Sistemas automáticos de manutención en el sector del automóvil
Principales medios de manutención automática
Se desarrolla a continuación una clasificación de los sistemas de manutención automática que se utilizan con mayor asiduidad en la industria del automóvil. A un primer nivel, se pueden clasificar en dos subgrupos, uno dedicado principalmente al transporte de material entre los diferentes puestos de un proceso productivo y otro más orientado a su utilización como sistemas de almacenamiento inicial, intermedio o final de los productos manipulados. Esta clasificación, no obstante, es relativa, pues a menudo estas dos funcionalidades básicas se entremezclan en un sistema concreto. Lógicamente, los diferentes medios logísticos utilizados se encontrarán interconectados entre sí mediante otros mecanismos de interacción humanos o automatizados (manipuladores, robots, etc.).
Medios de transporte de material
La funcionalidad de estos sistemas se encuentra orientada fundamentalmente al transporte, entre los diferentes procesos productivos y de almacenaje, de la materia prima, ensamblados intermedios y producto terminado en proceso de fabricación. En general, estos sistemas se utilizan en el movimiento de materiales de un tamaño y peso relativamente uniforme, a velocidades que pueden variar en un amplio espectro entre un conjunto especificado de posiciones, a lo largo de una serie de rutas prefijadas. Aunque esta característica se considera, normalmente, un requisito previo para la aplicación de este tipo de sistemas, existen también soluciones más flexibles basadas, por ejemplo, en la utilización de pequeños transportadores reubicables (como los utilizados en los aeropuertos).
Cintas transportadoras
En esta clase de sistemas, el producto se desplaza a lo largo de líneas cuya superficie de transporte consiste en un conjunto de rodillos o ruedas que rotan sobre su eje longitudinal, una serie de cintas sin fin, etc., dispuestas linealmente o en curva y con o sin pendientes. Suelen utilizarse para el transporte de producto a granel, agrupado en palés de carga o pequeños contenedores, o también como componentes individuales. Pueden instalarse directamente a nivel del suelo, sobreelevados mediante soportería apoyada en éste o bien en ejecuciones aéreas con soportería al techo de la planta.
El producto puede ser transportado de manera continua, intermitente o totalmente asíncrona, gobernando adecuadamente los mecanismos de tracción o los dispositivos de dosificación del producto transportado. En los sistemas más complejos, es posible también realizar el control de flujo del producto, al emplear mecanismos que permiten distribuir la unidad de carga en ciertos puntos a diferentes zonas del mismo u otro circuito. La complejidad tecnológica de estos sistemas puede variar desde sencillos sistemas de control “marcha-paro”, que interconectan dos puestos de trabajo para realizar el trasiego de material entre ambos, hasta sofisticados sistemas de transporte con direccionamiento del flujo que componen la principal línea de producción de una factoría, trenes de laminado con un desarrollado sistema para el control y sincronización de las velocidades de avance a lo largo de la línea, etc.
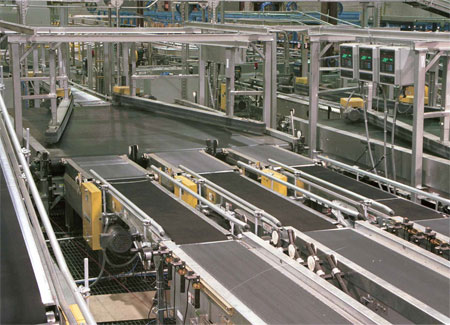
Transportadores monorraíl
En este caso, las unidades de transporte circulan ligadas, en general de modo equidistante entre sí, por medio de cadenas a lo largo de un único raíl que conforma un circuito cerrado de recirculación. La propulsión de esta cadena de componentes se realiza, en la mayoría de los casos, con dispositivos de arrastre mecánico, acoplados a esta cadena cinemática y comandados de forma continua por motores eléctricos, hidráulicos o neumáticos. Cada unidad de transporte dispone de un portador, suspendido generalmente mediante un gancho, sobre el que se dispone el producto individual o lote de productos a transportar y del que es posible descolgarlo, existiendo un elevado rango de pesos, dimensiones y formas para su ejecución. Asimismo, el rango de velocidades de transporte es amplio, oscilando desde las más pequeñas, que se utilizan en los sistemas de limpieza, desengrasado, lavado y secado de los productos, hasta las más elevadas cadencias, utilizadas en manutenciones más ligeras como ocurre, por ejemplo, en la industria textil.
El principal inconveniente de estos transportadores es la imposibilidad de poder controlar, internamente, la distribución de material: al ser un circuito cerrado de unidades de transporte fuertemente acopladas, no es posible distribuir el producto direccionando individualmente cada unidad a un determinado lugar. Una forma posible de lograrlo consiste en la aplicación de mecanismos que permitan el trasvase del portador, o del producto, desde las unidades de transporte de un determinado circuito a las existentes en otros circuitos independientes.
Transportadores birraíl
Se trata de una evolución de los descritos anteriormente y son conocidos en la industria con el nombre de sistemas ‘Power and Free’. Con el fin de evitar la limitación indicada en los sistemas monorraíl, relativa a la imposibilidad de controlar individualmente el desplazamiento y ruta de cada unidad de transporte, en este caso se dispone de dos cadenas en su configuración. Una de ellas (denominada habitualmente cadena motriz o ‘Power’) es similar a la descrita en el caso de los sistemas monorraíl; es decir, consiste en una serie de elementos, unidos entre sí mediante cadenas, que se desplazan de manera continua a lo largo de un circuito cerrado. Cada uno de estos elementos dispone de un mecanismo de arrastre con desenclavamiento, que puede ser acoplado y desacoplado de los portadores que circulan libremente por otra vía independiente (denominada cadena libre o ‘Free’), y que son los encargados verdaderamente de realizar el transporte del producto.
La posibilidad de desacoplamiento existente entre los elementos del circuito de arrastre y los portadores de la línea de transporte, permite desarrollar configuraciones topológicas más complejas, siendo posible, en este caso, el control individualizado de la ruta que sigue cada uno de los portadores de producto en el sistema. El control se realiza por medio de dispositivos de retención, que permiten forzar el desenclavamiento entre las unidades de arrastre y los portadores de manera independiente, y dispositivos de distribución, que permiten seleccionar la ruta por la que va a discurrir cada uno de los portadores. Por ejemplo, es posible desarrollar aparcamientos laterales a los circuitos del flujo principal para poder, de este modo, enviar cada portador a un puesto de trabajo concreto del sistema, clasificar el producto según la referencia transportada, etc. La acumulación de portadores en una determinada zona del circuito se obtiene por medio de soluciones, habitualmente mecánicas, que permiten su desenclavamiento automático con el sistema de arrastre, cuando éste se aproxima suficientemente al portador situado a continuación.
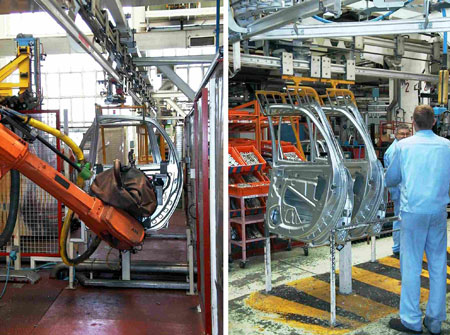
Aerovías
Estos sistemas constituyen otra variante de los basados en monorraíl, en los que la unidad de transporte dispone de capacidad de movimiento autónomo a lo largo de un raíl al que se encuentra enlazado mecánicamente. Éste dispone, en todo el trazado, de líneas de transporte de energía y comunicaciones que permiten implantar el control del desplazamiento individual de cada unidad a lo largo del mismo. Por lo tanto, en este caso cada unidad de transporte incorpora un sistema de propulsión (generalmente eléctrico) gobernado localmente por medio de un controlador especializado. Aunque la ejecución más habitual de estos sistemas logísticos está basada en la utilización de viales suspendidos o aéreos (de ahí su nombre), existen también configuraciones instalables a nivel del suelo o a media altura.
Las capacidades logísticas de este tipo de sistemas se ven incrementadas con la utilización de dispositivos que permiten controlar el direccionamiento de cada unidad a un determinado emplazamiento de un conjunto posible, normalmente por medio de cambios de agujas y desvíos electromecánicos o electroneumáticos. También es factible emplear aparcamientos laterales para estacionar las unidades de transporte en un puesto de trabajo, de manera que no se interrumpa el tránsito de otras unidades a través del circuito principal. Se utilizan para el transporte de productos relativamente pesados y las velocidades de transporte empleadas son habitualmente bajas, aunque es posible conmutarlas a lo largo de las zonas de un circuito utilizando, por ejemplo, dispositivos de regulación de velocidad o motores con múltiples velocidades en cada unidad de transporte.
Vehículos con guiado automático
Los transportadores analizados hasta este momento se utilizan mayoritariamente para la transferencia punto a punto de materiales a lo largo de rutas totalmente prefijadas de forma mecánica. Frente a éstos, los sistemas basados en la utilización de vehículos con guiado automático o AGV's (Automated Guided Vehicles) aportan fundamentalmente, desde el punto de vista logístico, una mayor flexibilidad a la hora de realizar modificaciones o ampliaciones en la configuración topológica de los circuitos de transporte. De manera similar a los equipos descritos en el subapartado precedente, estos sistemas logísticos disponen de un conjunto de vehículos autónomos, cada uno de los cuales puede transportar una unidad de carga, siendo la principal diferencia que en este caso su evolución no está mecánicamente ligada a la existencia de un vial o carril que direccione sus movimientos, permitiendo así realizar las funciones de transporte entre un número finito de localizaciones y rutas predefinidas, que suelen ser más fácilmente reubicables, modificables y ampliables que en el caso de las aerovías.
Gran parte de estos sistemas basan el subsistema de navegación local en el seguimiento de guías electromagnéticas, ópticas o químicas dispuestas habitualmente en el suelo (aunque existen sistemas basados en otras tecnologías como radiobalizas, sensores láser, plataformas de guiado inercial, visión artificial, etc.). La monitorización de las posiciones de los vehículos, y el control de tráfico, puede estar totalmente centralizada en un único controlador jerárquicamente superior o encontrarse distribuido en una serie de controladores locales en las diferentes secciones del sistema. En los puntos de distribución prefijados, se dispone de elementos que permiten comunicar los vehículos con el controlador principal de tráfico e intercambiar información, fundamentalmente órdenes de parada, identificación, selección de ruta y marcha.
Los vehículos deben interaccionar también con otros sistemas de carga, manipulación y descarga del producto transportado. Es característica la existencia de lugares dedicados a la recarga de los acumuladores de energía, normalmente eléctrica, de que dispone cada vehículo; dicha recarga puede realizarse de manera dinámica en puntos situados estratégicamente a lo largo del circuito o bien en aparcamientos retirados de las rutas principales de transporte destinados al efecto. En el caso de los puestos productivos, las operaciones pueden realizarse directamente sobre el propio vehículo o bien éste puede descargar el material en otro sistema intermedio y proceder, de inmediato, a la realización de otra tarea, todo ello de forma manual o automática.
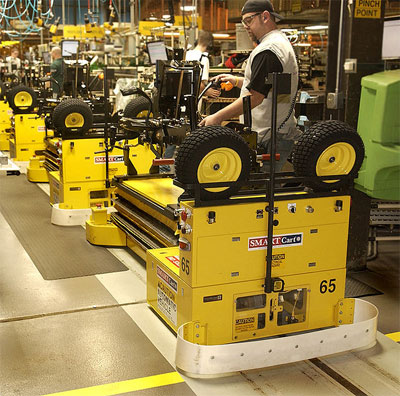
Medios de almacenamiento de material
La funcionalidad primordial de estos medios se encuentra orientada al almacenaje de las materias primas, componentes intermedios y productos terminados que se manipulan a lo largo de un determinado proceso productivo, pudiendo encontrarse situados en zonas interiores de la planta de fabricación o bien en edificios independientes. De modo general, disponen de zonas para la recepción del material a almacenar, medios físicos de almacenamiento en los que distribuir el producto recibido, dispositivos que permiten realizar la introducción y extracción de los productos allí almacenados y zonas de recogida de los productos solicitados al sistema. El nivel tecnológico también puede variar en estos sistemas desde soluciones manuales hasta las totalmente automatizadas. En este último caso, el sistema debe encargarse de la asignación automática de los productos recibidos a las correspondientes zonas de almacenamiento, así como de la selección de los productos que va a retirar para su envío a las zonas de recogida del material solicitado, respetando habitualmente el orden y prioridad de extracción de las peticiones recibidas.
Una de las decisiones estratégicas de consideración en los sistemas de almacenamiento automático, es la relativa a las políticas de almacenamiento que se van a implantar, pudiendo distinguir entre las “dedicadas” y las “aleatorias”. En el primer caso, existe una asociación explícita entre las clases o referencias de producto manipulado y las zonas dedicadas en exclusiva para su almacenaje, de manera que las operaciones de cálculo de asignaciones o selecciones de producto son simples, pues se basan en la determinación de la referencia a manipular y en el conocimiento de dichas asignaciones. Por el contrario, las políticas aleatorias permiten el almacenamiento de cada tipo de producto en cualquier posición disponible en el sistema, requiriendo por tanto la existencia de un subsistema de gestión de información que mantenga, en todo momento, una imagen de la situación de cada producto presente en el sistema, así como de las posiciones disponibles para el almacenamiento.
Almacenes aéreos
El almacenamiento en estos sistemas se realiza en el propio portador, que circula a lo largo de unas vías de transporte, pudiendo desplazarse autónomamente gracias a la acción de la gravedad o bien ser arrastrado con técnicas similares a las empleadas en los transportadores birraíl descritos anteriormente. Las zonas de acumulación propiamente dichas, se organizan habitualmente en conjuntos de líneas individuales de acumulación dispuestas en paralelo, a las que es posible dirigir cada uno de los portadores que se desea almacenar desde unos determinados puntos de acceso que regulan y direccionan el flujo a estas zonas a través de un vial de entrada, habitualmente compartido. Del mismo modo, existen puntos de evacuación a los que es posible dirigir los portadores almacenados en las líneas de acumulación a través de un vial de salida común. Estas zonas de acumulación en paralelo se disponen generalmente en posiciones sobreelevadas de la edificación, con el fin de no ocupar el valioso espacio que es necesario dedicar prioritariamente a los procesos productivos. Sin embargo, estos sistemas deben interaccionar, en las zonas de carga y descarga, con otros situados en planta, predominando en estos casos la utilización de dispositivos elevadores o rampas motorizadas en la interconexión de zonas situadas a niveles significativamente diferenciados.
Los almacenes aéreos deberían disponer de zonas de acumulación de portadores vacíos, cuya capacidad se dimensiona en función de las fluctuaciones previstas en los niveles de almacenamiento dinámico de producto, llegando en casos extremos a la necesidad de requerir la misma capacidad de almacenamiento que en las zonas de acumulación productivas. Las soluciones aplicadas varían desde aquéllas en las que el almacenamiento se realiza de forma independiente al propio sistema, hasta las que disponen de un circuito cerrado, con zonas de acumulación de portadores vacíos, que comunica las zonas de descarga con las de carga de material. Este tipo de medios se utilizan en general para el almacenamiento de grandes cantidades de productos con pesos relativamente pequeños y que deben ser manipulados a elevada cadencia.
Transelevadores
En estos sistemas, las zonas de acumulación de producto constan de una serie de estanterías apiladas, sustentadas por una soportería de pilares, uniformemente dispuestos a lo largo de la superficie horizontal dedicada, y unidos entre sí mediante vigas situadas a niveles equidistantes a lo largo del espacio vertical disponible, conformando así una rejilla de almacenamiento, en la cual cada posición dispone de un ancho y alto uniforme en el que es posible almacenar una o varias unidades portadoras de carga, generalmente contenedores o palés, en las que se encuentra el producto manipulado. La unidad de carga de estos sistemas puede variar desde pequeñas cajas que permiten almacenar, por ejemplo, componentes electrónicos básicos, hasta bandejas que contienen productos de varios centenares de kilos de peso. Es posible lograr la acumulación de más de un portador en cada una de las celdas de la estantería incorporando elementos de transporte dispuestos a lo largo de cada celda, que permitan el desplazamiento de los portadores allí almacenados, utilizándose para esta función, por ejemplo, caminos de rodillos motorizados o deslizantes, con o sin frenado inercial.
Los puntos o bahías para la carga y descarga de material suelen encontrarse dispuestos en los extremos de cada una de estas áreas de almacenamiento. La entrada y salida de los portadores en dichos puntos se realiza frecuentemente mediante cintas transportadoras motorizadas que comunican estos sistemas con otros medios logísticos. El trasvase de los portadores entre estos puntos y el conjunto de estanterías de almacenamiento se realiza por medio de mecanismos manuales, semiautomáticos o totalmente automáticos, cuya morfología da nombre a estos sistemas, pues constituyen el componente esencial del sistema. En el caso de los transelevadores, estos manipuladores constan de un pilar principal que puede desplazarse longitudinalmente sobre una vía o cremallera dentada situada en el suelo y que discurre a lo largo de una de las superficies laterales de la zona de almacenamiento. El sistema de tracción mecánica se acopla a un conjunto de ruedas o piñones, accionados generalmente por motores eléctricos, que se disponen sobre la misma vía o bien lateralmente. Cuando la altura del pilar y/o el peso de la unidad de carga manipulada son elevados, una vía paralela situada en la zona superior dirige su evolución a lo largo del recorrido y confiere mayor estabilidad y rigidez al conjunto. Sobre este pilar principal se articula un dispositivo elevador que puede desplazarse verticalmente a lo largo del mismo, utilizándose en estos casos para la tracción mecánica soluciones, basadas en poleas o piñones, comandadas por motores eléctricos, cilindros hidráulicos o neumáticos, etc.
Finalmente, sobre el elevador se acopla una plataforma que puede desplazarse transversalmente, con el objetivo de introducir o retirar los portadores de cada una de las estanterías existentes en la zona de almacenamiento considerada. Con respecto al utillaje empleado para el trasvase de las unidades de carga entre la plataforma del transelevador y las estanterías, existen soluciones basadas en uñetas, similares a las empleadas en las carretillas elevadoras, cintas de transferencia motorizadas, mesas con desplazamiento transversal, etc.
En los medios automatizados de este tipo, para el control de posición de cada uno de los ejes de estos componentes se aplica en general sistemas de odometría, siendo los empleados con mayor frecuencia los codificadores (encoders) relativos o absolutos, y los medidores láser. Los motores eléctricos más empleados son servomotores y/o motores asíncronos trifásicos, utilizando en este caso, para la regulación de velocidad y posición, convertidores de frecuencia. En el caso de utilizar políticas automáticas de almacenamiento aleatorio, es factible aplicar el principio de recirculación, de manera que, si se desea extraer un producto que no se encuentra en cabecera de la estantería, sea posible retirar los productos que le anteceden y almacenarlos en otra estantería hasta lograr el acceso al seleccionado. Sin embargo, en estos sistemas los retardos producidos por la necesidad de recirculación suelen ser mayores que en el caso de los sistemas de almacenamiento aéreo.
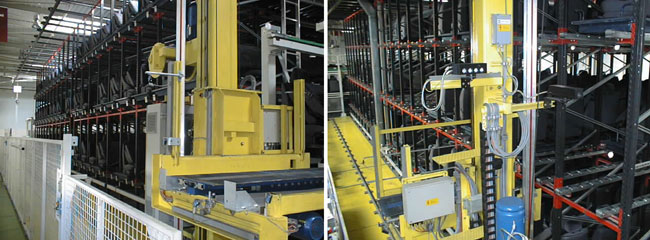