Industria 4.0, el camino a la smart factory para la industria alimentaria: retos y palancas
En mi opinión, hay que ser justos con la industria de alimentación y bebidas, y reconocer la enorme evolución que ha experimentado en los últimos años, fruto de los cambios en los hábitos de consumo. Este desarrollo es, sin lugar a duda, un factor clave en el desarrollo-país, ya que estamos hablando de la primera industria en facturación con un volumen de negocio superior a los 95.000 millones de euros, y que representa el 20,2% del empleo industrial en España.
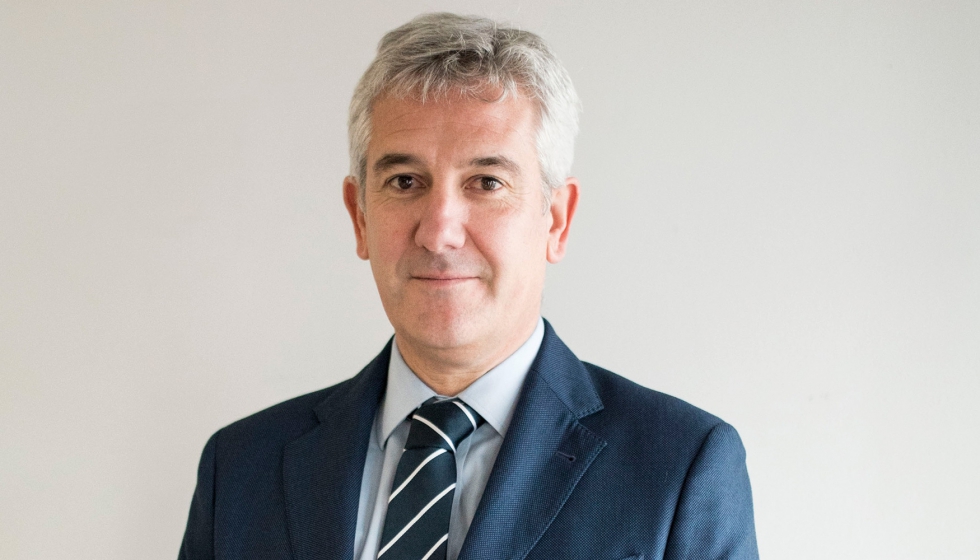
Para entender el camino andado y planificar el que nos queda por recorrer, hay que poner en el centro de este proceso a nuestro cliente, ya que los cambios en sus gustos y modos de consumo están impulsando la revolución del sector:
- Los consumidores requieren estar cada vez más conectados a las empresas productoras y canales de distribución,
- Demandan innovaciones constantes en los productos,
- Exigen respuesta ágil adaptada a su modelo de consumo.
Todo esto nos lleva a movernos hacia entornos de personalización en serie, con una producción extremadamente individualizada y ágil.
En esta visión centrada en el consumidor, la aparición de nuevos modelos de negocio que integran los requisitos del cliente con los procesos de producción y distribución de manera colaborativa, van a adquirir una relevancia fundamental en el futuro. Podemos empezar a hablar del 'consumidor conectado' que requiere de experiencias personalizadas en los productos que consume. Esta personalización afectará a la configuración del propio producto, atendiendo a requisitos personalizados de composición o envasado, así como al modo de entrega en cuanto a cantidad, plazo y localización.
La transformación de la industria hacia fábricas inteligentes es una condición imprescindible en este proceso, y uno de los puntos clave en este camino es el cuestionamiento y la reinvención de los procesos de explicitación y distribución del conocimiento en planta. Es un camino apasionante que ofrece diferentes escenarios por los que cualquier compañía puede transitar, en función del nivel de madurez operativa y tecnológica que adquiera.
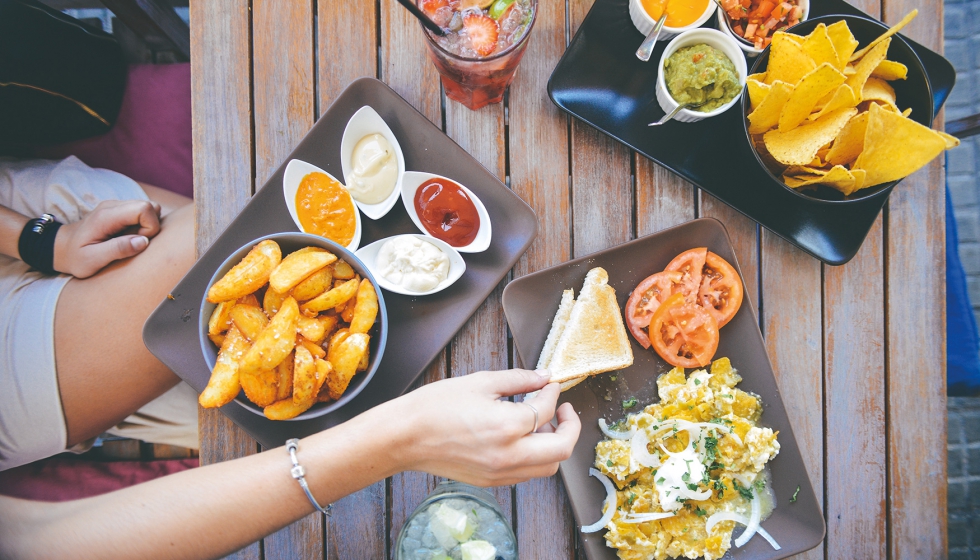
Primer paso: control de las operaciones en planta
La primera etapa en este proceso es la definición y estandarización de los procesos en planta que permita la modelización de los mismos, implantando herramientas que comparan de forma objetiva la situación actual y la deseada. La planta empieza a ser gestionada mediante KPIs que permiten identificar las pérdidas de valor y establecer dinámicas de mejora orientadas a la eliminación del desperdicio.
En esta fase se hace necesaria la implantación de herramientas de fábrica digital y el despliegue de modelos de excelencia operacional para la reducción de pérdidas. Los equipos de decisión en planta disponen de una plataforma de fábrica visual sobre la que apoyan la toma de decisiones.
La optimización del OEE y la consecución de procesos robustos mediante aplicación de SPC y 6sigma deben ser objetivos irrenunciables en esta etapa.
Segundo paso: comprender los procesos en planta
Cuando el modelo descrito en la etapa anterior alcanza un importante grado de madurez, nuevos retos empiezan a evidenciarse necesarios para la organización; no es suficiente robustez elevada y alto grado de calidad, necesito cero defectos; los tiempos de cambio de formato reducidos no son bastante, necesito cambio cero; la fiabilidad que me ofrece el preventivo y el predictivo no son suficiente para las exigencias de disponibilidad de mis líneas. Dispongo de procesos controlados y de KPIs que permiten identificar los gaps entre la situación real y la prevista, pero evidenciamos que el camino de reducción del desperdicio y la mejora del OEE, ha llegado a su límite y tenemos que activar nuevas palancas.
La experiencia de los equipos de planta es importante y su grado de conocimiento de los procesos es elevado, pero mis tecnologías de fabricación son complejas y el conocimiento es difícil de explicitar. Hemos obtenido ganancias importantes mediante la reducción sistemática de las pérdidas de valor, pero necesito un conocimiento explícito de cómo funcionan mis procesos en planta para seguir evolucionando.
Estamos evidenciando algunos de los síntomas que indican que estamos claramente en un punto de inflexión. Es el momento de incorporar más inteligencia a nuestro modelo de planta.
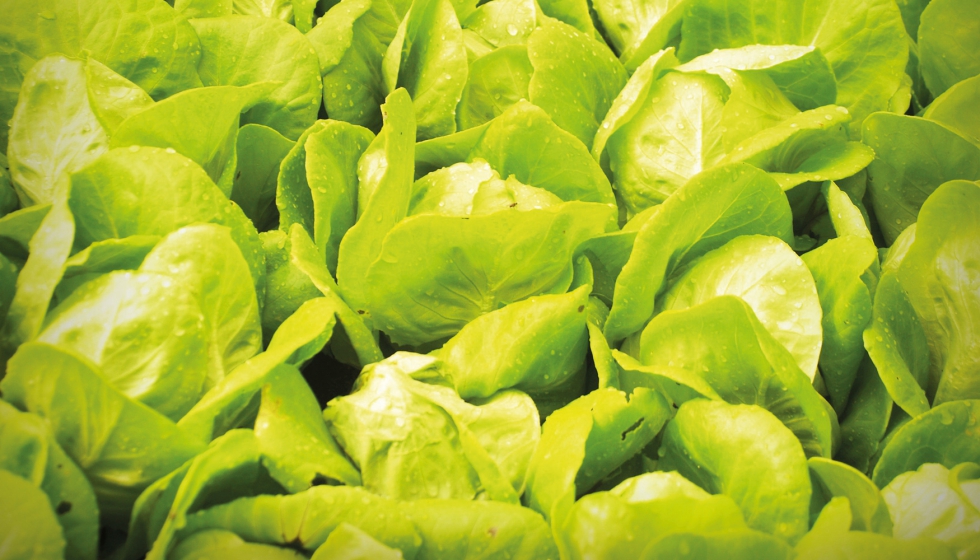
Es el momento de aplicar herramientas Machine Learning que generen modelos matemáticos de nuestros procesos productivos y del comportamiento de nuestros activos. Permiten entender cómo se relacionan la variables de regulación con los outputs obtenidos, identificar la condiciones de contorno en cada punto de operación y en definitiva, ser capaces de explicitar el conocimiento intuitivo acumulado por nuestras personas durante años de experiencia.
Identificamos nuevas condiciones de operación y regulación de los procesos y equipos que mejoran de forma sustancial la productividad y robustez de los mismos. Más importante aún, generamos en nuestras personas la conciencia de que la mejora de los procesos no se basa sólo en el control de KPIs, sino que tiene su fundamento en el conocimiento profundo de las reglas que los gobiernan.
Ya estamos en condiciones de abordar la última fase.
Tercer paso: dominar los procesos
Disponemos de conocimiento explícito de nuestros procesos que nos permite regularlos inteligentemente, pero también hemos aprendido que el control de los procesos depende sensiblemente del punto de operación y que éste es cambiante y nos obliga a adoptar cambios cuando el contexto varía.
Un paso adelante es embeber esa inteligencia en los propios procesos, de forma que vayan aprendiendo de forma permanente y dispongan de funciones que les permitan la adaptación a la situación actual y la auto-regulación atendiendo a las condiciones de operación de cada momento. La materia prima informa a la instalación de sus parámetros específicos y la línea se adapta; disponemos de modelos que permiten la identificación de la necesidad de revisión o sustitución de los útiles empleados; pronosticamos la probabilidad de aparición de un modo de fallo asegurando la fiabilidad de nuestros activos;… nuestros medios en planta incorporan funciones embebidas que les permiten estar trabajando permanentemente en condiciones óptimas de operación.
Un apasionante camino que, independientemente del grado de madurez en que se encuentre, toda empresa es capaz de recorrer. Importante; identificar con precisión el origen y trazar con determinación el roadmap hasta el primer punto de destino. Después… Todo sigue.