Fatronik en la industrialización del proceso de unión Friction Stir Welding
(Fundación Fatronik)15/10/2004
Soldadura
A nivel nacional, Fatronik colabora con distintas empresas, como CAF, Irizar y MTorres para la explotación e implementación industrial de esta nueva técnica de unión. Además participa en el proyecto Eureka Eurostir, que aglutina a expertos y potenciales usuarios del proceso en Europa, con el objetivo de acelerar su industrialización.
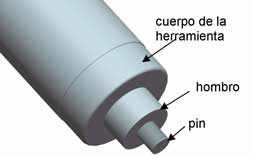
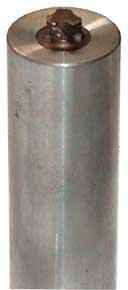
Descripción del proceso
Antes de pasar a una descripción más exhaustiva del proceso y para un mejor entendimiento del mismo, conviene conocer en primer lugar cómo es una herramienta típica de FSW. La herramienta de FSW consta básicamente de dos partes: el ‘pin’ o tetón y el ‘hombro’ o shoulder (Figura 1). El ‘pin’, que penetra completamente en el material a unir y discurre a lo largo de la línea de unión, suele estar perfilado de forma similar a una rosca o hélice, facilitando así el transporte del material a su alrededor, y contribuyendo a una mejor calidad de la soldadura. El ‘pin’ está contenido en el ‘hombro’, cuyas tres funciones básicas son: asegurar una perfecta colocación de la herramienta, proporcionar calor friccional a través de su rotación y la presión que ejerce contra la superficie, y evitar que el material plastificado salga a la superficie durante el proceso de soldadura. (Figura 1).
La soldadura por fricción se puede considerar como un proceso de ‘forjado y extrusión continuo’. La secuencia del proceso es sencilla (Figura 2a). La herramienta rotatoria se posiciona sobre la línea de unión (1), empieza a descender, entra en contacto con las piezas a unir aún frías (2), y aplica fuerza axial hasta que el ‘hombro’ contacta con la superficie de los componentes (3). La fricción entre la herramienta y las piezas a unir da origen a la energía de fricción, que conlleva un aumento de la temperatura de las piezas en las proximidades de la herramienta, justo hasta un valor por debajo de la temperatura de fusión de los componentes. En este rango de temperatura, la resistencia de las piezas disminuye hasta tal punto que pasa a un estado plástico. Debido a la rotación de la herramienta, el material “pastoso” se transporta alrededor de él, por una especie de “canal de extrusión” (región que se crea entre el material frío y aún sólido, y la herramienta rotatoria). Así, cuando empieza el movimiento de avance de la herramienta, se produce la mezcla de los dos componentes a lo largo de la línea de unión (4). Al final de la soldadura (5), la herramienta asciende y sale de la zona de unión (6). En la Figura 2b se pueden observar las fuerzas axiales que tienen lugar a lo largo de todo el proceso. En la Figura 2c se observa el aspecto de una unión realizada mediante esta técnica en perfiles planos de aluminio. (Figura 2ª, Figura 2b, Figura 2c)
Habitualmente, la herramienta suele estar inclinada en el eje Z hacia el lado contrario a la dirección de movimiento, facilitando así la presión del hombro y el flujo del material.
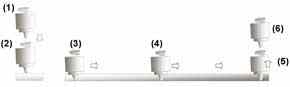
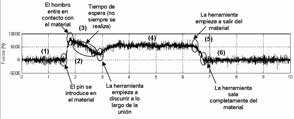
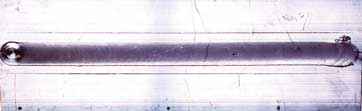
- Espesor de las chapas a soldar: t
- Profundidad de penetración del hombro de la herramienta: z1
- Ángulo de inclinación de la herramienta respecto a la normal de la superficie: a
- Velocidad de avance de la soldadura: Vf
- Velocidad de rotación de la herramienta: Vr
- Profundidad de penetración del pin: z2
- Diseño del pin y el hombro de la herramienta
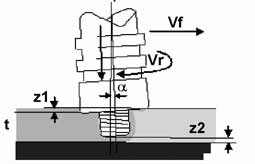
Ventajas
- Al tratarse de un método sin aporte de material y en estado sólido se evitan los problemas generados por el empleo de terial fundido (soldadura tradicional)
- Las uniones poseen unas buenas propiedades mecánicas y muy pocos defectos, incluso en materiales insoldables por otros métodos de soldadura, p.ej.: aluminios 7XXX, empleados en construcción aeronáutica.
- Las soldaduras sufren poca distorsión, un encogimiento bajo, y bajas tensiones residuales, por lo que no requieren un posterior tratamiento de rectificado ni enderezado.
- Se trata de un proceso de bajo coste cuya eficiencia energética es alta.
- Es una técnica automatizable y controlable y no requiere una preparación especial ni gran habilidad del soldador.
- Se puede emplear en distintas posiciones (horizontal, vertical, elevado…), a diferencia de otros procesos tradicionales, ya que no se ve influenciado por la gravedad.
- Se trata de un proceso seguro y respetuoso con el medio ambiente, ya que no genera humos, gases tóxicos, radiación ni chispas.
Aplicaciones
Son varios los tipos de materiales susceptibles de ser soldados mediante el proceso de Friction Stir Welding. Así, aunque a nivel industrial se emplea fundamentalmente para soldar aluminio (desde la serie 1xxx hasta la 7xxx), existen también aplicaciones en cobre y magnesio, y experiencias en laboratorio soldando titanio o acero con resultados satisfactorios.
Del mismo modo, existe gran diversidad en cuanto a sectores en los que se puede aplicar la soldadura por fricción. Entre otros, destacan: sector ferroviario (perfiles extrusionados para trenes con estructura de aluminio, etc.), marina y construcción naval (perfiles extrusionados, paneles para cubiertas, costados, mamparos, suelos…), construcción (puentes de aluminio, paneles fachada…), transporte terrestre (llantas de aluminio, brazos de suspensión, planchas a medida…), aeronáutico / aerospacial (alas y fuselajes, depósitos de combustible), otros (industria eléctrica, mobiliario, equipamientos de cocina,…).
Como se ve, el interés suscitado por esta nueva técnica ha sido muy relevante en muchos sectores, y ha puesto en evidencia la necesidad de una normativa específica del Friction Stir Welding. La consecución de un estándar que garantice la calidad del proceso será fundamental para acelerar aún más su explotación e implantación industrial. Actualmente existen grupos de trabajo en distintos organismos (IIW, AWS), que trabajan en la estandarización del proceso, prevista para el año 2006.
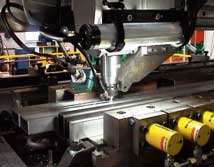
Máquinas adaptadas al proceso
El proceso exige máquinas de rigidez elevada, especialmente en el eje axial de la herramienta, con sistemas avanzados de control de la posición de la herramienta, que den medidas veraces de la posición real de la herramienta, con independencia de las deformaciones en la máquina y/o en los utillajes que se producen como consecuencia de las elevadas fuerzas del proceso.
Algunas soluciones pasan por medir directamente la posición de la herramienta mediante sensores láser o mediante sensores de contacto, en lugar de medir indirectamente la posición de la herramienta mediante reglas o encoders que desestiman el efecto de las deformaciones de la máquina en la posición real de la herramienta.
Otras soluciones más desarrolladas e implantadas es el del control indirecto de la posición de la herramienta mediante el control de la fuerza axial. Este parámetro está directamente relacionado con la posición de la herramienta en sentido axial. Este tipo de control permite soldar asegurando una fuerza en el sentido axial de la herramienta constante, parámetro directamente relacionado con la calidad de la unión.
Por último, otro aspecto fundamental es una refrigeración adecuada de la herramienta y del cabezal.
Una buena alternativa para este tipo de proceso son las máquinas de cinemática paralela, Sus características de alta rigidez y carga útil, sobre todo en el eje axial a la herramienta, las hacen muy interesantes para este proceso, tanto para soldaduras planas como para soldaduras en tres dimensiones.
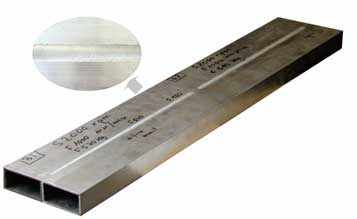
El Friction Stir Welding en Fatronik
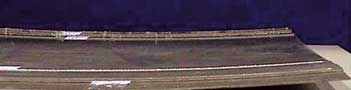
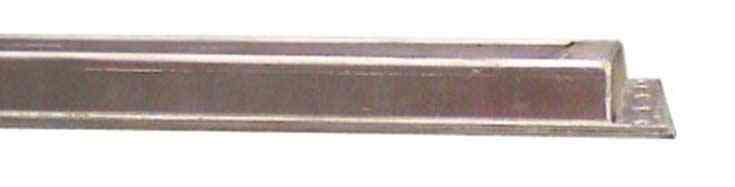
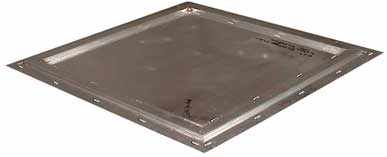
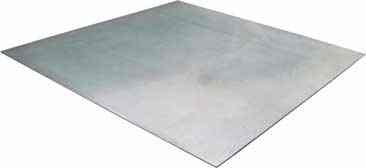
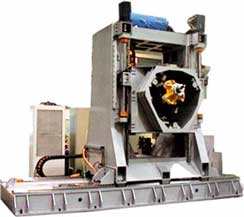
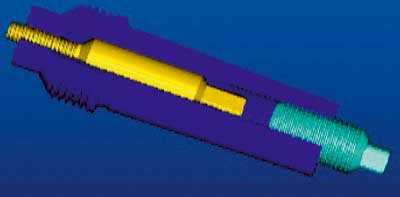
En los trabajos con la empresa Irizar, se ha realizado un estudio de viabilidad técnica y económica para fabricar mediante soldadura por fricción paneles laterales de la carrocería de los autocares. Se trata de soldar en solape nervios rigidizadores de aluminio, a una plancha también de aluminio de aleación muy blanda y de espesor reducido. Los requerimientos estéticos son elevados y exigen total planicidad en la cara vista, objetivos difíciles de conseguir debido a que la presión y temperatura del proceso de soldadura provoca fácilmente marcas en la plancha. (Figuras 7,8a, 8b, 8c).
Además de los sectores anteriores, Fatronik ha comenzado a trabajar recientemente en el sector aeronáutico, concretamente, realizando para MTorres un estudio de aplicabilidad del proceso de FSW en elementos estructurales aeronáuticos
Otras líneas de investigación de Fatronik relacionadas con este proceso trabajan en el desarrollo de maquinas de soldadura por fricción basadas en cinemática paralela. En este sentido, está trabajando en la adaptación de Demodril (Figura 9), uno de sus múltiples desarrollos en cinemática paralela, en un demostrador de soldadura por fricción: DEMOSTIR. DEMOSTIR integrará un sistema de monitorización y control basado en las fuerzas y en la temperatura del proceso. Para la medición de este último parámetro, Fatronik ha desarrollado junto con le empresa NECO una herramienta que permite medir la temperatura en un punto muy próximo al pin captada por un termopar de respuesta ultrarrápida que se trasmite al sistema de adquisición de datos mediante un sistema de telemetría. (Figura 9, Figura 10a, 10b).
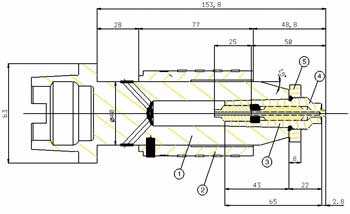