Boehringer Ingelheim integra el sistema de monitorización de condiciones de Ifm en sus unidades de tratamiento de aire
Las salas limpias son indispensables para la producción segura de productos sensibles que deben cumplir requisitos de calidad, como los de la industria farmacéutica. Y en este contexto, es muy importante que el suministro de aire de bajas partículas funcione correctamente en el laboratorio y en las salas de producción. Por ello, la empresa farmacéutica Boehringer Ingelheim supervisa sus sistemas de ventilación las 24 horas del día para garantizar un funcionamiento sin problemas. El mantenimiento basado en la condición podría llevar este proceso a un nuevo nivel. Boehringer Ingelheim está en camino de conseguirlo con su partner Ifm.
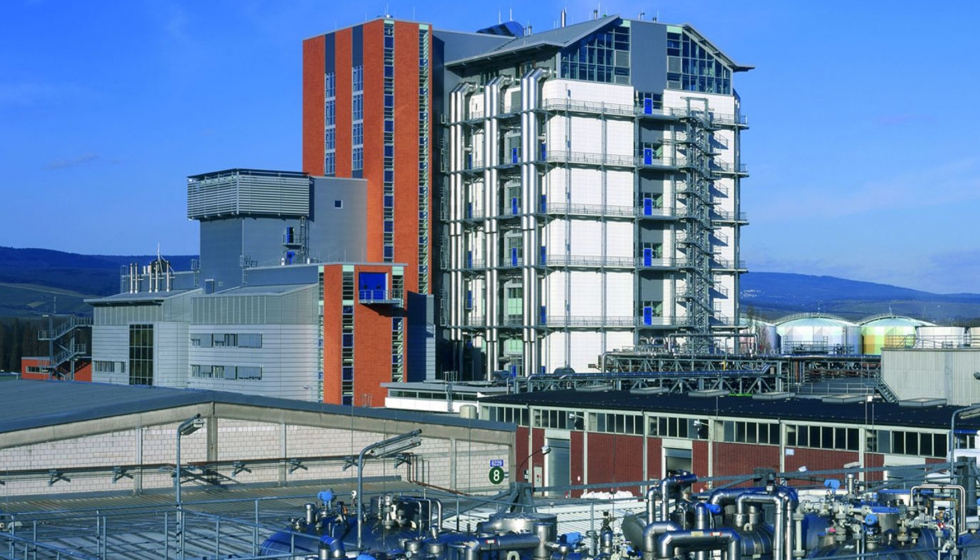
Desde 2008, el departamento de Ingeniería y Tecnología de Boehringer Ingelheim colabora con el especialista en automatización Ifm en el ámbito del análisis de vibraciones y rodamientos. El sistema de diagnóstico de vibraciones VSE100 desempeña un papel fundamental en la tecnología de procesos y ventilación, ya que garantiza el funcionamiento sin problemas de los sistemas de ventilación que cumplen las GMP (siglas en inglés de Buenas Prácticas de Fabricación). Se trata de directrices de aplicación internacional para el aseguramiento de la calidad que se utilizan principalmente en la fabricación de productos farmacéuticos.
El corazón del sistema es la unidad de evaluación VSE100, que ofrece entradas para hasta cuatro sensores de vibración. El comportamiento de las vibraciones se analiza y evalúa internamente. Los cambios anormales en el comportamiento de las vibraciones se detectan y se señalan en varias etapas mediante salidas de conmutación si se supera el valor límite. De este modo se garantiza una supervisión fiable de las vibraciones en máquinas e instalaciones. El desgaste, por ejemplo, en los rodamientos de los accionamientos, se detecta en una fase temprana antes de que se produzcan condiciones críticas o incluso fallos.
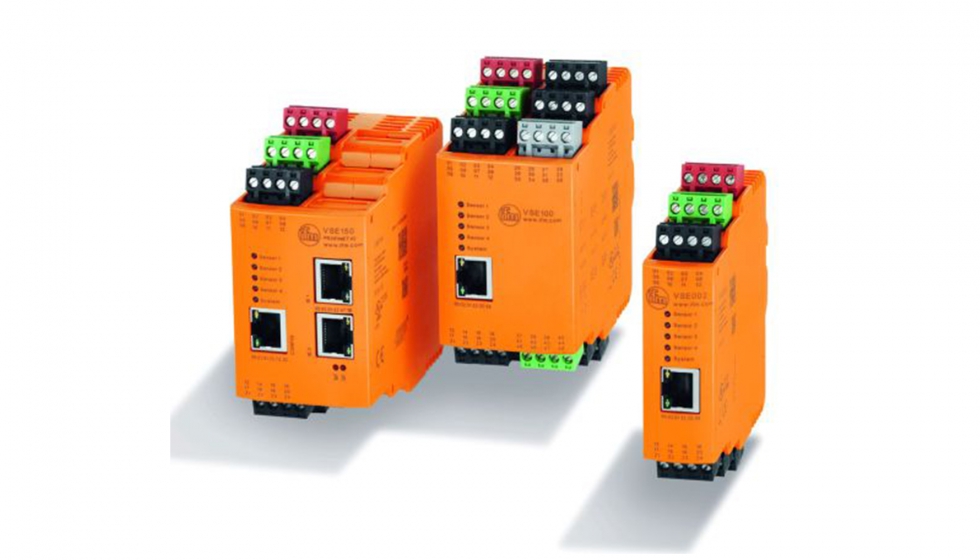
En la versión anterior del sistema de diagnóstico de vibraciones de Ifm, el comportamiento de las vibraciones y, por tanto, el estado de los ventiladores supervisados se visualizaba en el sistema de gestión de edificios con un semáforo. Cuando el color cambiaba de ‘verde’ a ‘amarillo’, los técnicos de servicio recibían indicaciones de posibles daños en el motor o el ventilador. Gracias al sistema, los sistemas de ventilación han funcionado sin problemas desde entonces. Sin embargo, para analizar más a fondo un mensaje, antes los técnicos de servicio tenían que conectarse con un ordenador portátil a la unidad de evaluación para leerlo y así evaluar los daños en detalle.
Hace unos tres años, el departamento de Ingeniería y Tecnología decidió realizar una inversión de futuro en el diagnóstico de vibraciones y rodamientos. Esto está asociado a un cambio del mantenimiento puramente preventivo al mantenimiento basado en la condición.
Rafael Cannas, director de mantenimiento y empleado de mantenimiento de Boehringer Ingelheim desde hace 26 años, explica: “Nuestro objetivo era implementar inicialmente una combinación de mantenimiento preventivo y basado en la condición. Un paso intermedio en nuestro camino hacia el mantenimiento basado en la condición es trabajar en la monitorización de la condición en nuestros equipos de ejemplo. En cuanto a la informática, nos basamos en el cuadro de mandos de Ifm que implantamos hace un año. Para el futuro, nuestro objetivo es la predicción de fallos basada en la IA. Se supone que los algoritmos calcularán y nos informarán de cuándo los equipos han alcanzado su vida útil restante”.
Varios sistemas probados
Al cabo de un año, se elaboró un currículum. Tras una evaluación exhaustiva, Boehringer Ingelheim se decidió por los sistemas de monitorización de vibraciones y rodamientos de Ifm. El factor decisivo fue la experiencia fiable y positiva con el sistema desde 2008, pero también el fácil manejo del cuadro de mandos que se utiliza para la evaluación.
Además, para Boehringer Ingelheim era importante tener en Ifm un partner que ya ha adquirido experiencia con estos sistemas en otros sectores industriales.
Una previsión precisa ahorra millones
El proyecto ‘Puesta en marcha del monitoreo de condición para el análisis de las vibraciones de los rodamientos’ comenzó en otoño de 2019. El objetivo: monitorizar los sistemas de ventilación seleccionados para el proyecto en un edificio de producción farmacéutica en Ingelheim para detectar el mayor riesgo económico de fallo.
Estos sistemas de ventilación abastecen a salas de la “clase D de salas limpias” sin excepción. El objetivo era supervisar la instalación únicamente de forma automática a través de una herramienta de análisis ya en el verano de 2020. Junto con Ifm, este objetivo se ha conseguido: los sistemas de ventilación se transformaron y se pusieron en funcionamiento en verano.
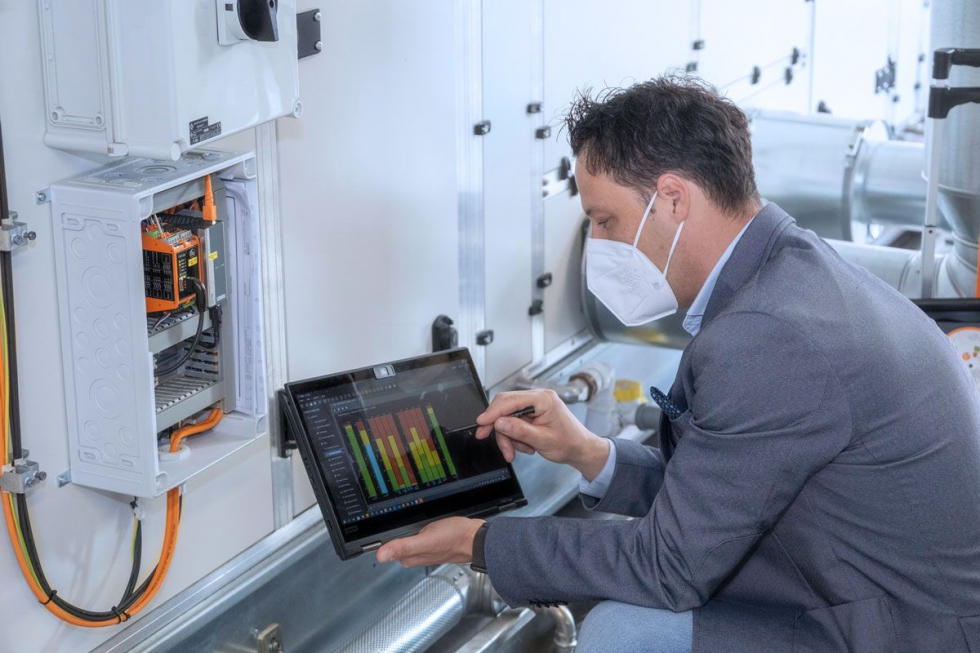
Ahorro a corto plazo de seis cifras
La formación se replantea en tiempos de la pandemia del COVID-19
Para ello, los datos del VSE100 se han integrado en una nueva arquitectura informática, y Boehringer Ingelheim colabora con los especialistas en datos de la filial de Ifm, Statmath, para llevar estos datos a una calidad utilizable para su posterior uso. “Nos conviene que statmath ya haya implementado con éxito precisamente estos puntos en la industria del automóvil y que, por tanto, tenga una amplia experiencia”, afirma Julia Kaufmann, directora de mantenimiento de Boehringer Ingelheim.
“En el contexto de la digitalización, el tema del mantenimiento del estado validado de los sistemas seguirá ocupándonos, al igual que la cualificación de nuestros propios técnicos para hacerlos aptos para el futuro. Ya hemos demostrado las ventajas de la monitorización de condición en nuestro proyecto piloto. En el futuro, prevemos predecir la probabilidad de que los equipos fallen, de modo que podamos utilizar ese conocimiento para planificar las reparaciones de forma que no perturben o interrumpan las operaciones de fabricación en su tiempo de producción”, explica Cannas.
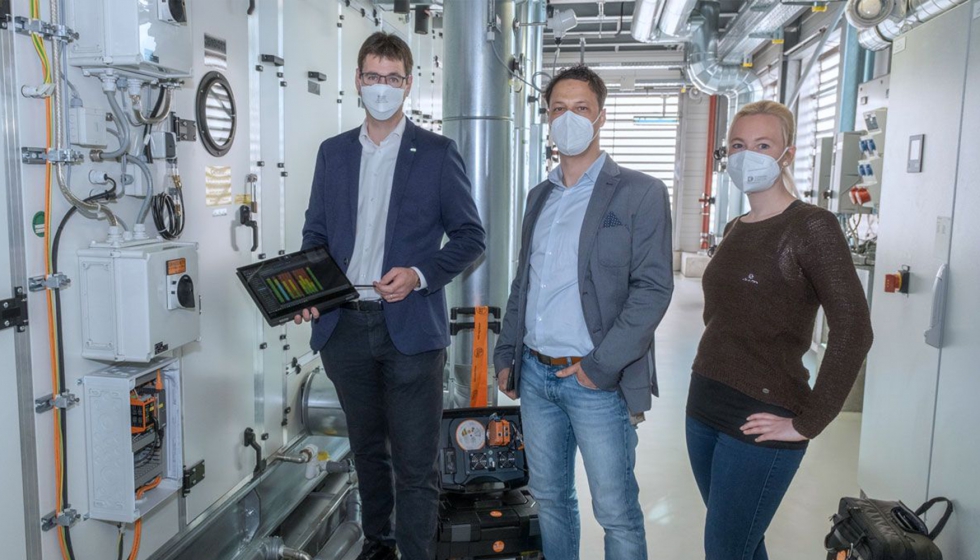
Conclusiones
El proyecto piloto de Boehringer Ingelheim lo demuestra: las empresas pueden beneficiarse significativamente del moderna monitorización de condición. Especialmente cuando el mantenimiento de las instalaciones de producción de gran relevancia puede llevarse a cabo según las necesidades y ya no en función del tiempo, se puede ahorrar en gran medida: La planificación específica del mantenimiento reduce los tiempos de parada, minimiza los costes de material y descarga al personal especializado y, por último, pero no menos importante, protege el medio ambiente.