Ducati relies on the detection of broken tools of Renishaw to manufacture exclusive camshaft trees
The most important phase of the production of camshafts for the Ducati Desmodromic engine is made in two Stama machining centers. Machines work tirelessly throughout the year manufacturing camshafts for Ducati engines.
Fulvio Abbondi, technical expert of Ducati Motor production, says: "Is required high accuracy to make the tree, with all the complicated process of machining made entirely in our facilities." It is a very expensive component. "It is made in an alloy of special steel which is already very expensive when positioned in the rough in the machine tool after a first turning of preparation".
A broken tool during the process of production of camshaft would be particularly serious, since it could generate discarded parts, repetition of the machining and loss of time. In addition, it could break the spindle of the machine and this, added to the cost of own specialized tools, would entail an expenditure of thousands of euros.
Abbondi explains the function that performs the detection of broken tools. "It is essential to make a follow-up to check the performance of the machines." We install systems NC4 of Renishaw in two machining centers: immediately after loading a tool in the spindle to start machining, goes through the beam of the device at a set height. If you break the cutting area, for example, instead of having 100 mm in length, stays in 97 mm, the laser system triggers an alarm.
"Obviously, each tool has its own length, diameter, etc., the system takes into consideration when the tool runs through the bundle of verification". Abbondi continues "the NC4 system also allows us to detect ruptures of the small tools employed to produce spots and other points of reference of the cam, crucial for perfect operation of the engine." If not for the Renishaw system, the machine could, for example, continue to operate with a broken cutting area and lead to disastrous results. "In addition, given that broken tool detection is automatic, a single operator can easily handle two machines: just place the pieces and make sure that everything works correctly".
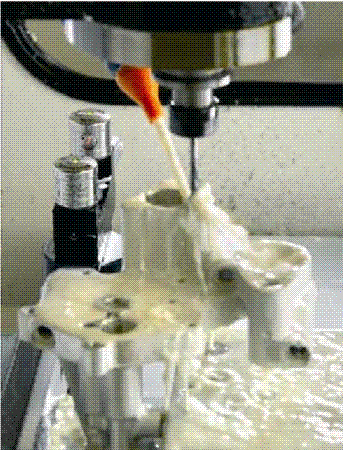
Essential process control in machining operations
While Abbondi explains: "the first thing we did was to install a system provided by the manufacturer of the machine tool that allows to verify the power used by the spindle motor". The system checks the degree of wear of the larger pieces, used to drill deeper holes and in which tension is more obvious, if you increase the couple of torsion, the tool is worn out by what the alarm. But we also need to detect tools broken quickly and accurately, so even the smallest, which usually manage to escape most of detection systems.
Checking through light
Advances experienced by the laser technology have enabled to develop non-contact detection systems, capable of measuring the smaller tools.
A laser beam is connected between a transmitter and a receiver, installed in the machine table or mounted on both sides of it, so that the beam passing through the area of work. When the tool runs through the beam, it reduces the amount of light detected by the receiver and it generates a trigger signal. If a reduction of the light is not detected, the system emits a signal of broken tool.
The Desmodromic system
The vast majority of the manufacturers of engines in the world use return springs in their motors to close the valves for admission and exhaust, these Springs return the valve to its original position after his move.
The only exception to this rule is Ducati, which is achieving great results with their Desmodromic, less conventional system. The Desmodromic distribution provides more reliability to the engine at higher speeds, as it solves the problem of inertia of the pier and reduces the friction of operation by approximately 30 per cent. In theory, the engine can easily exceed 20,000 rpm. Desmodromic uses a mechanical system to close valves, a concept originated in America, but later abandoned due to its high cost. However, the well-known manufacturer of Bologna had other plans and incorporated the Desmodromic distribution in their bicilíndricos engines in 1972, and it has continued to use this winning system for decades.