Crece la inversión en Industria 4.0
El Smart Industry 4.0 es ya uno de los informes de referencia a nivel nacional sobre el estado de la digitalización de la industria española siendo, además, el de esta edición, especialmente interesante por las circunstancias y contexto social y económico tan extraordinario que nos ha tocado vivir en los últimos meses.
Esta es la cuarta edición del estudio realizado por la consultora NTT Data junto con el Observatorio Industria 4.0 y la colaboración del Club Excelencia en Gestión y CEL Logística con el objetivo de analizar el estado actual de la industria española frente a la transformación digital, así como su evolución a lo largo de los años.
El informe vuelve a reafirmar el crecimiento exponencial de la digitalización en el sector industrial desde su primera edición, creciendo ligeramente la inversión en los planes de transformación digital debido a una mayor concienciación de la necesidad de llevarlo a cabo, incentivada entre otras por la crisis de componentes. La COVID-19 sigue impactando a las empresas, que determinan la necesidad de disponer de una cadena de suministro ágil y flexible, así como una mayor autonomía tecnológica. Además, ahora se centran en afrontar una correcta recuperación económica.
Por otro lado, aunque la resistencia a la innovación y el cambio de los individuos sigue siendo el mayor obstáculo dentro de las empresas hacia la transformación digital, la falta de formación de los trabajadores aumenta considerablemente y se sitúa muy cerca como preocupación de las empresas.
Frente a esto observamos una mayor implantación de la matriz de competencias donde recogen los conocimientos que los empleados han de tener en Industria 4.0, así como la transmisión de información entre la plantilla. El conocimiento, la gestión y explotación del dato siguen siendo los conocimientos más demandados por las organizaciones.
La cuarta edición del informe ‘Smart Industry 4.0’ continúa con el proceso de análisis tecnológico desarrollado en las ediciones anteriores. El objetivo principal de este informe es facilitar a las empresas la identificación de nuevas oportunidades a través de una autoevaluación de su nivel de madurez en relación con los nuevos paradigmas de la Industria 4.0.
Por otro lado, se reserva un espacio de análisis sobre la situación pandémica por la que hemos atravesado, haciendo hincapié en cómo la COVID-19 ha impactado en nuestras industrias. Además, se analiza cómo ha contribuido a acelerar la transformación digital en las empresas y cómo estas, se han enfrentado a la política de teletrabajo.
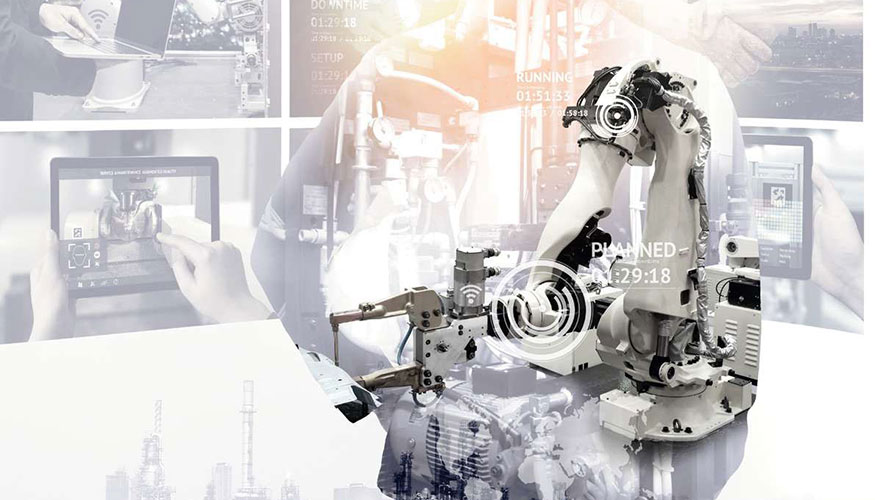
Digital Supply Chain
El objetivo del Digital Supply Chain es integrar completamente y hacer visible cada eslabón del movimiento de materias primas y producto terminado.
La clave de este elemento crítico de Industria 4.0 es el análisis, interpretación y visibilidad de los datos. Las compañías ya cuentan con las herramientas necesarias para monitorizar gran parte del estado actual de sus cadenas de suministro, lo que permite predecir posibles problemas y anticiparse en la toma de decisiones.
La clave de la digitalización es la capacidad de integración de cualquiera de los factores en toda la cadena, con el objetivo de optimizar activamente todos los procesos y agentes involucrados, incluyendo los proveedores y clientes.
Las ventajas operacionales de la aplicación de estas técnicas destacan en sostenibilidad (disminución de la huella de carbono) y resiliencia (flexibilidad y gestión absoluta de la cadena). Debido a la situación pandémica acontecida en nuestro país, la resiliencia de la cadena de suministro ha sido factor clave. Por ello, las soluciones que se aplican están siendo claves para acelerar la transformación digital, lo que hace impulsar la innovación e incrementar la productividad y rendimiento en las empresas de todos los segmentos de actividad.
Asimismo, las compañías han puesto el foco en la optimización de la operativa y las cadenas de suministro, buscando partners alternativos capaces de cubrir el déficit que sus actuales socios puedan tener. Además, están buscando un mayor acercamiento de las cadenas de suministro, así como la automatización de todos sus procesos productivos, lo que se conoce como hiperautomatización
Resultados del estudio:
- Las empresas han evolucionado a la hora de gestionar todos los procesos en la cadena de suministro. Se observa un crecimiento general hacia los Sistemas y la excelencia operacional.
- La incertidumbre en la que nos movemos hace que la Planificación de la demanda sea uno de los puntos a los que más importancia le dan los encuestados, seguido de la trazabilidad de los pedidos de los clientes.
- El 80% de los encuestados tiene previsto invertir a lo largo de 1-3 años en la planificación de la demanda y de la cadena de suministro.
- La monitorización centralizada y la trazabilidad a lo largo de la cadena, si bien se extienden algo más en el horizonte temporal, son también los ámbitos en los que las empresas van a invertir más.
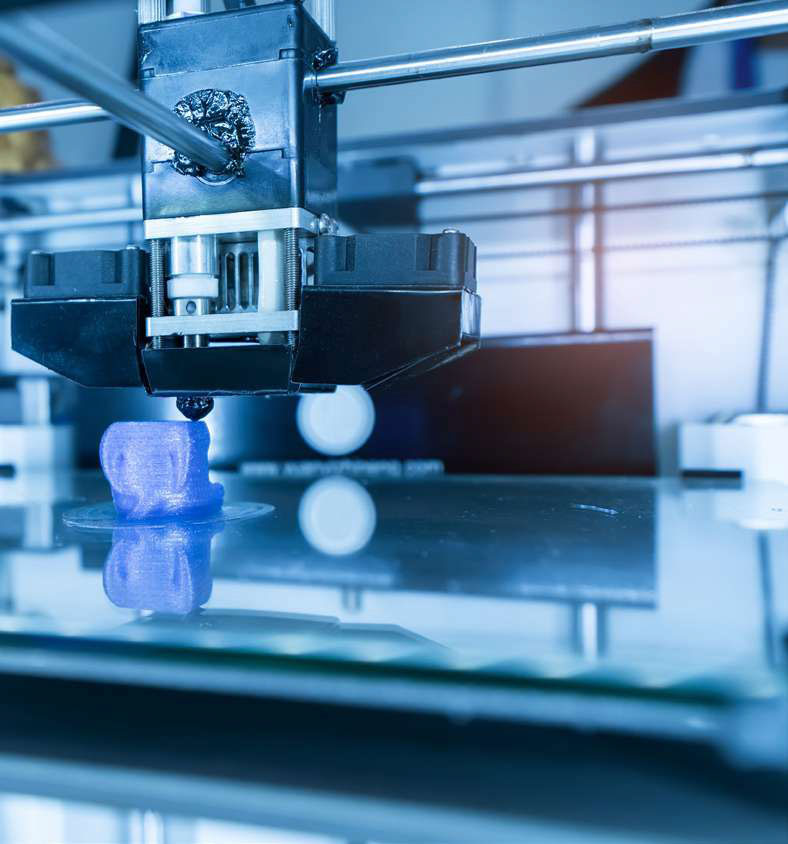
Digital Manufacturing
Entendemos por Digital Manufacturing el uso de un sistema integrado compuesto por herramientas de simulación, visualización 3D, análisis y colaboración de datos para la gestión simultánea de diseño de productos y procesos de fabricación.
Para conseguir una total armonía en el proceso productivo, es importante dotarlo de una gran conectividad en todos los procesos. Para ello, se está implementando una arquitectura de datos en tiempo real que permita la captura, procesamiento, visualización y aprovechamiento de datos de cualquier parte de los procesos productivos de la cadena de suministro.
Técnicas como el Machine Learning y la Inteligencia Artificial utilizan esta capa de datos para potenciar las capacidades industriales. Aportan modelos y funciones que permiten tomar mejores decisiones en el día a día para que, a través de técnicas más desarrolladas, se pueda operar de forma autónoma en tiempo real, consiguiendo así conectividad y autonomía.
El mantenimiento y la simulación de los procesos de la red de suministros también se han visto mejorados debido a la monitorización continua y los servicios de nube que captan la información. Esto ha permitido que se reduzcan los errores y se minimicen los problemas de calidad desde la fase de diseño. También supone una reducción de costes significativa y una mejora de proceso.
Un reto crucial de la Industria 4.0 es la convergencia IT-OT, garantizando en todo momento el intercambio de datos e información de manera estandarizada y segura, entre dispositivos, máquinas, sistemas y servicios.
Resultados del estudio:
- Crecimiento significativo de los procesos 4.0 con respecto al año anterior, debido principalmente a la pandemia.
- En prácticamente todos los procesos, más del 50% se gestionan a través de sistemas y excelencia operacional y procesos 4.0.
- Gestión del mantenimiento y Secuenciación de la producción son los procesos que los encuestados destacan en importancia.
- Íntimamente relacionado con sus planes de inversión en el corto medio plazo, las empresas centran sus esfuerzos en planificación y producción, con el objetivo de producir más eficientemente, sin errores y al mejor coste.
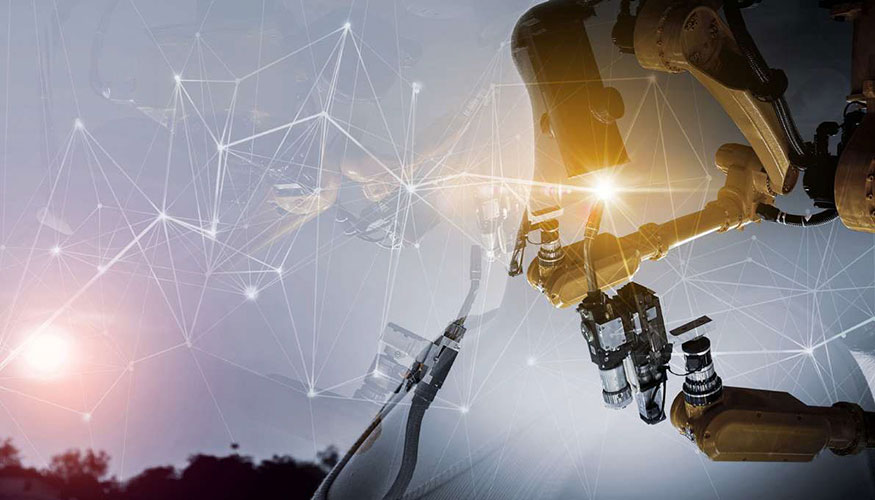
Digital Products
El producto digital, una vez diseñado y creado, lleva al extremo la definición de economía de escala, reduciendo el coste de producción y minimizando el de distribución. Son los artífices de la integración de todas las fases de las redes de suministro, ya sea a través de sistemas de monitorización o como herramientas de gestión. Se entregan digitalmente y evolucionan de la tradicional comercialización al servicio centrado en el cliente.
Tenemos innumerables ejemplos de productos digitales en nuestro vocabulario y nuestra vida cotidiana: desde eBooks, podcasts, encuestas online, servicios de streaming, software o aplicaciones móviles, hasta servicios de aprendizaje online.
Estos productos virtuales se han desarrollado de manera considerable desde el nacimiento de la Industria 4.0. Su desarrollo y consumo ha crecido exponencialmente en los últimos años motivado por los bajos costes de producción y distribución.
Coincidiendo con el auge de la transformación de productos físicos a digitales mediante procesos de sensorización y control a través del Internet de las cosas (IoT), los sistemas de simulación y el desarrollo de los modelos por ordenador han limitado el riesgo asociado a la creación de nuevos productos. Esto, unido a la reducción de los costes de producción y su facilidad de uso, ha generado un crecimiento en la cantidad de productos digitales y el consumo La fabricación digital evolucionó a partir de iniciativas como el diseño para la fabricación ‘Design for Manufacturing’ (DFM), la fabricación integrada por ordenador ‘Computer Integrated Manufacturing’ (CIM), la fabricación flexible y la fabricación ajustada, que resaltan la necesidad de un diseño colaborativo de productos y procesos.
Por otra parte, una de las tecnologías que está cambiando la dinámica del sector industrial, son los Digital Twin. Esta tecnología ya forma parte de la estrategia de las empresas dedicadas a la innovación y diseño de productos de la Industria 4.0, ya que se considera que transformará los procesos de fabricación permitiendo probar los diseños en entornos digitales, ofreciendo nuevas formas de disminuir costes, monitorizar activos, optimizar el mantenimiento, reducir el tiempo de inactividad y permitiendo la creación de nuevos productos conectados.
Resultados del estudio:
- Mejora la gestión de nuevos productos con respecto a años anteriores, pasando de un 29% a un 42% las empresas que ya cuentan con herramientas de gestión de la innovación.
- Se ve la evolución de cómo las empresas han vuelto a preferir departamentos y procedimientos a herramientas de gestión de la innovación.
- Más del 70% de los encuestados prevé invertir en mejoras en la producción de nuevos productos en un horizonte a corto y medio plazo.
- La creación de productos desde la conceptualización hasta la industrialización con metodologías ágiles y tecnologías digitales, son sin duda puntos ganadores que recortan el plazo de conceptualización y minimizan costes.
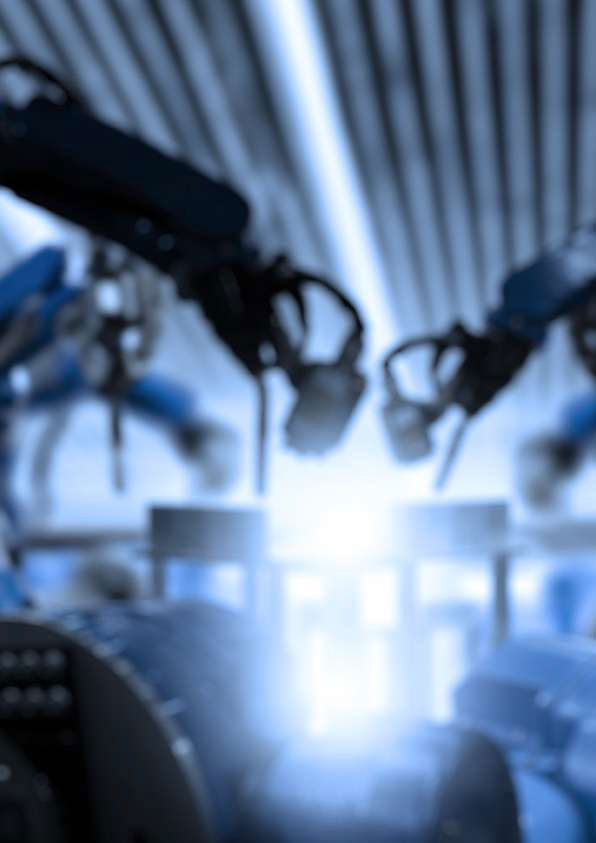
Digital Corporate
La Transformación Digital en las empresas supone una implementación tecnológica y procedimental que potencia la comunicación interna en las compañías, así como la transparencia de cara al exterior. Genera una mejora significativa en los procesos de negocio de la compañía.
La mejor manera de retener clientes y talento en las empresas es comprender las necesidades que tienen y cubrir sus expectativas aportando valor añadido a la propuesta estándar del mercado. Las empresas con intención de crecimiento han de tener un plan de integración de nuevas tecnologías de manera que se pueda aprovechar y potenciar el “expertise” que han adquirido. Esto sumado a la motivación del empleado son los factores clave en la retención de talento.
Los entornos VUCA en los que actualmente nos movemos, propician que el personal ha de tener un alto grado de adaptación al nuevo medio al que constantemente se enfrenta. La situación que acontece a todos los países en este momento, magnifica las características que describen al entorno VUCA. Una de las formas para reducir la inestabilidad generada por la COVID-19 es fomentando la comunicación interna y externa dentro de las compañías, es decir aumentando la comunicación corporativa.
Las compañías e instituciones han apostado por establecer diferentes planes y protocolos de comunicación, a través de la digitalización, intentando minimizar los daños que se pueden producir por causa del trabajo por vía telemática.
Para ello, es importante intensificar uno de los paradigmas más característicos de nuestra empresa: la movilidad. Ésta permite agilizar mediante dispositivos digitales la ejecución de las tareas de forma remota. A nivel de corporación es importante centrar esfuerzos en la formación y capacitación de los profesionales en nuevas tecnologías, metodologías, etc., que el mercado vaya demandando, de manera que nuestros profesionales sean capaces de cambiar de una herramienta a otra de manera ágil propiciando una rápida adaptación que genere mejoras en los procesos de la forma más cercana en el tiempo.
Resultados del estudio:
- Incuestionable tanto el avance en la materia, como la importancia que para las empresas tiene contar con un plan de transformación digital.
- El 71% de las empresas encuestadas este 2021 cuentan con un plan de transformación digital y ya están obteniendo resultados frente al 46% de 2019 y el 26% de 2018.
- Por otra parte, vemos la misma evolución en el caso contrario donde hemos pasado de un 50% en 2018 que no lo tenía, ni lo tenía previsto a tan solo un 16% en 2021.
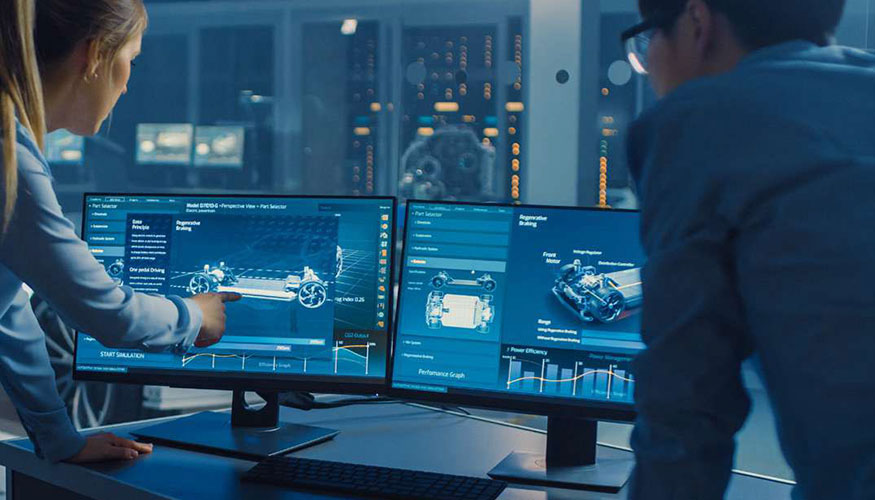
Paradigmas
Las organizaciones de una gran variedad de industrias se están enfrentando a una serie de retos como consecuencia de la COVID-19: Reducción del personal o de equipos completos de personal que trabajan desde casa, obligaciones de proteger la salud de los trabajadores mediante el distanciamiento, enormes caídas en la demanda de algunos productos o servicios, picos repentinos en la demanda de otros, y mayor necesidad de generar eficiencias en los procesos para impulsar la productividad y reducir los costes en la medida de lo posible.
Por consiguiente, muchas empresas se verán repercutidas durante un período largo de tiempo. Sin embargo, también está siendo una oportunidad única de aceptar los cambios en sus negocios que les ha impuesto la situación con la transformación digital y de reevaluar la ingeniería de sus procesos operativos para encontrar esas eficiencias clave y seguir siendo competitivos, algo que sólo será posible con la Automatización.
Algunos de estos paradigmas, están siendo esenciales en las empresas para poder mantener la eficacia de su productividad, ante las circunstancias extraordinarias a nivel mundial que está produciendo la COVID-19.
La introducción de estos paradigmas supone un crecimiento exponencial en la industria a través de la tecnología, pero también ayudan a combatir situaciones excepcionales que requieren de una adaptación rápida. Debido a la adopción del teletrabajo en las organizaciones, ha sido muy común el uso de Internet of Thing (IoT), así como RPA para aportar flexibilidad en ciertos procesos automatizándolos.
El uso de la fabricación aditiva por impresión en 3D para dotar de material sanitario, el uso de técnicas de Deep Learning mediante Big Data para acelerar los procesos de investigación o el uso de Robots autónomos mediante Inteligencia Artificial (IA) para desinfectar superficies contaminadas son otros de los ejemplos de tecnologías adoptadas durante la pandemia.
Conclusiones
- Aunque ha disminuido 10 puntos, la principal barrera para la transformación digital sigue siendo la resistencia a la innovación y al cambio, seguida de cerca por la falta de formación de los trabajadores, que ha tenido un incremento, situándose en el 18% en 2021.
- Es importante destacar que pierde importancia la creencia como barrera que sean necesarias inversiones muy altas, así como modelos tipo sobre los que trabajar.
- Crecimiento importante de la automatización, la cual ha recuperado importancia con respecto al año anterior situándose en un 21% en 2021.
- Los aspectos relativos a la planificación de inventario han ganado importancia en este último año pasando de un 0% a un 6%.
- Llama la atención el descenso que tiene el mantenimiento con respecto al año anterior, pasando de un 14% a un 8%, así como la disminución de la planificación de la cadena de suministro como oportunidad de ahorro de costes que ha pasado a perder toda la importancia.