La tecnología de la automoción evoluciona con el uso de alternativas ligeras
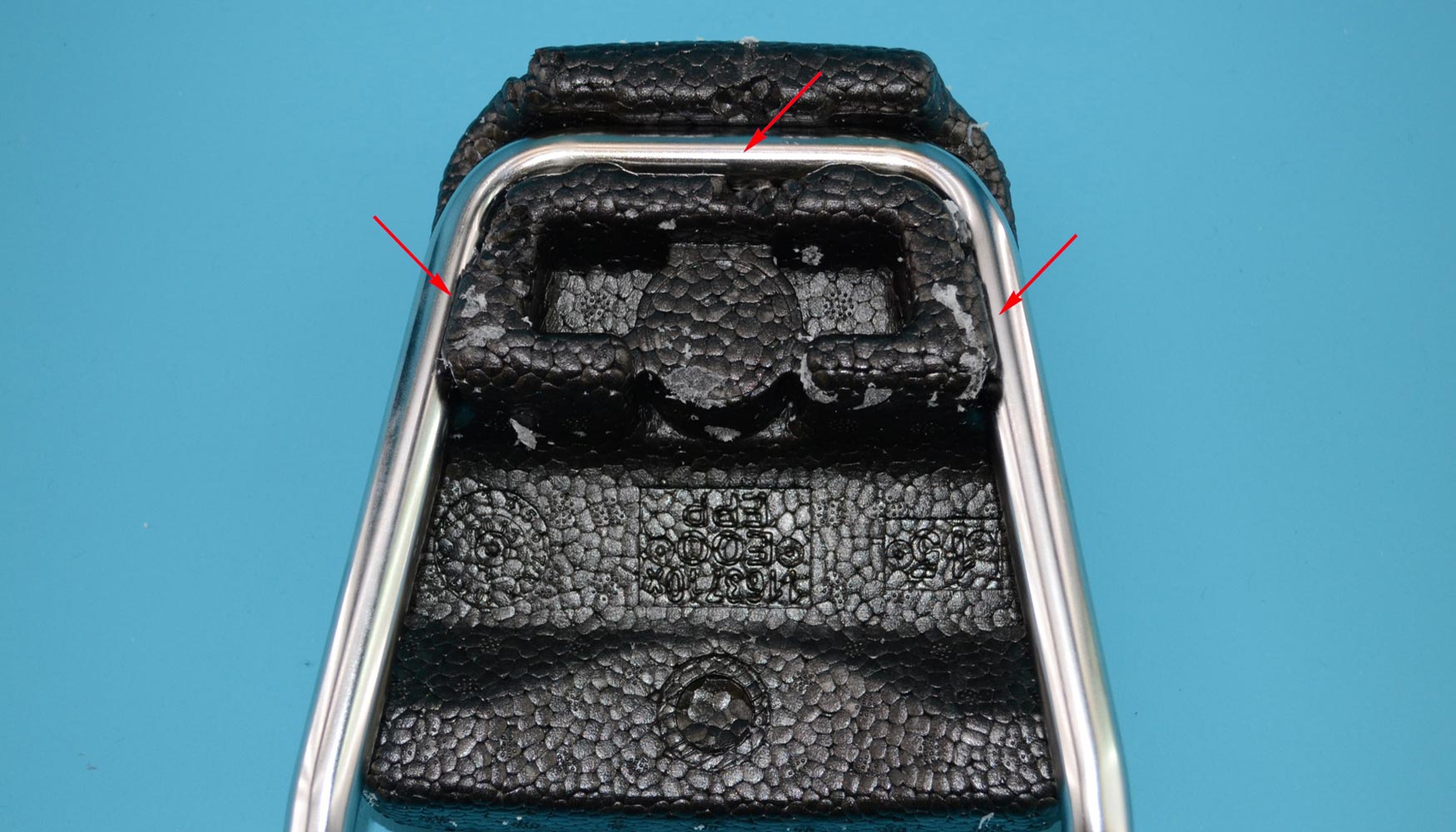
La sustitución de los componentes tradicionales de acero por materiales ligeros puede reducir directamente el peso de la carrocería y el chasis de un vehículo hasta un 50% con un efecto proporcional en el consumo de combustible. Una reducción del 10% en el peso total del vehículo puede proporcionar también un ahorro de entre un 6 y un 8% en el consumo de combustible. Usando materiales estructurales ligeros, los coches pueden llevar más sistemas avanzados de control de emisiones, dispositivos de seguridad y sistemas electrónicos integrados sin aumentar el peso total del vehículo.
Una innovación clave en las décadas pasadas ha sido el desarrollo de Arpro. Desarrollado por primera vez en la década de 1980, lleva más de tres décadas ya formando parte del parque europeo de vehículos. Idóneo para el diseño de automóviles, las grandes cualidades de absorción de energía del material ofrecen una mayor maleabilidad a los diseñadores y ya ha sido utilizado por fabricantes como BMW y Peugeot para aumentar la eficiencia de sus vehículos y lograr innovaciones en la industria de la automoción.
A diferencia de materiales anteriores cuyas cualidades de absorción de energía eran cuestionables, Arpro contaba con dos cualidades físicas fundamentales que lo establecieron rápidamente como material de ‘referencia’ en la protección de impactos a baja velocidad. En primer lugar, su estructura en forma de espuma de células cerradas es isotrópica y ofrece el mismo rendimiento constante independientemente de la dirección en que reciba el impacto. Esto representaba un enorme contraste respecto a los productos de poliuretano rígido y de moldeo por inyección, cuyo rendimiento en impactos no puede predecirse con precisión más que un 5% fuera de la dirección y velocidad anticipada. Su otra ventaja es que puede deformarse en múltiples ocasiones pero regresar a su forma original, lo que le hace idóneo para aplicaciones de impactos a baja velocidad. Con estas cualidades, el material no sólo cumple sino que en muchos casos, supera los estrictos requisitos de rendimiento gubernamentales y de la industria, como EURO NCAP.
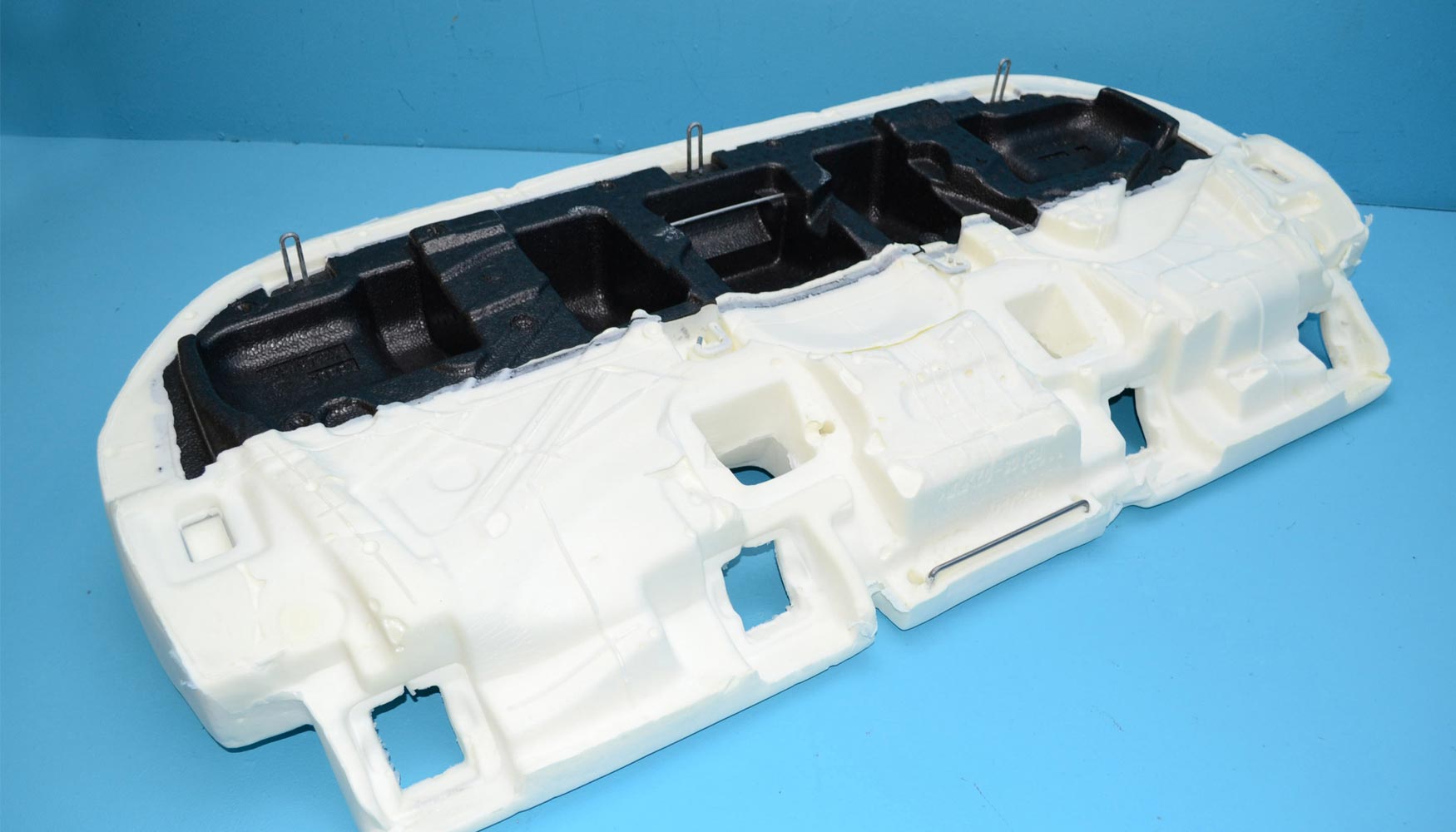
Los diseñadores de coches han aprovechado rápidamente las oportunidades que ofrece esta gama de materiales y, actualmente, es común encontrarlos en todo tipo de vehículos. Las aplicaciones incluyen desde productos de seguridad pasiva como puertas, amortiguadores de energía en impactos laterales y paneles de puertas, reposacabezas y estructuras de los asientos, protecciones para las rodillas y el asiento, y aplicaciones de almacenaje. Aquí, su excepcional relación entre resistencia y peso permite el almacenaje de kits de herramientas en los revestimientos del maletero, suelos de carga y componentes de la consola.
Un gran ejemplo de múltiples aplicaciones es el Peugeot 308. Recibido por la industria como referencia en diseño e ingeniería, el modelo ha sido alabado por su eficiencia y estructura más ligera hasta ser nombrado ‘Coche del Año en Europa en 2014’. Estas características se han logrado mediante el uso intensivo de materiales compuestos, el nuevo diseño de las áreas de impacto y el desarrollo de aplicaciones como la rampa de asiento universal y otros elementos clave fabricados con Arpro.
Al proporcionar una base sólida y adaptable como punto de apoyo, Arpro puede soportar las presiones de la conducción sin que sea necesario renunciar al espacio para garantizar la seguridad. El área almohadillada para las rodillas junto al volante ha sido rediseñada también para este material y permite un diseño más compacto además de dejar más espacio al conductor, a la vez que conserva toda la absorción de impactos requerida. Esta solución para ahorrar espacio ha sido empleada también en el maletero del coche, donde un componente Arpro de una sola pieza aloja la rueda de repuesto y deja un área de carga con el suelo plano.
Utilizado en seis aplicaciones en total dentro del 308, Arpro ha sido uno de los factores principales en la reducción del peso total del coche. El uso del material ligero ha mejorado la seguridad y el rendimiento, ha reducido el consumo de combustible y las emisiones de CO2, y además, la rampa de asiento integrada está hecha íntegramente del material, lo que ha permitido disponer de un chasis plano y modular. Fácil de montar, encajándola simplemente en su lugar, la rampa de asiento del 308 evita la molestia de tener que personalizar en cada modelo la rampa integrada en el chasis. Este diseño ha permitido que los ingenieros apliquen la nueva rampa a varios modelos de Peugeot para ahorrar peso, tiempo y el coste de cada modelo. En total, el uso de Arpro ha contribuido a que el actual 308 pese 140 kilos menos que el modelo anterior.
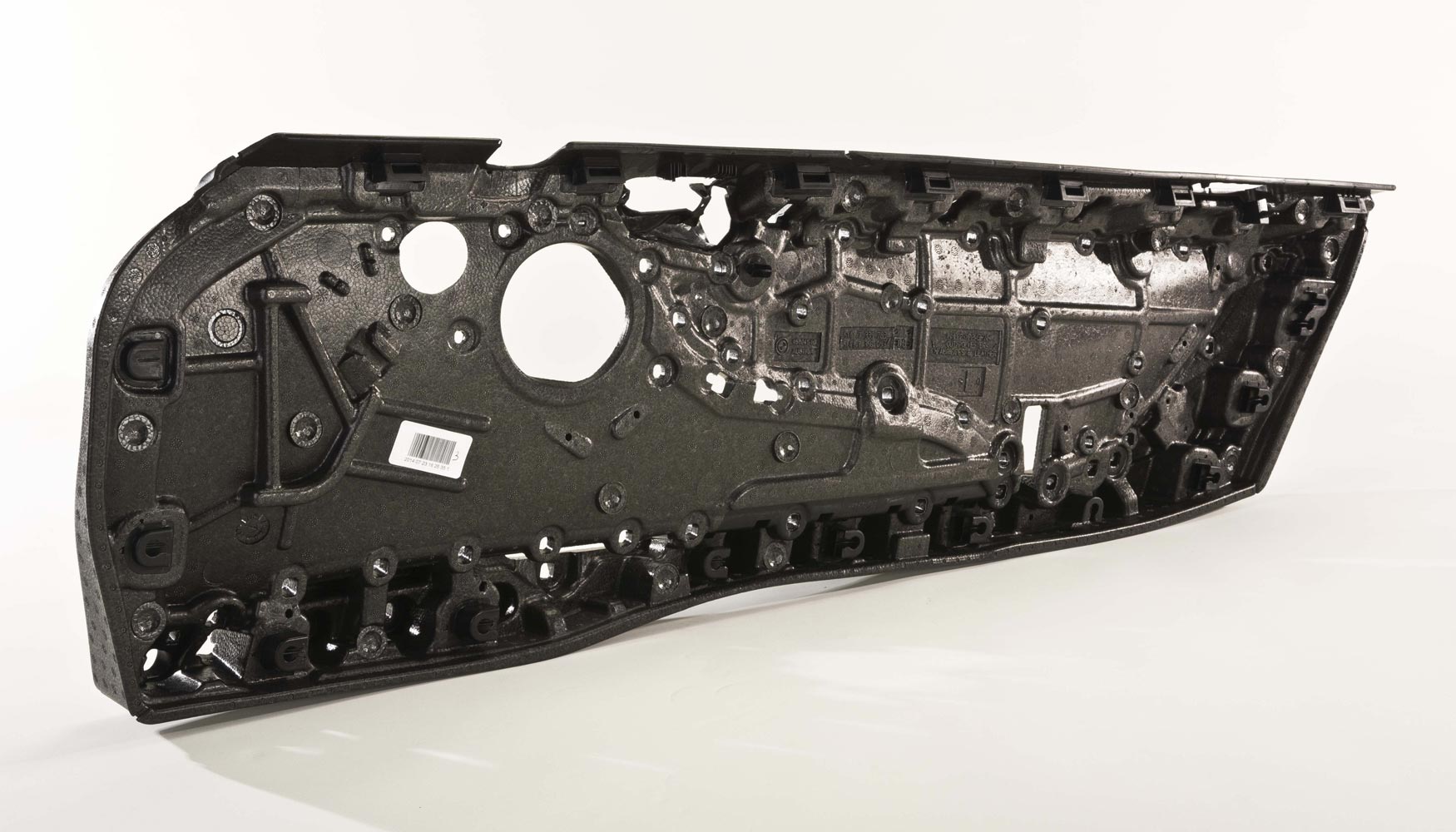
Las aplicaciones de estos materiales incluyen productos de seguridad pasiva como puertas, amortiguadores de energía en impactos laterales y paneles de puertas, entre otros.
Los fabricantes de coches han empezado también a utilizar materiales ligeros para realizar diseños más complejos y producir aplicaciones más elaboradas e innovadoras que anteriormente no eran viables con los materiales más tradicionales y pesados. Aplicaciones como las que exhibe el Peugeot 308 ahorran peso en diferentes áreas del coche, sin sacrificar resistencia o espacio, además de complementar otros materiales cuando es necesario.
Otra ventaja para la industria de la automoción es que los costes de las herramientas son significativamente inferiores que en el moldeo de inyección y los productos ligeros permiten además eliminar las características negativas del molde sin necesidad de realizar más inversiones en herramientas. En el caso de un material como Arpro, tiene la capacidad de reducir la inversión en herramientas en un 50%, al tiempo que reduce significativamente el peso de los componentes y ofrece la posibilidad de crear partes de mayor complejidad que pueden satisfacer requisitos multifuncionales dentro de un componente.
Los recientes desarrollos en los materiales y las mejores soluciones de herramientas han ampliado los límites de la viabilidad en las formas en 3D, además de permitir la creación de productos más pequeños y finos. Los clientes pueden seleccionar entre una amplia variedad de grados por densidad y, de esta forma, lograr la fórmula correcta con el mínimo consumo posible de vapor y una mínima duración de los ciclos. Los reposacabezas, por ejemplo, tienen que pasar rigurosas pruebas de impacto y son una función de seguridad clave en la prevención de traumatismos cervicales, aunque un vehículo estándar puede llevar hasta cinco y añadir un peso considerable. El método tradicional de moldeo de inyección produce componentes más pesados que requieren un revestimiento mayor. Sin embargo, usando un material más ligero como Arpro, los reposacabezas pueden llegar a ser tres veces más ligeros y seguir cumpliendo incluso sobradamente las normativas de seguridad.
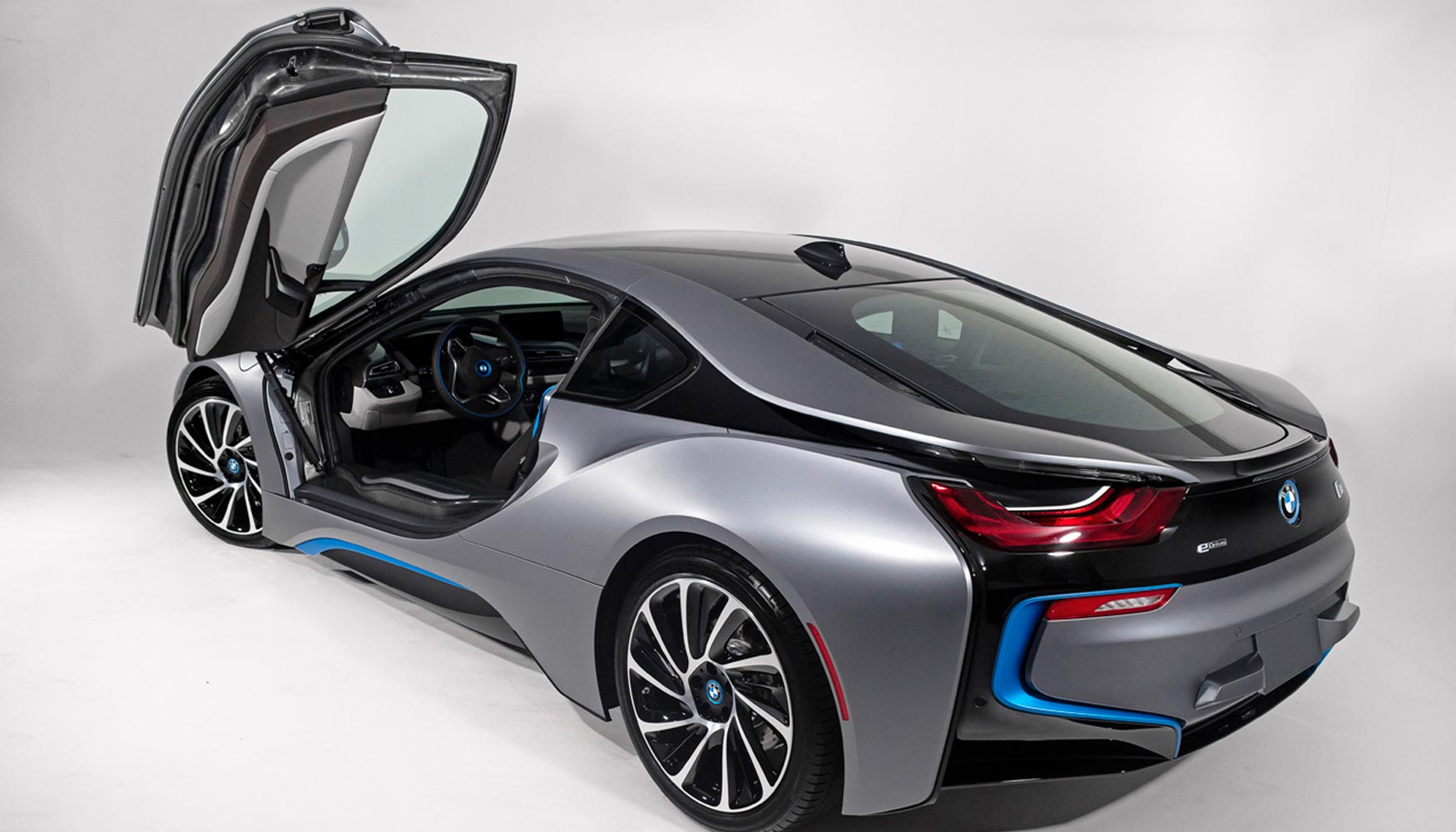
En cuanto al diseño del interior del automóvil, el BMW i8 lanzado recientemente ha adoptado una innovación usando Arpro para los paneles de las puertas del coche. Las puertas que se abren hacia arriba del modelo son atractivas y recalcan las características deportivas del coche, aunque con semejante diseño, los paneles tenían que incorporar un material más ligero que facilitase su elevación.
El diseño del panel de la puerta era particularmente complejo ya que necesitaba proporcionar estabilidad, estructura y resistencia, además de integrar componentes: tapicería, altavoces y mandos, junto al aislante térmico y acústico en una pared muy fina. Todo esto, con la necesidad global de lograr unas tolerancias perfectas apropiadas para un coche de alta gama, por tanto, los materiales más pesados debían ser descartados de inmediato para asegurar que el panel oscilase hacia arriba sin comprometer la estructura.
Arpro se ha utilizado ya ampliamente en modelos BMW, incluidas las aplicaciones estructurales como los bancos de asiento en los X5/X6 y el asiento posterior de la serie 5. Su capacidad para ser moldeado de forma personalizada e integrar canales de cables y mandos proporcionó una solución viable al i8, reduciendo el peso en un 22% aproximadamente y mejorando el rendimiento en colisiones.
El concepto de coche ligero sigue aún en ciernes y muchos diseños, hechos realidad por visiones creativas, se han ido mejorando con las nuevas técnicas y tecnologías. Un gran ejemplo de ello es el proyecto del panel de la puerta del BMW i8 que provocó la asociación entre un proveedor de automoción y un fabricante de materiales, para desarrollar y reconstruir una herramienta de moldeo existente con el fin de hacer realidad el diseño del panel de la puerta oscilante. El radical diseño requirió múltiples intentos hasta alcanzar la perfección, pero el resultado fue técnicamente un éxito y dio como resultado una pieza estéticamente única.
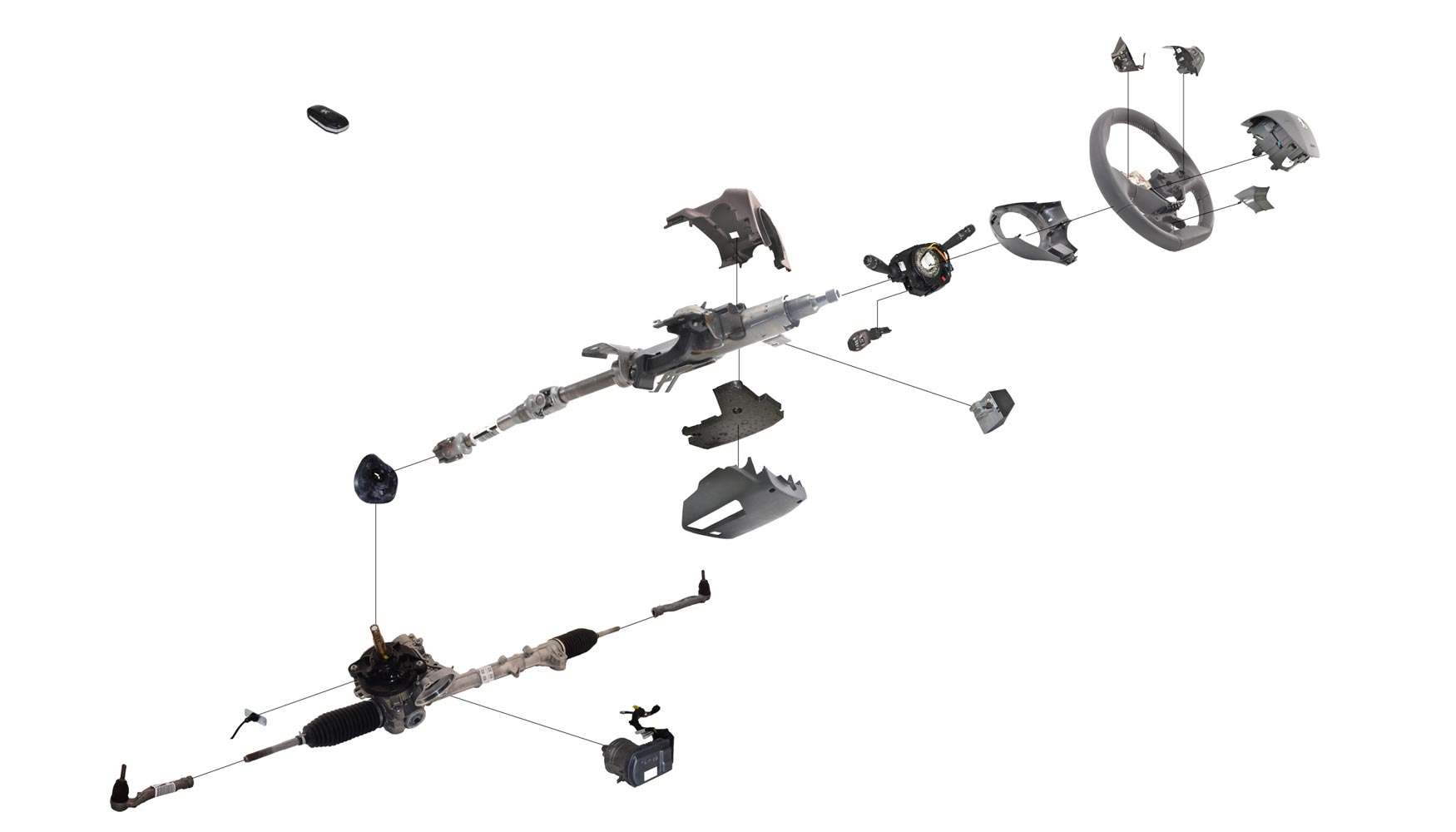
Los últimos desarrollos han creado también productos que proporcionan una mejora en el rendimiento y en la experiencia de la conducción. El sonido y las sensaciones que produce el coche son, en algunos casos, tan importantes como la fiabilidad del motor y por eso, los fabricantes han buscado materiales ligeros alternativos que reduzcan el ruido. Dichos materiales que protegen el motor y aíslan las vibraciones pueden ponerse bajo el capó para reducir los niveles de sonido y absorber energía. La estructura de células cerradas de Arpro puede proporcionar un rendimiento estructuralmente sólido, absorber una alta proporción del ruido e incluso modificar la frecuencia del sonido de un coche potente, para ofrecer al conductor la mejor experiencia en confort y sensaciones.
Tradicionalmente, han surgido cuestiones también en el área de la resistencia a las vibraciones, sobre todo para cuando el vehículo envejece, pero las extensas pruebas aceleradas en colaboración con los principales fabricantes han revelado que los niveles de vibración no son superiores a los que había con el chasis tradicional y están, en todo caso, dentro de los parámetros aceptados de confort y seguridad. La naturaleza isotrópica de Arpro permite, por ejemplo, que la energía del impacto se disipe rápidamente en todas las direcciones.
Estéticamente también, se sigue avanzando rápidamente. Los últimos materiales pueden ofrecer una diversidad de aspectos superficiales con los que el usuario puede olvidarse de la aspereza de la materia prima al presentar una textura superficial uniforme y cálida. Esto desempeñará un papel clave en la reducción del número y peso de los componentes, y no menos en las áreas ‘secundarias’ visibles donde su mínima exposición a los rayos UV hace que no sea necesario cubrirlas.
Otra razón para tener en cuenta los materiales alternativos es la aparición de vehículos eléctricos que proporcionan una oportunidad obvia dada la necesidad de minimizar el peso al máximo posible para alargar la vida de la batería. Aunque cualquier vehículo puede utilizar materiales ligeros, son especialmente importantes para los vehículos eléctricos, híbridos eléctricos e híbridos eléctricos enchufables. El uso de materiales ligeros en estos vehículos puede compensar el peso de los sistemas de alimentación, como baterías y motores eléctricos, mejorar la eficiencia y aumentar su autonomía funcionando sólo con energía eléctrica. Como alternativa, el uso de materiales ligeros podría requerir una batería más pequeña y de menor coste sin que variase la autonomía de los vehículos enchufables funcionando sólo con energía eléctrica.
El desarrollo de vehículos eléctricos es también una respuesta a la presión extrema que sufre el sector del automóvil para reducir las emisiones de escape con los duros objetivos de cumplimiento obligatorio que son cada vez más inminentes. Para 2020 y 2025, los fabricantes europeos deberán reducir las emisiones medias de su flota por debajo de 95 g de CO2/km y 75 g de CO2/km, respectivamente. Por tanto, los fabricantes se enfrentan a un verdadero desafío y el incumplimiento de estos objetivos podría ser catastrófico y acarrear importantes multas basadas en cada coche producido que incumpla la directiva.
La clave para cumplir las nuevas normas es utilizar materiales ligeros innovadores dentro del chasis del vehículo, aunque el reto es convencer a los diseñadores, fabricantes y compradores de vehículos de que pueden ofrecer los niveles necesarios de resistencia, estabilidad y seguridad. No obstante, la rigidez y la resistencia a la flexión de Arpro aumentan exponencialmente con el grosor del núcleo, lo que reduce firmemente las preocupaciones en este aspecto. Por otro lado, debido a la capacidad de integración de la función ‘inteligente’ —aislamientos, conductos de ventilación y puntos de montaje integrados— puede crearse una solución altamente eficiente y ligera con una mínima inversión de capital. Fijar el producto final también es sencillo, ya que a diferencia de algunos productos apanalados, puede ser sujetado, adherido, soldado por puntos o atado según los requisitos de la aplicación.