part location errors. International Journal of Machine Tools and Manufacture. 2004. 44, 373-382.
[5] A. Calleja, M.A. Alonso, A. Fernández, I. Tabernero, I. Ayesta, A. Lamikiz& L.N. López de Lacalle. Flank milling model for tool path programming of turbine blisksand compressors, International Journal of Production Research. 2015. 53, 3354-3369.
[6] S.A. Tobias, Machine Tool Vibration. 1965. Ed. Blackie ISBN 1291-1972.
[7] J.A. Sánchez. Desarrollo de un modelo dinámico tridimensional para la simulación de del proceso de fresado frontal. Tesis Dpto de Ingeniería Mecánica de la Universidad del País Vasco. 1998.
[8] Y. Altintas. Metal Cutting Mechanics, Machine Tool Vibrations, and CNC Design. 2000. Cambridge University Press, ISBN 0 521 65029 1. The Edinburgh Building, Cambridge.
[9] http://okigihan.blogspot.com.es/p/wings-wing-configurations-wings-are.html accedido el 14/06/2017 a las 8:20.
[10] O. Pereira, A. Rodríguez, A.I. Fernández-Abia, J. Barreiro, L.N. López de Lacalle. Cryogenic and minimum quantity lubrication for an eco-efficiency turning of AISI
304. Journal of Cleaner Production. 2016. 139, 440-449.
[11] L.N. López de Lacalle, C. Angulo, A. Lamikiz, J. Sánchez. Experimental and numerical simulation of the effect of spray cutting fluids in high speed milling. Jorunal of Materials Processing Technology. 2006. 172, 11-15.