Cojín servomecánico para prensas mecánicas eficiente y de alta prestación
El objetivo principal del proyecto que se presenta ha sido, fundamentalmente, el diseño y desarrollo de un cojín controlado más ecoeficiente para prensas mecánicas e hidráulicas.
Un repaso a la situación actual
Dicho de forma genérica, una prensa mecánica es una máquina cuyo fin es la conformación de chapas metálicas, utilizando para ello la fuerza que de forma mecánica son capaces de producir conjuntamente la mesa fija y el carro en movimiento que la componen, empleando dicha fuerza y movimiento relativo para dar una nueva forma a la chapa de metal, esto es, efectuando el proceso denominado embutición.
En dicho proceso, aunque una vez puesto a punto sea un proceso increíblemente productivo, las labores de puesta a punto no son nada fáciles, ya que son muchos los factores que intervienen en las características de la pieza final. Uno de esos factores importantes son las posibles arrugas o pliegues que pueden aparecer en la pieza. De hecho, las arrugas o pliegues son una de las típicas consecuencias indirectas del proceso de embutición. Para evitar dichas arrugas o pliegues, se estira directamente hacia el área de embutición el material de la periferia de la parte de la chapa a la que se está dando una nueva forma. Así pues, si ese movimiento no es controlado debidamente, se producen rugosidades.
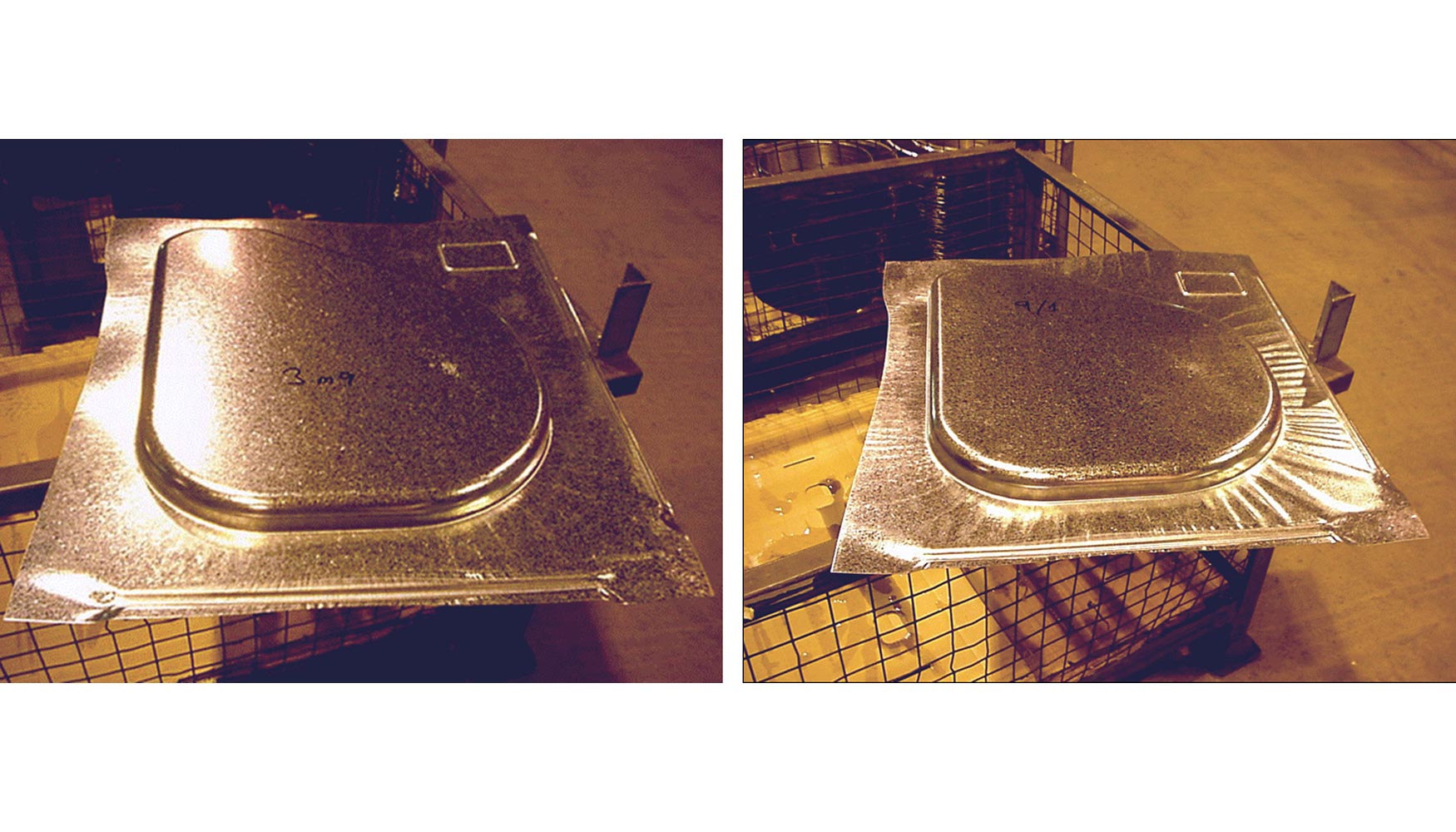
A la izq., pieza debidamente prensada. A la dcha., pieza no suficientemente prensada en la en la embutición, con rugosidades.
La forma de realizar dicho movimiento de una manera controlada consiste en pisar la chapa haciendo una cierta presión sobre ella, sin impedir el movimiento de deslizamiento de la chapa pero sí impidiendo que la chapa se mueva de manera perpendicular y se produzcan rugosidades. La magnitud de dicha fuerza de presión puede variar mucho de una instalación a otra, dado que la pieza depende de varias características: material, tamaño, profundidad de la embutición, etc.
Para que el cojín cumpla su función, éste debe hacer una fuerza en sentido opuesto al carro, a lo largo de todo el recorrido en el que se produce la embutición. Para ello, tradicionalmente se han usado unos cilindros neumáticos grandes como generadores de esa contrafuerza, los cuales actúan como un muelle sin modificar demasiado la magnitud de dicha contrafuerza (que se consigue utilizando depósitos grandes de aire). En este tipo de cojines, la contrafuerza producida por el propio cojín al carro hace que la energía acumulada como consecuencia del aumento de presión del aire sea devuelta al carro, en el momento en que el carro vuelve a ascender tras haber realizado la embutición. De esa manera, apena se pierde energía en el proceso (a menos que el cojín no lleve un sistema de bloqueo en el BIP).
En las últimas décadas, el cojín hidráulico se ha impuesto al cojín neumático, debido a que, por un lado, cuando el carro en movimiento choca contra el cojín que está fijo, se producen unos picos de fuerza y vibraciones que resultan perjudiciales, tanto para el troquel como para la máquina en general, y a que, por otro lado, el cojín hidráulico puede pre-acelerar el cojín, y conseguir de esa manera que la velocidad relativa de choque disminuya y que las consecuencias negativas sean menores. Pero la razón principal es la capacidad de controlar con gran precisión la contrafuerza que se realiza durante el movimiento de prensado, pudiendo configurarse diferentes fuerzas de prensado durante el recorrido y controlar así más exactamente el proceso.
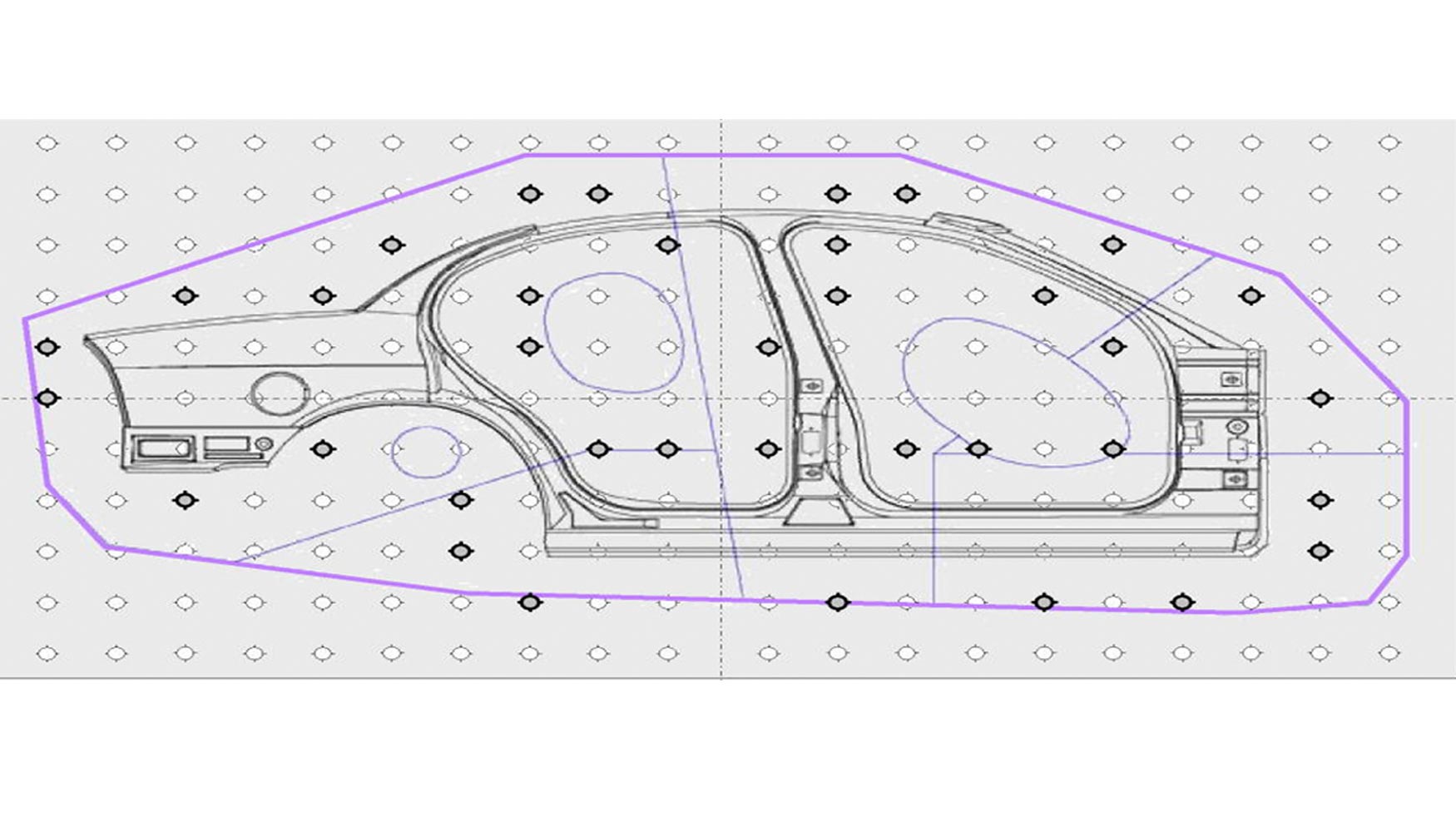
Distribución espacial de los puntos de presión para la embutición adecuada de un lateral de automóvil.
Dado que también el espacio físico que necesita dentro de la prensa es mucho menor (aunque fuera de la prensa requiere una instalación grande), se pueden introducir varios puntos de presión independientes en una única estructura de cojín, siendo capaz de presionar con diferentes fuerzas a lo largo de la superficie del cojín, y ofreciendo la posibilidad de adaptarse al deslizamiento de material requerido por cada forma de embutición.
Aunque en las últimas décadas se ha impuesto este tipo de cojín, también tiene una gran desventaja: la eficiencia energética. De hecho, un cojín hidráulico es, al fin y al cabo, un cilindro hidráulico que, cuando el carro de la prensa entra en contacto con él y empuja hacia afuera el aceite de la cámara, consigue que dicho aceite atraviese un paso estrecho regulable y presurice el aceite del cilindro, produciendo una contrafuerza en el recorrido del carro. Entonces ocurre que la energía que se produce por la contrafuerza durante ese recorrido se gasta calentando el aceite, debido a la “laminación” del aceite, al hacerlo atravesar por el paso estrecho. Si ese gasto de energía fuese poco, para que el aceite no se queme es necesario realizar un enfriamiento después de cada ciclo, por lo que a la falta de efectividad del sistema hay que añadir el consumo energético que tiene en sí el sistema de enfriamiento. Y como las prensas mecánicas precisan de una terrible fuerza, la energía que se pierde debido al uso de los cojines puede tomar magnitudes impresionantes: por ejemplo, el cojín del cabezal de prensa de una línea G1 puede consumir 3.000 kW y 2.100 kJ por pieza.
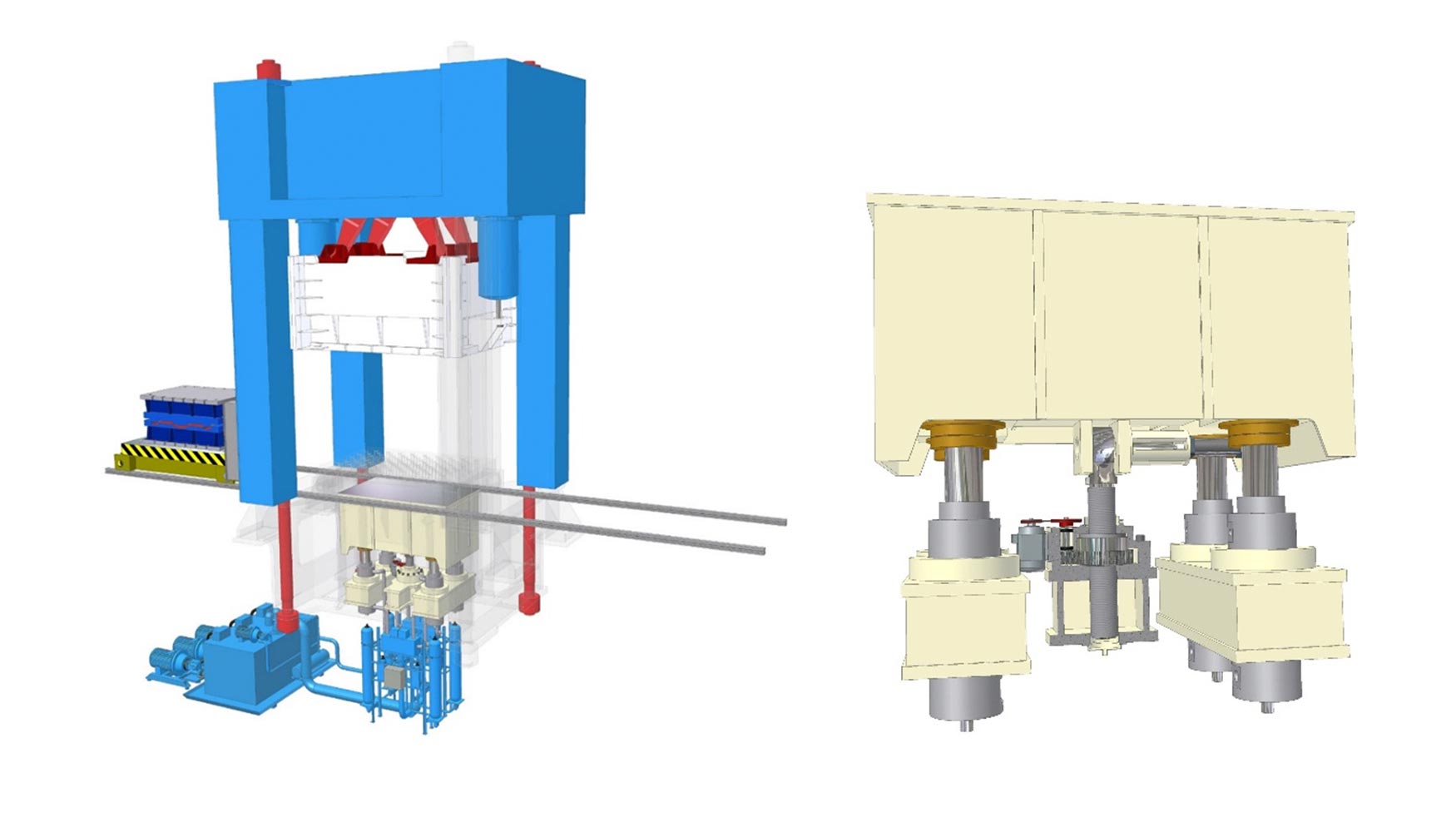
A la izq., cojín hidráulico en prensa, en azul la instalación. A la dcha., cojín hidráulico de 4 puntos.
Objetivo del proyecto
En estos momentos en los que el coste de la energía es cada vez mayor, los clientes han empezado a percatarse de que pueden ahorrar mucho con la compra de instalaciones que son energéticamente eficientes.
En este contexto, el objetivo final de este proyecto ha sido sustituir el cojín hidráulico por otro que sea mecánico y servoaccionado y que sea capaz de sincronizar el accionamiento principal de la prensa mediante un control inteligente y realizar una secuencia de trabajo definida.
La configuración actual del cojín hidráulico no permite gestionar la optimización energética. La servotecnología, por su parte, permite interaccionar energéticamente con el accionamiento principal, y de esa manera conseguir que el flujo de energía regenerada entre los dos dispositivos tenga resultados beneficiosos para el consumo general de la máquina.
Así, pues, este nuevo cojín de diseño eco garantiza un menor impacto en el medio ambiente (reducción muy importante en cuanto a perdida de aceite y consumo de energía) y ofrece, a su vez, mejores servicios y prestaciones en comparación con el cojín hidráulico convencional.
Detalles
El objetivo del cojín mecánico servoaccionado sería proporcionar una contrafuerza controlada al carro de la prensa, aprovechando la energía que se produce en esa contrafuerza para su reutilización, en vez de gastarla transformándola en calor, tal como ocurre en los cojines hidráulicos. Para ello el cojín mecánico servoaccionado utiliza un servomotor que trabaja a modo de generador en la parte del ciclo donde se produce la oposición. Dicha energía es enviada a un Buffer o almacén de energía, de donde el motor principal la cogerá para su uso, produciéndose una relación energética entre el motor y el almacén de energía sin que el suministro eléctrico de la fábrica ‘perciba’ picos de ciclo completo (alrededor de 3.000 kW en el proceso de embutición). Esta forma de gestionar la energía acepta un dimensionamiento menor del suministro de energía de la fábrica, con el ahorro económico que ello conlleva.
En la siguiente tabla aparece claramente cuál sería el ahorro de energía que se produciría en algunas condiciones habituales de producción si se utilizase el cojín servomecánico, así como el importe que supondría ese ahorro con el precio actual de la energía. Con dichos datos, y dado que el servocojín resulta más caro que el cojín hidráulico, se calcula cuál sería el tiempo de amortización de la inversión realizada en el servocojín.
Fuerza máxima del cojín |
6.000 |
KN |
Recorrido máximo |
350 |
mm |
Factor de uso |
75% |
|
Cadencia media |
10 |
gpm |
Horas trabajadas al día |
16 |
horas |
Horas de trabajo anuales |
330 |
días |
Energía en cada ciclo |
1.575 |
kJ |
Plazo de amortización |
2 |
años |
La inversión realizada en el cojín electromecánico queda amortizada en el plazo de 2 años, un plazo muy corto para una instalación como la de una prensa mecánica que tiene una vida media de algunas décadas. Vistas esas cifras se ve como algo muy interesante el desarrollo de este nuevo cojín, tanto desde el punto de vista del ahorro y calidad para el cliente como desde el punto de vista de un modelo energético más sostenible para el mundo.
Desarrollos realizados
A la hora de realizar el cojín mecánico servoaccionado se decidió utilizar la transmisión de piñón-cremallera para adecuar el movimiento lineal del carro de la prensa al metabolismo giratorio del servomotor, valiéndonos de su simpleza y de la larga experiencia que tenemos en estos elementos. Asimismo, para gestionar la energía que se extraerá al carro de la prensa, hay que conseguir que acceda en condiciones adecuadas al servomotor. Para ello se ha utilizado un reductor planetario de dos etapas, para que las magnitudes del momento y de la velocidad de giro sean las adecuadas para el servomotor.
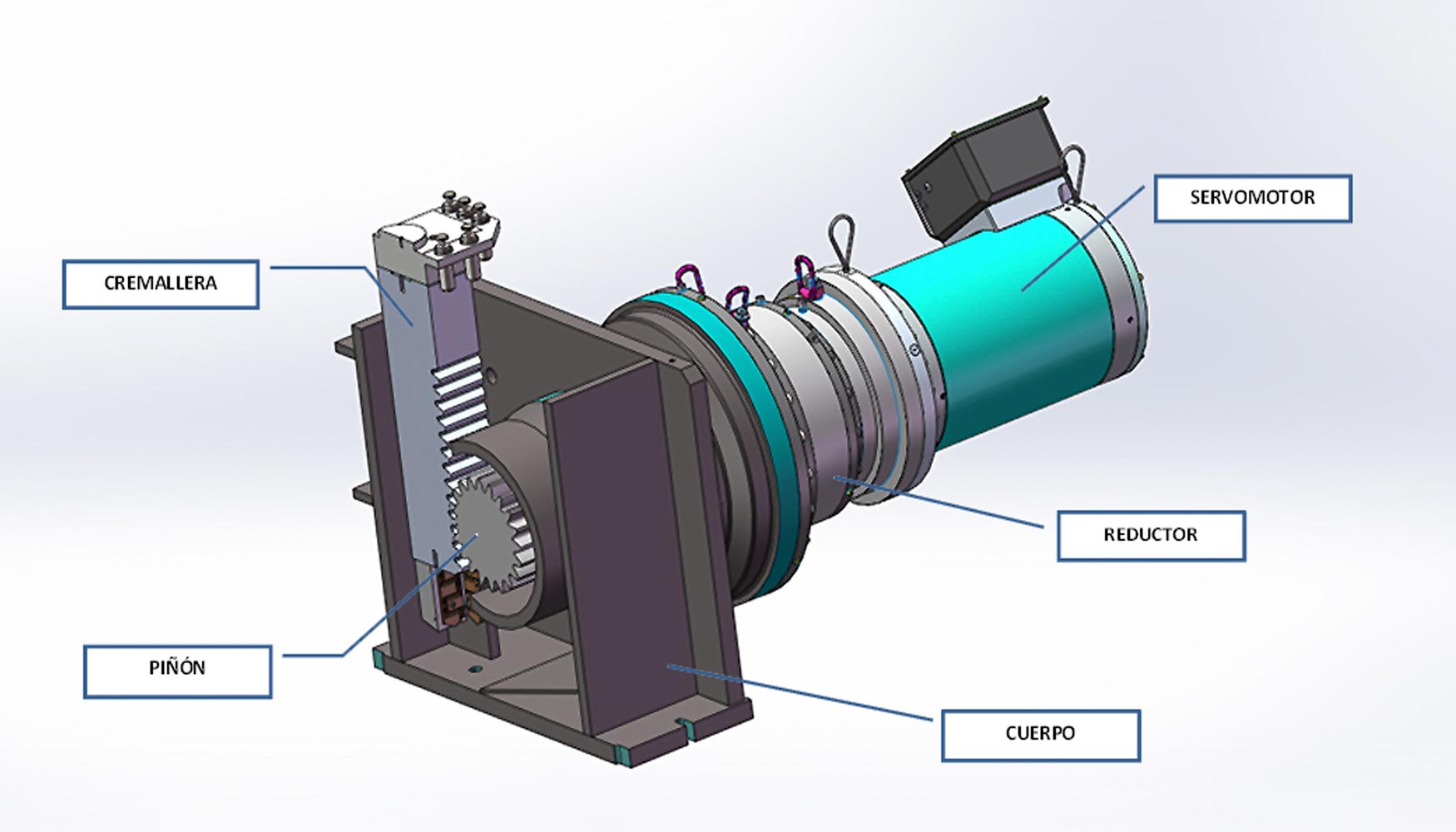
Corte de un cojín servomecánico.
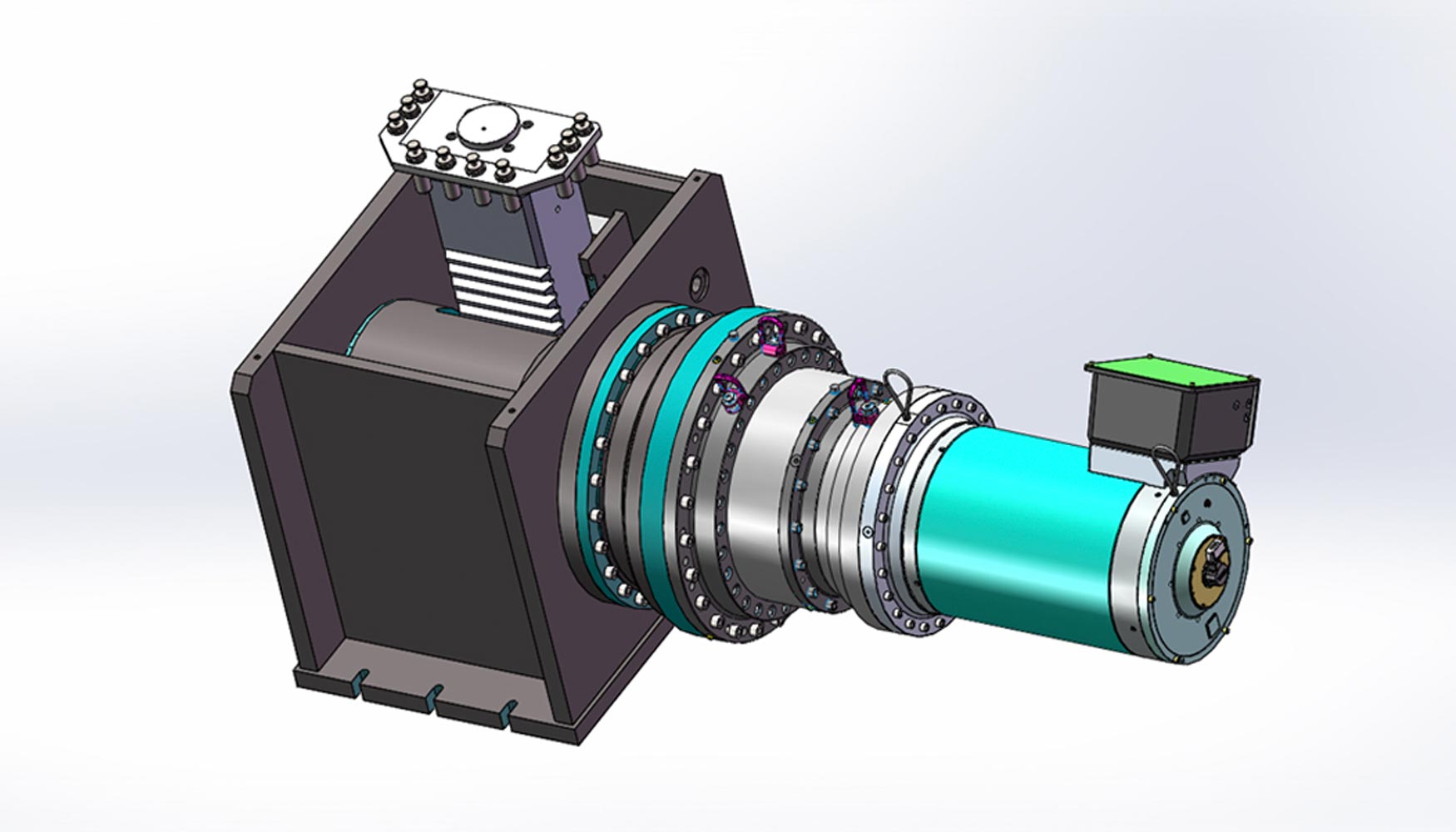
Cojín servomecánico en perspectiva.
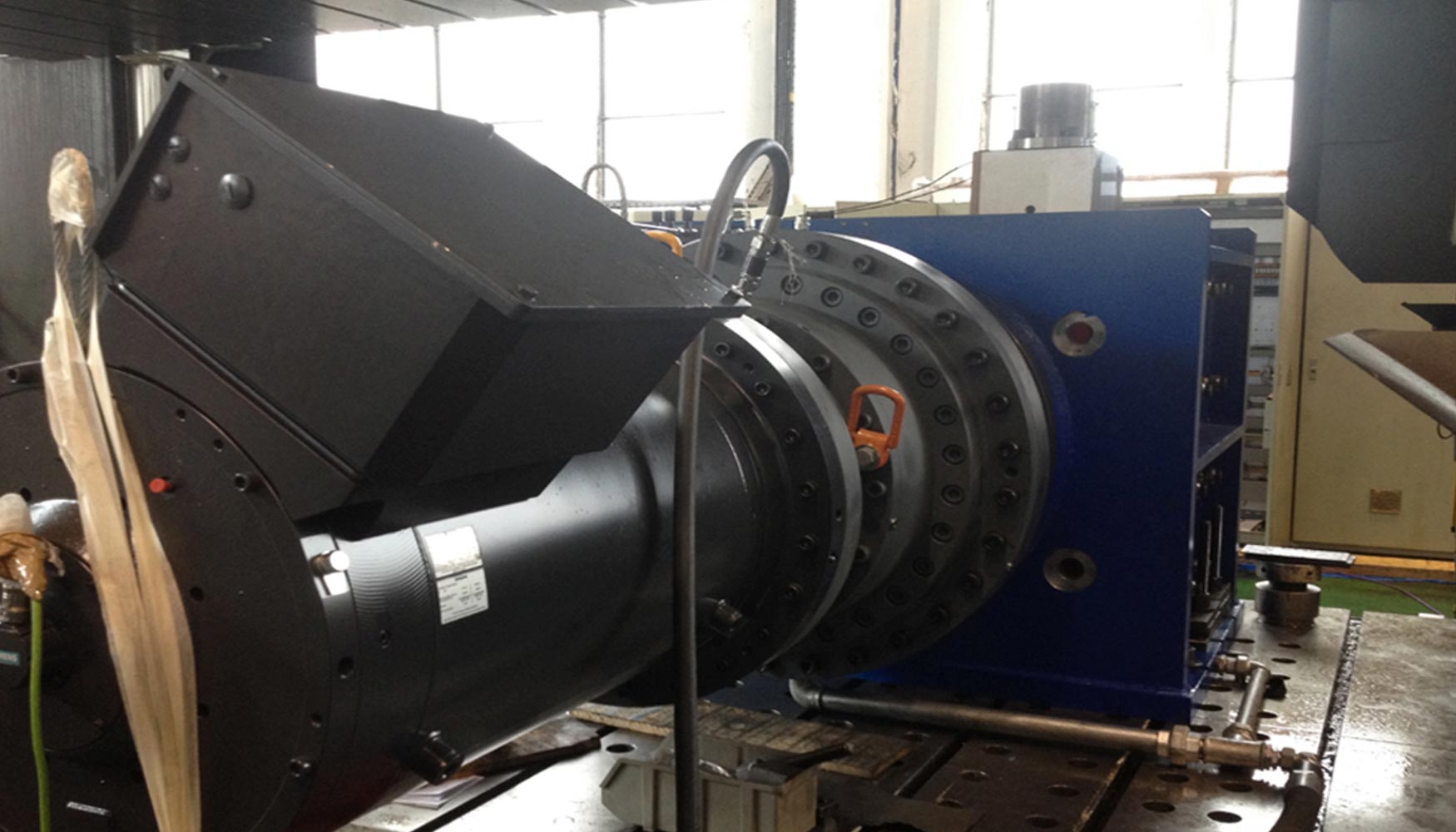
Prototipo construido del cojín servomecánico dentro de la prensa, probando las prestaciones.
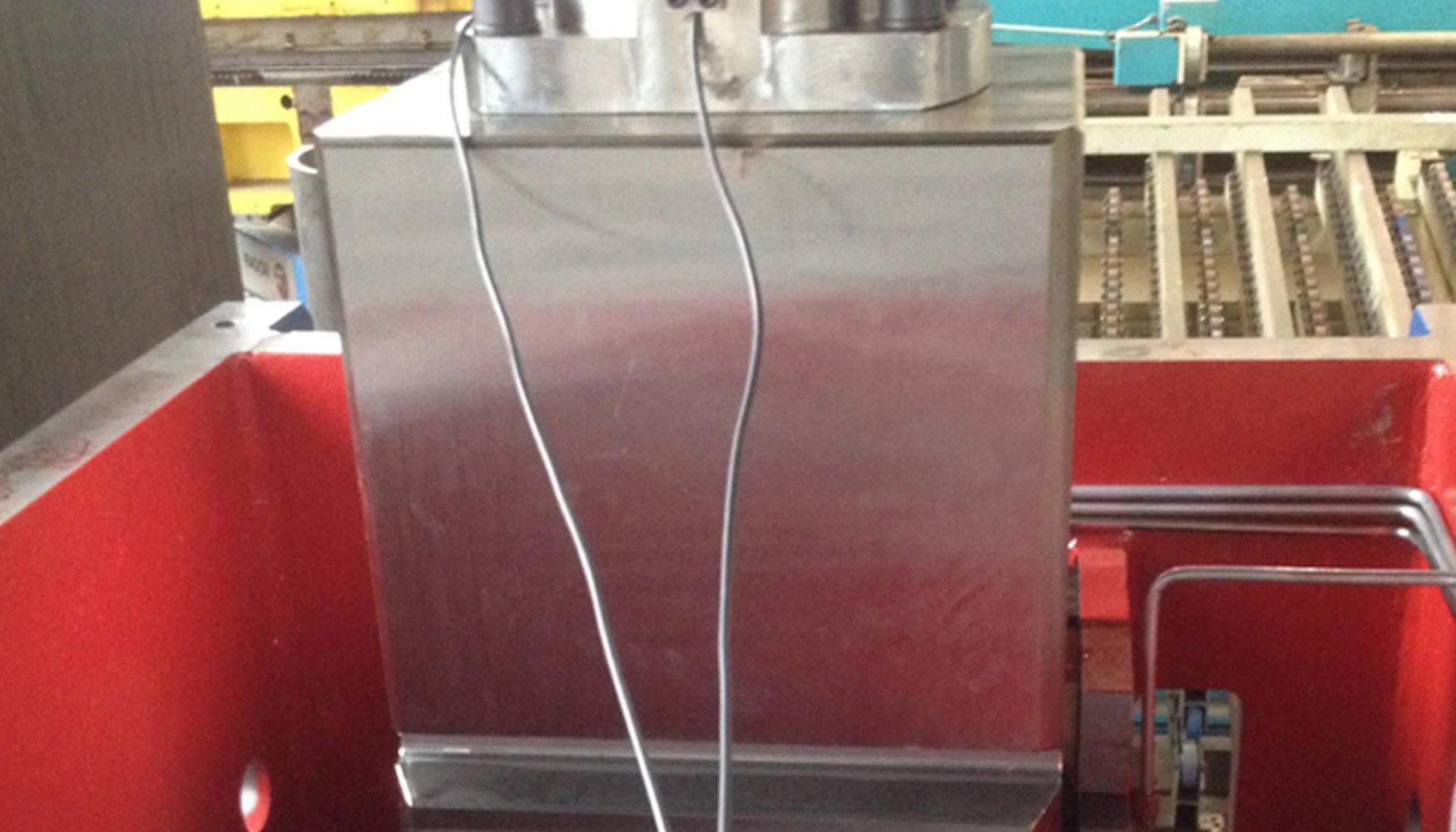
Prototipo construido del cojín servomecánico. El sistema de cremallera de piñón con los engrases correspondientes.
Por otro lado, la estructura de la base de la prensa requiere una profunda adaptación, debido a la forma que adopta el cojín en el espacio. De hecho, el cuerpo formado por el servomotor y el reductor planetario nos obliga a atravesar el lateral principal de la base, si se quiere que la cremallera acoja en el punto conveniente al cajón del cojín. Asimismo, la estructura que acogerá el piñón y el engranaje de la cremallera, con la guía y los puntos de engrase correspondientes, se ha integrado en la estructura de la base, teniendo en cuenta la rigidez correspondiente y la transmisión de fuerzas y dejando los huecos necesarios para los trabajos de mantenimiento.
En consecuencia, por debajo de la estructura de la base no asoma parte alguna del cojín, y resulta más fácil la instalación de esa zona de la prensa y acepta una distribución más óptima del foso. Sin embargo, a cambio, dado que los cuerpos que forman el servomotor y los reductores planetarios salen hacia los laterales de la base, se reduce el espacio a las tolvas, condicionando su geometría. A pesar de todo, esto no dificulta la función de las tolvas, solo pide tener en cuenta el librar los motores a la hora de diseñar.
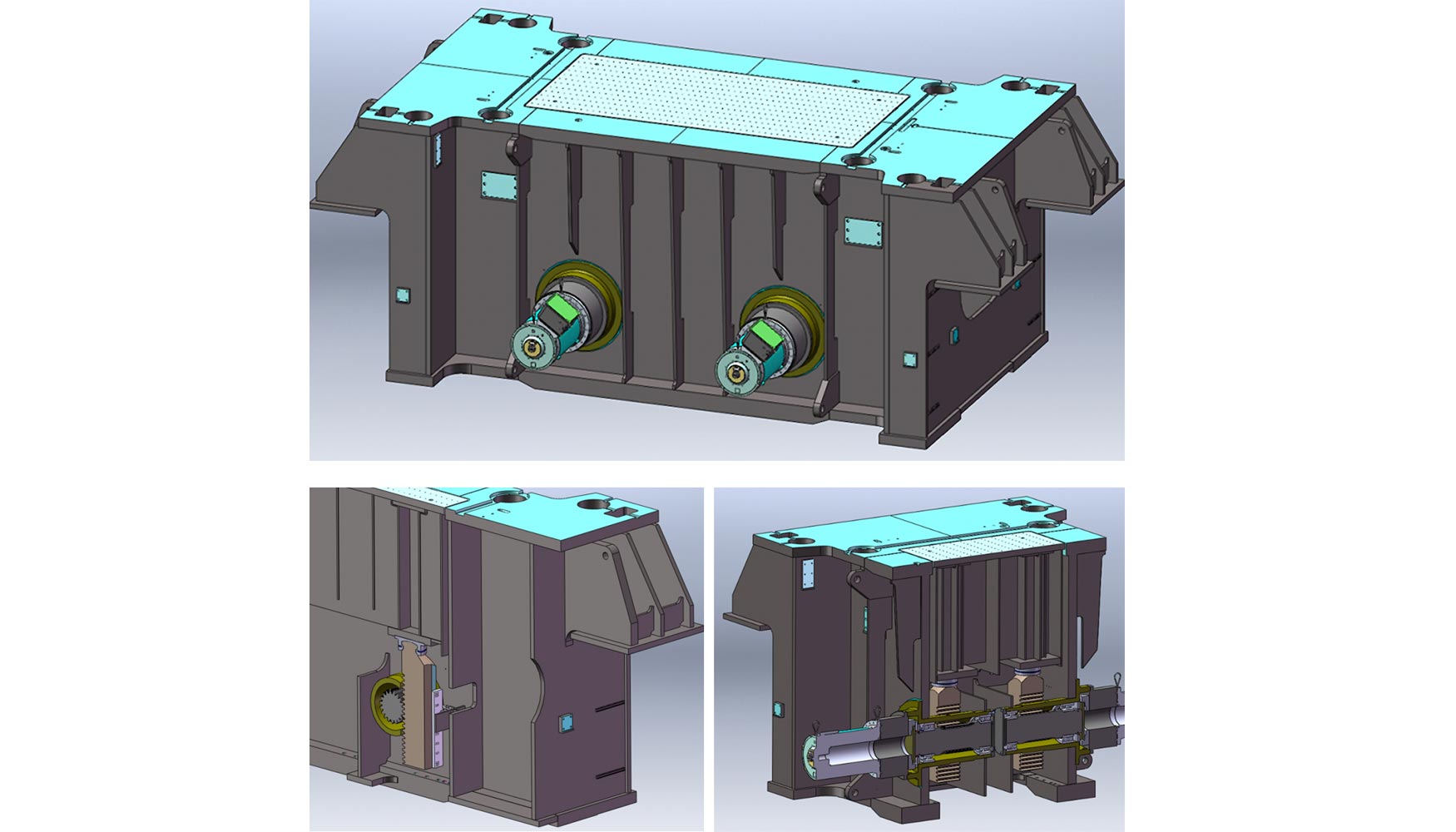
Adaptaciones en la estructura de la base para la introducción del cojín servomecánico, vista en perspectiva y corte.
En cuanto al software de control del cojín, el desarrollo ha sido realizado con elementos de Siemens, ya que hasta ahora se ha utilizado este material en las servoprensas, y de esta manera se consigue que el cojín y la servoprensa sean compatibles y se facilita mucho la comunicación entre dichos elementos.
Conclusiones
Aparte de la mencionada eficiencia energética, son varias las ventajas del cojín servomecánico respecto al cojín hidráulico. Cuenta con mejores prestaciones una vez producida la embutición: cuando el carro de la prensa ha iniciado el camino hacia arriba, un poco más atrás, el cojín debe levantar la pieza terminada hasta la posición inicial necesaria para que el transfer pueda sacar la pieza. Una vez expulsada la pieza y colocado otra vez el nuevo formato sobre el troquel, el carro que está descendiendo debe encontrar el cojín y la pieza en su sitio, para que se produzca adecuadamente el proceso de prensado. Así, pues, este movimiento de ascenso del cojín suele ser determinante en el cojín hidráulico, ya que frecuentemente, cuando se realizan embuticiones de mucha profundidad, no se pueden conseguir cadencias altas y el cojín no tiene tiempo para regresar con la rapidez que necesita a la posición inicial. Para el cojín servomecánico eso no es un problema, ya que puede realizar el movimiento bastante más rápidamente, haciendo desaparecer el “tendón de Aquiles” del cojín hidráulico.
Otra ventaja relevante es el enorme ahorro de espacio en el foso del taller, ya que el cojín hidráulico suele necesitar un sitio considerable para que la motobomba, el depósito de aceite, el acumulador y otros elementos tengan cabida (unos 22 m2 de media). Unido a eso, los trabajos de mantenimiento y los costes también se ven reducidos considerablemente, puesto que al no necesitar aceite se evita la necesidad de cambiar frecuentemente el aceite (unos 5000 litros), los filtros y otros.
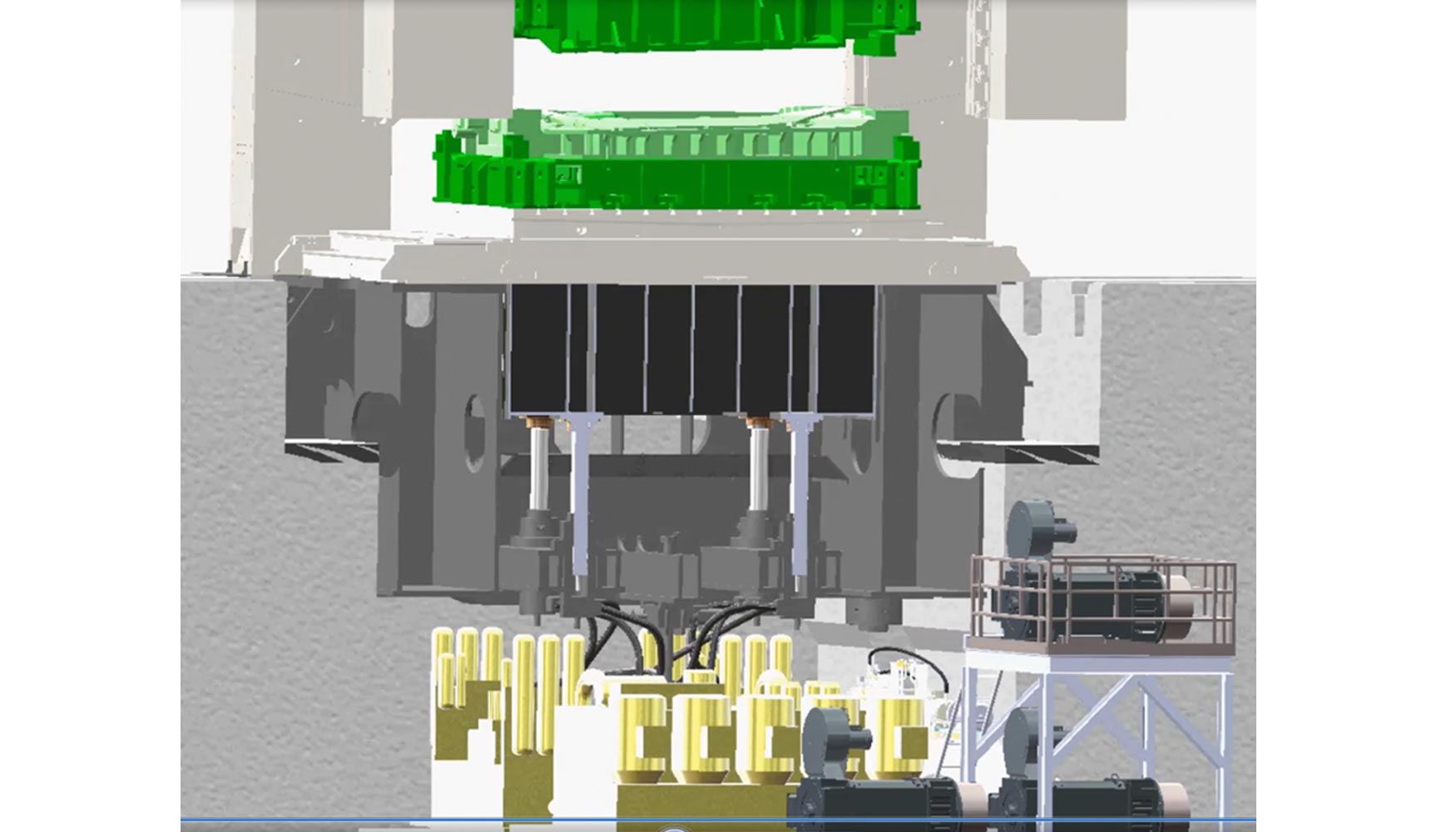
Espacio ocupado por el cojín hidráulico en la base y en el foso; en color amarillo el grupo hidráulico.
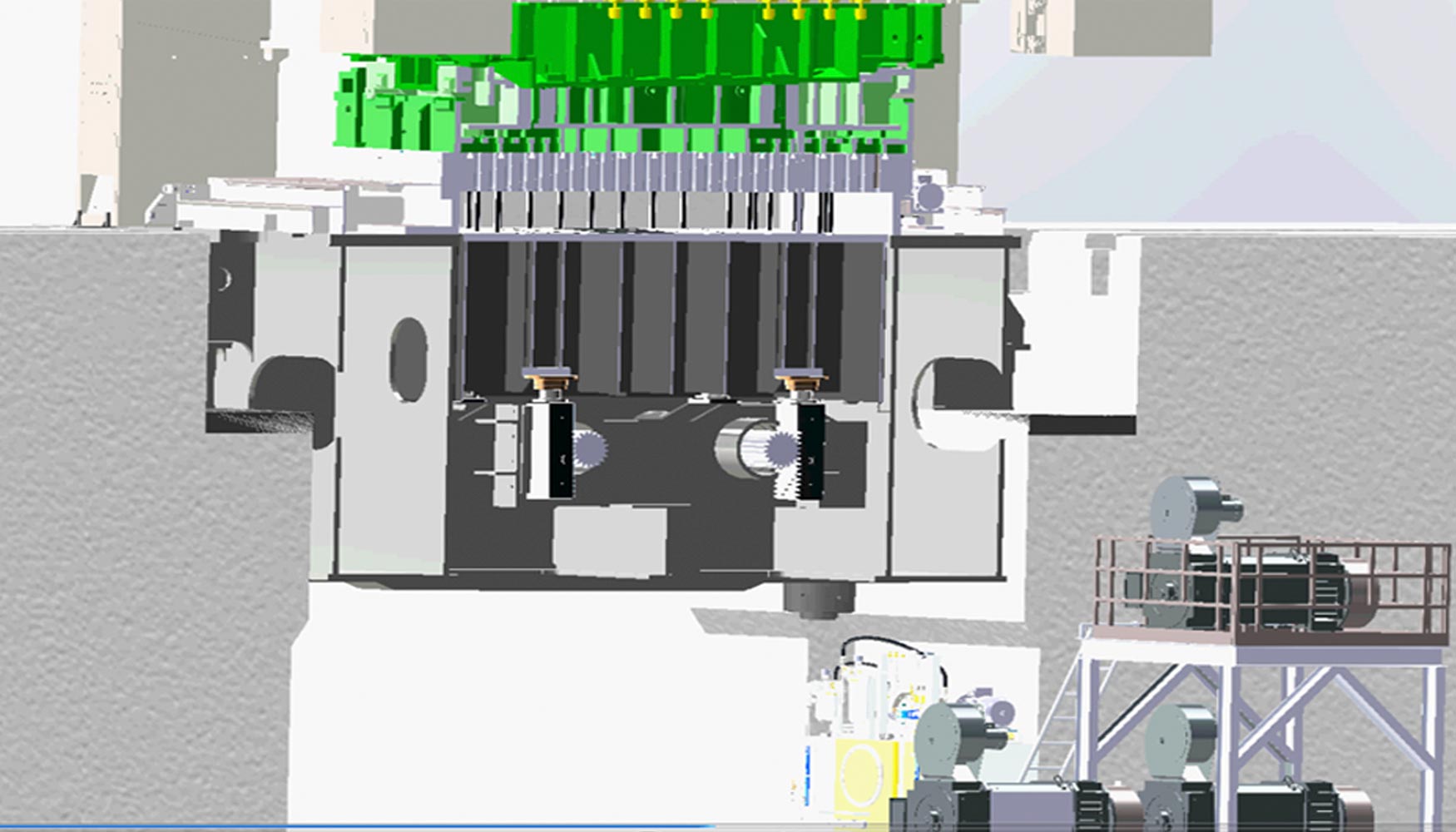
Espacio que ocupa el cojín servomecánico en la base y en el foso; observar todo el espacio libre que queda al no ser necesario un grupo hidráulico, sitio para la cinta de chatarra, para los grupos de prensa, etc.
Una empresa comprometida medioambientalmente
Fagor Arrasate es uno de los principales productores de maquinaria para el procesamiento y conformado de chapas de acero. Las líneas estratégicas definidas por la empresa para los próximos años prevén la comercialización de nuevos productos de alto valor añadido con el fin de mantener la competitividad. Entre dichos productos destaca la necesidad de desarrollar productos energéticamente más eficientes y respetuosos con el medio ambiente.
La cooperativa Fagor Arrasate S.COOP. inició su andadura en 1957, en Arrasate (Gipuzkoa). Su actividad principal es el diseño, fabricación y venta de máquinas y herramientas para la transformación de chapas, flejes y otros materiales. Cuenta con una plantilla de 700 personas (la mitad de ellas realizan labores de Ingeniería y de I+D), y forma parte del Grupo Mondragón (Mondragon Humanity at Work), una de las corporaciones industriales más grandes de Europa. Fagor Arrasate cuenta con 6 plantas de producción, que ocupan un total de 40.000 metros cuadrados, y a través de dichas plantas desarrolla su actividad en Arrasate (2), Markina, Donostia, Zamudio y Kunshan City (China). En el último ejercicio ha conseguido una facturación de 230 M€.
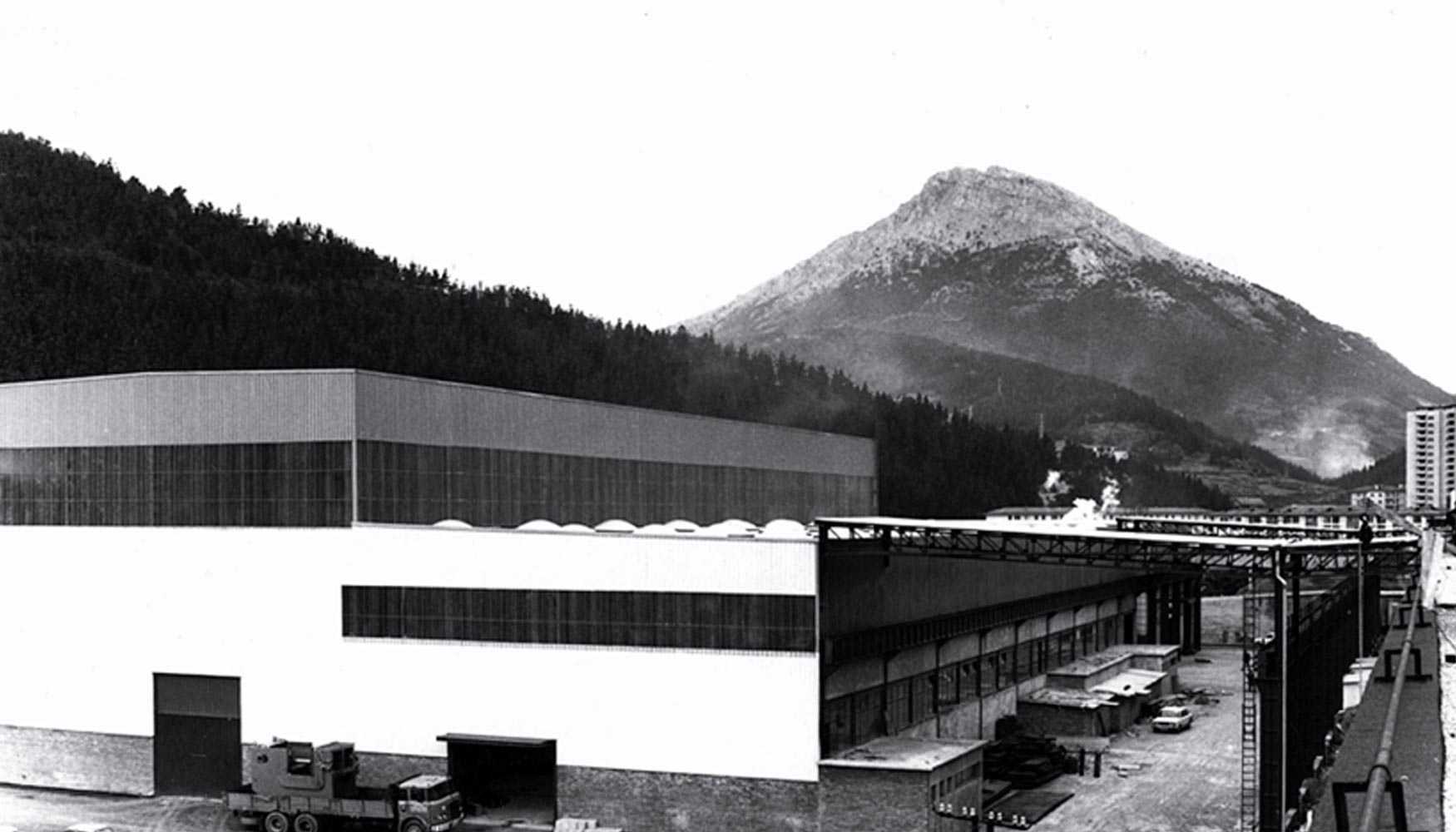
Instalaciones antiguas de Fagor Arrasate.
Como proveedor de primer orden de máquinas para la transformación de chapas, y muy especialmente de prensas de gran tonelaje, Fagor Arrasate provee con sus equipamientos a las empresas más exigentes de los sectores del automóvil y de los electrodomésticos y está especializada en ingeniería, desarrollo y puesta en marcha de medios para la conformación de materiales metálicos, en cualquiera de sus ramas de especialización. Su mercado principal es el de los equipamientos para aplicaciones específicas o equipamientos a medida para exigencias productivas de un cliente en concreto. Dentro de su catálogo de productos, el producto más importante es el correspondiente al diseño y fabricación de prensas de estructura seccionada, para la obtención de piezas de chapa mediante corte y deformación. Así mismo, otra área de actividad importante es el diseño y fabricación de instalaciones de procesamiento de chapas metálicas.
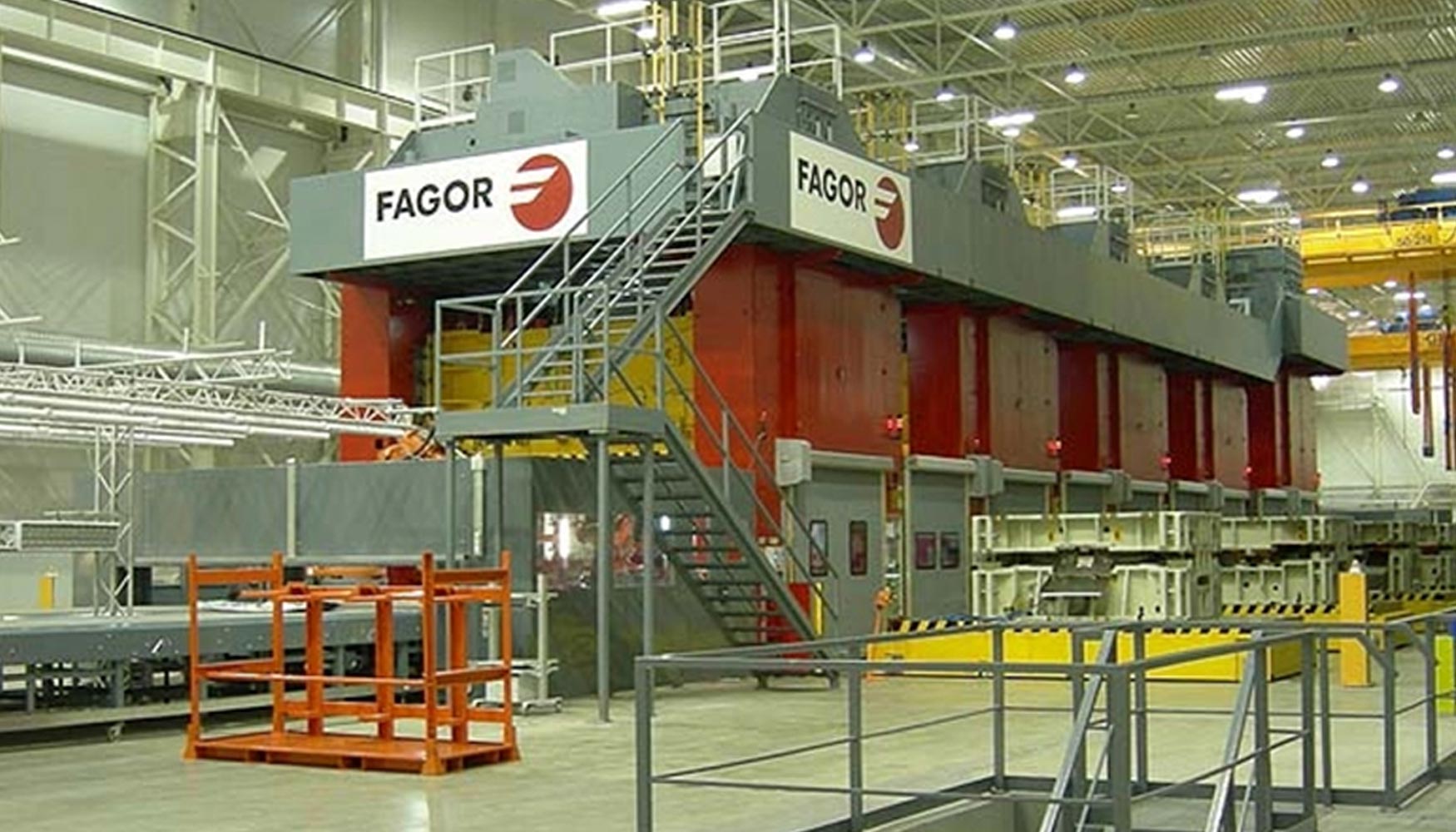
Línea de prensas mecánicas para producciones de grandes series.
Los productos que fabrica Fagor Arrasate pueden dividirse en cinco grandes grupos:
- Prensas y sistemas de estampación, tanto mecánicas como hidráulicas.
- Líneas de corte y sistemas de procesamiento de bobinas, formatos y chapas metálicas de todo tipo.
- Líneas para la fabricación de tubos y sistemas de perfilado.
- Sistemas especiales para la fabricación de piezas complejas de chapa y sistemas de transferencia.
- Troqueles.
Actualmente la firma exporta alrededor del 90% de sus productos. Además de querer crecer para satisfacer nuevos mercados, en los próximos cuatro años su producción ira dirigida prioritariamente a mercados de Europa, en especial a Alemania, y de China. Además de eso, pretende impulsar aún más países como Brasil, México e India, con el fin de que en un futuro sean receptores productivos de la empresa. Y con los nuevos planes previstos para el 2014, teniendo en cuenta la situación actual del mercado, prevé que el porcentaje de exportación sea del 90-95% aproximadamente.
Plantas productivas de Fagor Arrasate.