Control de calidad en línea en la soldadura láser de alta potencia
El control activo de la calidad y la supervisión de la soldadura pueden ayudar al fabricante a conseguir que sus productos cumplan los exigentes niveles de calidad de la norma ISO 9000. Un método que, sin duda, ayuda a conseguir estos resultados es el control de la calidad en línea del proceso de soldadura láser: este sistema contribuye a obtener únicamente piezas óptimas o, al menos, permite disponer de la información sobre el resultado unos milisegundos después de la soldadura. Si los datos recopilados por estos sistemas de control se almacenan, se logrará además una trazabilidad total de los productos.
Todos y cada uno de los pasos de control de calidad de una soldadura (seguimiento de la costura de unión, control de plasma, análisis del baño de fusión de la soldadura y análisis topográfico del cordón de soldadura) están bien estudiados y comprobados en el sector industrial. El siguiente paso es integrar estas tecnologías en una herramienta inteligente de soldadura por láser, para facilitar el proceso y ahorrar costes.
Zonas de control de calidad en línea
El concepto de control de calidad en línea significa que todos los sensores van montados muy cerca del útil de soldadura y operan simultáneamente. Así pues, no se necesita tiempo adicional ni más operarios para llevar a cabo el control o análisis, ni tampoco ninguna estación de inspección especial, y se evita la destrucción de las piezas soldadas.
El control de calidad en línea se realiza en tres zonas.
La primera zona se encuentra situada delante del proceso de soldeo, y corresponde al “seguimiento de la costura de unión”.
La segunda zona de control es el propio proceso de soldeo, y corresponde a lo que se llama “sistemas de control de plasma” y “sistemas con cámara”, que evalúan las señales ópticas procedentes del proceso de soldeo o del baño de fusión.
La tercera zona se sitúa detrás del cabezal de soldadura. Aquí, el proceso de soldeo ha finalizado y lo que se analiza es el cordón solidificado.
Además de éstos, y sobre todo para la zona posterior del útil de soldadura, hay otros métodos de supervisión, como el control en línea por ultrasonidos o por corrientes de Foucault. No obstante, la técnica más habitual de control de calidad en línea es el uso de sensores ópticos en la herramienta de láser. Quizá los avances que se introduzcan en el futuro hagan que cambie esta situación.Es obvio que en la región posterior ya no es posible controlar el proceso de soldeo en sí, es decir, ya no se puede alterar el proceso.
Por el contrario, la calidad del proceso puede mejorarse considerablemente mediante el seguimiento de la costura de unión y el control del volumen de separación (gap), delante del cabezal. También existen técnicas que utilizan las señales emitidas por el plasma para controlar, por ejemplo, la potencia del láser y conseguir así una penetración constante. Así, en el soldeo de plásticos con láser de diodo y en los procesos de endurecimiento superficial, se utilizan sensores de temperatura para controlar la potencia del láser y evitar daños en el producto. Quizá en el futuro los procesos de soldeo de alta potencia puedan controlarse también mediante estos métodos.
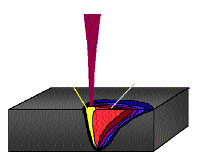
Discontinuidades y defectos en la producción en serie
Otros factores fundamentales son la selección del dispositivo de láser y del equipo adecuado y la optimización de los parámetros de soldeo.
En la producción en serie es fundamental realizar bien este análisis previo al inicio de la producción. No obstante, también es cierto que en el resultado de la producción en serie intervienen e influyen otros muchos parámetros desconocidos. La misión del control de calidad es vigilar estos parámetros imprevistos y avisar al operario para que compruebe el proceso.
La norma EN ISO 13 919 contiene una lista de las categorías de las imperfecciones que puede utilizarse como guía.
Para encontrar el proceso de control de calidad adecuado, es necesario preguntarse en primer lugar cuál es la razón por la que ocurre un fallo determinado. En esto radica precisamente la diferencia con los procesos de control de calidad tradicionales, en los que sólo se tiene en cuenta la calidad del cordón una vez acabado y no el proceso, que contiene una gran cantidad de información.
El control del cordón/unión y el control en línea permiten detectar, y evitar en muchos casos, los defectos de soldeo más graves. El análisis topográfico aporta más datos. Los dispositivos de evaluación de imágenes de alta frecuencia presentan unos costes similares o superiores a los del sistema de seguimiento de las costuras de unión. En este documento no se tratan dichos dispositivos.
Control de la unión de soldadura
El aumento de la utilización de la soldadura por rayos láser en el sector de fabricación de carrocerías de automóviles y, en general, para el soldeo de planchas de metal estampado ha hecho surgir la necesidad de aplicar un control activo con seguimiento de la unión. De hecho, hoy en día, en casi todos los procesos de soldadura en techo mediante láser de CO2 o de Nd:YAG se utiliza un sistema de control de la costura de unión. Ciertos tipos de costuras especiales, como las soldaduras de ángulo en la junta de recubrimiento, exigen un manejo muy preciso del útil de soldadura. En los procesos de soldadura por recubrimiento, la estrechez del canal a veces hace necesario utilizar un sistema de seguimiento de la unión. Con una velocidad de unos 5 m/min., la precisión del propio robot no es suficiente para mantener el cabezal correctamente encauzado. La cámara de control de la unión (imagen 3), situada delante del cabezal de soldadura, toma como referencia el borde de la plancha de recubrimiento para controlar el movimiento lateral del útil de soldadura. La rueda de reacción mantiene la posición vertical.
La aparición de nuevos conceptos de unión flexible, por ejemplo la soldadura de planchas de diferente composición y/o grosor (tailored blank welding), y el reciente desarrollo de cordones no lineales son otros factores que han hecho surgir la necesidad de contar con sistemas de seguimiento de las costuras de unión. Para conseguir unos resultados homogéneos, se necesita una precisión de guiado superior a 0,1 mm a una velocidad de 10 m/min.
No obstante, la resolución de la cámara, normalmente superior a 0,05 mm, no basta para mantener correctamente orientado el útil de soldadura; las guías y la herramienta de guiado también influyen. La cámara de seguimiento de la unión va midiendo la alineación unos 10 a 50 mm por delante del punto de central de la herramienta. Los movimientos de corrección se realizan en un intervalo de unos milisegundos según la velocidad de soldeo. Conocer la posición de la cámara durante la medición es tan importante como la propia precisión de la cámara. Por esta razón, utilizamos unas guías especiales, diseñadas para mover el cabezal y la cámara de forma independiente con respecto al sistema de medición de la posición del robot. El sistema de seguimiento de la unión que hemos creado no necesita comunicarse con el sistema de control del robot: éste no interviene para nada en los movimientos de corrección. La conexión entre ambos sistemas se realiza mediante una simple señal digital de E/S. Para optimizar el comportamiento dinámico del bucle de control de posición es más fácil trabajar con nuestros pequeños accionamientos lineales que con los ejes del robot, cuyo comportamiento cambia en función de la posición real.
Otros elementos que permiten conseguir un seguimiento adecuado son las rutinas de software especiales con corrección previa de la imprecisión del robot y los filtros informáticos para suavizar el movimiento de los ejes.
La medición del tamaño de la separación (gap) y el cálculo del volumen de material de relleno son otros procesos que se utilizan, por ejemplo, para controlar la alimentación de cable con un sistema de control en bucle cerrado (por ejemplo, en soldadura híbrida). El control del tamaño de la separación puede proporcionar datos importantes sobre la calidad, que pueden llevar a rechazar una pieza bruta o a interrumpir el proceso de soldeo para comprobar el estado de la unión en aplicaciones de soldadura tailored blank.
Control en curso
Hay dos tipos de control en curso: por un lado, un sistema con cámara (QUALAS), que evalúa las propiedades geométricas y térmicas del ojo de cerradura y del baño de fusión mediante el procesamiento de imágenes; por otro lado, un sistema de control de plasma equipado con un fotodiodo (control de soldadura láser).
Qualas
El área y la longitud del baño de fusión se miden mediante una cámara especial que controla el baño mediante infrarrojos. Entre la longitud del baño y la profundidad de penetración existe una relación lineal. A partir de esta relación, se pueden detectar desviaciones de hasta +/- 0,15 mm con respecto a la profundidad de penetración exigida.
Este sistema también puede utilizarse para el control de soldaduras con penetración completa. En estas aplicaciones, en la imagen también puede verse si los bordes están bien alineados y si la separación está aumentando de tamaño. Si la soldadura con penetración completa está terminada, se verá un punto oscuro en medio del ojo de cerradura brillante. Si la separación está aumentando, el ojo de cerradura estará partido en dos semicírculos. Por su parte, si los bordes están mal alineados, la forma circular del ojo de cerradura cambia y este adquiere una geometría asimétrica.
Soldadura láser tailored blank
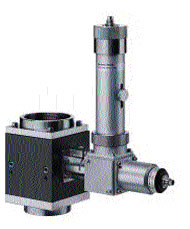
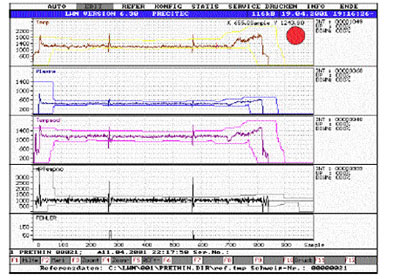
La soldadura láser tailored blank es un proceso muy utilizado en el sector de la fabricación de automóviles. El aumento del número de planchas y su uso en diversas partes vitales del automóvil han dado lugar a un aumento en las exigencias de calidad. Así pues, en estos momentos no es admisible que la proporción de planchas defectuosas supere unas pocas piezas por millón.
La soldadura láser es un proceso muy fiable; además, se han producido enormes avances en la tecnología de las máquinas de soldadura por láser. No obstante, para garantizar que la tasa de fallos sea mínima, es necesario aplicar un proceso de supervisión y control de calidad completo. Los pequeños defectos mecánicos en los bordes de soldadura, el esfuerzo mecánico en las planchas, la contaminación de aceite y otras suciedades son algunos de los factores por los que más se ve afectada la calidad.
Algunos factores que influyen en la calidad son:
Velocidad de soldadura
Con una velocidad de soldadura de 12 m/min. o 200 mm/s -velocidad que se puede alcanzar con matrices de un grosor de 1 mm, por un lado, y un tamaño de fallo menor que 0,5 mm, por otro- se consigue una frecuencia de detección alta. Un fotodiodo, que procese valores analógicos, puede alcanzar sin problemas un rango de varios cientos de Hz o kHz.
Repetibilidad, preparación del borde y sujeción
El principio de los llamados controladores de plasma exige una alta repetibilidad y condiciones de soldeo constantes. Si hay grandes oscilaciones con respecto al patrón de referencia de soldadura, la capacidad de detección de fallos se reduce. La importancia de una buena preparación de los bordes y de una buena sujeción es evidente [3].
Revestimiento de cinc y capas de aceite
Los recubrimientos de cinc galvanizados o estañados en caliente aumentan las fluctuaciones con respecto al patrón de referencia, especialmente si no hay un gas de protección para controlar el plasma o la neblina de vapor metálico (algo común en los procesos de soldadura mediante láser de Nd:YAG). En el sector del troquelado es normal que la superficie de las planchas presente una cierta cantidad de aceite. En la mayoría de los casos, esto no afecta a la calidad del cordón de soldadura, pero el aceite evaporado aparece en las trazas del sistema de control de plasma, lo que disminuye la validez de la evaluación de las trazas.
Fusión incompleta
En los procesos de soldadura tailored blank es normal que se utilicen planchas de distinto grosor. El uso de un solo detector de plasma no es suficiente para detectar si hay algún fallo en la alineación entre el cabezal de soldadura y el borde. Para mejorar la capacidad de detección de este grave defecto es conveniente utilizar un sistema multisensor con uno o más sensores de temperatura.
Existen diversos sensores especiales con una mejor relación señal/ruido, que ofrecen el nivel de detección adecuado.
En las imágenes 7 y 8, se muestra el montaje común de los sensores en un cabezal de soldadura normal. Precitec KG ha descubierto una forma de integrar el conjunto sensor en un nuevo cabezal de soldadura de alta potencia (con el fin de reducir la dimensión exterior del cabezal de soldadura, especialmente en procesos guiados por robots).
Este cabezal presenta todas las características necesarias para llevar a cabo un proceso de soldeo mediante láser de Nd:YAG de alta potencia y con un estricto control de calidad. El cabezal tiene integrados varios sensores para la supervisión del proceso, así como otros dispositivos de control activo para evitar fallos. El chorro transversal con flujo supersónico de aire reduce al mínimo la contaminación de la pantalla de protección. El monitor de filtros de protección manda una señal de alarma en caso de éstos presenten una contaminación importante. Gracias a estos sistemas, se evita la posibilidad de soldar con una pérdida de potencia debido a que los dispositivos ópticos estén sucios.
Los sistemas de guiado del flujo de aire y del gas de proceso están integrados en la paredes de la resistente carcasa de aluminio. Además, es imposible que los cables o tubos exteriores sufran daños térmicos o mecánicos.
La brida de montaje, que está diseñada para poder cambiarse rápidamente en caso de ruptura, permite montar una cámara de seguimiento de la costura de unión. Este cabezal, combinado con un sistema de seguimiento de costuras y un sistema de guiado lineal, constituye un paquete completo de control de procesos de soldadura por láser.
Conclusión
La tecnología láser lleva utilizándose varias décadas en los procesos de soldadura aplicados en el sector de la automoción, lo que ha hecho surgir la necesidad de montar sensores de control en línea. En el mercado hay una gran variedad de sensores y sistemas de control en bucle cerrado. Los sistemas de control más importantes son el seguimiento de costuras de unión para controlar la tolerancia de las piezas (por ejemplo, en la soldadura de piezas de automóviles o en procesos tailored blank no lineales), y el llamado control de plasma, que permite supervisar cada una de las piezas. Otro sistema de control es el análisis geométrico del baño de fusión, un dispositivo dotado de una cámara, que permite captar datos muy importantes para la calidad. Estos sofisticados sistemas ópticos deben integrarse en las máquinas láser, que operan en entornos industriales en condiciones extremas. La utilización de sistemas de control de bucle cerrado integrados en el útil/cabezal de soldadura está permitiendo simplificar el trabajo tanto de los fabricantes como de los operarios de las máquinas.
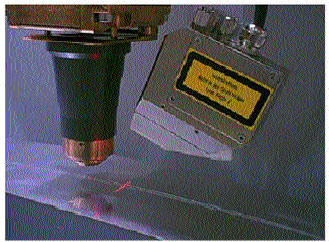
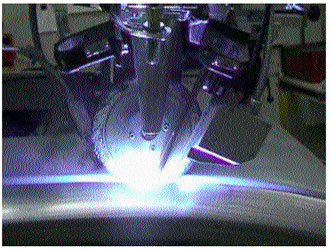
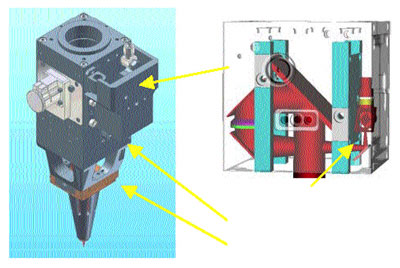
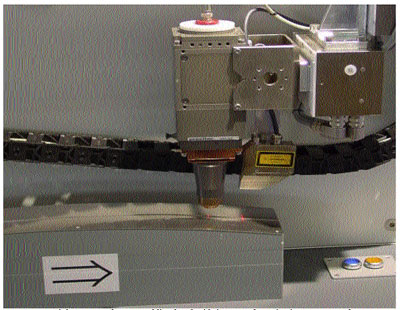
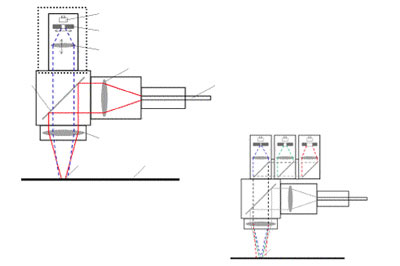
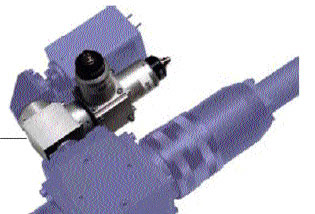