Análisis de las instalaciones de RTM necesarias para fabricar piezas de automoción de composite de fibra de carbono
Para llevar a cabo el presente análisis se han realizado simulaciones numéricas por elementos finitos para determinar las condiciones de procesado, y se han diseñado las células de fabricación seleccionando los equipos más avanzados del mercado. La principal conclusión es que el HP-RTM es 9 veces más caro, debido a que las presiones de procesado son mucho más elevadas (moldes, inyectoras y prensas más caros) y el CRTM es un 80% más rápido.
1. Introducción
Los polímeros reformados con fibra han obtenido un gran interés en los últimos años por su alta resistencia y rigidez específica, alta absorción de energía de impacto por unidad de peso, capacidad de amortiguar vibraciones y excelente resistencia a la fatiga [1]. El alto coste operativo de las actuales técnicas de fabricación ha restringido el uso de los composites [2]. Por esta razón, se está trabajando en el desarrollo de nuevas alternativas más eficaz para la fabricación de compuestos. El moldeo por transferencia de resina (Resin Transfer Moulding, RTM) termoestable es un proceso bien establecido para ciertos nichos de aplicación [3]. Sin embargo, para la fabricación de piezas de alto contenido en fibra (mayores que 40% para aplicaciones estructurales) se encuentran problemas, ya que, aumentando el contenido en fibra se reduce la permeabilidad de la preforma, aumentando así el tiempo de llenado, creando zonas sin impregnar y generando altos contenidos en vacíos. Para hacer frente a este problema se proponen diferentes estrategias dirigidas a modificar el proceso de RTM convencional. Una de las alternativas más prometedoras para obtener una inyección rápida es utilizar procesos como High-Pressure RTM (HP-RTM), proceso que posibilita la inyección de resina a altas presiones (100 bar) [4]. La rápida inyección, hace que se reduzca el tiempo de llenado y por consiguiente aumentan el índice de producción/rendimiento. Otra de las estrategias para la reducción del tiempo de llenado y contenido de vacíos, es combinar el RTM tradicional con la compresión. Este proceso se denomina Compression Resin Transfer Molding (CRTM) y puede ser una técnica adecuada para la fabricación de piezas estructurales partiendo de las ventajas del RTM convencional [5-9]. En el CRTM, a diferencia del RTM convencional, el molde está parcialmente cerrado cuando se inyecta la resina. Esto hace que aumente la sección transversal, aumentando la permeabilidad y posibilitando que la resina fluya más fácil, reduciendo el tiempo de llenado. En algunos casos, el molde está abierto, generándose así un hueco entre la superficie de la preforma y la pared superior del molde, facilitando el flujo preferencial de la resina. Una vez que se inyecta la dosis de resina en el hueco, se cierra el punto de inyección, y a continuación se desplaza el molde superior hacia abajo hasta cerrar el molde. Este último movimiento hace que la resina que estaba en el hueco empieza a impregnar la preforma y conforma el laminado hasta la cota de espesor deseado. Por lo tanto, en vez de que la resina impregne la preforma en la dirección del plano como en RTM, en el CRTM impregna en la dirección del espesor.
El objetivo de los diseñadores y fabricantes de componente de automoción es la reducción de coste y peso por pieza. Por lo que, el objetivo del presenta artículo es mostrar una comparativa de estructura de costes de los procesos HP-RTM y CRTM para un volumen de producción de 90.000 techos al año. Estas dos últimas técnicas son las candidatas para obtener piezas estructurales rentables de automación [4,5].
2. Estudio: techo del vehículo
2.1. Definición del techo
Para el análisis de este estudio se ha seleccionado un techo de un vehículo urbano con una ventana circular. En cuento a las características geométricas del techo, el área proyectada es de 1,72 m2 y el espesor es 3 mm. La rigidez torsional y de flexión del techo de material compuesto (epoxy reforzado con un tejido cuasi isotrópico y un contenido en fibra del 60% en volumen), es equivalente a un techo de acero de 0,7 mm de espesor. El volumen de producción de 90.000 piezas por año se divide durante un periodo de siete años con tres relevos (1.754 h/relevo).
Diferentes estudios de costes [2] han demostrado que el coste asociado al material es dominante en el coste total del componente. Pero, sabiendo que en este estudio la resina y la preforma que se utilizan es la misma para HP-RTM y CRTM, el coste de materia prima no se tendrá en cuenta. Los parámetros cinéticos y reológicos de la resina, como la permeabilidad de la preforma se muestran en la tabla 1. El tiempo de gel (tgel), el cual gobierna el límite de la viscosidad de la impregnación en función de la temperatura de curado, (Tcuring) está gobernada por la ley de Arrhenius [10]:
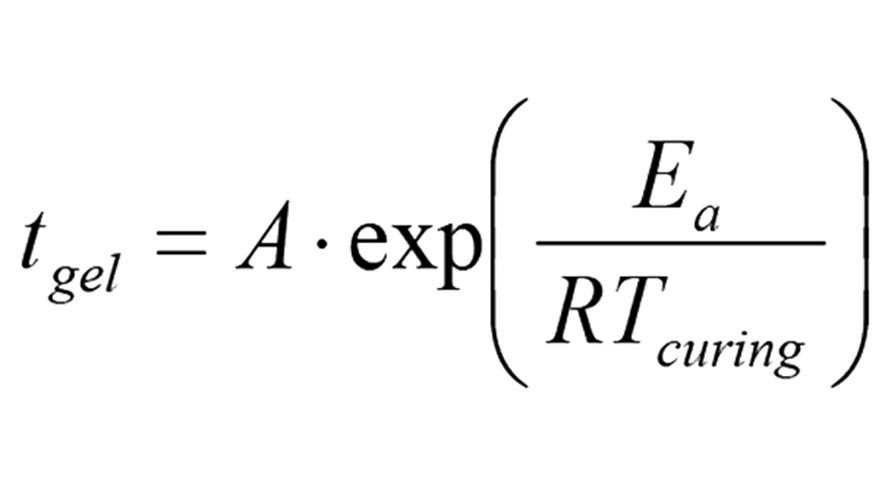
donde Ea es la energía de activación, A es contante cinético y R es contante universal de gases.
La reacción de polimerización Rα se calcula mediante el modelo de Kamal and Sourour.
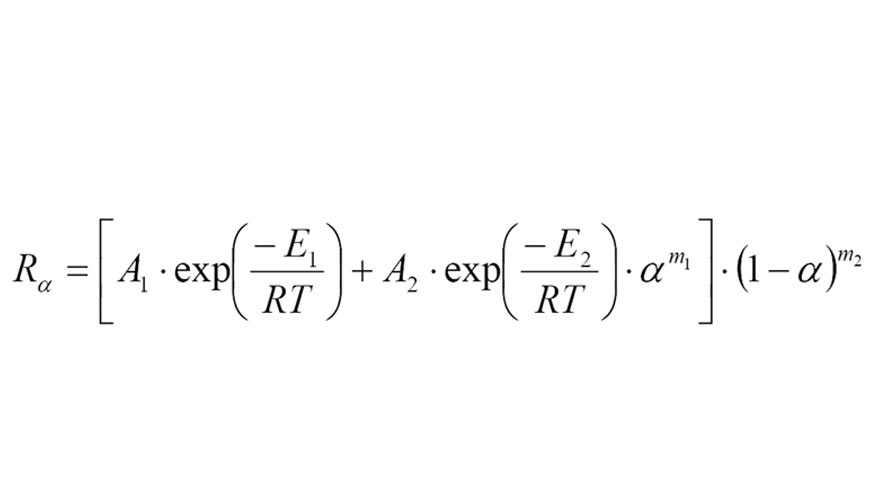
donde A1 and A2 son contantes, E1 y E2 energías de activación, m1 y m2 contantes catalíticas y T temperatura absoluta de la reina.
![Tabla 1. Propiedades de resina [10] y preforma [11] Tabla 1. Propiedades de resina [10] y preforma [11]](https://img.interempresas.net/fotos/1294452.jpeg)
2.2. Análisis de costes
El coste de fabricación es la suma de material, equipamiento, mano de obra y gastos generales. La mano de obra se considera equivalente para todos los casos estudiados por el hecho de la alta automatización. Como CRTM es un nuevo proceso los gastos generales no se pueden definir, por lo que no se tendrán en cuenta. Por lo que, el coste del proceso depende de; equipamiento (unidad de inyección, prensa y robot), área de la instalación, utillaje y energía. El análisis del cálculo de costes se lleva a cabo mediante el estudio paramétrico de costes (TCM) [2]. TCM divide el proceso en los pasos más relevantes para la fabricación del techo. Los pasos para las dos variantes de RTM son; carga de la preforma en el molde, cierre del molde, inyección de resina, curado de la resina, apertura del molde y extracción de la pieza.
3. Resultados y discusión
3.1. Parámetros de procesado
Las simulaciones del llenado se han llevado a cabo con el software PAM-RTM. El número de puntos de inyección afecta al tiempo de llenado, siendo clave para la optimización del RTM. Sin embargo, como el objetivo del presente trabajo se centra en comparar los variantes del RTM, se utilizará un único punto de inyección para los procesos de HP-RTM y CRTM. La posición de los puntos de inyección, ha sido optimizada para reducir el tiempo de llenado. Para las simulaciones del CRTM tendrá un hueco de 1,2 mm de espesor, lo que corresponde al volumen de resina a inyectar. La permeabilidad del hueco está relacionada con su espesor, que le confiere una la alta permeabilidad. Esto permite asumir que la resina fluye solo por el hueco [5-9], sin impregnar la preforma. La compresión del CRTM se ha definido como 0,6 mm/s, sumando 2 s al tiempo de la inyección de la resina. La presión de inyección, tiempo de llenado y máxima fuerza de cierra se muestran en la tabla 2.
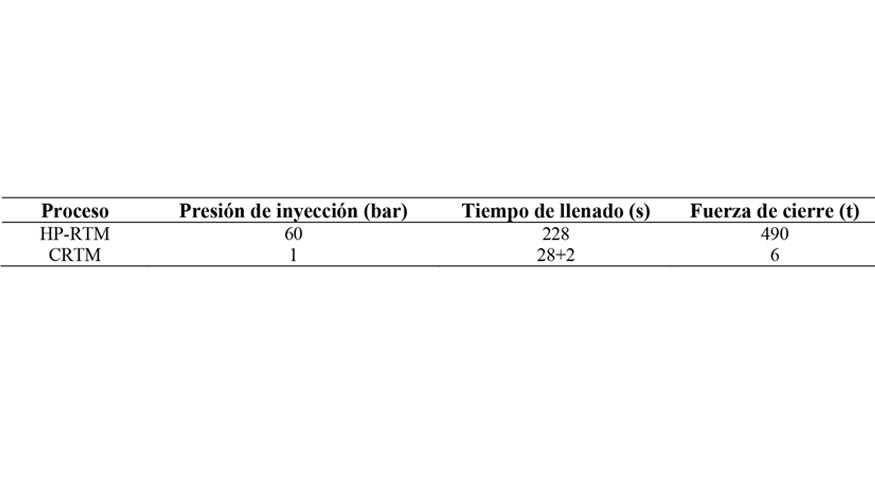
Tan interés como la fuerza de cierre es la distribución de presión al final de llenando. Como se muestra en la figura 1, la distribución de presión es asimétrica en las dos vertientes del RTM. En el caso del HP-RTM el molde está cerrado a tope, por lo que el control de paralelismo actúa durante la fase de cierre de molde y no tiene que contrarrestar grandes esfuerzos. Sin embargo, en el caso de CRTM, aun generando presiones más pequeñas, debe mantener el paralelismo con el molde semi-abierto, lo que requiere de un sistema de control de paralelismo específico.
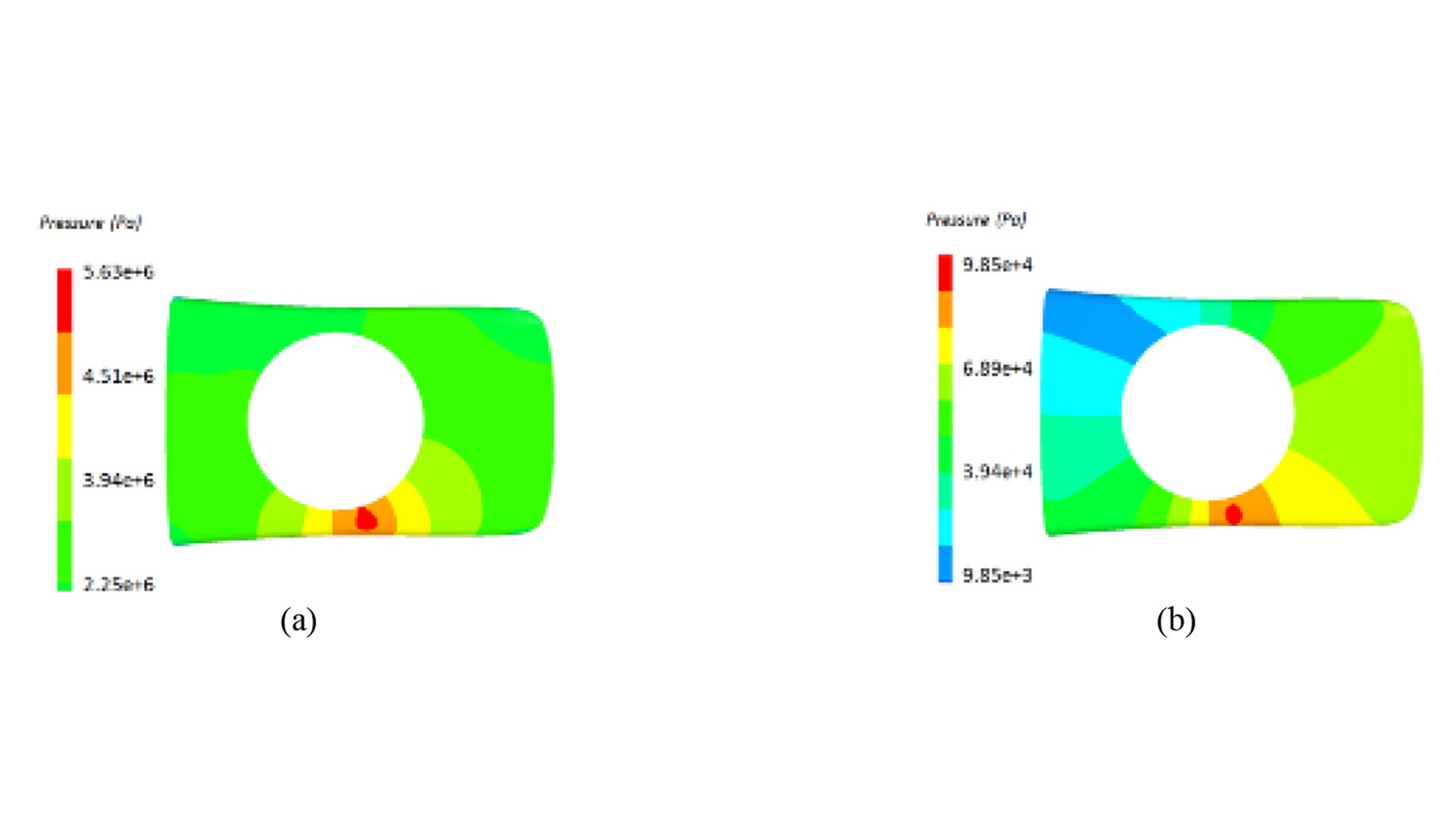
Una vez estimado el tiempo de llenado, se puede seleccionar la temperatura de curado. Aumentar la temperatura permite un menor tiempo de curado [12], pero reduce el tiempo de gel. Basándose en esto, la temperatura de curado se selecciona asegurándose de que el tiempo del gel es mayor que el tiempo de llenado. Partiendo de la ecuación 1, e introduciendo los tiempos de llenado de la tabla 2, se determina la temperatura de curado para cada variante del RTM y el correspondiente tiempo de desmoldeo (ecuación 2) para un grado de conversión del 80%. Se asume que la inyección es isoterma, por lo que el tiempo de inyección está incluido en el tiempo de curado. Para calcular el tiempo total de ciclo por cada variante del proceso de RTM, la carga de la preforma y extracción de pieza, como cierre y apertura del molde deben sumarse al tiempo de curado. Estas operaciones adicionales son las mismas para todos los procesos estudiados, pero la contribución relativa es diferente. En la tabla 3 se resumen los tiempos de ciclo.
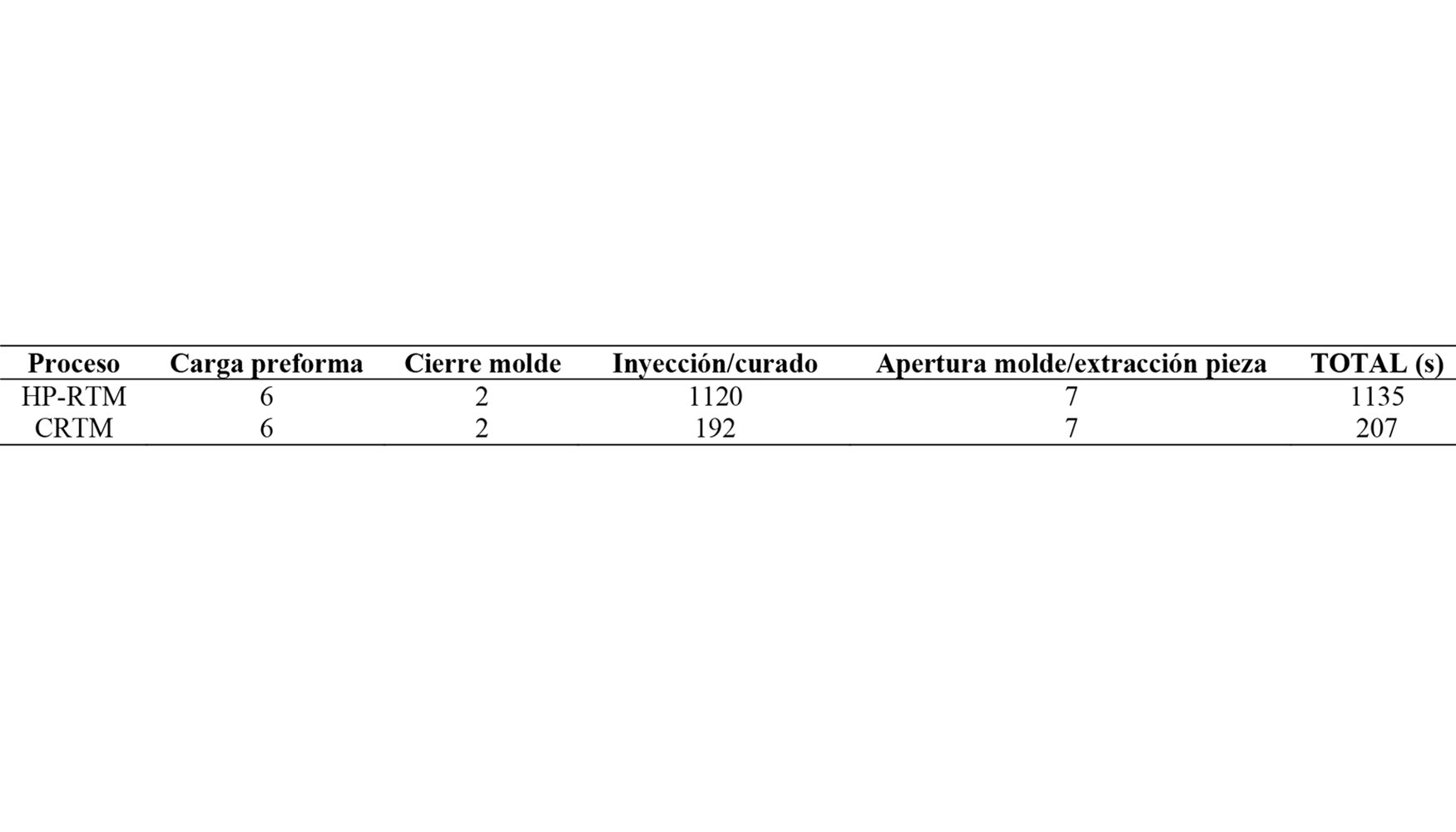
3.2. Coste de la instalación
Basándose en el tiempo total de ciclo, y para un volumen de producción de 90.000 techos/año de producción, la célula de HP-RTM debe equiparse con 6 prensas y la de CRTM con 1. Siendo los tiempo de llenado largos, posibilita utilizar un único robot para la carga de la preforma y otra para la descarga. Con este dato, se calcula el área ocupado de cada proceso siendo 385 m2 para HP-RTM y 57 m2 para CRTM. El coste de la prensa, unidad de inyección, molde, robot y el área ocupado en la planta se muestra en la tabla 4. El coste de la prensa de cada variante del RTM se ha calculado usando la fuerza de cierre como único parámetro influyente. La unidad de inyección para HP-RTM es más cara, mientras que para CRTM una inyectora convencional es suficiente. Los moldes para HP-RTM, como la presión interna es mayor, deben ser mayores que para CRTM, aunque se asume que es el mismo para ambos procesos. La diferencia del coste del robot, aun siendo idénticos, Se justifica por el control más complejo en el caso de HP-RTM al tener que trabajar con más prensas.
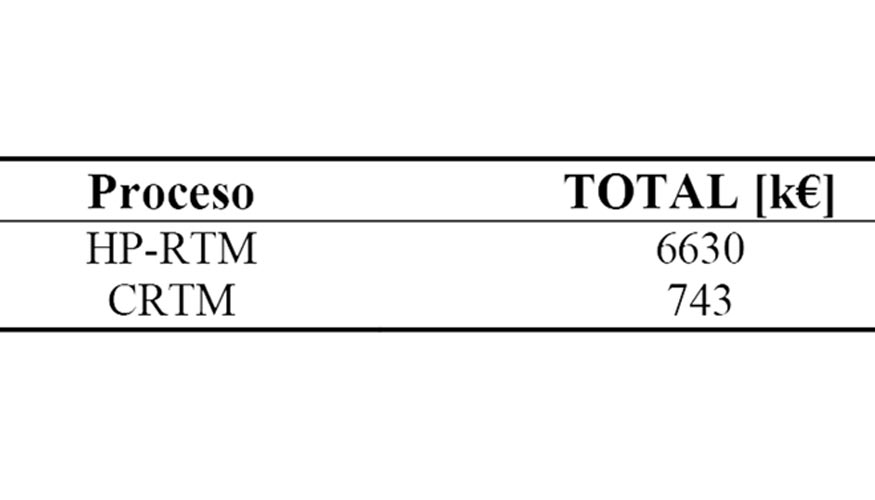
3.3. Coste de energía
Se asume que el consumo de energía se asocia al de la prensa y la del sistema de calefacción del molde para el curado. El consumo de energía de la prensa depende de la fuerza de cierre y del tiempo de ciclo. Los sistemas hidráulicos consumen energía para mantener el fluido en circulación (~30%). Además, para compensar la presión interna generada en la cavidad del molde, se necesita una bomba de mantenimiento. Estos dos característicos valores dependen de la fuerza máxima de cierre de la prensa y se muestran en la tabla 5 por cada proceso de fabricación. Las dimensiones del molde son 600 mm × 2.500 mm × 3.000 mm. La energía consumida para mantener la temperatura de curado ha sido calculada asumiendo que el aislamiento es perfecto. También se asume que el espesor del molde de acero (50 W/km2) es de 500 mm y está cubierto con 20 mm de material aislante. La temperatura de la planta se asume que es 25 °C y tiene un coeficiente de transmisión de calor por convección de 5,8 W/km2. La energía consumida en el curado de cada proceso se muestra en la tabla 5.
![Tabla 5. Consumo y coste de energía. Coste energía 0,1 €/kWh [13] Tabla 5. Consumo y coste de energía. Coste energía 0,1 €/kWh [13]](https://img.interempresas.net/fotos/1294457.jpeg)
3.4. Coste del techo
El coste final del techo, así como cada uno de los factores que contribuyen en él, se resume en la tabla 6. Partiendo del CRTM como referencia, el coste de fabricación del techo con HP-RTM es de 9,2 veces más caro. El coste de equipamiento y utillaje, y especialmente el número de unidades, son las variables más relevantes, ya que representan el 90% del coste total de cada proceso. Por otro lado, en número de prensas afecta directamente en el área de la instalación.
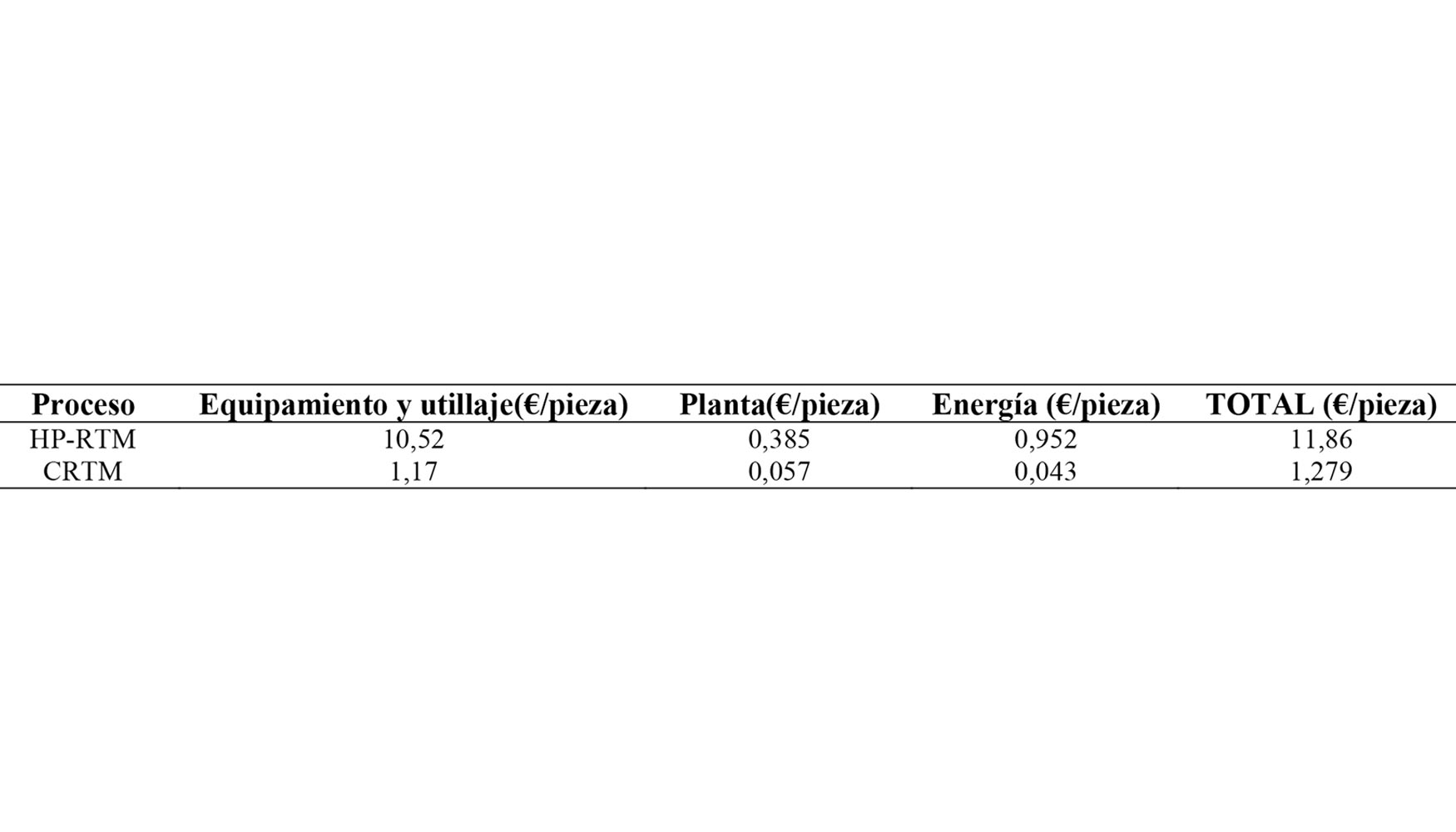
4. Conclusiones
Se ha estimado el coste de fabricación de un techo de automóvil fabricándolo mediante el proceso HP-RTM y CRTM. La principal conclusión es que el coste del HP-RTM es 9,2 veces superior al CRTM. Esto se debe al corto tiempo de inyección del CRTM, posibilitando usar temperaturas de moldeo altas y así acelerar el curado del composite. La principal consecuencia es que para fabricar 90.000 techos/año, la instalación de CRTM debería estar equipada con una única prensa/molde, mientras que se necesitarían 6 para HP-RTM. El área de la planta es directamente proporcional al número de prensas, por lo que los costes del HPRTM también son mayores. Los resultados de la simulación muestran las fuerzas de cierre de la prensa para el CRTM es 6 t y 490 para HP-RTM. Por lo que, el molde, prensa y unidad de inyección del CRTM son los más económicos. Se puede concluir que el CRTM es un proceso prometedor para pieza de gran área y geometría simple.
Referencias
[1] P. Feraboli, A. Masini, A. Bonfatti. Advanced composites for the body and chassis of a production high performance car. International Journal of Vehicle Design, 44: 233-246, 2007.
[2] M.G. Bader. Selection of composite materials and manufacturing routes for costeffective performance. Composites Part A: Applied Science and Manufacturing, 33: 913–934, 2002.
[3] B. Räckers. Ch. 1 Introduction to resin transfer moulding. In T.М. Kruckenberg and R. Paton, editors, Resin Transfer Moulding for Aerospace Structures, 1–24. Springer, Dordrecht, 1999.
[4] R. Chaudhari, M. Karcher, P. Elsner, F. Henning. Characterization of high pressure RTM processes for manufacturing of high performance composites, 15th European Conference on Composite Materials, Venice, Italy, 24-28 June 2012.
[5] P. Simacek, S.G. Advani. Modeling flow in compression resin transfer molding for manufacturing of complex lightweight high-performance automotive parts. Journal of Composite Materials, 42: 2523–2545, 2008.
[6] P. Bhat, J. Merotte, P. Simacek, S.G. Advani. Process analysis of compression resin transfer molding. Composites Part A: Applied Science and Manufacturing, 40: 431–441, 2009.
[7] J. Merotte, P. Simacek, S.G. Advani. Resin flow analysis with fiber preform deformation in through thickness direction during Compression Resin Transfer Molding. Composites Part A: Applied Science and Manufacturing, 41: 881–887, 2010.
[8] W.A. Walbran, B. Verleye, S. Bickerton, P.A. Kelly. Prediction and experimental verification of normal stress distributions on mould tools during Liquid Composite Moulding. Composites Part A: Applied Science and Manufacturing, 43: 138–149, 2012.
[9] J. Aurrekoetxea, A. Agirregomezkorta, G. Aretxaga, M. Sarrionandia. Impact behavior of carbon fiber/epoxy composite manufactured by vacuum assisted compression resin transfer molding. Journal of Composites Materials, 46: 43–49, 2013.
[10] W.B. Young. Development of a helicopter landing gear prototype using resin infusion molding. Journal of Reinforced Plastics Composites, 28: 833–849, 2009.
[11] R. Parnas. Ch.7 Preform permeability. In T.М. Kruckenberg and R. Paton, editors, Resin Transfer Moulding for Aerospace Structures, 1–24. Springer, Dordrecht, 1999.
[12] A. Gupta, P.A. Kelly, S. Bickerton, W.A. Walbran. Simulating the effect of temperature elevation on clamping force requirements during rigid-tool Liquid Composite Moulding processes. Composites Part A: Applied Science and Manufacturing, 43: 2221–2229, 2012.