Los tres recursos imprescindibles para la óptima comunicación industrial son la información, la instrumentación y la formación
Hacia una planificación efectiva de las comunicaciones industriales
En los últimos años las necesidades de comunicación entre dispositivos dentro del entorno industrial ha experimentado un crecimiento exponencial. Esta rápida expansión ha dado como resultado en muchos casos una pérdida de perspectiva sobre el adecuado diseño, implementación y tendido de las diferentes redes industriales que deben convivir en una planta. Cada uso da lugar a determinados requerimientos que pueden entrar en conflicto con otros, tanto a nivel hardware como software. Pese a que puede parecer sorprendente, es habitual en la industria no alcanzar la estabilidad necesaria en las comunicaciones y tener dificultad en la diagnosis de las problemáticas existentes.
Clásicamente podíamos distinguir dos tipos de comunicación industrial: una comunicación vertical donde el flujo de la información se desplazaba desde y hacia el autómata, los ordenadores de control y los sistemas MES y ERP. Por otro lado, una comunicación horizontal desde el propio autómata a los diferentes elementos de campo como entradas y salidas, impresoras de etiquetas, paneles de operador, etc.
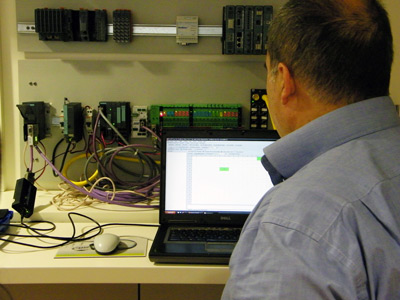
Como consecuencia del avance tecnológico industrial han aparecido muchos otros dispositivos que difícilmente podemos incorporar a la clasificación anterior: telefonía IP, controles de accesos, cámaras de vigilancia… Adicionalmente han surgido nuevas inquietudes y necesidades que deben abordarse sin falta como son el control de la seguridad de las personas y las cosas ante ataques internos o externos, la protección de datos o la protección de la propiedad intelectual.
Los departamentos de IT de las empresas han sabido adaptarse dentro del entorno de oficina a esas necesidades que acabamos de citar, pero las características de las comunicaciones industriales hacen que no todas las soluciones aplicables en oficina sean aplicables en planta. Los errores más comunes suelen venir por fallos en la concepción y montaje de las infraestructuras, y en menor medida por interferencias y fallos en dispositivos.
¿Qué características caracterizan a las comunicaciones Industriales respecto a las de oficina?
Vamos a citar algunas:
- Multimedio. Mientras que en oficina las comunicaciones se centran sobre todo en Ethernet, dentro de la industria podemos encontrar otros medios físicos, por ejemplo, basados en tecnología 485 como Profibus, Devicenet, Serie…
- Arquitectura. La arquitectura típica de oficina, basada en una estructura en árbol a base de switches contrasta con la que podemos encontrar para una comunicación de bus de campo como Profinet, con elementos en línea, en árbol o en anillos redundantes.
- Disponibilidad. Un timeout de 5 décimas de segundo, inapreciable por ejemplo en un proceso de impresión de un informe, es completamente inaceptable dentro de una comunicación industrial donde un pequeño retraso de 10 milésimas de segundo puede provocar el paro de una máquina.
- Especificaciones de protocolo. Dentro de las comunicaciones industriales los dispositivos suelen comunicar entre sí con un protocolo bastante determinado (aunque generalmente propietario). Por ejemplo entre una pantalla de operador y un autómata o entre ese mismo autómata y su periferia las tramas utilizadas en la comunicación son fácilmente identificables y raramente codificadas.
- Funciones de seguridad. Muchos elementos industriales no incorporan un sistema operativo diseñado específicamente para el control de la seguridad de acceso o modificación de la información que manejan, siendo relativamente sencillo acceder a ellos desde la red.
A nivel de diseño, montaje y explotación de la red también hay que tener en cuenta algunos aspectos:
- Personal. El personal encargado de dichas comunicaciones suele tener una formación generalista y no especializada.
- Multitecnología. Las comunicaciones industriales se basan en diferentes tecnologías con diferentes características. Por ejemplo, no tiene nada que ver una configuración de seguridad OPC para la monitorización industrial que una comunicación basada en Profibus.
- Extensión. La extensión de una red industrial puede requerir la conectividad entre dispositivos separados centenares de metros lo que puede implicar problemas específicos en la separación de redes.
- Dispositivos. Los dispositivos y accesorios utilizados en comunicación industrial disponen muchas veces de funcionalidades especificas que difícilmente son apreciadas por los departamentos de IT (aceleración de tramas de diferentes protocolos, mirroring…) y viceversa, funcionalidades IT no son implementadas por los departamentos de automatización: VPNs, segmentación…
Entonces, ¿cómo se debe abordar un proyecto de mejora de las comunicaciones industriales de una planta ya en funcionamiento? ¿Por dónde comenzar? Como premisa, cabe recalcar que las soluciones de comunicaciones dentro de los ámbitos industriales difieren enormemente dependiendo del sector productivo. Por ejemplo, en el ámbito de control de entradas y salidas, la industria de manufactura requiere de altas velocidades en distancias cortas; el control de procesos exige distancias medias a velocidades medias y las comunicaciones remotas, por ejemplo en la gestión del agua, funcionan con distancias importantes donde la velocidad no un factor determinante.
Es imprescindible disponer de las herramientas necesarias para responder a los desafíos y concretar una mejora de las comunicaciones efectivas. Los tres recursos considerados como imprescindibles serían la información, la instrumentación y la formación.

En primer lugar es necesario un conocimiento exacto de todos los dispositivos que conforman nuestra red de comunicaciones, sus características, interconexión y parámetros de funcionamiento. Es muy frecuente que un departamento de mantenimiento no disponga de dicha información o que la responsabilidad de la misma esté repartida entre diferentes departamentos de una empresa: ingeniería, mantenimiento, IT....
En segundo término, sobre la instrumentación se ha de tener en consideración que buses específicos requieren herramientas específicas: desde un osciloscopio digital, un comprobador de cables, un analizador de protocolos...
En relación a la formación, el tercero de los recursos necesarios para abordar un proyecto de mejora de las comunicaciones en planta, no se puede ignorar que muchos estándares de comunicación industrial incorporan especificaciones técnicas particulares que hay que tener en cuenta durante el diseño, tendido y puesta en marcha. Es necesario disponer de la formación adecuada en dichos estándares para afrontar los problemas. Asimismo, la información reportada por la instrumentación necesita de la correspondiente formación para ser analizada y poder aplicar las contramedidas adecuadas para solucionar problemas.
La arquitectura perfecta sería la que nos permite cumplir con las expectativas de velocidad y disponibilidad necesarias para el funcionamiento de las instalaciones, que prevé las posibilidades de ampliación futuras y que tiene en cuenta la debida protección de la misma contra interferencias externas, como ataques voluntarios e involuntarios.
Adicionalmente, hay que contemplar también aspectos relativos a la alta disponibilidad, ya que muchas instalaciones requieren una redundancia en los sistemas y en las comunicaciones para obtener una alta disponibilidad en el funcionamiento; al acceso remoto, sobre todo en el caso donde los suministradores de maquinaria ofrecen a sus usuarios diagnóstico y mantenimiento remoto que muchas veces representa un punto débil en el acceso a la red que debe ser convenientemente protegido, a la seguridad, esto es, la protección de la red contra intrusiones, y por último, en relación a la aplicación de estándares, siempre necesarios en este tipo de proyectos pero complejos ya una misma red puede incorporar diferentes tipologías.