IK4-Tekniker muestra en BIEMH2018 sus tecnologías posibilitadoras para máquinas inteligentes
IK4-Tekniker expone en la BIEMH sus novedades para hacer frente a los retos de la digitalización industrial para máquina nueva y parque instalado de màquina.
La progresiva implantación de la Industria 4.0 y las tecnologías digitales en el sector de la máquina-herramienta presenta desafíos como el aumento de la exigencia de calidad, el incremento de los niveles de precisión o la introducción de sistemas automatizados, interconectados y con capacidad de funcionamiento autónomo. Para dar respuesta a estos y otros retos, el centro tecnológico vasco IK4-Tekniker trabaja un conjunto de tecnologías altamente innovadoras dirigidas tanto a nuevas máquinas inteligentes como a la incorporación de aplicaciones innovadoras en parque instalado de máquinas, que permitan entornos de fabricación digitalizados.
Estos desarrollos forman parte de la oferta tecnológica que el centro tecnológico lleva a la próxima edición de la Bienal Española de Máquina-Herramienta.
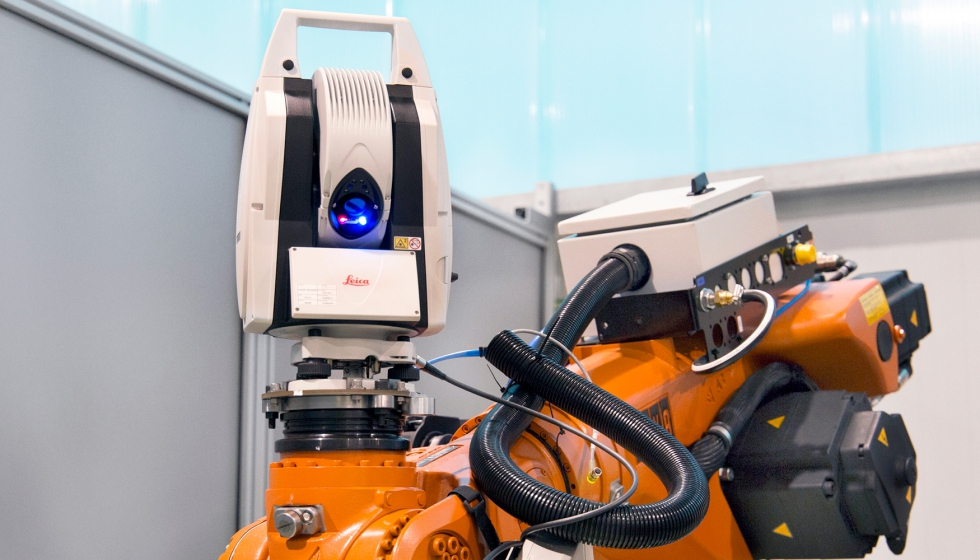
IK4-Tekniker da a conocer una propuesta de valor tecnológica que busca, además, dar respuesta a las nuevas demandas del sector y que desde el punto de vista tecnológico cuenta con muchas posibilidades. Para estructurar el análisis de “qué puede hacer más competitiva mi empresa y qué prestaciones le tengo que pedir a la máquina”, es bueno tener un modelo de referencia para el diagnóstico e identificación de oportunidades en el ámbito de Industria 4.0, enmarcado en el sector de máquina-herramienta.
A continuación, se describen las tecnologías posibilitadoras más relevantes en las que el usuario de máquina-herramienta se puede apoyar:
Flexibilidad y re-configurabilidad: Robótica flexible
La primera operación que se realiza en un proceso de mecanizado es la carga de la pieza sobre un utillaje predeterminado. Esta operación suele ser manual y en los casos en lo que se automatiza, se construyen sistemas especiales, muy predefinidos por las características de las piezas. Por estos motivos los sistemas de carga son muy poco flexibles y muy difícilmente reconfigurable. IK4-Tekniker puede ofrecer la solución completa (bin picking, visión artificial, generación de trayectorias, control de fuerza, etc.) que permite a las empresas aumentar la productividad de sus máquinas y reducir el coste de estas operaciones de carga y descarga, habitualmente realizada de forma manual.
La solución está orientada a empresas que mecanizan piezas en centros de mecanizado y células de fabricación flexible.
Máquina virtual: modelizado y simulación de máquina-proceso
El objetivo es investigar de manera integral en las tecnologías de simulación (de máquinas y procesos), monitorización y análisis de datos para configurar una plataforma de modelización híbrida y actuación ágil que permita a empresas fabricantes de máquinas y, en especial a sus usuarios, optimizar (en tiempo y coste) drásticamente sus procesos de diseño, ramp-up, ciclo de vida de producción y adaptación a nuevos requisitos, incrementando, además, sus ratios de calidad y fiabilidad.
Health assesment
Sensorizar las máquinas de manera eficiente, distribuida y global mediante dispositivos de monitorización multivariable permite que se tenga de manera continua y en tiempo real, información del estado de los diferentes componentes de la máquina, del estado de los procesos productivos, de los parámetros de calidad de las piezas fabricadas y del entorno variable que rodea a la producción.
A esta medida de los sensores, tanto internos como externos, desde IK4-Tekniker se propone la realización de una serie de test de máquina, muy sencillos y rápidos, que permitan conocer el estado de la misma, mediante la evolución temporal de diferentes parámetros. Es lo que IK4-Tekniker denomina ‘Fingerprint.
De este modo, se puede comprobar cómo funcionan las máquinas y hacer un seguimiento de la salud de los equipos de forma controlada.
Este sistema permite conocer el estado de salud de la máquina a la hora de la toma de decisiones para la operación y el mantenimiento. Asimismo, permite adelantarse a la aparición de errores geométricos en las piezas, avanzando hacia la fabricación “cero defectos”, fundamental sobre todo en el caso de piezas de alto valor económico.
Optimización del proceso
Hasta ahora, los modelos teóricos de simulación analizaban la máquina-herramienta y el proceso de mecanizado de forma independiente, sin ninguna interacción entre sí.
Actualmente, se están desarrollando plataformas en las que se integran diferentes modelos de simulación para analizar el funcionamiento de la máquina y sus procesos de mecanizado de manera global. Esta tecnología supone un nuevo concepto de simulación que engloba proceso y máquina.
Por otra parte, los modelos de simulación se utilizaban en la fase de diseño como modelos predictivos para obtener información antes de realizar la operación real. Sin embargo, en la actualidad se ha dado un salto, de forma que sea posible utilizar los resultados para efectuar un control online durante el mecanizado.
Se han desarrollado estrategias de optimización multiobjetivo para que a partir de la información recopilada en tiempo real y en base a los modelos y patrones establecidos, los propios medios productivos sean capaces de tomar de manera autónoma e inteligente decisiones sobre los parámetros del proceso y sobre las condiciones dinámicas de los diferentes componentes mecánicos, que aseguren, en cada caso, la consecución de los objetivos productivos marcados (costes, producción, consumo energético, estados de máquina, etc.). Este proceso redundará en una optimización de los procesos de fabricación.
Fleet management: pasar de una máquina a la gestión de flotas
El primer paso es sensorizar y monitorizar las máquinas con los diferentes modelos de simulación, tanto de máquina como de proceso, trabajando todos de forma coordinada (en bucle cerrado) y enriquecidos con los ensayos ‘Fingerprint’. Estos permiten optimizar los procesos y conocer el estado de salud de los diferentes componentes de la máquina.
Una vez dado ese importante paso, el siguiente es conocer el estado de toda la flota de máquinas de un fabricante.
Referentes en inspección y medida
A medida que el volumen de la máquina-herramienta aumenta, la verificación de la geometría de estos sistemas se complica cada vez más. En este escenario, el uso de tecnologías de verificación tradicionales como la interferometría o los niveles electrónicos dejan de ser útiles, ya que no garantizan la elevada precisión que demandan sectores de gran exigencia como la aeronáutica.
Con el objetivo de garantizar la geometría y funcionalidad de las máquinas herramienta, IK4-Tekniker apuesta por la técnica de multilateración para desarrollar un procedimiento que permita medir la geometría de una máquina-herramienta en todo su volumen de trabajo en un plazo de tiempo más corto, de forma automatizada y con mayor precisión que las tecnologías actuales. En concreto, el centro tecnológico vasco ha completado el desarrollo tecnológico con el uso de un Láser Tracker situado sobre un sistema mecatrónico. Este desarrollo se encuentra en la actualidad en proceso de patente.
Industry 4.0 + Inspección y Medida = Verificación automática e integrada en máquina
El sistema también permite detectar fácilmente pequeñas diferencias en el comportamiento de la máquina a lo largo de un periodo de tiempo prolongado y reducir su deriva térmica. La aplicación real de esta solución puede verse funcionando en el espacio expositivo del centro tecnológico en la Bienal.