Elementos de fijación roscados en los generadores eólicos
www.profiroll.de • E-mail:pes@profiroll.de27/08/2008
El sector eólico
Los primeros molinos eólicos producidos de manera más o menos en serie proporcionaban una potencia máxima de 30 kW/h. Hoy en día los molinos más comunes proporcionan potencias entre 850 kW y 2,3 Mw y se han desarrollado prototipos de potencias hasta 3Mw. Este incremento de potencia se ha conseguido principalmente por medio de la mejora de los rendimientos y el aumento del tamaño de las palas que conlleva un aumento en el resto de los elementos que componen en generador.
En relación a su forma, los elementos de fijación utilizados en los generadores eólicos se dividen en dos grandes grupos. Por una parte los tornillos con cabeza y por otra parte los tirantes, de los que existen dos tipos diferentes, los tirantes con rosca parcial en ambos extremos y los tirantes roscados en toda su longitud.
Dependiendo del fabricante se utilizan bien los tornillos o bien los tirantes para realizar las uniones entre elementos.
El aumento del tamaño de las torres y las mayores prestaciones de éstas requieren por una parte que los elementos de fijación sean cada vez de mayores dimensiones y por otra parte que los materiales utilizados sean cada vez más resistentes. El objetivo es poder utilizar el mismo número de tornillos de las mismas dimensiones y así evitar tener que utilizar tornillos de dimensiones excesivas o un número mayor de estos, que significaría una mayor dimensión de las piezas que unen para tener una superficie mayor donde poder situar los tornillos.
En las primeras torres lo más común era usar tornillos hasta M 30 en calidad 8.8, hoy en día lo normal es el uso de tornillos hasta M42 y en calidad 10.9, lo que unido a la mayor longitud de rosca que se deriva del uso de tornillería de mayores métricas significa la necesidad de laminadoras de prestaciones muy superiores a las utilizadas hasta el momento.
Máquina, herramienta y proceso de una sola fuente para el sector eólico
Soluciones de Profiroll
Como ejemplo un tornillo de cabeza hexagonal de M42x 4,5 de 250mm. de longitud pesa 3 Kg y un tirante de M42 de 700mm. de longitud pesa 6,5 Kg.
Tomando esto en consideración Profiroll se han centrado en buscar soluciones en esos dos campos bien diferenciados. Por una parte la optimización del proceso de laminado, desarrollos realizados en las máquinas, y la optimización de los sistemas de carga- descarga de piezas a las máquinas.
Desarrollos de la máquina
Para la aplicación de laminación de tornillos para los generadores eólicos Profiroll ha utilizado las máquinas electrónicas de la serie económica que disponen de importantes ventajas respecto a las máquinas hidráulicas que se conocen normalmente en el mercado. Las máquinas utilizadas principalmente han sido las de 50 y 60 toneladas.
El cuerpo de las máquinas está realizado en acero fundido con diseño en “C” y el carro está guiado sobre guías lineales precargadas de rodillos que aseguran un deslizamiento suave y la rigidez necesaria al conjunto. Este diseño es el resultado de los 65 años de experiencia de Profiroll en el diseño y construcción de laminadoras.
Fuerza de laminado (kN) 600
Diámetro de pieza (mm) 10-120
Ancho de rodillo max. (mm) 230
Diámetro de eje (mm) 100
Diámetro max. de rodillo (mm) 308
Revoluciones (RPM) 10-100
Inclinación de cabezales (grados) +/-4
Potencia a conectar (kW) 45
Longitud (mm) 2450
Ancho (mm) 2550
Alto (mm) 1960
Peso (kg) 8000
Engrase centralizado +
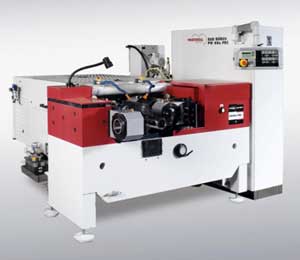
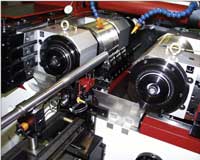
Posibilidad de influir sobre el proceso de laminado
La máquina dispone de 8 curvas diferentes de penetración del proceso de laminado. Esto permite controlar principalmente el inicio del proceso de laminado. En las máquinas sin control sobre el carro este avanza y al producirse el contacto entre el rodillo y la pieza el grupo hidráulico proporciona la fuerza necesaria para que el rodillo penetre en la pieza. Como la superficie de contacto entre el rodillo y la pieza, al inicio de la laminación, es mínimo el carro encuentra poca fuerza de resistencia en sentido contrario por lo que penetra en la pieza a mucha velocidad y sin ningún control. Profiroll ha desarrollado un programa especial para la laminación de materiales de alta resistencia que se aplica a través del control electrónico y permite realizar una penetración suave en el inicio del proceso de roscado e ir aumentando la fuerza a medida que esta es necesaria. De esta manera se asegura la calidad de la rosca y se mejora notablemente la vida de la herramienta.
Control del 100% de las piezas a través de la monitorización de la fuerza ejercida durante el laminado
Cuando se va a iniciar la producción de una pieza en concreto se puede establecer una fuerza de laminado estándar para esa pieza. Esto se realiza laminando una serie de 5 piezas previamente controladas de manera que la máquina automáticamente tome las fuerzas realizadas durante el laminado de estas piezas y establezca la media de las mediciones como “fuerza de laminado estándar”. Una vez que se ha establecido esta fuerza estándar se establece una ventana de variación de la fuerza, normalmente ± 5 por ciento. Al iniciarse la producción en serie la máquina monitoriza la fuerza de laminado realizada en cada pieza y si esta no está dentro de la ventana establecida anteriormente la máquina, dependiendo del tipo de carga de pieza que se esté usando, informa de esta anomalía en la pieza o bien descarga la pieza con la anomalía a un contenedor separado de las piezas buenas. De esta manera se realiza un control del 100% de las roscas en las piezas laminadas.
Almacenamiento de gran número de programas de pieza
Se almacenan en el sistema de la máquina gran número de programas de pieza de manera que al realizar un cambio de pieza a producir el operario solo debe realizar el cambio de rodillos. Los demás parámetros del proceso de laminado (punto de penetración de los rodillos, curva del proceso de laminado, fuerza estándar de laminado, etc.) son almacenados en el programa de pieza y cargados automáticamente al cargar el programa correspondiente a la pieza a laminar.
Sistema PRS (Pitch Reference System) para el sincronizado de los rodillos
Este sistema permite sincronizar un rodillo respecto al otro con gran facilidad y precisión desde el frente de la máquina. Una vez realizada la marca de los rodillos sobre la pieza se mide la diferencia entre marcas y se introduce este valor en el control que devuelve el valor en grados a corregir de la posición del rodillo izquierdo respecto al derecho. La posición relativa del rodillo izquierdo respecto al derecho se visualiza en la pantalla. El valor establecido nos servirá siempre que se usen estos rodillos, de manera que la siguiente vez que se monten el operario no necesitará realizar el sincronizado de los rodillos, simplemente llevando el rodillo izquierdo a su posición, por medio del volante situado en el frente de la máquina, los rodillos quedan perfectamente sincronizados.
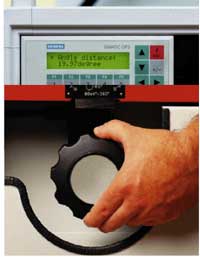
Sistemas de carga- descarga de piezas
Para ello en estrecha colaboración con el principal productor de elementos de unión roscados para la industria eólica Profiroll ha desarrollado tres aplicaciones que cubren todos los diferentes tipos de elementos de sujeción.
Sistema de laminado de piezas con cabeza
Como ejemplo un tornillo hexagonal de M42x 4,5 de 400mm. de longitud pesa aproximadamente 4,5 Kg. Una producción de 6.500 piezas por turno, que es la producción del sistema suministrado por Profiroll, significa manipular aproximadamente 29.000Kg en un turno normal de 8 horas. Con los requerimientos de seguridad en el trabajo hoy en día es impensable que un operario manipule este tipo de volumen manualmente por lo que es prácticamente obligatorio el uso de sistemas de carga- descarga automático de piezas en las que estas sean manipuladas automáticamente sin que el operario deba intervenir directamente en la operación de carga- descarga.
En el sistema desarrollado por Profiroll la carga de las piezas se realiza en una tolva y la salida de las piezas roscadas se hace a contenedores situados en el frente de la instalación con lo que la manipulación de las piezas se realiza totalmente por medios motorizados.
Las principales partes que componen el sistema son:
• Tolva de carga donde se vuelcan las piezas a laminar, capacidad de 500 lts. Este proceso se realiza normalmente por medio de una carretilla elevadora y las piezas se vuelcan sin ningún control de la posición u orientación de estas.
• Orientador de piezas. Las piezas son elevadas por medio de un seleccionado de persiana al sistema de orientación donde las piezas se orientan de manera que queden colgadas por la cabeza. Este parte de la instalación se encuentra dentro de una campana insonorizada para minimizar el ruido que invariablemente producen piezas de estas dimensiones al golpear unas contra otras.
• Rampa de unión entre seleccionador y máquina. Por medio de esta rampa se trasladan las piezas, colgadas por la cabeza, a la máquina.
• Seleccionador de piezas. Este elemento selecciona las piezas para que se introduzcan en la máquina una a una.
• Alimentador- expulsor de piezas. Este elemento posiciona la pieza a laminar ente los rodillos a medida que expulsa la pieza ya laminada.
• Rampa de salida de piezas. Desde esta rampa las piezas caen a los contenedores dispuesto para el almacenamiento de la piezas.
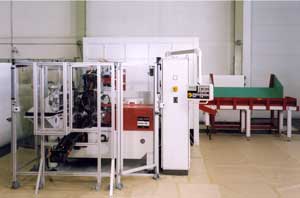
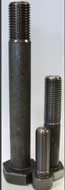
Métricas a laminar: M24- M42
Longitudes de tornillos: 80 - 400 mm
Producción M42x4,5 long.de rosca 100 mm: 15 piezas/ min.
Tiempo de cambio de máquina, cambio total de máquina: 20- 30 min.
Posibilidad de laminar piezas más largas o de mayores diámetros retirando el alimentador- expulsor a un lateral y realizando la alimentación manualmente.
Sistema de laminado de espárragos
Como se ha indicado anteriormente en los generadores eólicos actualmente se utilizan dos tipos de espárragos bien diferenciados a la hora de laminar las roscas. Espárragos con roscas en ambos extremos y espárragos con rosca en toda su longitud.
Las roscas de los espárragos con roscas en ambos extremos se laminan normalmente a plongee, es decir los rodillos son de una anchura un poco superior a la longitud de la rosca a laminar y la deformación del material se produce por medio de la penetración de los rodillos en la pieza. Dependiendo del perfil a laminar, cuanto mayor paso de rosca más material a deformar por lo que se necesitará más fuerza de laminado, la longitud de la rosca y la resistencia del material a laminar el requerimiento de la fuerza necesaria se ve incrementado notablemente.
Las roscas de los espárragos con rosca en toda su longitud se laminan en enfilada. La laminación en enfilada se utiliza en estos casos ya que sería imposible laminar estas longitudes de rosca en plongee. Este método de laminación se realiza con rodillos especialmente diseñados siendo el ángulo de la rosca de los rodillos diferente al ángulo de la rosca de la pieza. Para igualar los ángulos se inclinan los cabezales y debido a esta inclinación y a la diferencia de ángulos se produce un movimiento axial de la pieza que va penetrando entre los rodillos y saliendo con la rosca deformada por la parte trasera de estos.
Teniendo en cuenta que el requerimiento de los fabricantes de poder laminar ambos tipos en la misma máquina Profiroll ha desarrollado un sistema de alimentación que puede trabajar tanto con roscas a plongee como con roscas en enfilada. Además gracias a disponer de una zona de trabajo muy amplia y a que la posición a la que el manipulador desplaza la pieza para el laminado está controlada por el autómata de la máquina se pueden roscar roscas de diferentes métricas en cada extremo del espárrago. De esta manera se dispone de un sistema de alimentación muy flexible.
En el sistema desarrollado por Profiroll la carga de las piezas se realiza en una rampa, que normalmente se conecta a la máquina que realiza las operaciones previas al laminado, y la salida de las piezas roscadas se hace a una rampa situados la parte trasera de la instalación.
Este tipo de soluciones se han instalado principalmente en Alemania y también en diferentes países como Japón, India, Italia, Corea, Japón y EEUU.
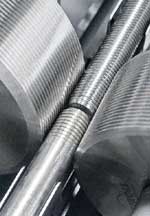
Métricas a laminar: M24- M42
Longitudes de espárragos 200 700mm.
Producción M30x45 long. 475, rosca en ambos extremos: 4 piezas/ min.
Velocidad recomendada para el laminado en enfilada: 600-900 mm/min.
Tiempo de cambio de máquina, cambio total de máquina: 20- 30 min.