Avenços recents en els processos de fabricació ràpida i tractament superficial amb làser
La neteja és un altre camp d'aplicació interessant de la tecnologia làser. Els últims desenvolupaments se centren en la neteja de dispositius electrònics, en els quals cal eliminar de laques soldables, contaminació, residus polimèrics i capes d'òxid de la superfície. Per a això, s'utilitza radiació làser polsada, amb polsos de 10 a 250 ns de durada. A causa de l'alta intensitat i al curt interval d'interacció, els recobriments no metàl·lics s'evaporen, mentre que la superfície metàl·lica del substrat roman intacta.
El polit de superfícies és un nou camp d'aplicació per als làsers. En aquest procés, la rugositat superficial, originada per exemple després d'un procés de fressat o desbarbat, s'allisen mitjançant la fusió d'una fina capa de material. La velocitat d'aquest procés sol situar entre 0,2 i 5 cm2/min. Aquesta tècnica podria aplicar-se al polit de motlles d'injecció i de fosa ja instruments mèdics.
El procés de fosa selectiu per làser (SLM) pot utilitzar per a la fabricació directa de peces de metall a partir de materials en sèrie. Gràcies a una tècnica de fosa complet del material en pols, es poden aconseguir densitats properes al 100 per cent, amb bones propietats mecàniques. Els materials que s'estan investigant són l'acer inoxidable 1.4404, l'acer per a eines 1.2343 i el titani TiA16V4. La utilització de la tècnica SLM ofereix avantatges en certs processos. La fabricació de prototips funcionals a partir de materials en sèrie permet estalviar temps en comparació amb els processos convencionals, com la fosa. Un altre exemple d'aquests avantatges és l'ús del procés SLM per a la fabricació de petits lots en sèrie o de peces individuals (per exemple, implants mèdics), amb gran flexibilitat i possibilitat de substituir altres processos convencionals.
Revestiment per làser
Fes làser
Broquet d'injecció de pols
Flux de pols
Peça base
Bany de fusió
Capa de revestiment
Zona de dilució
Zona tèrmicament afectada
Direcció d'escombrat

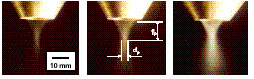
Slit size: mida de l'escletxa
injecció de pols coaxial contínua amb diferents mides d'escletxa
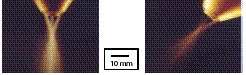
Conceptes sobre injecció de pols
En el revestiment mitjançant làser, el subministrament del material d'aportació és un dels factors més importants per al control del procés. No obstant això, els equips que existeixen en aquests moments en el mercat es van dissenyar per satisfer les necessitats dels centres de recerca i, per això, és necessari seguir treballant per crear equips que s'ajustin als requisits de la indústria en termes de fiabilitat, manteniment i vida útil. Existeixen tres tècniques d'injecció de pols:
• Injecció fora de l'eix (un únic flux de pols s'injecta de forma lateral al feix làser, Figura 1)
• Injecció coaxial contínua (s'injecta un flux de pols cònic que cobreix el feix làser, Figura 2)
• nyección coaxial discontínua (s'injecten tres o més fluxos de pols en sentit coaxial al feix, Figura 3).
La injecció de pols fora de l'eix és adequada per al revestiment de pistes amples. En el cas de pistes amb una amplada d'entre 0,5 i 5 mm, s'ha d'utilitzar una escletxa amb secció transversal circular amb un diàmetre d'entre 1,5 i 3,5 mm. Per pistes més amples (5-25 mm), s'ha d'utilitzar una escletxa amb secció transversal rectangular (per exemple, 1,5 x 15 mm2). La tècnica d'injecció fora de l'eix també pot utilitzar-se per el revestiment d'àrees de difícil accés. No obstant això, en la injecció fora de l'eix, el broquet toca posició lateral al feix làser i, per tant, no és una tècnica adequada per al revestiment tridimensional.
En el cas de la injecció coaxial contínua s'utilitza un flux de pols cònic que cobreix el feix làser. El flux de pols es caracteritza pels següents factors: diàmetre en el punt focal del flux de pols (dp) i distància entre el filtre i el punt focal (fp) (Figura 4). Al seu torn, aquests paràmetres depenen de la mida del broquet, el flux del gas portador, el cabal de pols i la mida de les partícules de pols. Tal i com es veu a la Figura 5, amb un filtre major, el diàmetre del punt focal augmenta. El mateix passa si el cabal de pols s'incrementa. Per la seva banda, la reducció en la grandària de les partícules provoca una disminució del diàmetre focal del flux. El diàmetre focal del flux de pols en la injecció coaxial contínua sol estar comprès entre 1 i 3 mm.
L'avantatge principal que presenta la injecció coaxial contínua enfront de la injecció fora de l'eix és que es pot utilitzar en revestiments tridimensionals. No obstant això, la inclinació del broquet està limitada. Com que l'homogeneïtat del con de pols depèn de la distribució de la pols dins de la cambra d'expansió del broquet, quan el filtre estigui inclinada, el flux es veurà afectat per la gravetat. S'ha comprovat que l'angle d'inclinació màxim, sense que la geometria del revestiment es vegi significativament afectada, és de 20 º.
En el cas de la injecció coaxial discontínua, tres o més fluxos de pols es distribueixen al voltant del feix làser per formar el punt focal del flux (Figura 3). El punt focal en aquests casos sol presentar un diàmetre d'entre 2,5 i 4 mm. El principal avantatge de la injecció coaxial discontínua és que pot utilitzar per a treballs de revestiment en tres dimensions i amb qualsevol angle d'inclinació del broquet. A la Figura 5 es mostra un flux de pols vertical i un flux amb una inclinació de 45 º. El punt focal amb prou feines es veu afectat per la inclinació. De fet, s'han provat broquets que permeten utilitzar un angle d'inclinació de 180 º (revestiment invers).
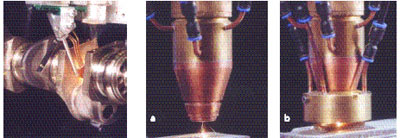
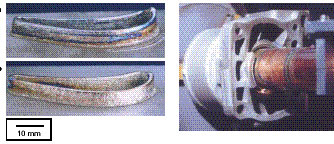
Fig 7: Revestiment de la superfície de rodament d'un cilindre del motor d'una motocicleta mitjançant una cavitat òptica amb unitat d'injecció integrada, material base i material d'aportació: aliatge AlSi
Aplicacions del revestiment làser
La tècnica del revestiment làser pot utilitzar potencialment en la reparació de coixinets de cigonyals de grans dimensions (camions i vaixells, grans motors de plantes elèctriques). A la Figura 4 es mostra el revestiment del coixinet del cigonyal d'un camió. Per dur a terme el revestiment de les vores del coixinet, cal utilitzar un filtre d'injecció estreta, de manera que en aquest cas no es pot utilitzar un sistema d'injecció coaxial.
La injecció coaxial s'utilitza, per exemple, en el sector aeroespacial per reacondicionar algunes peces dels motors de turbina, com les juntes o els extrems dels àleps. Com que en la majoria d'aquests casos la pista que es va a revestir és petita, la millor tècnica és la injecció coaxial, donat la grandària del punt focal del flux. A la Figura 5 es mostra el revestiment de l'extrem d'un àleps en TiA16V4 sobre un substrat llis. A més, mitjançant un revestiment addicional, es pot minimitzar l'oxidació de la peça (Figura 6). Encara que els tres tipus d'injecció de la pols poden utilitzar per a diferents aplicacions, els treballs especials exigeixen solucions especials. Un exemple de "treball especial" seria el revestiment d'una superfície interior. Quan el diàmetre de l'escletxa ha de ser menor d'uns 300 mm, no es pot utilitzar cap de les tres tècniques descrites. En aquest cas, s'ha d'utilitzar una cavitat òptica especial amb unitat d'injecció integrada. A la Figura 7 es mostra el revestiment de la superfície de rodament d'un cilindre del motor d'una motocicleta. La cavitat òptica pot utilitzar-se amb obertures amb un diàmetre mínim de fins a 50 mm.
El revestiment per làser es pot utilitzar per reparar àleps de turbines. En l'exemple de la imatge (Figura 8), en primer lloc, es va establir una cadena de procés cíclica. Per reparar un àleps mitjançant revestiment per làser, s'utilitzen les dades CAD de la peça per generar les trajectòries NC (pistes que es van a revestir). Si no es disposa de les dades CAD o si les dimensions del àleps han canviat amb l'ús, caldrà digitalitzar la geometria del lloi erosionat. Per calcular el volum a generar, també ha de digitalitzar un àleps de referència. Mitjançant un sistema CAD / CAM i macros CAD / CAM, aquest volum es divideix en capes i, a continuació, es creen les trajectòries NC ISO amb els paràmetres del procés (potència del làser, velocitat d'escombrat, solapament i estratègia d'ompliment o acumulació). Les trajectòries NC ISO es converteixen en trajectòries NC llegibles per una màquina en un pas de procés posterior. El programa NC generat es transfereix al sistema de control NC. Amb això obtenim un procés de revestiment per làser totalment automatitzat.
La modelització permet predir els resultats i és una fase essencial per entendre el procés i reduir el treball experimental. Les simulacions més fiables es basen en el mètode d'elements finits. Al ILT, es va crear un model en què es tenia en compte el flux de calor i massa dins del bany de fusió així com les dades de massa en la injecció de pols. Amb això, es pot simular la generació d'una ànima com la mostrada a la Figura 9. En aquests moments, el model s'està perfeccionant i s'utilitzarà per optimitzar les estratègies de revestiment per a reparacions.
La xapa d'acer sol protegir-se contra la corrosió mitjançant un galvanitzat en continu seguit d'un recobriment en bobina amb polímers (tècnica "Duplex"). No obstant això, quan posteriorment aquesta xapa es talla en un procés de fabricació, la superfície metàl·lica de les vores queda exposada a la corrosió i, per tant, es necessita un altre recobriment. Alguns experiments han demostrat que és possible revestir amb zinc i polímers mitjançant làser. Com que els polímers es descomponen a baixes temperatures, no es pot utilitzar una injecció directa (Figura 1). En aquests casos, es posa el feix làser per davant del flux de pols, escalfant la superfície de la vora de la xapa. Les partícules polimèriques es fonen per la transmissió de calor. A la Figura 10 es pot veure una mostra sotmesa a un assaig de 1.000 hores d'aspersió de sal: la part de la vora de la xapa que havia estat revestida mitjançant RILSAN (capa d'un gruix d'uns 0,2 mm) no mostra corrosió alguna. En el cas de recobriments de zinc (capa d'un gruix d'uns 10-60 _M) es van obtenir resultats similars.
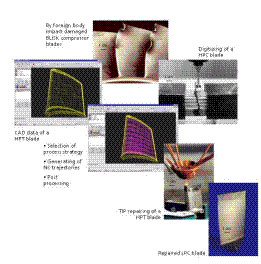
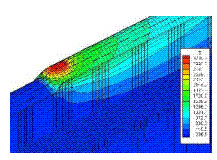
Neteja i polit amb làser
Per a la fabricació i muntatge final de dispositius electrònics són necessaris nombrosos processos de neteja i activació. Així, és necessari eliminar de la superfície laques soldables, contaminació, residus de polímers, capes d'òxid. En alguns processos posteriors, com les unions (soldat, unió per adherència) i revestiment (per exemple, galvanitzat), la neteja de les superfícies resulta especialment important. Les tècniques de neteja convencionals solen basar-se en processos químics o mecànics i, en molts casos, el processat i eliminació dels residus és car. D'altra banda, la tendència a la miniaturització exigeix l'ús de processos de neteja d'alta precisió. La tècnica làser elimina tots aquests inconvenients associats a les tècniques de neteja tradicionals. Depenent de les propietats d'absorció dels revestiments i dels materials de base, es poden utilitzar làsers premuts de CO2, Nd: YAG o d'excímeros amb polsos de 10 a 250 ns de durada. A causa de l'alta intensitat ia la curta interacció temporal, les capes de recobriment no metàl·liques s'evaporen, mentre que la superfície metàl·lica del substrat roman intacta. Un exemple de neteja de dispositius electrònics és l'escatar i descalcificació de taps petits (Figura 11).
Un altre camp d'aplicació del làser és el polit de superfícies (Figura 12). En aquest procés, la rugositat superficial, originada per exemple després d'un procés de fressat o desbarbat, s'allisen mitjançant la fusió d'una capa fina del material. L'altíssima precisió d'aquest procés evita que es produeixin arestes arrodonides o desviacions geomètriques. La velocitat sol situar entre 0,2 i 5 cm2/min en funció del material, la rugositat inicial i final exigida. Per dur a terme aquestes funcions, en les línies de producció és fàcil integrar un làser de Nd: YAG amb fibra, premut o continu. Alguns camps en els quals es podria aplicar aquesta tècnica són el polit de motlles d'injecció i de fosa o els instruments mèdics.
Fosa selectiva amb làser
En els últims anys (referències 7-11) han sorgit nombrosos processos de manufactura generativa (els anomenats processos de prototipatge ràpid). En general, en aquests processos s'utilitza un material o una composició específics. Per tal de superar aquesta limitació d'un material concret, Fraunhofer ILT i TRUMPF estan treballant en el desenvolupament d'un procés làser de funció selectiva o SLM (sigles de Selective Laser Melting). El punt de partida, igual que en els processos de fabricació generatius, és un model CAD 3D que es subdivideix en capes d'un gruix determinat. La peça final es crea mitjançant un procés repetitiu d'addició de capes, en el qual la informació sobre l'àrea i el contorn de cada capa es transfereixen mitjançant un feix láser.2343 o titani TiA16V4, per altra banda, el procés físic consisteix en una refosa completa de les capes de pols amb una unió metalúrgica entre les capes i una densitat d'aproximadament el 100% en un paso.2343 o titani TiA16V4, per altra banda, el procés físic consisteix en una refosa completa de les capes de pols amb una unió metalúrgica entre les capes i una densitat d'aproximadament el 100% en un paso.el 100% en un pas. Gràcies a aquestes característiques, el camp d'aplicació d'aquesta tecnologia ha pogut ampliar i estendre l'prototipat ràpid a la fabricació ràpida de peces funcionals i eines en sèrie. Amb els materials abans esmentats es pot obtenir una densitat propera al 100%. A més, gràcies a aquesta alta densitat, les peces SLM presenten bones propietats mecàniques. La rugositat i la precisió dimensional són factors decisius per a l'ús i acceptació del procés SLM en la indústria. En aquest sentit, la rugositat Rz de les mostres SLM se situa al voltant dels 30 i 40 º m i depèn principalment de l'estructura de les capes i de les partícules foses unides a la superfície de les peces.
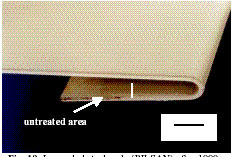
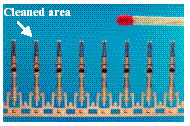
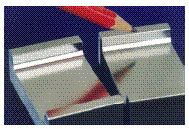
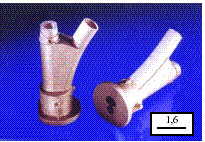
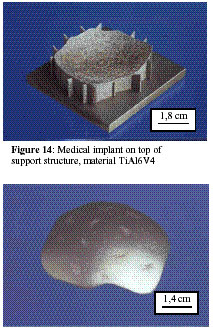
Fig 15: Implant metge després acabat superficial
Prototips funcionals
Els dos objectius més importants que s'han d'assolir amb un prototip funcional són: l'obtenció d'una peça amb unes propietats similars a les d'una produïda en sèrie i la reducció del temps de desenvolupament del producte. Tots dos requisits poden complir amb ajuda d'un procés SLM. Tot i que el temps de processament real d'una peça pugui ser més gran a causa del temps que requereix la producció de la capa, el procés complet de fabricació exigeix bastant menys temps que un procés convencional. En les tecnologies tradicionals, la producció de motlles és una fase que consumeix, especialment, molt de temps. Mitjançant l'ús de materials en pols és possible crear pràcticament qualsevol tipus de geometria a partir de dades CAD, d'aquesta manera, ja no són necessaris els materials semiacabats ni tampoc les fases de postprocessat (per exemple, la creació de programes de maquinat complexos o altres fases de fabricació). En resum: la fosa selectiva amb làser permet fabricar peces complexes en menys temps ia partir de materials amb propietats en sèrie.
Una aplicació del làser en el prototipat és la fabricació de peces que en general es creen en sèrie mitjançant emmotllament per injecció de metall (MIM). El procés SLM permetre disminuir el temps de fabricació de les peces de la Figura 13 de dues setmanes (inclosa la producció del motlle) a set hores. El material és acer inoxidable 1.4404, que també s'utilitza per a la producció de peces en sèrie.
Peces individuals
Un altre camp d'aplicació interessant de les tecnologies SLM és la producció d'implants mèdics. En els últims anys, l'ús de tecnologies de prototipat ràpid s'ha estès i convertit en alguna cosa comú en aquesta àrea. Mitjançant un programari especial CAD 3D es creen models a partir de les dades de CT (tomografia computeritzada) dels pacients i, a continuació, prenent com a base, es creen models mestres mitjançant tecnologies de prototipat com l'estereolitografia. Amb l'aplicació de la tecnologia SLM, va a sorgir una nova cadena de procés per als implants mèdics, una cadena en què es passarà directament de les dades CT a la fabricació de l'implant individual sense fases intermèdies com el modelatge. En aquesta cadena de fabricació, mitjançant un sistema de producció totalment automatitzat, com una màquina SLM, es podrien fabricar peces individuals o peces en petits lots a partir de diferents materials. L'implant que es veu a la Figura 14 i 15 ha estat fabricat en set hores, inclosos tots els processos posteriors, com l'eliminació de l'estructura de suport i l'acabat superficial. L'implant està fet en TiA16V4, un aliatge de titani amb excel lents característiques de biocompatibilitat.
La gairebé il limitada llibertat geomètrica ha obert noves opcions en el disseny dels canals de refrigeració, alguna cosa decisiu per rendibilitzar al màxim els processos de fabricació. El dissenyador de la refrigeració del motlle ja no s'ha de preocupar de facilitar els processos posteriors amb tecnologies convencionals (per exemple, trepat). Els canals de refrigeració poden dissenyar, per exemple, de manera que estiguin a la mateixa distància de la cavitat, adaptats a la forma de la cavitat (geometria lliure) i, en general, en àrees inaccessibles per als sistemes convencionals (Figura 16). La refrigeració de geometria lliure, en millorar el refredament, té un efecte directe en el temps del cicle d'injecció i en la qualitat de les peces. L'interval del cicle d'injecció disminueix amb el nombre de peces produït, de manera que el disseny de canals de refrigeració especials és una tècnica perfecta per als inserts de motlles en sèrie. En contra del que passa amb altres tecnologies de prototipat de metalls, el procés SLM permet fabricar aquests inserts a partir de materials en sèrie, és a dir, és un procés de fabricació ràpida. La possibilitat d'utilitzar canals de refrigeració de geometria lliure i l'estalvi de temps fan del procés SLM un suplement interessant per als mètodes de fabricació de motlles tradicionals, com l'EDM (maquinat per descàrrega elèctrica).
Conclusions
Els exemples exposats demostren el potencial del làser en els tractaments superficials. Un factor essencial és la millora de la qualitat del feix (per exemple, barra làser de Nd: YAG) i el desenvolupament de nous làsers d'alta eficiència (làser de Nd: YAG bombejat per díodes), avenços que ajudaran a reduir els costos i contribuiran a que el làser pugui utilitzar-se en un major nombre aplicacions. De cara al futur, la investigació s'ocuparà també de l'automatització i el control de processos, per augmentar la fiabilitat. D'altra banda, els avenços en la modelització serviran per comprendre millor el procés i reduir el temps d'estudi dels paràmetres.
L'ús de materials de sèrie en el procés SLM ofereix noves possibilitats en la creació de prototips i en la fabricació directa de peces. A més, la possibilitat de fabricar peces amb noves característiques geomètriques complementa els mètodes de fabricació convencionals en diversos camps (fabricació d'implants mèdics, usos aeroespacials i fabricació d'eines i motlles). Fraunhofer ILT va a continuar les seves investigacions en cooperació amb diversos socis industrials amb l'objectiu d'aconseguir geometries més complexes i ampliar la gamma de materials i materials compostos. Quant a la fabricació d'eines i motlles, l'objectiu és reduir els temps de manufactura, millorar la qualitat mitjançant refrigeració de geometria lliure i augmentar la vida útil de les peces.
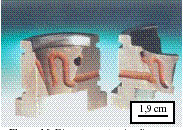
R eferències
El ministeri alemany d'Educació i Ciència (BMBF) ha finançat el projecte "Modulars Diodenlaser-Strahlwekzeuge" (MDS) i per la seva banda, la CE ha finançat del projecte "Awfors", mitjançant els quals s'han obtingut alguns dels resultats sobre revestiment per làser que s'han descrit abans.