Sistemas alternativos de lubricación para taladrados profundos y roscados en fundición gris
Teniendo en cuenta el proceso de mecanizado desde los puntos de vista económico y medioambiental, la industria evoluciona hacia nuevos procesos y métodos de lubricación. El paso más lógico en esta evolución ha sido el mecanizado en seco, esto es, el mecanizado sin fluidos de corte.
Mecanizado en seco y sistemas de mínima cantidad de lubricante
El taladrado, escariado y roscado con macho en cambio manifiestan serios inconvenientes al ser realizados en seco puesto que no son operaciones tan accesibles como las anteriores y aparecen problemas de evacuación de viruta y calentamiento.
Una solución para estos problemas es la utilización de sistemas de lubricación/refrigeración basados en la inyección de un chorro de aire a alta velocidad con partículas de aceite biodegradable en suspensión. Esta técnica se denomina MQL (Minimum Quantity of Lubricant). Debido a que la cantidad de lubricante utilizada es mínima (0.5-50 ml/h), tanto la herramienta como la pieza permanecen secas con lo que los costes en lubricantes y tratamiento de residuos se minimizan obteniendo un proceso ecológico y económico como en el mecanizado totalmente en seco.
A pesar de estas ventajas, el sistema de lubricación MQL no cumple de la misma forma con las funciones de los fluidos de corte tradicionales. Este sistema alternativo dota al corte de una buena lubricación pero la refrigeración de la pieza-herramienta y el transporte de viruta son menos eficientes que con los fluidos tradicionales, por lo que exige nuevos desarrollos en recubrimientos, herramientas y estrategias de mecanizado para suplir estas carencias. Por otra parte, la variedad de sistemas de MQL existentes en el mercado hace necesario la realización de estudios analizando la compatibilidad de éstos a la máquina y operación de mecanizado a realizar. Estos sistemas se pueden dividir en dos grandes grupos; los de aplicación externa, donde el suministro de la mezcla aire-aceite se realiza a través de boquillas direccionadas hacia la zona de corte, y los de aplicación interna, donde la mezcla se suministra a través de la herramienta.
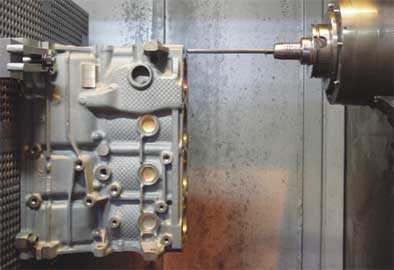
Nueva estrategia para el mecanizado ecológico del cárter motor
Ubicación de los mecanizados del cárter motor analizados
Actualmente, el mecanizado de estos orificios se realiza utilizando gran cantidad de fluido refrigerante de base acuosa y debido a la gran profundidad de los orificios a taladrar, primeramente se realiza un taladrado de 10.6 mm de diámetro y 80 mm de profundidad que sirve de guía para el siguiente taladrado de 10.5 mm, que profundiza el anterior orificio hasta lograr 133 mm de profundidad. Posteriormente se realiza un retaladrado de 12.7 mm de diámetro y 90 mm de profundidad y finalmente, en la parte no retaladrada y más profunda, se realiza un roscado de M12.
Ideko sugiere para este proceso un mecanizado con sistema de lubricación MQL combinada con una nueva estrategia de mecanizado para favorecer el proceso de corte, reducir el tiempo de mecanizado y eliminar la generación de residuos derivados de la utilización de los fluidos de corte tradicionales. Se trata de mecanizar primeramente un orificio de 10.5 mm de diámetro y 133 mm de profundidad (12x&) para posteriormente retaladrar el orificio con una broca de 12.7 mm y 90 mm de profundidad (7x&). Finalmente, se realiza el roscado con macho rígido de M12 en la parte no retaladrada.
Para ello se han analizado diferentes tipos de metal duro y diferentes geometrías de herramientas de la empresa herramentista Gühring y la influencia del recubrimiento multicapa nACO-MLH+Movic de la empresa Platit. Se ha utilizado el sistema de MQL de aplicación interna LubriLean Vario de la casa Vogel y el aceite recomendado por esta misma casa Lubrioil, con cualidades esencialmente lubricantes. Por último señalar que las pruebas se han realizado en las instalaciones de Ideko, en el centro de mecanizado DS630 fabricado por D+S Sistemas, empresa integrante del Grupo Danobat.
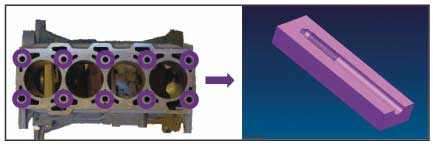
Influencia del sustrato de herramienta
Duración de vida de herramientas con diferentes tipos de metal duro
Se examinó el desgaste medio (VBb) que sufrieron los filos de corte de cada herramienta y el material que mejor respuesta mostró fue el que presentaba mayor tamaño de grano y menor % de cobalto, el DK255F. Estas características parecen favorecer la respuesta de la herramienta de DK255F ante el desgaste, por lo que se seleccionó este sustrato como base para las siguientes herramientas a analizar.
Influencia de la geometría de la herramienta y el recubrimiento en el taladrado profundo
Vida de herramienta con brocas helicoidales y rectas, con y sin recubrimiento
No cabe duda que la herramienta más adecuada para mecanizar este material es la herramienta recta, no solo por la duración de vida lograda (hasta un 200% de mejora en herramientas no recubiertas) sino también por su comportamiento respecto a la estabilidad durante el proceso.
La herramienta helicoidal no recubierta mecaniza con acusadas vibraciones desde el comienzo, provocando un acabado rugoso inicial en el orificio que empeora notablemente la calidad superficial del orificio y a su vez, deteriora la herramienta hasta que se produce la rotura lateral del filo. El desgaste de la broca recta no recubierta en cambio se produce gracias a una combinación de desgaste y rotura del filo.
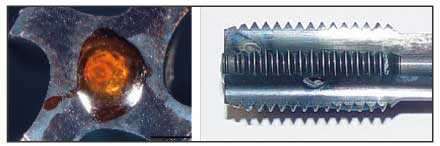
Rotura y desgaste en brocas no recubiertas de 10.5 mm de diámetro
Por otra parte, la utilización del recubrimiento nACO-MLH+Movic de Platit mejoró notablemente el comportamiento de las herramientas en general causando un aumento de vida de las brocas de un 375% en las helicoidales, y de un 125% en las rectas. Asimismo, las herramientas recubiertas a diferencia de las no recubiertas, han sufrido un desgaste progresivo del filo de corte principal y lateral hasta que se han roto por torsión, comportamiento que denota un proceso de corte más estable.
Posteriormente se analizaron brocas helicoidales de 12.7 mm de diámetro que retaladraban los orificios de 10.5 mm de diámetro hasta una profundidad de 90 mm (7x&). El caudal de aceite aplicado con el MQL fue de 20 ml/h y las condiciones de corte las mismas que en las brocas de 10.5 mm de diámetro. Los resultados obtenidos muestran que el uso del recubrimiento provoca la misma tendencia al aumento de vida que en las herramientas de diámetro 10.5 mm, aunque la mejoría no resulta tan acusada. Con la herramienta sin recubrir se han mecanizado 26 m y el desgaste del filo principal ha sido el que ha determinado la vida de la herramienta, llegando a los 500 mm. La herramienta recubierta en cambio ha conseguido mecanizar 53 m y se ha dado por concluido el ensayo al rebasar el desgaste del filo de corte lateral los 1500 mm.
Desgaste en brocas recubiertas y sin recubrir de 12.7 mm de diámetro
El retaladrado resulta una operación menos severa que el taladrado en macizo porque evacúa una menor cantidad de material y no trabaja todo el filo de corte. Además, esta herramienta posée 1 diente de corte más que la broca de 10.5 mm lo que le confiere mayor rígidez y estabilidad en el corte. Consecuentemente, este mecanizado no ha supuesto problema alguno para la herramienta y sería posible un aumento en las condiciones de corte o reducción del caudal de aceite suministrado para optimizar el proceso.
Roscado con macho rígido
Cambio de ubicación en los orificios de refrigeración de los machos rígidos
Conclusiones
En cuanto a la geometría de la herramienta, las brocas rectas son más productivas que las helicoidales para el taladrado de fundición con MQL debido a su mayor duración de vida. Las herramientas helicoidales producen vibraciones lo que repercute negativamente en el proceso acortando la vida de la herramienta y empeorando notablemente la calidad del orificio mecanizado.
Por otra parte, el recubrimiento nACO-MLH+Movic mejora el rendimiento de las brocas tanto en las de diámetro de 10.5 mm como en las de 12.7 mm llegando incluso a triplicar la vida útil de la herramienta en algunos casos. Produce un efecto lubricante-refrigerante en la herramienta que ayuda de una forma muy efectiva a prolongar su vida.
Finalmente detacar que la ubicación de los orificios de refrigeración para el MQL es fundamental en los machos de roscar. De esto depende en gran medida, la eficacia de una herramienta a la hora de mecanizar, sobre todo con sistemas de lubricación MQL.