Taladrado láser de chapa mediante un láser convencional
El haz láser puede definirse como una luz de características especiales como son la monocromaticidad, coherencia y direccionalidad. Gracias a ellas, se consigue concentrar energías considerables en un área de pequeñas dimensiones. En función de esta densidad de energía y del tiempo de interacción entre pieza-láser, se pueden conseguir desde un calentamiento localizado de la pieza (para procesos como el temple o pulido), la fusión (en el proceso de soldadura o láser cladding) o hasta la vaporización directa del material (mecanismo buscado en el proceso de taladrado).
Motivación del proyecto
El proyecto aquí descrito surgió ante la creciente necesidad de la industria en explorar soluciones para el proceso de taladrado de pequeños diámetros (menores que un 1 mm) en chapas de espesores que oscilan entre 0,1 a 2 mm de espesor.
Aunque existen distintas alternativas para la realización de estos taladros, como son el taladrado mediante micro-brocas, taladrado EDM, mecanizado por ultrasonidos (USM) e incluso la microestampación, etc. todos ellos presentan alguna de las siguientes desventajas: elevado coste, incapacidad de asegurar las tolerancias necesarias, etc. En cualquier caso, la principal desventaja de todas estas técnicas es la lentitud del proceso. Si se considera que algunas piezas se diseñan con cientos o miles de agujeros para que se refrigere un determinado área o se controle un determinado caudal de gas, la productividad del proceso es clave. Por ello, el taladrado láser se presenta como la alternativa adecuada para la realización de estas operaciones, ya que permite la realización de agujeros de muy buena calidad en tiempos del orden de milisegundos por agujero.
La principal desventaja del proceso láser es la dependencia del equipo. Existen diferentes soluciones industriales para realizar agujeros por debajo del milímetro de diámetro, pero se trata de soluciones costosas y específicas, que no se disponen en muchos talleres. Por otro lado, los láser convencionales que se utilizan en corte y soldadura presentan mejores calidades de haz y posibilidades de trabajar en régimen pulsado a elevadas frecuencias. Así, la incorporación del láser de disco y fibra a la industria ha supuesto un incremento de las prestaciones del láser industrial en términos de calidad y control de tiempo de interacción del láser con la pieza.
Por ello, el presente proyecto ha investigado la posibilidad de realizar dichos orificios mediante un láser de fibra convencional y se ha analizado la calidad de los mismos. El equipo empleado es un láser de fibra Rofin FL010, localizado en el Taller Mecánico del Departamento de Ingeniería Mecánica de la UPV/EHU y que tiene una potencia máxima de funcionamiento en continuo de 1 kW. Se ha trabajado sobre diferentes materiales, incluyendo una chapa de acero inoxidable, AISI 304 de 1mm de espesor, una probeta de tungsteno puro de 100µm de espesor y una probeta de aluminuro de titanio de 1mm de espesor. Para el análisis de calidad de los taladros, se han medido los diámetros de salida y entrada, la conicidad del agujero, la repetitividad del proceso y la geometría interna de los mismos.
Metodología experimental
En primer lugar se ha analizado la influencia de las distintas variables del proceso (potencia, posición del plano focal, duración del pulso, etc.) sobre la geometría final del agujero (diámetros de entrada y salida, conicidad del agujero, etc.) y se ha obtenido así la zona óptima de taladrado para los distintos casos.
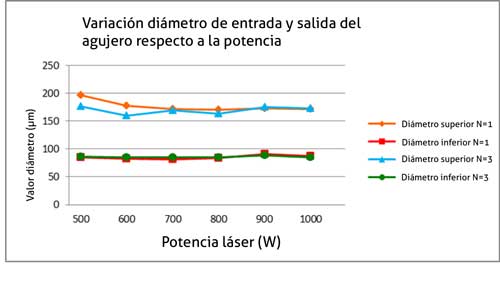
A continuación se muestran unas imágenes de los distintos taladros realizados sobre diversos materiales. El láser permite una gran flexibilidad de operación, pudiendo realizarse agujeros de diversos diámetros, empleando diferentes estrategias. En caso que el espesor de la pieza lo permita, se puede realizar el taladro en un único pulso, mientras que, si el espesor de la pieza es mayor, se realiza la operación mediante un tren de pulsos (lo que se denomina como laser percusion drilling o taladrado láser por percusión). Por último, si el diámetro del agujero es elevado (por encima de las 100µm en nuestro caso) se puede emplear una estrategia de trepanado.

Análisis de la calidad de los taladros
El taladrado láser es un proceso de arranque de material mediante aporte térmico, en el cual no interviene filo de herramienta alguno, ni existen fuerzas que puedan deformar la pieza. Sin embargo, el proceso de taladrado láser tiene una serie de defectos inherentes del propio proceso, como son la generación de una capa de material refundido y la aparición de una zona afectada térmicamente. También es probable que aparezcan rebabas formadas por material fundido que se ha resolidificado en el borde de salida del agujero.
Así, es necesario ajustar correctamente los parámetros de proceso para garantizar una buena calidad de los taladros. Para asegurar la calidad de los agujeros, además de analizar la redondez de los orificios de entrada y salida, se ha analizado también la geometría interna de los mismos. Para el análisis de la geometría interna de los taladros, se ha realizado el corte longitudinal los orificios mediante WEDM. El corte se ha realizado en un plano que contiene el eje de los taladros, de esta manera se puede comprobar que la conicidad de los agujeros es mínima.
Para la visualización de la zona afectada térmicamente (ZAT) se ha atacado la sección del taladro mediante Nital, que revela mediante un color más claro dicha zona. Como puede verse en la imagen inferior de la derecha, la zona afectada térmicamente es de unas pocas micras.
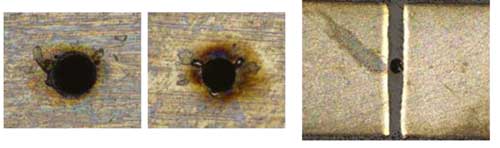
Modelización del proceso
Paralelamente a los ensayos experimentales, se ha desarrollado un modelo numérico basado en diferencias finitas centrales que simula el proceso de taladrado láser y permite predecir la geometría de los taladros y el campo de temperaturas de la pieza con precisión. Lo que permite la minimización del número de ensayos a realizar en la máquina, con el consiguiente ahorro económico que ello conlleva.
Aunque no se va a profundizar en las bases del modelo numérico, debe mencionarse que se basa en el balance energético en cada uno de los elementos que conforman el cuerpo mediante la aplicación del primer principio de la termodinámica:
dEentrada – dEsalida + dEgenerada = dEacumulada
Desarrollando esta ecuación, se obtiene la ecuación general del campo de temperaturas por conducción:
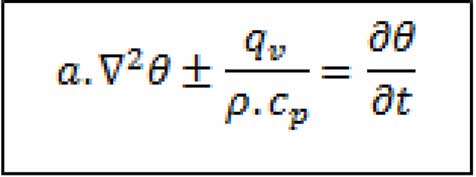
Donde:
- cp: Calor específico [KJ/Kg.K]
- qv: Potencia calorífica por unidad de volumen [W/m3]
- ρ: Densidad del cuerpo [Kg/m3]
- a: Difusividad térmica [m2/s] donde a= λ/ (ρ.cp)
Desarrollando esta ecuación e introduciendo las condiciones iniciales y de contorno, se llega a la siguiente ecuación, que debe resolverse iterativamente para la obtención del campo de temperaturas de la pieza.
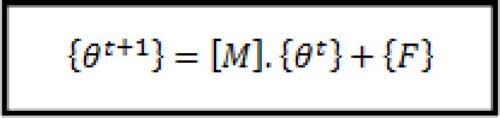
Donde, [M] = Matriz de transferencia y [F]= Vector fuente.
Tras la realización de todos los cálculos, el programa desarrollado permite la representación gráfica de la geometría tridimensional del microagujero. A modo de ejemplo, en las siguientes imágenes se muestran las representaciones 3D de un taladro, tanto como si fuera un cuerpo sólido (donde se muestra el campo térmico alcanzado durante la operación de taladrado) y una vista en alámbrico del mismo (que permite una mejor visión del agujero internamente).
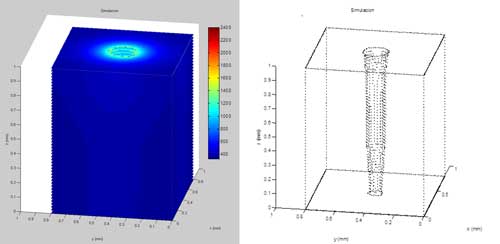
Además de ello, el programa permite realizar secciones de la geometría 3D, lo que ha permitido validar del modelo numérico en comparación con las secciones obtenidas de los agujeros reales.
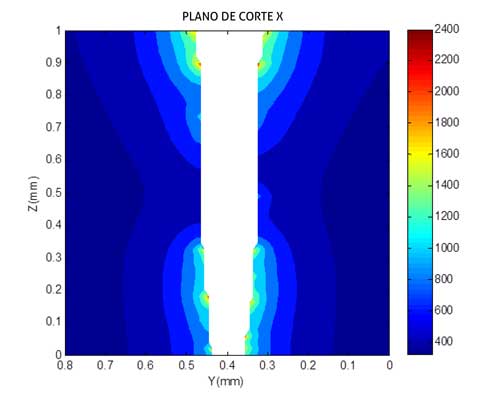
Conclusiones
Mediante el presente trabajo se ha verificado que con un láser convencional de fibra se pueden realizar taladros de diámetros por debajo del milímetro y de alta calidad en tiempos razonables, llegando a taladrar una chapa de acero inoxidable AISI 304 de 1mm de espesor en un tiempo total de 3ms por agujero. La calidad obtenida muestra que el proceso es capaz de obtener orificios regulares, con una precisión del orden de micras, sin embargo el proceso presenta algunas limitaciones si se compara con los resultados obtenidos con equipos específicos de taladrado láser basados en equipos pulsados capaces de emitir pulsos de picosegundos.