Micromecanismos de fallo de aceros estructurales durante la galvanización en caliente
Introducción
El fallo durante la galvanización de aceros estructurales es un problema que se detectó por primera vez en Alemania en los años 50[1], aunque es en los años 80 cuando desde Japón empiezan a hacerse estudios sistemáticos sobre el mismo [2]. El fallo consiste en la aparición de grietas en aceros estructurales hasta 500 MPa de límite elástico durante su galvanización en caliente en discontinuo (consistente en la inmersión de la pieza en Zn líquido a 450°C). Dichos fallos son ocasionales y asistemáticos y sólo ocurren durante la galvanización. Es decir, una pieza de acero que no se haya fragilizado durante el proceso de galvanización no se fragilizará después y presenta las mismas propiedades que una pieza sin galvanizar.
Este fallo no debe confundirse con el fallo por hidrógeno que aparece en piezas galvanizadas de acero de alta resistencia (límite elástico > 600 MPa), cuyo origen es el hidrógeno absorbido durante las fases de decapado y fluxado (inmersiones en ácido) de preparación superficial previa a la galvanización. Este tipo de fallos ha sido convenientemente tratado por las normas ASTM, especialmente la ASTM A123 [3] (cuya primera versión surgió en 1928) e ISO, especialmente la ISO 1461 [4]. Los aceros estructurales afectados por fallo durante la galvanización tienen estructura ferrítico perlítica, poco susceptibles a fragilización por hidrógeno. Además, Donnay ha demostrado que un aumento de la agresividad del decapado apenas tiene influencia en el aumento del fallo durante la galvanización de los aceros estructurales, gracias a los inhibidores utilizados habitualmente en dicha etapa [5].
A partir de los años 90 se produjo un repunte de los casos de fallo durante la galvanización, en paralelo a la aparición de nuevos baños de galvanización, que además del aditivo habitual de un 1% de Pb en el baño de Zn, incluían un 1% de Sn y un 0,1% de Bi, que se utilizaban para controlar mejor el espesor de los recubrimientos de Zn cuando se galvanizaban aceros calmados al Si, procedentes de horno eléctrico de arco. A raíz de este aumento en los casos de fallo, en Norteamérica y en Europa aparecieron grandes proyectos de investigación que trataron de resolver el problema [5-9].
Estos proyectos se centraron mucho en resolver el problema a gran escala, en eliminar las grietas de los componentes estructurales. Aunque han hecho avances en la comprensión de los fenómenos que dan lugar al fallo durante la galvanización, estableciendo que se trata de un proceso de corrosión bajo tensión debido a metal líquido, en el que no está clara la influencia del hidrógeno procedente de las etapas previas a la galvanización (el decapado y el fluxado), no han sido capaces de elaborar un modelo que explique los micromecanismos por los que tiene lugar el fallo durante la galvanización.
La presentación de ese modelo es el objetivo de este artículo, basándose en el trabajo experimental de años ya expuesto por los autores en otros artículos [10-13], en una Tesis Doctoral [14], y también en otras fuentes bibliográficas independientes.
MODELO DE MECANISMO DE FALLO DURANTE LA GALVANIZACIÓN EN CALIENTE
Se trata de un modelo por etapas, que explica cómo ocurre el fallo durante la galvanización desde el comienzo del fluxado (etapa inmediatamente previa a la inmersión en Zn líquido) hasta la parada de fisura o rotura total de la pieza. Se tienen en cuenta, además, dos casos. Aquel en el que el baño de galvanización tiene un contenido en Sn mayor del 0,5% y aquel en el que el contenido del baño en dicho elemento es menor a ese 0,5%. A continuación se realiza la presentación de las etapas del modelo.
2.1. Fluxado
En la Figura 1 se representa esquemáticamente lo que ocurre en la etapa de fluxado.
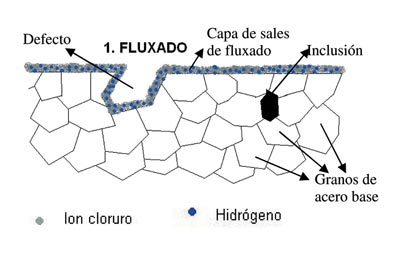
En contra de lo que se creía habitualmente en industria, los autores demostraron en [11] que las reacciones de activación entre las sales de fluxado y el acero base que son necesarias para la galvanización, descritas en [15], tienen lugar desde el instante inicial del fluxado, a temperatura ligeramente superior a la ambiente, no en la galvanización a 45°C. Estas reacciones producen la formación de depósitos de fases Fe-Zn en la superficie del acero, aumento de la rugosidad superficial del mismo, lo que puede ser el origen de futuros defectos a partir de los cuales se produzca fisuración, y un aumento de la concentración de hidrógeno en la superficie del acero. Según el mismo artículo [11], no parece que el hidrógeno pase en una cantidad significativa al interior del acero debido al corto tiempo del fluxado (10-15 minutos) y a la estructura ferrítico perlítica del acero.
2.2. Inmersión en el baño de galvanización
En la Figura 2 se muestra de forma esquemática lo que ocurre en esta segunda fase del modelo.
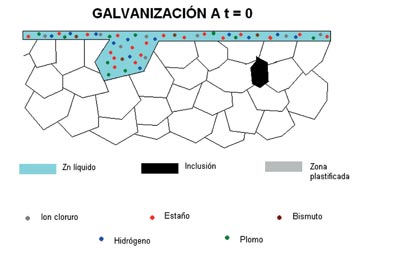
El contacto del acero base con el metal líquido a 45 °C tiene tres efectos inmediatos que pueden afectar al proceso de fallo durante la galvanización:
a) El acero estructural aumenta su temperatura de forma brusca, con lo que, como se demostró en [11], se reducen sus valores de resistencia y ductilidad hasta aproximadamente un 30 %.
b) Tal y como describe la bibliografía técnica sobre el tema [15, 16], las sales de fluxado al pasar a 450 °C en Zn líquido se “queman”, acelerándose las reacciones comentadas en el punto 2.1 anterior. Sin embargo, tal y como se muestra en [13, 14], es habitual que queden restos de sales de fluxado sin reaccionar, quedando por lo tanto grandes cantidades de hidrógeno en zonas adyacentes a defectos en la superficie del acero a galvanizar, que continuarán acelerando las reacciones Fe-Zn en esos puntos, tal y como hacen en el proceso global de galvanización.
c) Según Feldmann [9], debido a que el acero está a una temperatura mucho más fría que el metal líquido, de forma temporal se produce una “congelación” del metal líquido justo en contacto con el acero base, hasta que el dicho acero alcance la temperatura del baño. Este efecto de congelación puede ser beneficioso ya que evita el contacto entre el acero base y el metal líquido fragilizante durante un tiempo en el que tienen lugar importantes tensiones en el acero base debido al choque térmico. En los pasos siguientes de este modelo se tomará el caso desfavorable (del lado de la seguridad) en el que ese efecto de congelación no es relevante para evitar el fallo durante la galvanización.
2.3. Formación de fases Fe-Zn
En la Figura 3 se muestra de forma esquemática lo que ocurre en la tercera etapa del modelo.
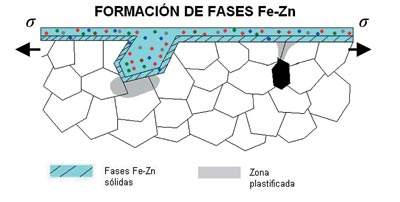
En este paso lo que se produce es la formación habitual de las fases Fe-Zn, según lo expuesto por Marder [16], mientras tiene lugar una tensión en el sistema por choque térmico. La baja solubilidad de los elementos de bajo punto de fusión del baño de galvanización (Pb, Sn, Bi, etc.) en dichas fases Fe-Zn [17] hace que en la parte central de los pequeños defectos del acero base suba la concentración de dichos elementos, formándose un metal líquido de punto de fusión más bajo y, por lo tanto, más corrosivo. Esto se ha comprobado experimentalmente en diversos casos reales [5] y en laboratorio [13]. Véase un ejemplo en la Figura 4.
![Figura 4. Distribución de fases del recubrimiento de galvanización que rellena una fisura del acero [14] Figura 4. Distribución de fases del recubrimiento de galvanización que rellena una fisura del acero [14]](https://img.interempresas.net/fotos/952726.jpeg)
También se ha comprobado en [12] que, a pesar de la tensión del sistema, mientras no se produzca que el factor de intensidad de tensiones KI no supere el umbral KIscc o, aun superándolo, no sea creciente, no se producirá la rotura de las fases Fe-Zn y no se producirá la propagación del defecto o fisura inicial.
2.4. Rotura de las fases Fe-Zn
En la Figura 5 se muestra de forma esquemática lo que ocurre en la cuarta etapa del modelo.
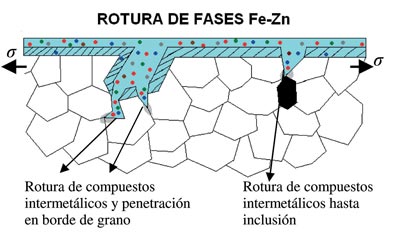
Si se producen las condiciones citadas en el apartado anterior, que el factor de intensidad de tensiones KI supere al valor umbral (para que se puedan romper las fases Fe-Zn) y sea creciente (para que se abran vías de penetración de más metal líquido), se producirá la propagación de la fisura. Debido a que KI es creciente, y siguiendo las teorías clásicas de fragilización por metal líquido [18], que aquí se asumen, se producirá un enromamiento del frente de fisura que permita la aparición de más metal base fresco, preferentemente en borde de grano (en este caso borde de subgrano ferrítico [12, 13]), que reaccionará con más metal líquido procedente de la fisura abierta. El proceso de fisuración continuará repitiendo de forma cíclica los pasos 3 y 4 del modelo, tal y como muestra la Figura 9 al final del artículo, mientras KI sea superior al umbral, creciente y además la concentración de Sn en el baño de galvanización o en el frente de fisura sea menor a 0,5%.
2.5. Formación del compuesto FeSn
En la Figura 6 se muestra de forma esquemática la quinta etapa del modelo.
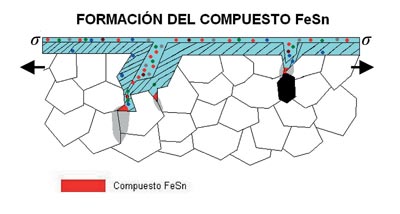
Según la información que nos da el diagrama de fases ternario Fe-Zn-Sn a 450 °C [19], si se supera la concentración de 0,5% de Sn en un sistema Fe-Zn, se produce un equilibrio entre el Fe, la fase Fe-Zn denominada y el compuesto intermetálico FeSn. Por lo tanto, en el fondo de un defecto o fisura de un acero que se está galvanizando, donde tiende a aumentar la concentración de Sn, según lo explicado en 2.3, llegará un momento en que se empiece a formar el compuesto FeSn en vez de las fases habituales Fe-Zn. Esto se ha comprobado experimentalmente, como puede apreciarse en la Figura 7.
![Figura 7. a) Micrografía y b) Análisis del fondo de fisura de un caso real de fallo durante la galvanización[13] Figura 7. a) Micrografía y b) Análisis del fondo de fisura de un caso real de fallo durante la galvanización[13]](https://img.interempresas.net/fotos/952729.jpeg)
2.6. Rotura del compuesto FeSn
En la Figura 8 se muestra de forma esquemática la sexta y última etapa del modelo de fallo durante la galvanización.
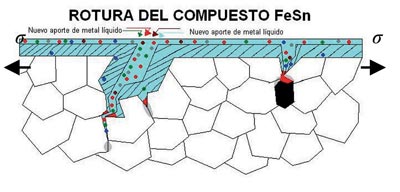
El FeSn es un material de una dureza de 500-700 HV, mayor a la de las fases Fe-Zn, y cristaliza en un sistema hexagonal muy rígido [20], por lo que teóricamente ha de presentar una mayor fragilidad que dichas fases Fe- Zn en el proceso de fallo durante la galvanización. El efecto, según los experimentos presentados en [11, 12], la tenacidad a fractura de probetas CT de acero sumergidos en baño de Zn líquido a 450 °C con un 1% de Sn era menor a la tenacidad de las probetas sumergidas en un baño sin Sn o, alternativamente, el fallo se producía en un tiempo menor. Al examinar las fractografías de las probetas ensayadas en baño con un 1% Sn aparecía el compuesto FeSn, y donde no se había utilizado Sn sólo aparecían fases Fe-Zn.
Como se comenta en el apartado 2.4 y en la Figura 9 al final del artículo, en un fallo durante la galvanización en un baño con más de un 0,5% de Sn la fisuración continuará repitiendo de forma cíclica los pasos 5 y 6 del modelo hasta que se produzca la rotura total de la pieza o hasta que KI deje de ser creciente.
Conclusiones y recomendaciones
En este artículo se ha presentado un modelo de mecanismo de fallo durante la galvanización, cuyo resumen se muestra en la Figura 9 a continuación. Se trata de un modelo de corrosión bajo tensión debido a metal líquido, en el que el hidrógeno actúa como catalizador, es decir, acelerante del fallo. Se consideran dos casos. El primero de ellos es que el baño de galvanización tenga menos de un 0,5% de Sn, en cuyo caso sólo se han de aplicar los 4 primeros pasos del modelo, y el segundo es que el baño tenga más de un 0,5% de Sn, caso en que hay que aplicar los 6 pasos.
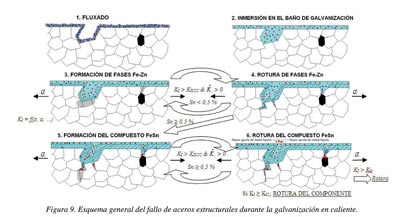
Se impone como condicionantes mecánicos que para se produzca el fallo el factor de intensidad de tensiones KI ha de ser mayor a un umbral KIscc y además ha de ser creciente. Estos dos condicionantes, junto con la composición del baño de galvanización en Sn, sirven como criterio para evaluar si las recomendaciones dadas a los galvanizadores para evitar el fallo durante la galvanización, recomendaciones que venían de la experiencia en experimentos a gran escala, están fundadas teóricamente o no. Cualquier recomendación encontrada en cualquier guía (por ejemplo [21, 22]) ha de facilitar que KI deje de ser creciente o mayor que un umbral.
En general las recomendaciones en [21, 22] y de otras guías similares [5], aunque no se dedujeron del estudio de los micromecanismos de fallo sino de experiencias a gran escala sí cumplen con las citadas condiciones. A estas recomendaciones habría que añadir las siguientes específicas del modelo desarrollado en este artículo.
- No superar un contenido en Sn del baño mayor de 0,5% en la galvanización de estructuras de responsabilidad. Otras recomendaciones ponían este límite entre un 0,15-0,3% para el Sn, por lo que se quedaban del lado de la seguridad.
- Limitar el contenido de Pb a no más del 1% y eliminar el Bi en estructuras con responsabilidad.
- Evitar fluxados agresivos que, como se ha visto en este artículo, agravan el problema del fallo durante la galvanización.
Y, aunque estas recomendaciones ya venían en otras recopilaciones, conviene insistir en que se han de elegir aceros de alto grado de tenacidad, con superficies lo más lisas posible y no prolongar el contacto del metal base con el Zn líquido más allá del tiempo necesario para que el recubrimiento alcance el mínimo exigido por la norma ISO 1461.
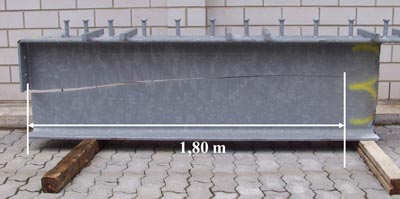
Agradecimientos
Los autores desean agradecer a la Comisión Europea y al Ministerio de Ciencia e Innovación Español (actual Ministerio de Economía y Competitividad) la financiación del proyecto FAMEGA, que constituye el trabajo base para la realización de este modelo. También desea agradecer la ayuda y el material prestado a las empresas Corus-Tata y Arcelor-Mittal y al resto de socios del proyecto Famega.
Referencias
[1] Rädeker, W., “Die Erzuegung von Spannugsrissen in Stahl durch flüssiges Zink”. “Stahl und Eisen”, 73, No.10. Dusseldorf, Alemania, 1953. pp. 654-658.
[2] Kikuchi, M. Liquid Metal Embrittlement of Steels during Hot Dip Galvanizing. En Tetsu to hagane (Iron and Steel). Vol. 68, núm. 14. Japón, 1982. pp. 1870-1879.
[3] ASTM A123/A123M-12. Standard Specification for Zinc (Hot-Dip Galvanized) Coatings on Iron and Steel Products. ASTM International. 8 pp., Pennsylvania, USA, Mayo 2009.
[4] Norma UNE-EN ISO 1461:2010. Recubrimientos galvanizados en caliente sobre productos acabados de hierro y acero. Especificaciones y métodos de ensayo. AENOR. 21 pp., Madrid, Enero 2010.
[5] Rudd, W.J., Donnay, B., Gutiérrez-Solana, F., et al. FAMEGA. Failure Mechanisms During Galvanizing. Final Report. Research Fund for Coal and Steel (RFCS) Joint report EUR-23195-EN 2008. European Commission. 110 pp., Bruselas, 2007.
[6] Kinstler, T.J. Current Knowledge of the Cracking of Steels During Galvanizing. A Synthesis of the Avaliable Technical Literature and Collective Experience for the American Institute of Steel Construction. En http://www.aisc.org/Content/ContentGroups/Engineering_and_Research/Research1/Final5906.pdf. Galvascience LLC. 79 pp., Springville, USA, 2005.
[7] Elboujdaini, M., Tyson, W.R., et al. ZM-396: Control of Cracking During Galvanised Structurals: Final Report Phase 2, 3 and 4b. CANMET, Metals Technology Laboratories, International Lead Zinc Organisation Inc. Canadá, 1995-1997.
[8] James, M. N. International Lead Zinc Research Organisation Programme ZC-21-1: Galvanizing High Performance Steels for the Construction Market. European General Galvanizers Association Assembly 2007. Edimburgo, Reino Unido, 12-14 de Junio 2007. pp. 90-105.
[9] Feldmann, M., Pinger, T., Schäfer, D., Pope, R., Smith, W., Sedlacek, G. Hot-Dip-Zinc-Coating of Prefabricated Structural Steel Components. Background Document in Support to the Implementation, Harmonization and further Development of the Eurocodes. Joint Report. JRCEuropean Commission cooperation agreement for the evolution of the Eurocode 3 (programme of CEN/TC 250). EUR 24266 EN-2010. 110 páginas.
[10] Carpio, J., Casado, J.A, Álvarez, J.A., Gutiérrez-Solana, F. Design and Validation of a Device for Tensile and Toughness Tests of Specimens Immersed in Liquid Zinc. Engineering Failure Analysis. Vol. 15-3. Elsevier. Cambridge, Reino Unido, 2008. pp. 229-236.
[11] Carpio, J., Casado, J.A, Álvarez, J.A., Gutiérrez-Solana, F. Environmental factors in failure during hot-dip galvanizing. Engineering Failure Analysis. Vol. 16-2. Elsevier. Cambridge, Reino Unido, 2009. pp. 585-595.
[12] Carpio, J., Casado, J.A, Álvarez, J.A., Méndez, D., Gutiérrez-Solana, F. Stress corrosión cracking of structural steels inmersed in hot-dip galvanizing baths. Engineering Failure Analysis. Vol. 17-1. Elsevier. Cambridge, Reino Unido, 2010. pp. 19-27.
[13] Carpio, J., Casado, J.A, Álvarez, J.A., Méndez, D., Gutiérrez-Solana, F. Estudio microscópico del fallo durante la galvanización: casos reales y de laboratorio. XXXI Encuentro del Grupo Español de Fractura. San Lorenzo del Escorial, España. 6 páginas, 2014.
[14] Carpio, J., Mecanismo de fallo de aceros estructurales durante la galvanización en caliente. PhD. Thesis. 339 páginas. Santander, España, 2013.
[15] “Fluxing bathes”. En www.fib.be/en/products/rm_pages/00125b.htm. Le Fur Industriel Belge. Bélgica, 2005.
[16] Marder, A.R. The Metallurgy of Zn-coated Steel. En Progress in Materials Science. Vol. 45. Pergamon. Pennsylvania, USA, 2000. pp. 191-271.
[17] http://www.crct.polymtl.ca/FACT/documentation/SG TE/SGTE_Figs.htm%20. Center for Researck in Computational Thermochemistry. Montreal, Canadá.
[18] Pugh, E.N. Stress Corrosion Cracking and Hydrogen Embrittlement of Iron Based Alloys. National Association of Corrosion Engineers, 1977. P. 37.
[19] Avettand-Fénöel, M.N., David, N., Reumont, G., Fiorani, J.M., Vilasi, M., Perrot, P. Assessment of the Fe-Sn-Zn Phase Diagram at 450°C. Application to the Batch Galvanizing. Journal of Thermal Analysis and Calorimetry. Vol. 90-2. Springer. Nueva York, 2007. pp. 329-332.
[20] Giefers, H., Nicol, M. High Pressure X-ray Difraction Study of all Fe-Sn Intermetallic Compounds and one Fe-Sn Solid Solution. Journal of Alloys and Compounds. Vol. 422. Elsevier. 2006. pp. 132-144.
[21] Galvanizing Structural Steelwork. An Approach to the Management of Liquid Metal Assisted Cracking. The British Constructional Steelwork Association Ltd. Londres, Reino Unido, 2005. 20 páginas.
[22] Recommendations for the Prevention of Cracking in Hot Dip Galvanized Steel Structures. Draft report. German Steel Union Industrial Association of Hot Dip Galvanizers. Germany, 2005. 4 pages.