El proyecto Imop crea un sistema pionero para automatizar el trabajo en fábricas
Conocer cómo y a qué actividades se destinan los recursos económicos y humanos es una de las principales dificultades de las empresas, sobre todo de las pymes que carecen de las infraestructuras y herramientas necesarias para tener un control objetivo y a tiempo real. En esta línea, el Clúster de Innovación en Envase y Embalaje, como entidad que apuesta por la innovación y la cooperación entre empresas, ha finalizado el proyecto ‘Imop. Modelo avanzado para la Imputación automática de Mano de Obra a Producto fabricado’ que se ha centrado en solventar todas esas carencias junto a las compañías MESbook, TST, CLR y Gráficas Lersi, además de la colaboración del Clúster de Empresas Innovadoras Valle del Juguete (CEIV).
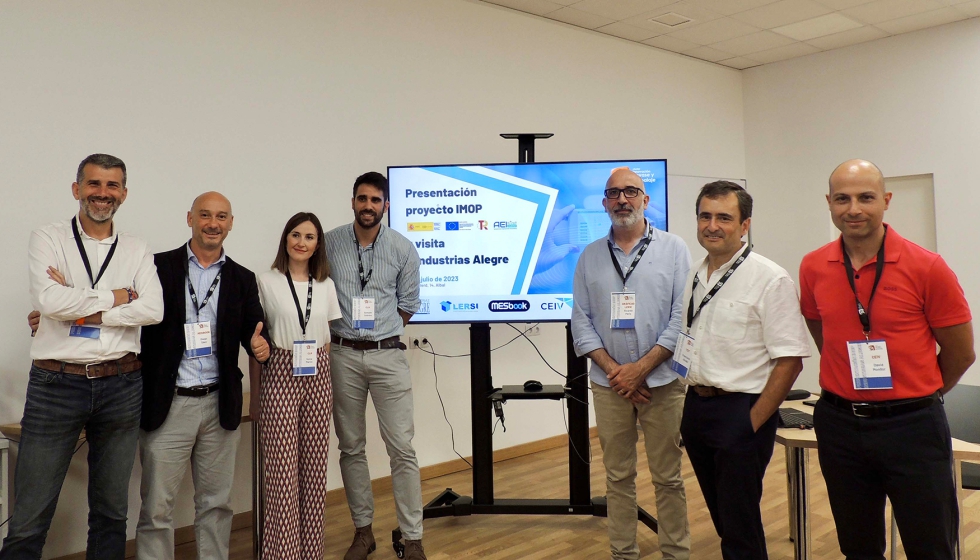
En la presentación de resultados de este proyecto, realizada en la sede de la empresa Industrias Alegre, Jesús Pérez, director del Clúster de Innovación en Envase y Embalaje, ha destacado: “Imop busca fomentar el desarrollo económico de las empresas mediante la transformación digital, siendo una solución de bajo coste y alta autonomía”.
En concreto, en este proyecto se ha desarrollado un sistema de localización de personal en fábrica con imputación de horas automática a la orden de fabricación, a través de la combinación de tecnologías 4.0. Hasta ahora no existía ningún sistema que utilizara las tecnologías inalámbricas para este cometido en las fábricas. En esta línea, el nuevo desarrollo supone una solución innovadora para la localización en interiores, una herramienta capaz de aprender y corregir la ubicación del sujeto.
En esta línea, Diego Sáez de Eguílaz, socio director de MESbook, ha confirmado que en las pruebas realizadas en las empresas colaboradoras se ha demostrado que esta iniciativa puede lograr ahorros de entre 50.000 y 100.000 euros en la mano de obra indirecta (MOI) y en los gastos generales.
Además, desde TST se han desarrollado algoritmos avanzados de cálculo y corrección de la posición que permiten a las empresas conocer el tiempo invertido en cada uno de los proyectos. Francisco Alcalá, CEO de esta compañía, ha subrayado que “nuestra aportación, a través de nuestra tecnología de última generación basada en Bluetooth Angulo de Llegada (BLE AoA), ha sido el encaje perfecto para cubrir las necesidades de localización en interiores de las fábricas”. Con la tecnología inteligente desarrollada por TST se logra calcular, en tiempo real, el esfuerzo invertido en cada uno de los puestos de trabajo, discriminando situaciones no imputables a esfuerzo real, como “pases momentáneos del trabajador por otro puesto de trabajo y manteniendo al trabajador registrado en el puesto a pesar de ausencias no computables como aquellas debidas al acopio de material o la ayuda puntual a otro compañero”, ha explicado.
Implantación real del proyecto
Todas estas novedades se han puesto en marcha en las dos empresas colaboradoras del proyecto: CLR, especializados en motorreductores de corriente continua y alterna; y Gráficas Lersi, especialistas en packaging en diferentes sectores como alimentación, hortofrutícola, cárnico y cosmética.
“En nuestro día a día tenemos muchos trabajos que son manuales, y según el producto con el que trabajemos, las horas reales dedicadas al proyecto varían, pues hay materiales más costosos de manejar”, ha destacado Ricardo Perís, director de operaciones en Gráficas Lersi, que ha continuado explicando que a través de diferentes tablets asignadas a mesas de trabajo, pueden monitorizar los diferentes procesos, adaptándose a las exigencias de su día a día.
Una visión positiva que desde CLR también comparten y así lo ha enfatizado en su intervención Gonzalo Sobrino, ingeniero de proyectos de la compañía, destacando que “hemos obtenido una mejora en la efectividad y la productividad, pero eso no es todo pues gracias a estas mejoras podemos conocer los costes y tiempos de nuestros procesos y así eliminar esas tareas que no aporten valor”.
Visita a Industrias Alegre
Para finalizar la presentación de resultados, los asistentes han podido conocer las instalaciones de Industrias Alegre, visitando la zona de inyección y la de fabricación aditiva de la mano de Jesús Ibáñez, Kam Packaging de la empresa.
Además, Amparo Vázquez, directora de I+D+i en Industrias Alegre, ha explicado en su intervención algunas de las novedades de la compañía como la fabricación aditiva avanzada en la que llevamos años investigando para que sea un proceso complementario a la inyección; o su unidad de packaging a medida, Hybrid Box, diseñado con paredes plegables que, además, incorpora un sistema interior que permite prescindir de los habituales protectores no retornables.
Finalmente, el proyecto Imop ha sido cofinanciado por el Ministerio de Industria, Comercio y Turismo (Mincotur) mediante la segunda convocatoria de las AEI del 2022 en el marco de las ayudas Next Generation y el Plan de Recuperación, Transformación y Resiliencia.
Sobre el Clúster de Innovación en Envase y Embalaje
El Clúster de Innovación en Envase y Embalaje es una asociación empresarial que cuenta con más de 70 asociados. Su objetivo es facilitar la generación de negocio entre las empresas asociadas integrando a toda la cadena de valor del envase y embalaje.
Sus asociados, entre los que se encuentran empresas de papel, cartón, plástico y madera, dan respuesta a la industria agraria y alimentaria, automovilística y azulejera.
El sector del envase y embalaje tiene unas ventas superiores a 3.200 millones de euros anuales y emplea a más de 12.000 personas en la Comunidad Valenciana. El sector representa el 10% de la facturación agregada de las industrias con sede en la comunidad y el 2,6% del PIB valenciano.