Diseño de un amortiguador activo para la eliminación de chatter en máquina-herramienta
En este trabajo se muestra el actuador electromagnético diseñado íntegramente en IK4-Ideko para la eliminación de chatter en operaciones de mecanizado. Además del diseño del mismo, se pueden observar los diferentes ensayos de validación (temperatura, linealidad…) que se han llevado a cabo en dicho actuador y los resultados de mejora que se han obtenido al introducirla en un centro de mecanizado.
1. Introducción
Hoy en día, las vibraciones autoexcitadas o chatter son unas de las restricciones más importantes de los procesos de mecanizado. Estas vibraciones se producen principalmente debido al efecto regenerativo [1][2] y son causantes de acabados superficiales inaceptables, de roturas de herramienta y de la reducción de vida de diferentes elementos mecánicos. Una de las soluciones más empleadas para aumentar el margen de estabilidad es probablemente la de añadir un amortiguador pasivo sintonizado a la estructura [3][4]. Esta técnica no es nueva y ha sido ampliamente usada desde que fue propuesta por Den Hartog [5]. Sin embargo, el uso de los amortiguadores pasivos no es factible en muchos procesos de mecanizado donde la dinámica del sistema puede variar durante el proceso.
Los actuadores activos pueden superar parte de estas limitaciones con su capacidad de adaptarse a unas condiciones cambiantes. Estos actuadores básicamente producen una fuerza de reacción, controlada mediante un algoritmo de control, sobre la estructura principal.
El desarrollo de absorbedores activos tuvo su origen en la industria aeronáutica. En una publicación de 1968, Bies and Yang [6] mostraron que los problemas que presentan los absorbedores pasivos podrían solucionarse añadiendo un elemento activo al absorbedor pasivo. En 1970, Cowley and Boyle [7] propusieron el uso de un actuador inercial electromagnético con un acelerómetro para introducir amortiguamiento activo sobre la estructura de una máquina herramienta.
La combinación de dispositivos activos y sensores forman una solución mecatrónica avanzada, cuyo comportamiento es comparable a la de un material inteligente como los actuadores piezoeléctricos. De hecho, los actuadores inerciales tienen mejores características para mejorar el comportamiento dinámico de las máquinas de grandes dimensiones en operaciones de desbaste [8].
Los actuadores piezoeléctricos suelen ser colocados sobre la máquina en serie, es decir, están dentro del flujo de la fuerza y por tanto, transmiten fuerzas de corte. Esto requiere que los estos actuadores tengan una alta rigidez. Sin embargo, los actuadores inerciales suelen ser colocados paralelamente, manteniendo así la rigidez original de la estructura [8][9]. La introducción de actuadores inerciales para máquinas de grandes desbastes ha sido estudiada por varios autores en los últimos años. Ehmann y Nordmann [8], por ejemplo, recomendaron la introducción de actuadores inerciales en las máquinas-herramienta de grandes dimensiones. Entre los actuadores inerciales, destacan sobre todo los electromagnéticos, aunque también ha habido aplicaciones donde la tecnología hidráulica ha sido empleada, como Brecher y Schulz [10], que desarrollaron un actuador electro-hidráulico para ensayar diferentes estrategias de control para la eliminación de chatter. La tecnología hidráulica es interesante debido a las grandes fuerzas y desplazamientos que ofrecen, pero también presenta grandes desventajas como los problemas de mantenimiento, no-linealidad, y los retrasos que conllevan.
En lo que se refiere a los actuadores electromagnéticos, se debe mencionar que el consumo energético será mayor sobre éstos que sobre los piezoeléctricos, ya que se debe superar continuamente la resistencia del mismo actuador, mientras que los piezoeléctricos solo necesitan energía para cambiar su estado. Aun así, este mayor consumo disminuye su importancia debido al hecho de que el coste de los actuadores piezoeléctricos puede ser hasta 3-4 veces mayor que un actuador electromagnético. Además, los actuadores electromagnéticos presentan la ventaja de que no hay contacto físico entre la parte móvil y la fija, lo que hace que sean muy usados para aplicaciones de vibraciones. Entre los dispositivos electromagnéticos, los actuadores de fuerza de reluctancia o fuerza de atracción ofrecen grandes fuerzas, pero esta fuerza es proporcional al cuadrado de la velocidad e inversamente proporcional al cuadrado del gap de aire. Esto hace que estos actuadores sean difíciles de controlar y no sean normalmente usados para aplicaciones de gran precisión. Los actuadores de fuerza de Lorentz, son capaces de generar menor fuerza, pero la linealidad que ofrecen hace que sean muy usados en el control de vibraciones. En este caso, la fuerza es proporcional al campo magnético, a la componente de velocidad perpendicular a este campo y a la carga de la partícula, por lo que cuando se usan imanes permanentes la fuerza es únicamente proporcional a la corriente aplicada (ver Figura 1). En la literatura se han desarrollado también varios actuadores inerciales electro-magnéticos que se basan en las fuerzas de Lorentz y que han servido para eliminar chatter sobre centros de mecanizado [9][11].
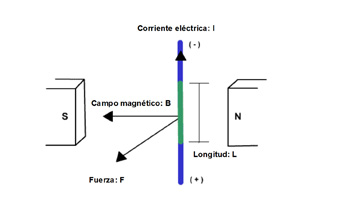
En los últimos años, se han desarrollado y patentado otros actuadores que combinan tanto las fuerzas de reluctancia como las fuerzas de Lorentz [12]. Estos actuadores denominados como MICA, ofrecen una mayor fuerza, pero requieren un guiado muy preciso. En este trabajo, se presenta el desarrollo de un pequeño actuador activo basado en las fuerzas de Lorentz, y que ha sido íntegramente diseñado en IK4-Ideko. En el apartado 2, se describe el diseño del actuador, que se puede dividir en 5 partes: los requerimientos, el diseño magnético, el diseño mecánico, el diseño de la electrónica de potencia y lo configuración final. En el tercer apartado se muestran los ensayos que se han realizado para validar el actuador y finalmente se resumen las conclusiones.
2. Diseño del actuador
2.1. Requerimientos
El diseño del actuador es una tarea de gran importancia debido a que los actuadores suelen tener sus no-linealidades y limitaciones que deben tomarse en cuenta a la hora de su dimensionamiento. El objetivo de este proyecto ha sido el de familiarizarse con diferentes aspectos en el diseño de actuadores de este tipo. Por ello, el actuador desarrollado ha sido un dispositivo a pequeña escala que sirva para máquinas-herramienta de no muy grandes dimensiones. Debido a la importancia que tiene la linealidad del actuador para aplicar ciertas estrategias de control o diferentes filtros, se ha procurado construir un actuador capaz de realizar como mínimo 120 N de la forma más lineal posible. El ancho de banda de frecuencias debe estar entre los 20-90 Hz, debido a que la mayoría de los problemas de vibraciones estructurales están en este rango.
2.2. Diseño magnético
El diseño magnético se ha basado en una variante de motor lineal con un curso limitado. Para ello se han fabricado dos bobinados que transportarán la corriente sinusoidal con la frecuencia deseada. Mediante la introducción de imanes permanentes de neodimio (NdFeB) y gracias a la ley de Lorentz, se generará una fuerza de desplazamiento lineal sobre la parte móvil del actuador
El dimensionamiento de los imanes y de los bobinados se ha basado en un cálculo de elementos finitos magnéticos (Flux), donde se ha podido calcular la fuerza teórica obtenible con el diseño deseado. En la Figura 2 se pueden observar el modelo y el resultado del flujo magnético sobre dicho modelo.
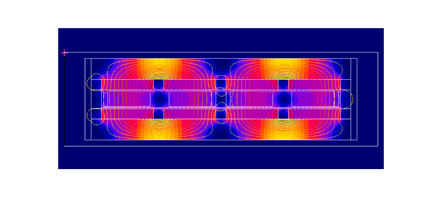
Figura 2. Modelo de elementos finitos magnéticos mediante Flux.
2.3. Diseño mecánico
Aparte del diseño magnético, es necesario diseñar correctamente el guiado encargado de soportar las fuerzas magnéticas. Este diseño cobra importancia debido a que el sistema de guiado será a posteriori el que dotará de la linealidad necesaria al actuador y el que determinará la rigidez del mismo. En este proyecto, se ha diseñado un doble flexo para dicha función. Los flexos presentan como mayor ventaja la linealidad, lo que hace interesante su uso en este tipo de aplicaciones. Además, el hecho de que sea doble hace que el movimiento sea totalmente lineal, es decir, verticalmente no tendrá ningún desplazamiento. Esto resulta interesante en esta aplicación, ya que este movimiento que ocurre entre el bobinado y los imanes debe ser el menor posible.
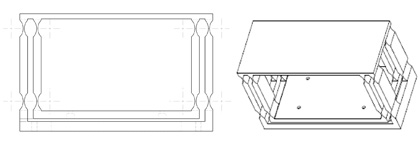
Figura 3. Diseño del doble flexo.
Para dimensionar este flexo, se han realizado dos cálculos mediante elementos finitos (I-deas). Por un lado, se ha lanzado un cálculo para comprobar si los flexos aguantarán a fatiga las fuerzas magnéticas generadas. Además de soportar la menor tensión posible, debe tener la suficiente rigidez para que el desplazamiento de la parte móvil no sea muy alto. Por otro lado, se ha realizado un cálculo dinámico para predecir el comportamiento dinámico que tendrá el flexo. En este caso, interesa que el modo de suspensión del propio flexo ocurra en una frecuencia baja, para que no afecte al comportamiento a la hora de realizar el control activo. Por lo tanto, para cumplir dicho objetivo debemos tener la menor rigidez posible, siempre y cuando se cumpla lo calculado en el primer cálculo. Otra opción es la de aumentar la masa móvil, pero esta masa tiene un espacio limitado dentro del actuador, por lo que la masa móvil también tendrá su valor máximo. Finalmente tras diferentes modelos, se ha diseñado un flexo capaz de soportar oscilaciones a fatiga y con un modo de suspensión que rondará los 18 Hz contemplando una masa móvil de unos 7 kg. Esta frecuencia del modo de suspensión se encuentra muy cerca del rango deseado y podría afectar en parte a funcionamiento del actuador cuando se actúe sobre máquinas con una frecuencia cerca de este modo de suspensión del actuador. Para solucionar este problema, habría que reducir la rigidez del flexo, pero esto conllevaría un debilitamiento a la hora de afrontar el problema de la fatiga, y durante el diseño del flexo se ha visto que no es viable. Por tanto, la solución que se va a proponer es la de no cambiar el diseño del flexo y atacar este problema desde el punto de vista del control [11]. El actuador dispone de un acelerómetro colocado en la parte fija que medirá la vibración a reducir. Para recibir estas señales, el actuador dispone de conectores en los que se podrá conectar el cable con total facilidad. La señal de corriente también será introducida mediante un conector Harting.
2.4. Diseño de la electrónica de potencia
Tras desarrollar el dispositivo, es necesario el proveerlo de energía para que pueda generar las señales sinusoidales y de este modo se obtenga la fuerza de vibración. En el caso de este actuador, se ha optado por el servo amplificador Elmo Violin de 0.95kW de potencia.
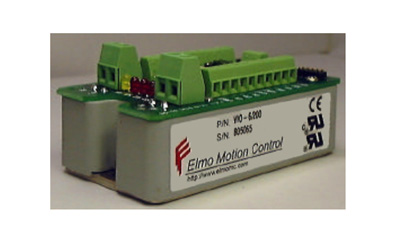
2.5. Configuración del amortiguador activo
Una vez diseñadas todas las partes del actuador, el conjunto forma el sistema mecatrónico capaz de reducir las vibraciones sobre una estructura. En la Figura 5 se muestra de manera esquemática la configuración del sistema.
En él, se puede observar el actuador montado en el carnero de un centro de mecanizado, con cuyo acelerómetro colocado en la parte fija se mide la vibración en el punto de localización del actuador. Esta señal es llevada al controlador donde será convertida a una señal digital y será manipulada dependiendo del algoritmo de control que se vaya a emplear en este controlador. Una vez calculado el voltaje a realizar, éste es enviado al amplificador donde conociendo las características del actuador se proporcionará la corriente necesaria para realizar la fuerza requerida. Todo esto se realizará de manera continua con una frecuencia lo suficientemente alta para que no haya retrasos considerables en la actuación.
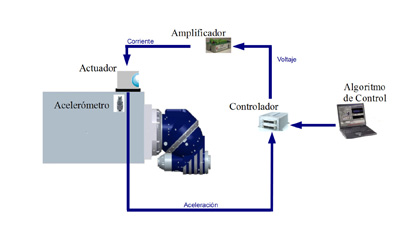
Figura 5. Configuración del sistema mecatrónico.
3. Validación y caracterización
Una vez construido el actuador (Figura 6), se ha comprobado su funcionamiento. La validación del actuador se ha realizado mediante 4 ensayos. El primero de ellos es el de caracterizar la dinámica del actuador y analizar la linealidad que ofrece en función del nivel de fuerza. El segundo trata de conocer el máximo nivel de fuerza que es capaz de ofrecer el actuador. Tras estas dos validaciones, se ha realizado un ensayo para analizar el comportamiento térmico del actuador. Finalmente, se ha introducido el actuador en un centro de mecanizado para observar si es capaz de eliminar casos de chatter.
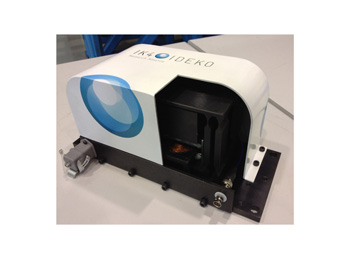
3.1. Caracterización Fuerza/Voltaje
Para analizar esta relación, se mete un barrido de frecuencia con un valor constante de voltaje a la entrada del servo amplificador de corriente y se obtiene la función de respuesta en frecuencia (FRF) entre la fuerza obtenida y el voltaje de entrada. La medida de la fuerza ha sido realizada mediante una placa dinamométrica.
Tal y como se puede observar en la Figura 7, la frecuencia del modo de suspensión está en 17,6 Hz, validando así el modelo de elementos finitos realizado. Por otro lado, también se puede ver que el comportamiento no cambia con el nivel de fuerza por lo que se puede considerar que el actuador tiene un comportamiento lineal, tal y como se esperaba gracias al flexo diseñado.
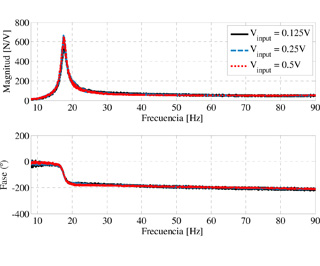
3.2 Fuerza máxima
Para conocer la máxima fuerza que es capaz de realizar el actuador, se han introducido varios niveles de corriente en dos frecuencias diferentes y se ha medido la fuerza mediante la placa dinamométrica. El resultado es reflejado en la Tabla 1.
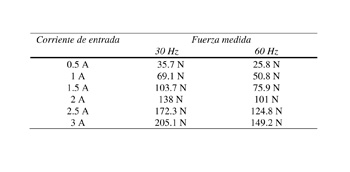
Como se puede observar, se obtiene sobradamente la fuerza deseada para las dos frecuencias analizadas. Incluso la fuerza real ha superado lo calculado teóricamente mediante el software de análisis electromagnético.
3.3 Análisis térmico
El térmico es un importante test para validar el actuador. Debido a la resistencia que ofrecen los bobinados, estos se calientan cuando una corriente les es introducida. Este calentamiento no puede alcanzar valores altos debido a que a partir de ciertos valores los imanes permanentes pierden facultades y no se pueden obtener los mismos niveles de fuerza. Además, existe el riesgo de que a altas temperaturas puedan desmagnetizarse estos imanes permanentes y que el aislante de los bobinados se resienta. En el caso de este actuador, se ha colocado la temperatura máxima en los 100°C, de manera que se introduce un margen de seguridad antes de entrar en la zona donde pueden aparecer los problemas comentados. En este ensayo, se han testeado 3 diferentes amplitudes de voltaje de entrada y se ha analizado la evolución de la temperatura en el bobinado mediante sensores de temperatura. El voltaje de entrada analizado lleva una frecuencia de 60Hz. Los resultados (Figura 8) muestran como a partir de la hora se empiezan a estabilizar las temperaturas y aún se encuentran lejos de la temperatura límite impuesta. Por ello, se puede dar como validado su comportamiento térmico. Aun así, siempre es recomendable introducir un sistema de refrigeración al actuador.
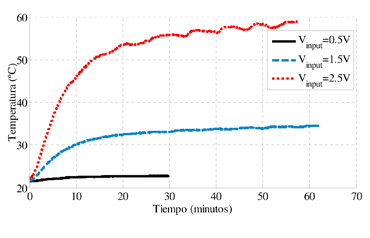
3.4. Pruebas de corte
Como último paso para validar el actuador, se debe analizar si es capaz de eliminar el chatter. Para ello, se ha colocado el actuador en el carnero del prototipo de centro de mecanizado DS-630, tal y como se puede ver en la Figura 9. El algoritmo de control empleado ha sido el Direct Velocity Feedback (DVF) por el hecho de que es el que mejor resultados ha ofrecido hasta ahora en problemas de vibraciones de máquina herramienta [13]. Antes de realizar las pruebas de corte, se ha analizado mediante un martillo dinamométrico la respuesta que ofrece la máquina según se aumenta la ganancia del actuador. El resultado puede ser observado en la Figura 9. Mediante esta gráfica podemos asegurar que el funcionamiento del actuador es correcto ya que el principal modo del sistema es reducido considerablemente. El aumentar más la ganancia puede hacer que se inestabilicen otros modos.
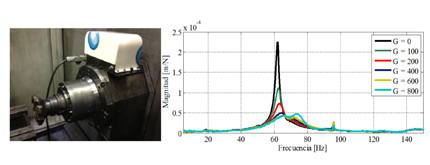
Una vez visto el apropiado funcionamiento del actuador y las ganancias necesarias, se ha definido un proceso de corte. Las condiciones de corte y la herramienta son descritas en la Tabla 2. Se trata de operaciones de planeado en un plano vertical, cortando en dirección X. De este modo, se han realizado cortes a 6 diferentes alturas Y. Como se ha mencionado en el apartado 2.2, el modo de suspensión ha sido compensado mediante el control [11].
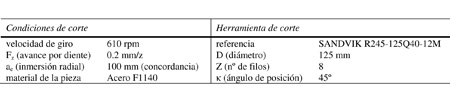
La Figura 10 muestra la estabilidad del sistema para diferentes valores de Y y profundidades de corte. Por motivos de confidencialidad, no han sido proporcionados los valores absolutos en mm de profundidad de corte y los valores mostrados dependen de un valor b, cuyo valor ha sido ocultado.
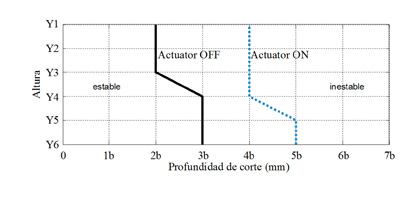
Como se puede observar, la capacidad de corte ha sido doblada para ciertas alturas, por lo que se puede ver que aunque se trate de un actuador de poca capacidad de fuerza, también es capaz de mejorar la capacidad de corte.
4. Conclusiones
En este trabajo ha sido presentado el actuador inercial electromagnético desarrollado íntegramente en Ideko-IK4. Se ha mostrado el diseño magnético realizado para obtener una fuerza que finalmente ha resultado ser mayor que 140 N y se ha explicado el diseño de un complejo doble flexo que sirve para guiar de forma totalmente lineal la masa móvil. En la validación del actuador, se ha visto que el principal modo de suspensión se encuentra cerca del rango de frecuencias en el que se quiere actuar, por lo que se ha planteado el uso del control para que este modo no afecte en el buen funcionamiento del actuador. Por otro lado, se ha demostrado la linealidad conseguida en el actuador, lo que facilita el empleo de diferentes estrategias o filtros de control.
Se ha mostrado que el actuador térmicamente no presenta ningún problema ya que no se alcanza en ningún momento la temperatura crítica acordada. Aun así, se debe tomar en cuenta que para posteriores diseños de actuadores puede ser posible el tener que diseñar un sistema de refrigeración para poder aumentar la amplitud de la corriente sobre los bobinados. Finalmente se ha demostrado que aunque se trata de un actuador de poca fuerza disponible, es capaz de aumentar la capacidad de corte de un centro de mecanizado. Para ello se ha colocado el dispositivo en el carnero y mediante un algoritmo de control que realimenta la velocidad de vibración, ha llegado a doblar esta capacidad en ciertos casos.
Agradecimientos
Este trabajo ha sido realizado dentro del proyecto ER-2012/00019 PAINT (Polo Aeronáutico de Innovación en Turbinas) financiado por el Gobierno Vasco a través de su programa Etorgai
Referencias
[1] J. Tlusty, L. Spacek, Self-excited vibrations on machine tools, Nakl. CSAV (1954).
[2] S.Tobias, Machine-tool Vibration, Blackie. London, Glasgow (1965).
[3] N.D. Sims, A. Amarasinghe, K. Ridgway, Particle dampers for workpiece chatter migration, ASME International Mechanical Engineering Congress and Exposition (2005),
Orlando, USA, 825-832.
[4] Y. Yang, J. Muñoa, Y. Altintas, Optimization of multiple tuned mass dampers to supress machine tool chatter, International Journal of Machine Tools & Manufacture 50(9)(2010), 834-842.
[5] J.P. Den Hartog, Mechanical vibrations, Dover, New York, 1985.
[6] D.A. Bies, T.M. Yang, Hybrid Vibration Isolation System For Helicopters”, Shock and
Vibration Bulletin (1968).
[7] A. Cowley, A. Boyle, Active Dampers for Machine Tools, CIRP Annals 18(1)(1970),
213-222.
[8] C. Ehmann, R. Nordmann, Low Cost Actuator for Active Damping of Large Machines, IFAC Conference on Mechatronic Systems (2002), Berkeley, USA.
[9] N. Loix, J.Ph. Verschueren, Stand Alone Active Damping Device, ACTUATOR 2004,
Bremen, Germany.
[10] C. Brecher, A. Schulz, Electrohydraulic Active Damping System, CIRP Annals 54(1) (2005), 389-392.
[11] A. Bilbao, I. Azpeitia, S. Luyckx, N. Loix, J. Muñoa, Low Frequency Chatter Suppression using an Inertial Actuator, 9th CIRP International Conference on High Speed Machining (2012), San Sebastian, Spain.
[12] F. Claeyssen, G. Magnac, O. Sosnicki, Moving Iron Controllable Actuators, ACTUATOR 2008, Bremen, Germany.
[13] J. Muñoa, I. Mancisidor, N. Loix, L.G. Uriarte, R. Barcena, M. Zatarain, Chatter suppression in ram type travelling column milling machines using a biaxial inertial actuator, CIRP Annals – Manufacturing Technology (approved) (2013).